Types of Gerber Formats
There are several types of Gerber formats, each serving a specific purpose in the PCB design and manufacturing process:
RS-274-D
RS-274-D, also known as Gerber D-Code format, is the oldest and most basic Gerber format. It uses a simple ASCII format to describe the PCB layout, where each line represents a command or a coordinate. RS-274-D files have a .gbr extension and are used to describe the copper layers, solder mask, and silkscreen of a PCB.
RS-274X
RS-274X, also known as Extended Gerber or Gerber X format, is an enhanced version of the RS-274-D format. It adds support for aperture definitions, polarity, and interpolation. RS-274X files have a .gbr or .gbrx extension and are used to describe the same aspects of a PCB as RS-274-D, but with more flexibility and precision.
Aperture Definition Format (ADF)
Aperture Definition Format (ADF) is a companion format to RS-274X that defines the shapes and sizes of the apertures used in the Gerber file. ADF files have a .adf extension and contain a list of aperture definitions, each with a unique D-Code. The D-Codes are then referenced in the RS-274X file to specify which aperture to use for each element of the PCB.
Gerber Job File (GJF)
Gerber Job File (GJF) is a format used to group multiple Gerber files together and provide additional information about the PCB job. GJF files have a .gjs extension and contain a list of Gerber files, as well as job-specific parameters such as the PCB size, thickness, and material. GJF files are used to simplify the transfer of PCB design data between software tools and manufacturing equipment.
Advantages of Gerber Formats
Gerber formats offer several advantages for PCB design and manufacturing:
-
Widespread adoption: Gerber formats are the de facto standard in the PCB industry, supported by virtually all PCB design software and manufacturing equipment. This widespread adoption ensures compatibility and ease of data exchange between different tools and vendors.
-
Simplicity: Gerber formats are relatively simple and easy to understand, consisting of plain text files with straightforward commands and coordinates. This simplicity makes it easy to create, modify, and debug Gerber files, even without specialized software.
-
Precision: Gerber formats, particularly RS-274X, support high-precision coordinates and aperture definitions, enabling the creation of complex and detailed PCB designs. This precision is essential for modern high-density PCBs with fine pitch components and traces.
-
Flexibility: Gerber formats support a wide range of PCB design elements, including copper layers, solder mask, silkscreen, and drill holes. This flexibility allows designers to create comprehensive and accurate representations of their PCB designs.
Limitations of Gerber Formats
Despite their widespread adoption and advantages, Gerber formats also have some limitations:
-
Lack of design intent: Gerber files represent the final output of a PCB design, but they do not contain information about the design intent, such as component placement, routing constraints, or electrical properties. This lack of design intent can make it difficult to modify or optimize a PCB design based solely on Gerber files.
-
No standardized layer stackup: Gerber files do not have a standardized way to describe the layer stackup of a PCB, including the number of layers, their order, and their materials. This information is typically provided separately, either in a README file or through direct communication between the designer and the manufacturer.
-
Limited support for advanced features: While Gerber formats support a wide range of PCB design elements, they may not fully support some advanced features, such as embedded components, HDI structures, or 3D models. In these cases, additional formats or design files may be necessary to fully describe the PCB.
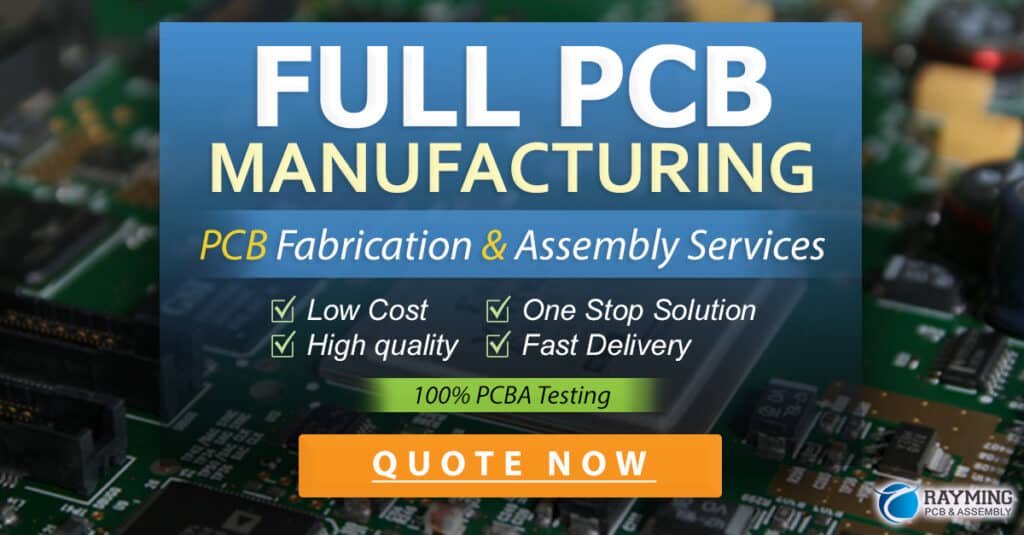
Best Practices for Using Gerber Formats
To ensure the best results when using Gerber formats for PCB design and manufacturing, follow these best practices:
-
Use the latest format version: Always use the latest version of the Gerber format, currently RS-274X, to take advantage of its enhanced features and precision. Avoid using older formats like RS-274-D unless absolutely necessary for compatibility with legacy tools.
-
Include all necessary files: When sending Gerber files for manufacturing, include all the necessary files, such as the copper layers, solder mask, silkscreen, drill files, and aperture lists. Use a Gerber Job File (GJF) to group these files together and provide additional job information.
-
Use consistent naming conventions: Adopt a consistent naming convention for your Gerber files, such as using a prefix or suffix to indicate the layer type (e.g., “top_copper.gbr” or “solder_mask_bottom.gbr”). This consistency helps avoid confusion and errors during the manufacturing process.
-
Verify your Gerber files: Before sending Gerber files for manufacturing, always verify them using a Gerber viewer or a PCB CAM tool. Check for any errors, missing features, or discrepancies between the Gerber files and your original PCB design. Many PCB manufacturers also offer free Gerber file verification services.
-
Communicate with your manufacturer: Maintain clear communication with your PCB manufacturer throughout the design and manufacturing process. Provide them with any additional information they may need, such as the layer stackup, material requirements, or special instructions. Be open to their feedback and recommendations to ensure the best possible results.
Table: Gerber File Extensions and Their Uses
Extension | Format | Description |
---|---|---|
.gbr | RS-274-D/X | Copper layers, solder mask, and silkscreen |
.gbrx | RS-274X | Copper layers, solder mask, and silkscreen (extended) |
.adf | Aperture Definition Format | Defines aperture shapes and sizes for RS-274X |
.gjs | Gerber Job File | Groups multiple Gerber files and provides job information |
.drl | NC Drill File | Contains information about drill holes and sizes |
Frequently Asked Questions (FAQ)
1. What is the difference between RS-274-D and RS-274X Gerber formats?
RS-274-D is the older Gerber format that uses a simple ASCII structure to describe PCB elements. RS-274X is an extended version that adds support for aperture definitions, polarity, and interpolation, providing more flexibility and precision in PCB design.
2. Can I view and edit Gerber files without specialized software?
Yes, since Gerber files are plain text files, you can view and edit them using any text editor. However, it is recommended to use specialized Gerber viewer or PCB CAM software to ensure proper visualization and avoid errors.
3. What is the purpose of the Aperture Definition Format (ADF)?
The Aperture Definition Format (ADF) is used to define the shapes and sizes of the apertures referenced in an RS-274X Gerber file. Each aperture is assigned a unique D-Code, which is then used in the Gerber file to specify which aperture to use for each PCB element.
4. How do I ensure that my Gerber files are correct before sending them for manufacturing?
Always verify your Gerber files using a Gerber viewer or PCB CAM tool before sending them for manufacturing. Check for any errors, missing features, or discrepancies between the Gerber files and your original PCB design. Many PCB manufacturers also offer free Gerber file verification services.
5. What additional information should I provide to my PCB manufacturer along with the Gerber files?
In addition to the Gerber files, provide your PCB manufacturer with information about the layer stackup, material requirements, and any special instructions. Use a README file or direct communication to convey this information clearly. Maintain open communication with your manufacturer throughout the design and manufacturing process to ensure the best results.
In conclusion, Gerber formats are essential for PCB design and manufacturing, providing a standardized way to describe and exchange PCB design information. By understanding the different types of Gerber formats, their advantages and limitations, and following best practices, PCB designers and manufacturers can work together to create high-quality, reliable PCBs efficiently.
Leave a Reply