Introduction to Ceramic Substrate PCBs
Ceramic substrate PCBs are a type of printed circuit board that uses a ceramic material as the base substrate instead of the more commonly used FR-4 or other organic materials. These PCBs offer unique properties that make them suitable for specific applications, particularly those involving high temperatures, high frequencies, and demanding environmental conditions.
Advantages of Ceramic Substrate PCBs
Ceramic substrate PCBs offer several advantages over traditional PCBs:
- High thermal conductivity
- Low dielectric loss
- Excellent dimensional stability
- High mechanical strength
- Resistance to harsh environments
Applications of Ceramic Substrate PCBs
Due to their unique properties, ceramic substrate PCBs are used in various industries and applications, such as:
- Aerospace and defense
- High-power electronics
- RF and microwave devices
- LED lighting
- Automotive electronics
Types of Ceramic Substrate Materials
Several ceramic materials are used in the manufacturing of ceramic substrate PCBs, each with its own set of properties and advantages.
Alumina (Al2O3)
Alumina is the most commonly used ceramic substrate material due to its excellent electrical insulation properties, high thermal conductivity, and good mechanical strength. It is available in various purities, with 96% and 99.6% being the most common.
Aluminum Nitride (AlN)
Aluminum nitride offers even higher thermal conductivity than alumina, making it suitable for applications that require efficient heat dissipation. It also has a low coefficient of thermal expansion (CTE), which helps minimize thermal stresses in the PCB.
Beryllium Oxide (BeO)
Beryllium oxide is another ceramic material known for its high thermal conductivity and low dielectric loss. However, due to the toxic nature of beryllium, its use is limited, and strict safety precautions must be followed during manufacturing.
Manufacturing Process of Ceramic Substrate PCBs
The manufacturing process of ceramic substrate PCBs differs from that of traditional PCBs due to the unique properties of the ceramic materials used.
Green Tape Casting
Green tape casting is a process used to create thin, flexible sheets of ceramic material. The ceramic powder is mixed with organic binders and solvents to form a slurry, which is then cast onto a carrier film using a doctor blade. The resulting green tape is dried and cut to size.
Via Formation and Filling
Vias are formed in the green tape layers using mechanical punching or laser drilling. These vias are then filled with conductive paste, typically made of silver or copper, to create electrical connections between layers.
Lamination and Firing
The green tape layers, with vias and conductive paste, are stacked and laminated under pressure and heat to form a solid structure. The laminated stack is then fired in a high-temperature furnace to sinter the ceramic material and form a dense, rigid substrate.
Metallization and Patterning
After firing, the ceramic substrate is metallized using thin-film or thick-film deposition techniques. The metallization layer, typically consisting of copper or gold, is then patterned using photolithography and etching processes to create the desired circuit layout.
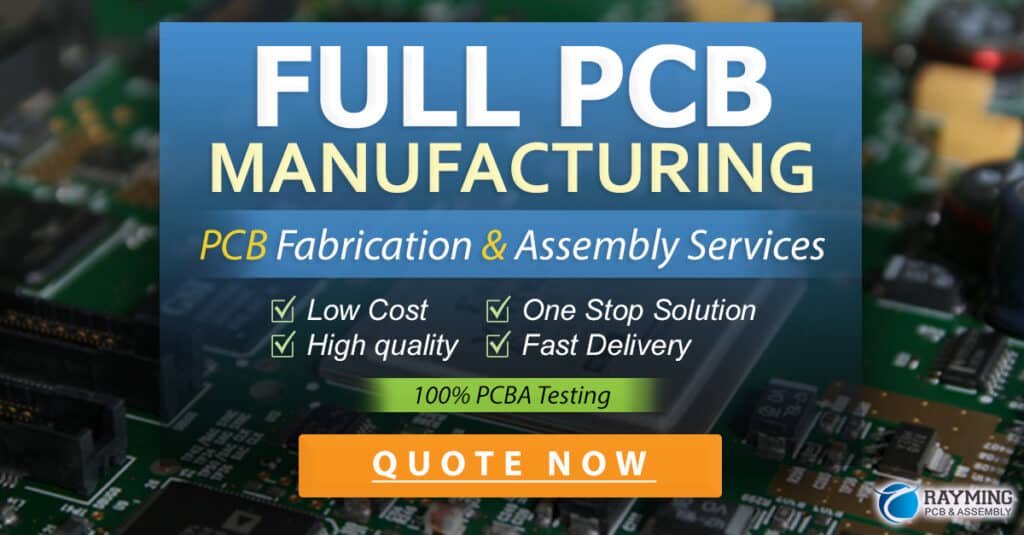
Design Considerations for Ceramic Substrate PCBs
When designing ceramic substrate PCBs, several factors must be considered to ensure optimal performance and reliability.
Thermal Management
Ceramic substrate PCBs are often used in high-power applications, making thermal management a critical design consideration. The high thermal conductivity of ceramic materials helps dissipate heat more efficiently, but proper design techniques, such as the use of thermal vias and heat spreaders, are still necessary.
Coefficient of Thermal Expansion (CTE) Matching
Mismatches in CTE between the ceramic substrate and other components, such as metal leadframes or semiconductor devices, can lead to thermal stresses and reliability issues. Designers must carefully select materials and design layouts to minimize CTE mismatches and ensure long-term reliability.
High-Frequency Considerations
Ceramic substrate PCBs are well-suited for high-frequency applications due to their low dielectric loss and stable dielectric constant. However, designers must still consider factors such as impedance matching, signal integrity, and electromagnetic compatibility (EMC) when designing high-frequency circuits on ceramic substrates.
Reliability and Testing of Ceramic Substrate PCBs
Ensuring the reliability of ceramic substrate PCBs is crucial, especially in critical applications such as aerospace and defense.
Environmental Testing
Ceramic substrate PCBs must undergo various environmental tests to ensure their reliability under harsh conditions. These tests may include:
- Thermal cycling
- Humidity testing
- Vibration and shock testing
- Salt spray testing
Accelerated Life Testing
Accelerated life testing is used to predict the long-term reliability of ceramic substrate PCBs by subjecting them to elevated stress levels, such as higher temperatures or voltages, for a shorter duration. This allows manufacturers to identify potential failure modes and make necessary improvements to the design or manufacturing process.
Future Trends in Ceramic Substrate PCBs
As technology advances, the demand for high-performance and reliable PCBs continues to grow. Some of the future trends in ceramic substrate PCBs include:
High-Temperature Electronics
With the increasing demand for electronics that can operate in extreme temperature environments, such as in aerospace and oil and gas industries, the development of high-temperature ceramic substrate PCBs is expected to grow.
Integration of Active and Passive Components
The integration of active components, such as semiconductor devices, and passive components, such as resistors and capacitors, directly onto the ceramic substrate is becoming more common. This approach, known as “embedded components,” helps reduce the size and improve the performance of electronic systems.
Advanced Packaging Techniques
Advanced packaging techniques, such as 3D packaging and wafer-level packaging, are being adapted for ceramic substrate PCBs to enable higher levels of integration and miniaturization.
Frequently Asked Questions (FAQ)
Q1: What is the main difference between ceramic substrate PCBs and traditional FR-4 PCBs?
A1: The main difference is the base material used. Ceramic substrate PCBs use ceramic materials like alumina or aluminum nitride, while FR-4 PCBs use a glass-reinforced epoxy laminate. Ceramic substrates offer higher thermal conductivity, lower dielectric loss, and better high-frequency performance compared to FR-4.
Q2: Can ceramic substrate PCBs be used for high-voltage applications?
A2: Yes, ceramic substrate PCBs are well-suited for high-voltage applications due to their excellent electrical insulation properties and high dielectric strength.
Q3: Are ceramic substrate PCBs more expensive than traditional PCBs?
A3: Yes, ceramic substrate PCBs are generally more expensive than traditional PCBs due to the higher cost of ceramic materials and the specialized manufacturing processes involved.
Q4: What are the main challenges in designing ceramic substrate PCBs?
A4: The main challenges include thermal management, CTE matching, and high-frequency considerations. Designers must carefully consider these factors to ensure optimal performance and reliability of the PCB.
Q5: How can the reliability of ceramic substrate PCBs be ensured?
A5: The reliability of ceramic substrate PCBs can be ensured through rigorous environmental testing, accelerated life testing, and adherence to industry standards and best practices during the design and manufacturing processes.
Conclusion
Ceramic substrate PCBs offer unique properties that make them ideal for applications requiring high performance, reliability, and the ability to withstand harsh environments. With their excellent thermal conductivity, low dielectric loss, and high mechanical strength, ceramic substrate PCBs are increasingly being used in various industries, from aerospace and defense to high-power electronics and RF devices.
As technology continues to advance, the development of new ceramic materials and manufacturing techniques is expected to drive further growth in the ceramic substrate PCB market. By understanding the advantages, design considerations, and reliability aspects of ceramic substrate PCBs, engineers and manufacturers can leverage this technology to create innovative and high-performance electronic systems.
Leave a Reply