Introduction to PCB Manufacturing Tolerances
Printed Circuit Boards (PCBs) are essential components in modern electronics, providing a platform for interconnecting electronic components. The manufacturing process of PCBs involves several critical parameters that must be carefully controlled to ensure the proper functioning and reliability of the final product. Among these parameters, track width and isolation gap tolerances play a crucial role in determining the performance and manufacturability of a PCB.
What are Track Width and Isolation Gap Tolerances?
Track width refers to the width of the copper traces on a PCB, while isolation gap represents the minimum distance between two adjacent copper features. These tolerances are specified by the PCB designer and must be adhered to during the manufacturing process to ensure the desired electrical characteristics and prevent short circuits or signal integrity issues.
Importance of Track-Isolation Tolerances
Maintaining proper track width and isolation gap tolerances is essential for several reasons:
-
Signal Integrity: Adequate track width ensures low resistance and minimal signal loss, while sufficient isolation gap prevents crosstalk and electromagnetic interference between adjacent traces.
-
Manufacturing Feasibility: Overly narrow tracks or isolation gaps can be challenging to manufacture consistently, leading to increased production costs and lower yields.
-
Reliability: Proper tolerances help prevent short circuits, open circuits, and other defects that can compromise the reliability of the PCB.
Factors Affecting Track-Isolation Tolerances
Several factors influence the achievable track width and isolation gap tolerances in PCB manufacturing:
PCB Material
The choice of PCB material, such as FR-4, high-frequency laminates, or flexible substrates, can impact the minimum achievable feature sizes. Some materials may have limitations on the smallest track width or isolation gap that can be reliably manufactured.
Copper Thickness
The thickness of the copper layer on the PCB affects the ability to achieve narrow tracks and isolation gaps. Thicker copper layers require wider minimum feature sizes to ensure proper etching and avoid undercutting.
Manufacturing Process
The PCB manufacturing process, such as etching, plating, or laser direct imaging (LDI), can influence the achievable tolerances. Advanced processes like LDI enable finer feature sizes compared to traditional photolithography.
PCB Complexity
The overall complexity of the PCB design, including the number of layers, via density, and component placement, can impact the achievable tolerances. High-density designs may require tighter control over track width and isolation gap to accommodate all the necessary features.
Industry Standards for Track-Isolation Tolerances
Various industry standards provide guidelines for track width and isolation gap tolerances in PCB manufacturing. These standards ensure consistency and reliability across different manufacturers and applications.
IPC-2221
The IPC-2221 standard, “Generic Standard on Printed Board Design,” provides recommendations for minimum track width and isolation gap based on the PCB class and copper thickness. It defines three classes of PCBs:
Class | Description |
---|---|
Class 1 | General Electronic Products |
Class 2 | Dedicated Service Electronic Products |
Class 3 | High Reliability Electronic Products |
The standard provides tables with minimum track width and isolation gap values for each class and various copper thicknesses.
IPC-6012
The IPC-6012 standard, “Qualification and Performance Specification for Rigid Printed Boards,” defines requirements for PCB fabrication, including tolerances for track width and isolation gap. It specifies different performance classes based on the intended end-use of the PCB.
Manufacturer-Specific Guidelines
PCB manufacturers often provide their own design guidelines and capabilities, which may vary depending on their equipment, processes, and experience. It is essential to consult with the chosen manufacturer to understand their specific tolerances and design rules.
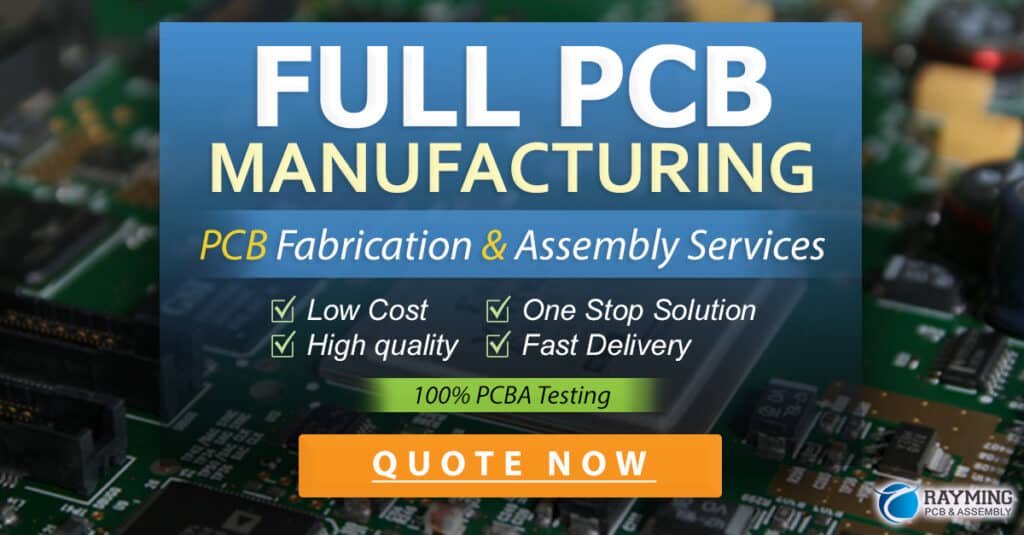
Designing for Manufacturability
To ensure the successful manufacturing of a PCB with appropriate track-isolation tolerances, designers should follow these best practices:
-
Understand the Manufacturing Process: Familiarize yourself with the capabilities and limitations of the chosen PCB manufacturing process to design within its constraints.
-
Follow Design Rules: Adhere to the design rules provided by the PCB manufacturer, including minimum track width, isolation gap, via size, and drill diameter.
-
Use CAD Tools: Utilize PCB design software with built-in design rule checks (DRC) to validate the design against the specified tolerances and identify any violations.
-
Communicate with the Manufacturer: Engage in open communication with the PCB manufacturer to clarify any design requirements, discuss feasibility, and resolve any potential issues early in the design process.
-
Consider Test Coupons: Include test coupons or design rule check (DRC) features on the PCB panel to verify the manufacturability and adherence to the specified tolerances.
Common Issues and Solutions
Despite careful design and manufacturing, issues related to track width and isolation gap tolerances can still arise. Some common problems and their solutions include:
-
Overetching: Overetching occurs when the etching process removes more copper than intended, resulting in narrower tracks or larger isolation gaps. This can be addressed by adjusting the etching parameters or using a more precise etching method.
-
Underetching: Underetching happens when the etching process does not remove enough copper, leading to wider tracks or smaller isolation gaps. Increasing the etching time or optimizing the etching chemistry can help resolve this issue.
-
Copper Thickness Variation: Inconsistent copper thickness across the PCB can affect the achievable tolerances. Proper process control and monitoring during the plating stage can minimize this variation.
-
Artwork Scaling: Inaccuracies in artwork scaling or registration can result in deviations from the desired track width and isolation gap. Ensuring accurate artwork generation and alignment during the manufacturing process is crucial.
Frequently Asked Questions (FAQ)
1. What is the minimum track width and isolation gap achievable in PCB manufacturing?
The minimum achievable track width and isolation gap depend on several factors, including the PCB material, copper thickness, manufacturing process, and PCB complexity. Typically, for a standard FR-4 PCB with 1 oz copper, a minimum track width of 0.1 mm (4 mil) and an isolation gap of 0.1 mm (4 mil) can be reliably manufactured. However, advanced processes and materials can enable even finer feature sizes.
2. How do I choose the appropriate track width and isolation gap for my PCB design?
When selecting track width and isolation gap values, consider the following factors:
– Electrical requirements: Ensure that the track width is sufficient to carry the required current without excessive resistance or heat generation. The isolation gap should be adequate to prevent crosstalk and maintain signal integrity.
– Manufacturing capabilities: Consult with your PCB manufacturer to understand their specific design rules and tolerances. Choose values that are within their capabilities to ensure reliable manufacturing.
– Industry standards: Refer to relevant industry standards, such as IPC-2221 or IPC-6012, for guidance on recommended track width and isolation gap values based on the PCB class and copper thickness.
3. What happens if the track width or isolation gap is too small?
If the track width or isolation gap is too small, several issues can arise:
– Manufacturing difficulties: Overly narrow features can be challenging to manufacture consistently, leading to a higher rate of defects and lower yields.
– Electrical problems: Insufficient track width can result in high resistance, causing signal loss or excessive heating. Inadequate isolation gap can lead to crosstalk, signal integrity issues, or even short circuits.
– Reliability concerns: PCBs with features that are too small may be more susceptible to damage during handling, assembly, or operation, compromising their long-term reliability.
4. Can I use different track widths and isolation gaps on the same PCB?
Yes, it is common to use different track widths and isolation gaps within the same PCB design. This is often necessary to accommodate various electrical requirements, such as power traces requiring wider tracks than signal traces. However, it is essential to ensure that all the values used are within the manufacturing capabilities and adhere to the design rules provided by the PCB manufacturer.
5. How can I verify that my PCB design meets the specified track-isolation tolerances?
To verify that your PCB design meets the specified track-isolation tolerances, follow these steps:
1. Define the design rules: Clearly specify the desired track width, isolation gap, and other relevant parameters in your PCB design software.
2. Perform design rule checks (DRC): Use the built-in DRC tools in your PCB design software to check for any violations of the specified tolerances. The DRC will highlight any areas where the design exceeds the allowed values.
3. Review manufacturer’s feedback: Share your PCB design files with the chosen manufacturer for their review. They will analyze the design and provide feedback on any potential issues or areas that may require modification to meet their manufacturing capabilities.
4. Iterate and refine: Based on the DRC results and manufacturer’s feedback, make necessary adjustments to your design to ensure compliance with the specified tolerances.
5. Verify with test coupons: Include test coupons or DRC features on the PCB panel during manufacturing to validate the adherence to the specified tolerances in the final product.
Conclusion
Understanding and properly specifying track width and isolation gap tolerances is crucial for the successful manufacturing of PCBs. These tolerances impact signal integrity, manufacturability, and reliability of the final product. By considering factors such as PCB material, copper thickness, manufacturing process, and industry standards, designers can make informed decisions when defining track-isolation tolerances.
Collaborating closely with PCB manufacturers, following design rules, and utilizing CAD tools with DRC capabilities are essential practices for ensuring the manufacturability of PCBs within the specified tolerances. Regularly reviewing and refining designs based on manufacturer feedback and test results helps minimize issues and achieve the desired performance and reliability.
As PCB technology continues to advance, the achievable track width and isolation gap tolerances will likely become even smaller, enabling more compact and high-performance designs. Staying updated with the latest industry standards, manufacturing processes, and design techniques will be crucial for designers to create PCBs that meet the ever-increasing demands of modern electronics.
Leave a Reply