What is a Gold Finger PCB?
A gold finger PCB is a printed circuit board that features gold-plated contact fingers along one or more edges of the board. These gold fingers are essentially exposed copper traces that have been plated with a thin layer of gold. The gold plating on the PCB fingers serves several purposes:
- Enhances conductivity
- Prevents oxidation and corrosion
- Improves durability and wear resistance
- Ensures reliable electrical contact
Gold is an ideal material for contact fingers due to its excellent electrical conductivity, resistance to corrosion, and compatibility with various mating connectors. The thickness of the gold plating typically ranges from 0.05 to 0.5 micrometers (μm), depending on the specific application and performance requirements.
Applications of Gold Finger PCBs
Gold finger PCBs find applications in numerous electronic devices and systems where reliable, high-density interconnections are essential. Some common applications include:
- Computer peripherals (e.g., memory modules, graphics cards, expansion cards)
- Mobile devices (e.g., smartphones, tablets)
- Consumer electronics (e.g., gaming consoles, digital cameras)
- Industrial equipment (e.g., automation systems, test and measurement devices)
- Telecommunications (e.g., network switches, routers)
- Automotive electronics (e.g., infotainment systems, sensors)
In these applications, gold finger PCBs enable efficient data transfer, power delivery, and signal integrity between the board and the mating connector or socket.
Gold Finger PCB Manufacturing Process
The manufacturing process for gold finger PCBs involves several key steps to ensure high-quality and reliable contact fingers:
- PCB Fabrication
- The PCB is fabricated using standard processes, such as etching, drilling, and solder mask application.
-
The copper traces that will become the gold fingers are left exposed, without solder mask coverage.
-
Surface Preparation
- The exposed copper traces undergo a cleaning process to remove any contaminants or oxidation.
-
This step ensures a clean and uniform surface for the subsequent plating process.
-
Nickel Plating (Optional)
- In some cases, a thin layer of nickel is plated onto the copper traces before the gold plating.
-
Nickel acts as a barrier layer, preventing the diffusion of copper into the gold layer and improving adhesion.
-
Gold Plating
- The exposed copper traces (or nickel-plated traces) are plated with a thin layer of gold using an electroplating process.
-
The gold plating thickness is carefully controlled to meet the specified requirements (typically 0.05 to 0.5 μm).
-
Inspection and Testing
- The gold finger PCBs undergo visual inspection and electrical testing to ensure the quality and functionality of the contact fingers.
-
This step verifies the gold plating thickness, uniformity, and conductivity.
-
Cutting and Packaging
- The PCBs are cut to the desired shape and size, with the gold fingers along the designated edges.
- The finished gold finger PCBs are packaged and shipped to the customer for assembly and integration into the final product.
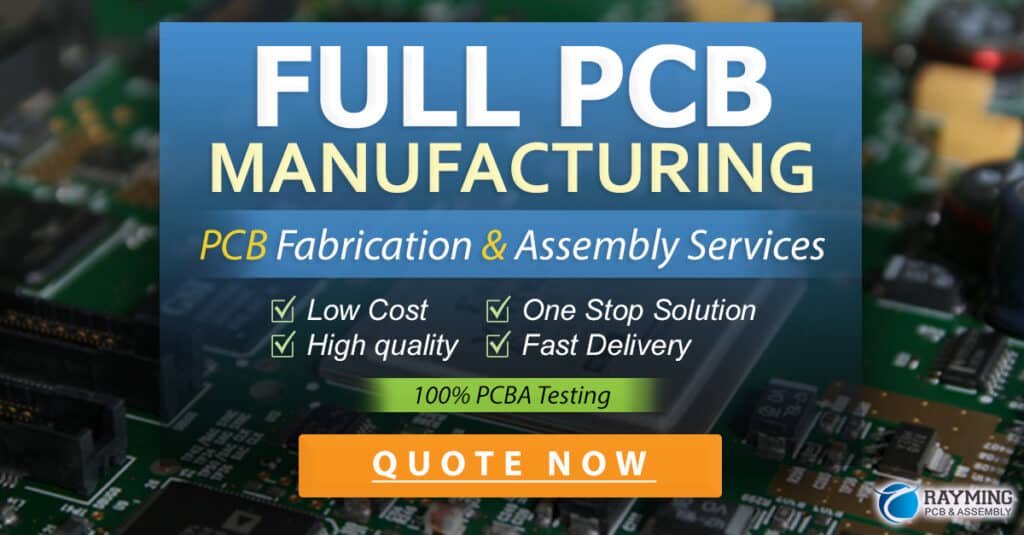
Design Considerations for Gold Finger PCBs
When designing a gold finger PCB, several key factors must be considered to ensure optimal performance and reliability:
- Contact Finger Dimensions
- The width, length, and pitch of the gold fingers should be designed to match the mating connector or socket.
-
Industry standards, such as the DIMM (Dual Inline Memory Module) or PCIe (Peripheral Component Interconnect Express) specifications, provide guidelines for contact finger dimensions.
-
Gold Plating Thickness
- The gold plating thickness should be specified based on the application requirements and the expected number of mating cycles.
-
Thicker gold plating offers better durability and wear resistance but increases the manufacturing cost.
-
Signal Integrity
- The layout of the PCB traces leading to the gold fingers should be optimized for signal integrity.
-
Proper impedance matching, minimizing crosstalk, and reducing signal reflections are crucial for high-speed applications.
-
Mechanical Stability
- The gold finger PCB should be designed with sufficient mechanical stability to withstand repeated insertion and removal from the mating connector.
-
Reinforcement techniques, such as using thicker PCB substrates or adding support structures, can enhance the mechanical integrity of the board.
-
Solder Mask Design
- The solder mask opening around the gold fingers should be designed to prevent solder bridging or contamination during the assembly process.
- A clear solder mask opening also ensures proper contact between the gold fingers and the mating connector.
Benefits of Using Gold Finger PCBs
Gold finger PCBs offer several advantages over other types of interconnect solutions:
- High Reliability
- Gold-plated contact fingers provide a highly reliable electrical connection, even in harsh environments.
-
The gold plating prevents oxidation and corrosion, ensuring consistent performance over the product’s lifetime.
-
Durability
- Gold fingers are resistant to wear and tear, making them suitable for applications with frequent mating cycles.
-
The hardness and abrasion resistance of gold minimize the risk of damage to the contact fingers during insertion and removal.
-
Excellent Conductivity
- Gold is an excellent electrical conductor, providing low contact resistance and enabling efficient current flow.
-
This property is particularly important for high-speed and high-frequency applications.
-
Compatibility
- Gold finger PCBs are compatible with a wide range of mating connectors and sockets.
-
Industry-standard specifications ensure interoperability between different manufacturers’ components.
-
Space Savings
- Gold fingers allow for high-density interconnections, enabling compact and space-efficient PCB designs.
- This is particularly valuable in devices where board space is limited, such as smartphones and wearables.
Challenges and Considerations
While gold finger PCBs offer numerous benefits, there are also some challenges and considerations to keep in mind:
- Cost
- Gold plating adds to the overall manufacturing cost of the PCB due to the precious metal content.
-
The cost impact can be significant for high-volume production or designs with extensive gold finger contact areas.
-
Mating Connector Wear
- Although gold fingers are durable, the mating connectors or sockets can experience wear over time.
-
Regular inspection and maintenance of the mating components are necessary to ensure reliable connections.
-
Handling and Assembly
- Gold finger PCBs require careful handling during assembly to avoid damage to the contact fingers.
-
Proper alignment and insertion techniques are essential to prevent bent or deformed fingers.
-
Compatibility with Lead-Free Processes
- When using gold finger PCBs in lead-free manufacturing processes, compatibility issues may arise.
- The higher soldering temperatures associated with lead-free processes can cause diffusion between the gold and the underlying copper, potentially weakening the bond.
Alternatives to Gold Finger PCBs
While gold finger PCBs are widely used, there are alternative interconnect solutions available, depending on the application requirements:
- Edge Connectors with Other Plating Materials
- Other plating materials, such as tin or silver, can be used instead of gold for edge connectors.
-
These alternatives offer lower cost but may have limitations in terms of durability and corrosion resistance.
-
Press-Fit Connectors
- Press-fit connectors utilize a mechanical connection between the PCB and the mating component.
-
They eliminate the need for soldering but require precise alignment and insertion force control.
-
Soldered Connectors
- Traditional soldered connectors, such as pin headers or surface-mount connectors, can be used for board-to-board or board-to-wire connections.
- Soldered connectors provide a permanent connection but may not be suitable for applications requiring frequent mating cycles.
Frequently Asked Questions (FAQ)
- What is the typical thickness of gold plating on gold finger PCBs?
-
The typical thickness of gold plating on gold finger PCBs ranges from 0.05 to 0.5 micrometers (μm). The specific thickness is determined based on the application requirements and the expected number of mating cycles.
-
Can gold finger PCBs be used in high-speed applications?
-
Yes, gold finger PCBs are well-suited for high-speed applications due to the excellent electrical conductivity of gold. However, proper PCB layout and signal integrity considerations are crucial to ensure optimal performance.
-
Are gold finger PCBs compatible with lead-free manufacturing processes?
-
Gold finger PCBs can be used in lead-free manufacturing processes, but compatibility issues may arise due to the higher soldering temperatures. Proper process control and material selection are necessary to mitigate any potential issues.
-
How do gold finger PCBs compare to other interconnect solutions in terms of cost?
-
Gold finger PCBs tend to have a higher manufacturing cost compared to other interconnect solutions due to the use of gold plating. The cost impact can be significant for high-volume production or designs with extensive gold finger contact areas.
-
What are the key design considerations for gold finger PCBs?
- When designing gold finger PCBs, key considerations include contact finger dimensions, gold plating thickness, signal integrity, mechanical stability, and solder mask design. Industry standards and application-specific requirements should be taken into account to ensure optimal performance and reliability.
Conclusion
Gold finger PCBs play a crucial role in establishing reliable, high-density interconnections in various electronic devices and systems. The gold-plated contact fingers provide excellent electrical conductivity, durability, and resistance to corrosion, ensuring consistent performance over the product’s lifetime. When designing and manufacturing gold finger PCBs, careful consideration must be given to factors such as contact finger dimensions, gold plating thickness, signal integrity, and mechanical stability. While gold finger PCBs offer numerous benefits, they also come with challenges, such as higher manufacturing costs and potential compatibility issues with lead-free processes. Alternative interconnect solutions, such as edge connectors with other plating materials, press-fit connectors, and soldered connectors, may be suitable depending on the specific application requirements. By understanding the characteristics, applications, and design considerations of gold finger PCBs, engineers and manufacturers can make informed decisions when selecting the most appropriate interconnect solution for their products.
Parameter | Typical Value Range |
---|---|
Gold Plating Thickness | 0.05 – 0.5 μm |
Contact Finger Width | 0.2 – 1.0 mm |
Contact Finger Length | 2 – 10 mm |
Contact Finger Pitch | 0.5 – 2.54 mm |
PCB Substrate Thickness | 0.6 – 2.4 mm |
Solder Mask Opening Width | 0.1 – 0.3 mm |
Leave a Reply