Introduction to 8 Layer PCB Stackup
An 8 layer PCB stackup is a complex printed circuit board configuration that consists of eight conductive layers laminated together with insulating material. This type of PCB offers numerous advantages over simpler designs, including increased routing density, improved signal integrity, and better electromagnetic compatibility (EMC) performance. As technology advances and electronic devices become more sophisticated, understanding the principles and best practices of 8 layer PCB stackup design becomes increasingly important for engineers and manufacturers.
In this comprehensive guide, we will delve into the intricacies of 8 layer PCB stackups, exploring their structure, benefits, design considerations, and manufacturing processes. By the end of this article, you will have a solid foundation in 8 layer PCB stackup design and be well-equipped to create high-quality, reliable printed circuit boards for your projects.
The Structure of an 8 Layer PCB Stackup
Layer Arrangement
A typical 8 layer PCB stackup consists of the following layers, from top to bottom:
- Top Layer (Signal)
- Ground Plane
- Signal Layer 2
- Signal Layer 3
- Power Plane
- Signal Layer 4
- Signal Layer 5
- Bottom Layer (Signal)
Between each conductive layer, there is an insulating layer, typically made of FR-4 material. The thickness of the insulating layers may vary depending on the specific requirements of the PCB design.
Signal Layers
The signal layers in an 8 layer PCB stackup are responsible for carrying the electrical signals between components. These layers are typically arranged in pairs, with one layer dedicated to horizontal routing and the other to vertical routing. This arrangement helps minimize crosstalk and improves signal integrity.
Power and Ground Planes
The power and ground planes in an 8 layer PCB stackup serve several important functions. First, they provide a stable reference voltage for the signal layers, reducing noise and improving signal quality. Second, they act as a shield between signal layers, minimizing electromagnetic interference (EMI) and crosstalk. Finally, they help distribute power evenly across the PCB, ensuring that all components receive the necessary voltage and current.
Benefits of 8 Layer PCB Stackup
Increased Routing Density
One of the primary advantages of an 8 layer PCB stackup is the increased routing density it offers. With eight conductive layers available, designers have more space to route traces and place components. This is particularly beneficial for complex designs with high component counts or limited board space.
Improved Signal Integrity
The alternating signal and plane layers in an 8 layer PCB stackup help maintain signal integrity by minimizing crosstalk and EMI. The power and ground planes act as shields between signal layers, reducing the impact of electromagnetic interference on sensitive signals. Additionally, the use of controlled impedance traces and proper termination techniques further enhances signal quality.
Better EMC Performance
The inherent shielding properties of an 8 layer PCB stackup make it an excellent choice for applications that require strong electromagnetic compatibility (EMC) performance. The power and ground planes help contain electromagnetic emissions, reducing the likelihood of interference with other electronic devices. This is particularly important for products that must meet strict EMC regulations, such as medical equipment or automotive electronics.
Improved Thermal Management
An 8 layer PCB stackup offers better thermal management compared to simpler designs. The increased number of layers allows for more efficient heat dissipation, as the copper in the power and ground planes helps conduct heat away from components. This can lead to improved reliability and longer product life, especially in high-power applications.
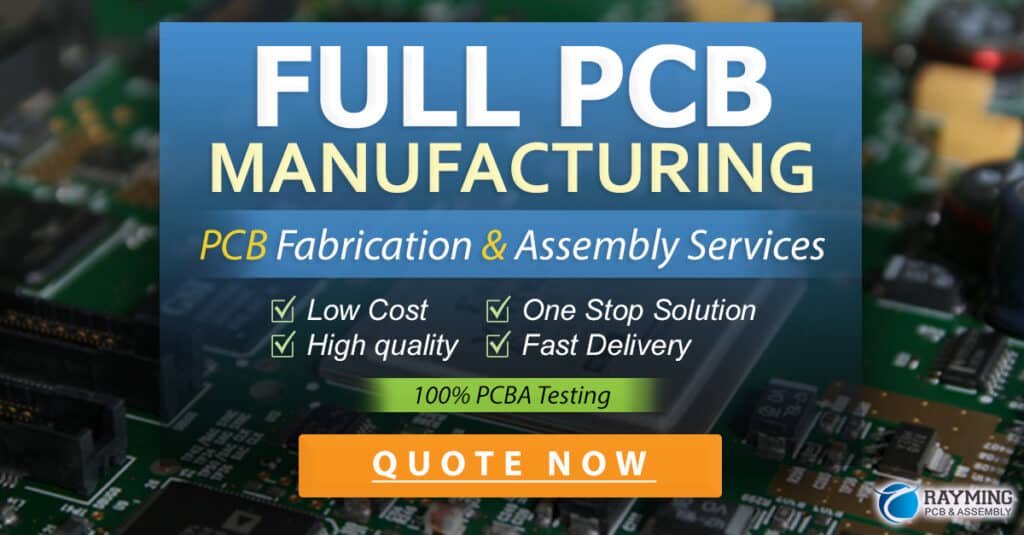
Design Considerations for 8 Layer PCB Stackup
Material Selection
Choosing the right materials is crucial for the success of an 8 layer PCB stackup design. The most common base material for PCBs is FR-4, a glass-reinforced epoxy laminate. However, for high-speed or high-frequency applications, designers may opt for low-loss materials like Rogers or Isola. These materials offer better dielectric properties and help maintain signal integrity at higher frequencies.
Trace Width and Spacing
Proper trace width and spacing are essential for maintaining signal integrity and preventing crosstalk in an 8 layer PCB stackup. Designers must carefully calculate the optimal trace width based on factors such as the desired impedance, current carrying capacity, and manufacturing constraints. Trace spacing should also be considered to minimize crosstalk and ensure manufacturability.
Via Placement and Design
Vias are an integral part of any multi-layer PCB design, as they allow signals to travel between layers. In an 8 layer PCB stackup, via placement and design require special attention to ensure signal integrity and manufacturability. Designers should consider factors such as via size, pad size, and anti-pad size to minimize the impact of vias on signal quality and prevent manufacturing issues.
Impedance Control
Controlling impedance is critical for maintaining signal integrity in an 8 layer PCB stackup, particularly for high-speed designs. Designers must carefully select the dielectric materials and calculate the appropriate trace widths and spacings to achieve the desired impedance. Common impedance values for high-speed designs include 50 ohms for single-ended signals and 100 ohms for differential pairs.
Manufacturing Processes for 8 Layer PCB Stackup
Lamination
The lamination process is a critical step in the manufacturing of an 8 layer PCB stackup. During lamination, the individual layers of the PCB are bonded together under high temperature and pressure. Proper lamination ensures that the layers are securely bonded and free of voids or delamination, which can lead to reliability issues.
Drilling
After lamination, the PCB undergoes a drilling process to create the necessary holes for vias and component mounting. In an 8 layer PCB stackup, the drilling process requires high precision to ensure that the holes are properly aligned and sized. Modern PCB manufacturing facilities use computer-controlled drilling machines to achieve the necessary accuracy and repeatability.
Plating
Once the holes are drilled, the PCB undergoes a plating process to create the electrical connections between layers. This typically involves electroless copper plating, followed by electrolytic copper plating to build up the necessary thickness. The plating process also helps to protect the exposed copper from oxidation and ensures good solderability.
Etching
The etching process removes the unwanted copper from the PCB, leaving only the desired traces and features. In an 8 layer PCB stackup, the etching process must be carefully controlled to ensure that the traces are properly formed and free of defects. Modern PCB manufacturing facilities use advanced etching techniques, such as pattern plating or differential etching, to achieve high-quality results.
Solder Mask and Silkscreen
The final steps in the manufacturing process for an 8 layer PCB stackup involve the application of solder mask and silkscreen. The solder mask is a protective coating that covers the copper traces, leaving only the exposed pads for component soldering. The silkscreen is a printed layer that provides labels and markings for components and other features on the PCB. Both solder mask and silkscreen play important roles in the overall functionality and appearance of the finished PCB.
Frequently Asked Questions (FAQ)
1. What is the typical thickness of an 8 layer PCB?
The typical thickness of an 8 layer PCB can range from 0.093 inches (2.36 mm) to 0.125 inches (3.18 mm), depending on the specific requirements of the design. The thickness is largely determined by the thickness of the individual layers and the insulating material used between them.
2. Can an 8 layer PCB stackup be used for high-frequency applications?
Yes, an 8 layer PCB stackup can be used for high-frequency applications. However, designers must carefully select the appropriate materials, such as low-loss dielectrics, and employ proper design techniques, such as controlled impedance and effective shielding, to ensure optimal performance at high frequencies.
3. How does the cost of an 8 layer PCB compare to simpler designs?
An 8 layer PCB stackup is generally more expensive than simpler designs due to the increased complexity of the manufacturing process and the higher material costs. However, the improved performance and functionality offered by an 8 layer PCB can often justify the additional cost, particularly for advanced applications.
4. What are some common applications for 8 layer PCB stackups?
Some common applications for 8 layer PCB stackups include:
- High-speed digital devices
- Telecommunications equipment
- Medical devices
- Aerospace and defense systems
- Automotive electronics
- Industrial control systems
5. Are there any special considerations for assembly with 8 layer PCBs?
Yes, assembling 8 layer PCBs requires careful attention to several factors, such as component placement, soldering techniques, and thermal management. Designers should work closely with the assembly team to ensure that the PCB is properly assembled and tested, minimizing the risk of defects or reliability issues.
Conclusion
An 8 layer PCB stackup is a powerful tool for creating high-performance, reliable electronic devices. By understanding the structure, benefits, design considerations, and manufacturing processes involved in 8 layer PCB stackups, engineers and manufacturers can create printed circuit boards that meet the demands of today’s advanced applications.
As technology continues to evolve, the importance of effective PCB design and manufacturing will only continue to grow. By staying informed about the latest techniques and best practices, designers and manufacturers can ensure that their products remain competitive and deliver the performance and reliability that customers expect.
Leave a Reply