What are Chamfered holes?
A chamfered hole is a mechanical feature that involves creating a angled or beveled edge at the entrance or exit of a drilled hole. The chamfer is typically a 45-degree angle, although other angles can be used depending on the specific requirements of the application. The primary purpose of chamfering is to remove sharp edges, improve the hole’s appearance, and facilitate the insertion of mating parts or fasteners.
Definition and Characteristics
Chamfered holes are characterized by the following key features:
- Angled or beveled edge: The chamfer is created by cutting away material at a specific angle, usually 45 degrees, relative to the hole’s axis.
- Depth of chamfer: The depth of the chamfer can vary depending on the application and the size of the hole. It is typically expressed as a percentage of the hole’s diameter or as a specific dimension.
- Symmetry: Chamfers are usually symmetrical around the hole’s circumference, ensuring a consistent and uniform appearance.
Types of Chamfered Holes
There are several types of chamfered holes, each serving a specific purpose and suited for different applications. Let’s explore the most common types:
1. Single Chamfered Holes
Single chamfered holes feature a chamfer on one end of the hole, either at the entrance or the exit. This type of chamfer is the most basic and commonly used in various industries. Single chamfered holes are often used for:
- Improving the appearance of the hole
- Facilitating the insertion of mating parts or fasteners
- Reducing stress concentrations around the hole’s edge
2. Double Chamfered Holes
Double chamfered holes have chamfers on both ends of the hole, creating a symmetrical appearance. This type of chamfer is particularly useful in applications where:
- Parts need to be inserted from either side of the hole
- The hole serves as a passage for fluids or gases
- Aesthetics are a crucial consideration
3. Countersunk Holes
Countersunk holes are a specific type of chamfered hole designed to accommodate the head of a countersunk screw or bolt. The chamfer angle in countersunk holes is typically 82 degrees for a flat head screw and 90 degrees for a raised head screw. Countersunk holes are used in applications where:
- A flush or semi-flush surface is required
- The screw head needs to be hidden or protected
- Aerodynamic or hydrodynamic properties are essential
Applications of Chamfered Holes
Chamfered holes find extensive use in various industries and applications. Some of the most common applications include:
1. Automotive Industry
In the automotive industry, chamfered holes are used in numerous components, such as:
- Engine blocks and cylinder heads
- Transmission housings
- Suspension components
- Brake systems
Chamfered holes in these applications help improve the overall fit and finish of the parts, reduce stress concentrations, and facilitate the assembly process.
2. Aerospace Industry
The aerospace industry relies heavily on chamfered holes for various purposes, including:
- Airframe construction
- Jet engine components
- Fastener holes in aircraft skin
- Fuel and hydraulic systems
Chamfered holes in aerospace applications ensure proper alignment, reduce stress concentrations, and improve the overall performance and reliability of the components.
3. Medical Devices
In the medical device industry, chamfered holes play a crucial role in:
- Orthopedic implants
- Surgical instruments
- Diagnostic equipment
- Dental implants
Chamfered holes in medical devices help improve the compatibility between mating parts, reduce the risk of tissue damage during insertion, and enhance the overall aesthetics of the devices.
4. Consumer Products
Chamfered holes are also widely used in various consumer products, such as:
- Electronic devices
- Home appliances
- Furniture
- Sporting equipment
In these applications, chamfered holes contribute to the overall aesthetics, ease of assembly, and user experience.
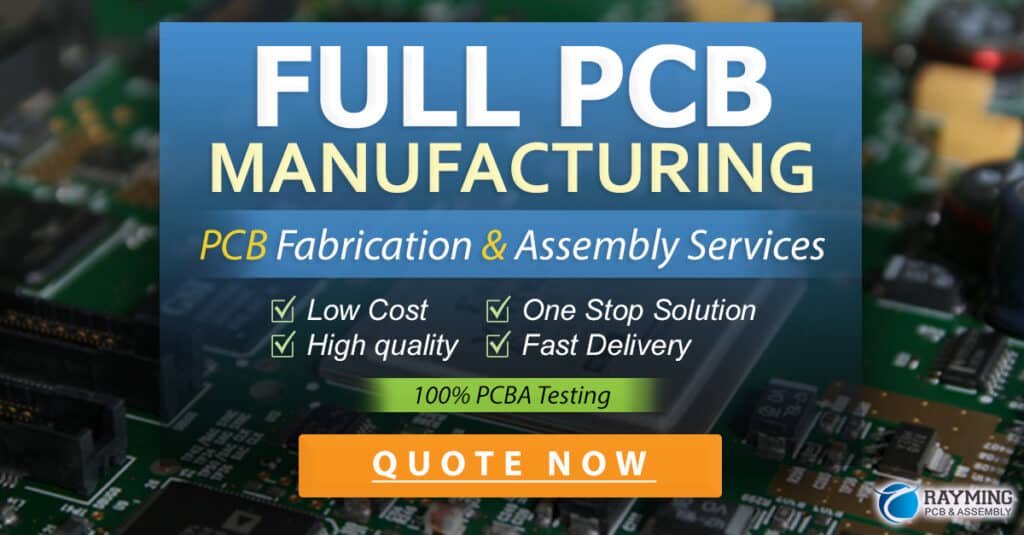
Techniques for Creating Chamfered Holes
There are several techniques used to create chamfered holes, each with its own advantages and limitations. The choice of technique depends on factors such as the material being machined, the required precision, and the production volume. Let’s explore some of the most common techniques:
1. Chamfer Drilling
Chamfer drilling is a specialized drilling process that uses a chamfer drill bit to create the chamfer and the hole in a single operation. Chamfer drill bits have a built-in chamfer angle, typically 45 degrees, and are available in various sizes and materials. Chamfer drilling is suitable for:
- Small to medium-sized holes
- Low to medium production volumes
- Materials such as metals, plastics, and composites
2. Spot Facing
Spot facing is a machining process that creates a flat, smooth surface around the entrance of a hole. While not strictly a chamfering technique, spot facing can be used to create a chamfer-like feature by controlling the depth and diameter of the spot face. Spot facing is commonly used for:
- Improving the seating of fasteners or mating parts
- Enhancing the appearance of the hole
- Creating a consistent surface for sealing or gasket applications
3. Chamfer Milling
Chamfer milling is a machining process that uses a specialized chamfer milling cutter to create chamfers on the edges of holes. The chamfer milling cutter is designed with the desired chamfer angle and can be used on a milling machine or a CNC machining center. Chamfer milling is suitable for:
- Large diameter holes
- High precision chamfers
- Materials such as metals, plastics, and composites
4. Chamfer Reaming
Chamfer reaming is a finishing process that uses a chamfer reamer to create a precise and smooth chamfer on a pre-drilled hole. Chamfer reamers are available in various sizes and chamfer angles and are typically used in conjunction with a drilling operation. Chamfer reaming is ideal for:
- High precision chamfers
- Improving the surface finish of the chamfer
- Maintaining consistent chamfer dimensions across multiple holes
Advantages of Chamfered Holes
Chamfered holes offer several advantages over non-chamfered holes, making them a preferred choice in many applications. Some of the key advantages include:
1. Improved Part Alignment
Chamfered holes facilitate the alignment and insertion of mating parts, such as shafts, pins, or fasteners. The angled surface of the chamfer acts as a guide, allowing for easier and more accurate assembly. This is particularly important in applications where precise alignment is critical, such as in the aerospace and automotive industries.
2. Reduced Stress Concentrations
Sharp edges and corners around holes can act as stress concentration points, leading to increased stress levels and potential failure of the component. Chamfered holes help alleviate this issue by providing a smooth transition between the hole and the surrounding material. The gradual change in geometry reduces stress concentrations, improving the overall strength and durability of the component.
3. Enhanced Aesthetics
Chamfered holes offer a clean and professional appearance, enhancing the visual appeal of the component. The chamfered edge creates a shadow effect, making the hole appear more defined and visually pleasing. This is particularly important in applications where aesthetics are a key consideration, such as in consumer products and architectural elements.
4. Improved Fluid Flow
In applications involving the flow of fluids or gases through holes, chamfered edges can help improve the flow characteristics. The smooth transition provided by the chamfer reduces turbulence and flow separation, leading to more efficient and streamlined flow. This is particularly relevant in the design of fluid power systems, hydraulic components, and fuel injection systems.
5. Easier Deburring
Deburring is the process of removing sharp edges and burrs from machined holes to improve safety and functionality. Chamfered holes make the deburring process easier and more efficient, as the chamfer provides a starting point for the deburring tool. This reduces the time and effort required for deburring, ultimately leading to cost savings in the manufacturing process.
Design Considerations for Chamfered Holes
When designing components with chamfered holes, engineers need to consider several factors to ensure optimal performance and functionality. Some of the key design considerations include:
1. Chamfer Angle
The choice of chamfer angle depends on the specific application and the mating parts involved. The most common chamfer angle is 45 degrees, as it provides a good balance between ease of insertion and strength. However, other angles, such as 30 degrees or 60 degrees, may be used in specific situations. It is essential to consider the design requirements and the standards applicable to the industry when selecting the chamfer angle.
2. Chamfer Depth
The depth of the chamfer is another crucial design consideration. The chamfer depth is typically expressed as a percentage of the hole diameter or as a specific dimension. Deeper chamfers provide better guidance for mating parts but may also reduce the effective diameter of the hole. On the other hand, shallow chamfers may not provide sufficient guidance and could lead to misalignment. Engineers need to strike a balance between chamfer depth and the functional requirements of the hole.
3. Material Compatibility
The choice of chamfer angle and depth should also consider the material properties of the component and the mating parts. Some materials, such as brittle plastics or composites, may be more susceptible to chipping or cracking during the chamfering process. In such cases, a shallower chamfer angle or a smaller chamfer depth may be necessary to prevent damage to the material.
4. Manufacturing Feasibility
The design of chamfered holes should also take into account the manufacturing processes available and their limitations. Some chamfering techniques, such as chamfer drilling or milling, may not be suitable for certain materials or hole sizes. Engineers need to collaborate with manufacturing experts to ensure that the designed chamfered holes can be produced efficiently and cost-effectively.
5. Assembly and Maintenance
The design of chamfered holes should consider the ease of assembly and maintenance of the component. Chamfered holes that facilitate the insertion of mating parts can significantly reduce assembly time and effort. Additionally, chamfered holes that allow for easy access to fasteners or other components during maintenance can help minimize downtime and improve the overall serviceability of the product.
Frequently Asked Questions (FAQ)
1. What is the difference between a chamfer and a countersink?
A chamfer is an angled or beveled edge created at the entrance or exit of a hole, typically at a 45-degree angle. A countersink, on the other hand, is a specific type of chamfer designed to accommodate the head of a countersunk screw or bolt. Countersinks have specific angles, such as 82 degrees for flat head screws and 90 degrees for raised head screws.
2. Can chamfered holes be created in any material?
Chamfered holes can be created in most machinable materials, including metals, plastics, and composites. However, the choice of chamfering technique and the design parameters may need to be adjusted based on the material properties. Some materials, such as brittle plastics or ceramics, may require special considerations to prevent chipping or cracking during the chamfering process.
3. What are the most common chamfer angles used in mechanical design?
The most common chamfer angle used in mechanical design is 45 degrees. This angle provides a good balance between ease of insertion, strength, and manufacturability. Other chamfer angles, such as 30 degrees or 60 degrees, may be used in specific applications or to meet certain design requirements.
4. How does the chamfer depth affect the performance of the hole?
The chamfer depth can affect the performance of the hole in several ways. A deeper chamfer provides better guidance for mating parts and can help reduce stress concentrations around the hole’s edge. However, a deeper chamfer also reduces the effective diameter of the hole, which may impact the strength or the flow characteristics of the hole. Engineers need to consider the functional requirements of the hole when determining the appropriate chamfer depth.
5. Are there any standards or guidelines for designing chamfered holes?
Yes, there are various standards and guidelines available for designing chamfered holes, depending on the industry and the specific application. For example, the American Society of Mechanical Engineers (ASME) provides guidelines for chamfered holes in their Y14.5 standard on dimensioning and tolerancing. Other industry-specific standards, such as those in the aerospace or automotive sectors, may also provide guidance on chamfered hole design. Engineers should consult the relevant standards and guidelines when designing chamfered holes to ensure compliance and optimal performance.
Conclusion
Chamfered holes are a fundamental feature in mechanical design, offering numerous benefits and enabling the efficient functioning of various components and systems. By understanding the types, applications, and design considerations of chamfered holes, engineers can create more reliable, aesthetic, and high-performing products.
As technology advances and new materials and manufacturing techniques emerge, the design and application of chamfered holes will continue to evolve. Engineers must stay up-to-date with the latest developments and best practices to ensure that their designs meet the ever-changing demands of the industry.
By mastering the art and science of chamfered holes, mechanical engineers can unlock new possibilities in product design and contribute to the advancement of their respective fields.
Leave a Reply