What is Front-End Data Optimization?
Front-end data optimization is the process of preparing and refining the data required for PCB assembly before the manufacturing process begins. This data includes:
- Design Files: The PCB design files, such as Gerber files, ODB++, or IPC-2581, contain the layout and specifications of the PCB.
- Bill of Materials (BOM): The BOM is a comprehensive list of all the components required to assemble the PCB, including their quantities, part numbers, and specifications.
- Assembly Instructions: These instructions provide detailed guidance on how to assemble the PCB, including the placement of components, soldering techniques, and any special requirements.
The goal of front-end data optimization is to ensure that all this data is accurate, complete, and optimized for the manufacturing process. This involves reviewing and verifying the data, identifying and resolving any issues or discrepancies, and making any necessary adjustments to improve the efficiency and quality of the assembly process.
The Benefits of Front-End Data Optimization
Improved Quality and Reliability
One of the primary benefits of front-end data optimization is improved quality and reliability of the assembled PCBs. By ensuring that the design files, BOM, and assembly instructions are accurate and complete, manufacturers can reduce the risk of errors and defects in the final product. This can help to improve the overall quality and reliability of the PCBs, which is critical for applications where failure is not an option, such as in aerospace, medical devices, and automotive systems.
Increased Efficiency and Productivity
Front-end data optimization can also help to increase the efficiency and productivity of the PCB assembly process. By identifying and resolving any issues or discrepancies in the data before the manufacturing process begins, manufacturers can avoid delays and downtime caused by incorrect or incomplete information. This can help to streamline the assembly process, reduce cycle times, and increase throughput, ultimately leading to faster time-to-market and lower production costs.
Reduced Costs and Waste
Another benefit of front-end data optimization is reduced costs and waste in the PCB assembly process. By ensuring that the BOM is accurate and complete, manufacturers can avoid purchasing excess or incorrect components, which can lead to waste and additional costs. Additionally, by optimizing the design files and assembly instructions, manufacturers can reduce the risk of errors and defects, which can result in costly rework or scrap.
Enhanced Communication and Collaboration
Front-end data optimization also promotes enhanced communication and collaboration between the various stakeholders involved in the PCB assembly process, including designers, engineers, suppliers, and manufacturers. By establishing clear and consistent data standards and processes, all parties can work together more effectively to ensure the success of the project. This can help to foster a culture of continuous improvement and innovation, leading to better products and services for customers.
Best Practices for Front-End Data Optimization
To achieve the benefits of front-end data optimization, manufacturers should follow these best practices:
-
Establish Clear Data Standards: Define clear and consistent standards for design files, BOMs, and assembly instructions to ensure that all data is accurate, complete, and optimized for the manufacturing process.
-
Use Automated Tools: Leverage automated tools and software to streamline the data preparation and verification process, such as CAD/CAM systems, BOM management tools, and data validation software.
-
Collaborate with Stakeholders: Work closely with designers, engineers, suppliers, and other stakeholders to ensure that all data is accurate and complete, and to resolve any issues or discrepancies in a timely manner.
-
Conduct Regular Reviews and Audits: Regularly review and audit the data to ensure that it remains accurate and up-to-date, and to identify any opportunities for improvement.
-
Provide Training and Support: Provide training and support to all stakeholders involved in the PCB assembly process to ensure that they understand the importance of front-end data optimization and how to achieve it.
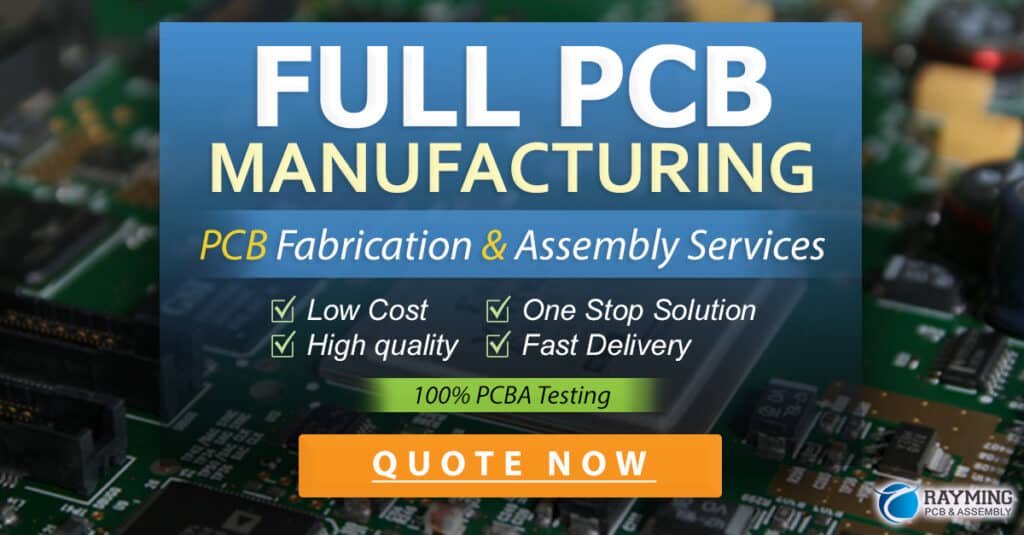
The Role of Automation in Front-End Data Optimization
Automation plays an increasingly important role in front-end data optimization, helping manufacturers to streamline and optimize the data preparation and verification process. Some of the key benefits of automation include:
-
Increased Accuracy and Consistency: Automated tools can help to ensure that all data is accurate and consistent, reducing the risk of errors and discrepancies.
-
Faster Processing Times: Automated tools can process and verify data much faster than manual methods, helping to reduce cycle times and increase throughput.
-
Improved Traceability and Auditability: Automated tools can provide a detailed record of all data changes and updates, improving traceability and auditability for compliance and quality control purposes.
-
Enhanced Collaboration and Communication: Automated tools can facilitate collaboration and communication between stakeholders, allowing for real-time data sharing and updates.
Some of the key automated tools and software used in front-end data optimization include:
Tool/Software | Description |
---|---|
CAD/CAM Systems | Computer-aided design and manufacturing systems used to create and optimize PCB design files. |
BOM Management Tools | Software used to create, manage, and optimize BOMs, ensuring accuracy and completeness. |
Data Validation Software | Tools used to validate and verify design files, BOMs, and assembly instructions, identifying any issues or discrepancies. |
Product Lifecycle Management (PLM) Systems | Comprehensive systems used to manage all aspects of the product lifecycle, including design, manufacturing, and supply chain management. |
By leveraging these automated tools and software, manufacturers can significantly improve the efficiency and effectiveness of their front-end data optimization processes, ultimately leading to better quality, reliability, and profitability in PCB assembly.
Frequently Asked Questions (FAQ)
1. What is the difference between design files and BOMs in PCB assembly?
Design files, such as Gerber files or ODB++, contain the layout and specifications of the PCB, while BOMs (Bill of Materials) are comprehensive lists of all the components required to assemble the PCB, including their quantities, part numbers, and specifications.
2. How can front-end data optimization help to reduce costs in PCB assembly?
Front-end data optimization can help to reduce costs in PCB assembly by ensuring that the BOM is accurate and complete, avoiding the purchase of excess or incorrect components. Additionally, by optimizing the design files and assembly instructions, manufacturers can reduce the risk of errors and defects, minimizing costly rework or scrap.
3. What are some of the key automated tools used in front-end data optimization?
Some of the key automated tools used in front-end data optimization include CAD/CAM systems for creating and optimizing PCB design files, BOM management tools for ensuring BOM accuracy and completeness, data validation software for identifying issues or discrepancies, and Product Lifecycle Management (PLM) systems for managing all aspects of the product lifecycle.
4. How can manufacturers ensure that all stakeholders are involved in the front-end data optimization process?
Manufacturers can ensure that all stakeholders are involved in the front-end data optimization process by establishing clear communication channels and collaboration platforms, providing training and support to all parties, and regularly reviewing and auditing the data to identify any opportunities for improvement.
5. What are the benefits of using automated tools in front-end data optimization?
The benefits of using automated tools in front-end data optimization include increased accuracy and consistency, faster processing times, improved traceability and auditability, and enhanced collaboration and communication between stakeholders. These benefits ultimately lead to better quality, reliability, and profitability in PCB assembly.
Conclusion
Front-end data optimization is a critical process in PCB assembly that can significantly impact the quality, reliability, and profitability of the final product. By ensuring that all the necessary data, including design files, BOMs, and assembly instructions, are accurate, complete, and optimized for the manufacturing process, manufacturers can reduce the risk of errors and defects, increase efficiency and productivity, and minimize costs and waste.
To achieve the benefits of front-end data optimization, manufacturers should establish clear data standards, use automated tools and software, collaborate with stakeholders, conduct regular reviews and audits, and provide training and support to all parties involved. By following these best practices and leveraging the power of automation, manufacturers can streamline their front-end data optimization processes and achieve better results in PCB assembly.
As the electronics industry continues to evolve and become more complex, the importance of front-end data optimization will only continue to grow. By investing in this critical process and adopting best practices and automated tools, manufacturers can position themselves for success in an increasingly competitive and demanding market.
Leave a Reply