Advantages of Carbon Contacts
Carbon contacts have a number of beneficial properties that make them well-suited for use in electrical applications:
1. High Temperature Resistance
One of the key advantages of carbon contacts is their ability to withstand high temperatures. Carbon materials have a much higher melting point compared to most metals. This allows carbon contacts to maintain their shape and conductive properties even under extreme heat.
Material | Melting Point (°C) |
---|---|
Carbon | 3550 |
Copper | 1085 |
Silver | 962 |
As shown in the table above, the melting point of carbon is over three times higher than copper and silver, two common materials used in electrical contacts. This makes carbon contacts ideal for applications where high temperatures are present, such as in industrial ovens, furnaces, or welding equipment.
2. Low Contact Resistance
Carbon contacts exhibit low contact resistance, which means they allow electrical current to flow through them with minimal energy loss. This property is essential for maintaining efficient power transmission and minimizing heat generation at the contact points.
The table below compares the typical contact resistance values of carbon and metal contacts:
Contact Material | Contact Resistance (mΩ) |
---|---|
Carbon | 10-30 |
Silver | 1-10 |
Copper | 1-10 |
While the contact resistance of carbon is slightly higher than silver and copper, it is still low enough to provide reliable current flow in most applications. The low contact resistance of carbon contacts helps reduce energy waste and improves the overall efficiency of electrical devices.
3. High Current Carrying Capacity
Carbon contacts are capable of carrying high electrical currents without suffering damage or degradation. This is due to their excellent thermal conductivity and ability to dissipate heat effectively. The high current carrying capacity of carbon contacts makes them suitable for use in high-power applications, such as electric motors, generators, and power distribution systems.
The following table shows the typical current carrying capacities of different contact materials:
Contact Material | Current Carrying Capacity (A/mm²) |
---|---|
Carbon | 100-200 |
Copper | 200-400 |
Silver | 400-800 |
Although the current carrying capacity of carbon is lower compared to copper and silver, it is still sufficient for many electrical applications. The combination of high current carrying capacity and high temperature resistance makes carbon contacts a reliable choice for demanding environments.
4. Wear Resistance
Carbon contacts are highly resistant to wear and tear, even under frequent switching cycles. The self-lubricating properties of carbon materials help reduce friction and minimize contact wear over time. This wear resistance translates to longer service life and reduced maintenance requirements for electrical devices using carbon contacts.
In contrast, metal contacts are more susceptible to wear due to their softer nature and tendency to form oxides or other surface contaminants. The table below compares the typical service life of carbon and metal contacts under similar operating conditions:
Contact Material | Service Life (Switching Cycles) |
---|---|
Carbon | 1,000,000 – 10,000,000 |
Silver | 100,000 – 1,000,000 |
Copper | 50,000 – 500,000 |
As evident from the table, carbon contacts can last several times longer than metal contacts, making them a cost-effective solution for applications that require frequent switching or long service life.
5. Chemical Resistance
Carbon contacts are highly resistant to corrosion and chemical attack. Unlike metal contacts, which can easily oxidize or react with environmental pollutants, carbon contacts remain stable and maintain their conductive properties even in harsh chemical environments.
This chemical resistance is particularly useful in applications where the contacts are exposed to corrosive gases, liquids, or other aggressive media. Some examples include:
- Chemical processing plants
- Wastewater treatment facilities
- Marine environments
- Food and beverage industry
The table below summarizes the chemical resistance of carbon contacts compared to common metal contacts:
Contact Material | Chemical Resistance |
---|---|
Carbon | Excellent |
Silver | Good |
Copper | Fair |
The excellent chemical resistance of carbon contacts ensures reliable operation and extends the service life of electrical devices in challenging environments.
Applications of Carbon Contacts
Carbon contacts find use in a wide range of electrical applications due to their unique properties and advantages. Some common applications include:
1. Electric Motors
Carbon brushes, which are a type of carbon contact, are widely used in electric motors to transfer electrical current from the stationary parts (stator) to the rotating parts (rotor). The high current carrying capacity and wear resistance of carbon brushes make them ideal for this application.
2. Circuit Breakers
Carbon contacts are used in circuit breakers to interrupt the flow of electrical current during overload or short-circuit conditions. The high temperature resistance and arc-quenching properties of carbon contacts help prevent damage to the circuit breaker and ensure reliable operation.
3. Relays and Contactors
Carbon contacts are commonly used in relays and contactors, which are devices that switch electrical circuits on and off. The low contact resistance and high wear resistance of carbon contacts provide reliable switching performance and long service life.
4. Welding Equipment
Carbon contacts are used in various types of welding equipment, such as resistance welding machines and spot welders. The high temperature resistance and current carrying capacity of carbon contacts enable them to withstand the intense heat and electrical currents generated during the welding process.
5. High-Temperature Switches
Carbon contacts are employed in switches designed for high-temperature environments, such as those found in industrial ovens, furnaces, and heating systems. The ability of carbon contacts to maintain their properties at elevated temperatures ensures reliable switching operation in these demanding applications.
Manufacturing of Carbon Contacts
The manufacturing process of carbon contacts involves several key steps to ensure the desired properties and performance. The main steps include:
- Raw Material Selection
- High-quality carbon or graphite materials are selected based on the specific requirements of the application.
-
The raw materials are typically in the form of powders or granules.
-
Mixing and Blending
- The carbon or graphite powders are mixed with binders, lubricants, and other additives to achieve the desired composition.
-
The mixing process ensures a homogeneous distribution of the components.
-
Pressing and Molding
- The mixed powder is pressed into the desired shape using high-pressure compression molding techniques.
-
The molding process can produce contacts of various sizes and geometries.
-
Sintering
- The molded contacts are heated to high temperatures (typically above 2000°C) in a controlled atmosphere.
-
During sintering, the binders evaporate, and the carbon particles fuse together to form a solid, dense structure.
-
Machining and Finishing
- After sintering, the carbon contacts are machined to achieve the final dimensions and surface finish.
-
Machining operations may include grinding, drilling, and threading, depending on the specific requirements of the application.
-
Inspection and Testing
- The manufactured carbon contacts undergo rigorous quality control inspections to ensure they meet the specified dimensions, electrical properties, and performance standards.
- Electrical and mechanical tests are conducted to verify the contact resistance, current carrying capacity, and wear resistance of the contacts.
The manufacturing process of carbon contacts requires precise control over the raw materials, processing parameters, and quality assurance measures to ensure consistent and reliable performance in electrical applications.
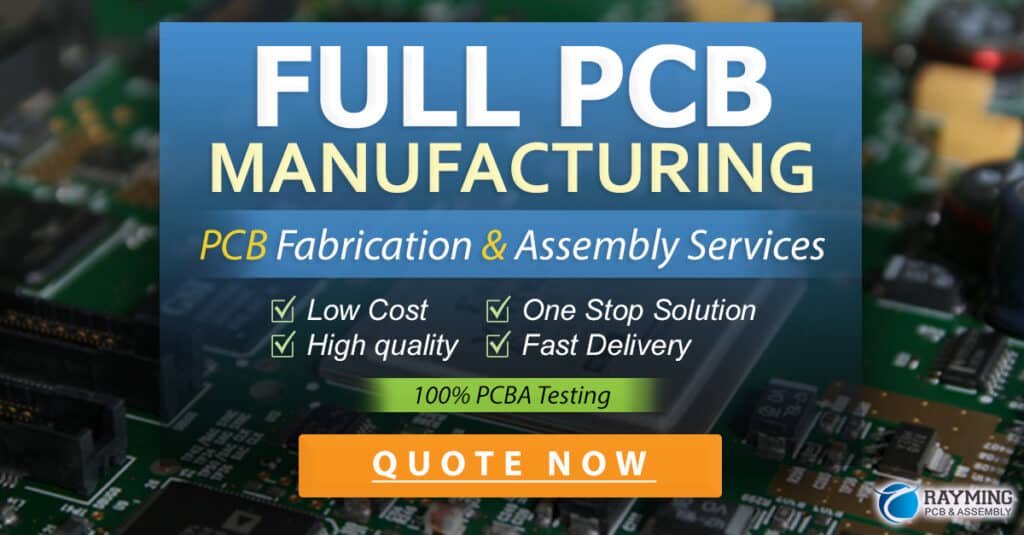
Frequently Asked Questions (FAQ)
1. What is the difference between carbon and graphite contacts?
Carbon and graphite are both allotropes of carbon, but they have slightly different properties. Graphite contacts are made from highly ordered, crystalline forms of carbon, while carbon contacts are made from amorphous or less ordered forms of carbon. Graphite contacts generally have higher electrical conductivity and lower contact resistance compared to carbon contacts. However, carbon contacts are often preferred for their lower cost and easier machinability.
2. Can carbon contacts be used in DC applications?
Yes, carbon contacts can be used in both AC and DC electrical applications. However, the performance of carbon contacts in DC applications may be affected by the polarity of the current. In some cases, the positive and negative contacts may experience uneven wear or erosion due to the unidirectional flow of current. To mitigate this issue, special grades of carbon contacts or reversible polarity designs can be employed.
3. How often do carbon contacts need to be replaced?
The replacement frequency of carbon contacts depends on various factors, such as the application, operating conditions, and the specific grade of carbon material used. In general, carbon contacts have a longer service life compared to metal contacts due to their high wear resistance and self-lubricating properties. However, regular inspections and maintenance are still necessary to ensure optimal performance and prevent premature failure. The manufacturer’s guidelines and application-specific requirements should be followed when determining the replacement interval for carbon contacts.
4. Are carbon contacts environmentally friendly?
Carbon contacts are generally considered environmentally friendly compared to metal contacts. Carbon is a naturally occurring element and is abundant in the Earth’s crust. The production of carbon contacts typically involves less energy and fewer harmful chemicals compared to the production of metal contacts. Additionally, carbon contacts do not contain hazardous substances like lead or cadmium, which are sometimes used in metal contacts. When disposed of properly, carbon contacts have minimal environmental impact.
5. Can carbon contacts be used in high-voltage applications?
Yes, carbon contacts can be used in high-voltage applications, but special considerations must be taken. High-voltage applications require contacts with excellent arc-quenching properties and the ability to withstand high electrical stresses. Special grades of carbon materials, such as metal-impregnated carbon or resin-bonded carbon, are often used in high-voltage contacts to enhance their performance. These grades offer improved arc resistance, higher mechanical strength, and better erosion resistance compared to standard carbon grades. Proper design and selection of carbon contacts are crucial for reliable operation in high-voltage environments.
Conclusion
Carbon contacts are a versatile and reliable choice for electrical applications that require high temperature resistance, low contact resistance, high current carrying capacity, wear resistance, and chemical resistance. These unique properties make carbon contacts suitable for a wide range of applications, including electric motors, circuit breakers, relays, welding equipment, and high-temperature switches.
The manufacturing process of carbon contacts involves careful selection of raw materials, mixing, molding, sintering, machining, and quality control measures to ensure consistent and reliable performance. Proper selection and maintenance of carbon contacts are essential for optimal performance and long service life in electrical devices.
As technology advances and new challenges arise in electrical engineering, carbon contacts continue to play a crucial role in enabling reliable and efficient power transmission. With their exceptional properties and environmental friendliness, carbon contacts are poised to remain a preferred choice for electrical contacts in various industries for years to come.
Leave a Reply