What are PCB Hole Tolerances?
PCB hole tolerances refer to the acceptable range of variation in the size of drilled holes on a printed circuit board (PCB). These holes are used for various purposes, such as mounting components, creating vias for electrical connections between layers, and providing mechanical support. Maintaining proper hole tolerances is crucial for ensuring the functionality, reliability, and manufacturability of the PCB.
Importance of PCB Hole Tolerances
Hole tolerances play a vital role in PCB design and manufacturing for several reasons:
-
Component Compatibility: Accurate hole sizes ensure that components can be properly inserted and soldered onto the PCB. If the holes are too small, components may not fit, while oversized holes can lead to poor connections and mechanical instability.
-
Electrical Connectivity: Vias, which are holes that connect different layers of a PCB, must be precisely sized to ensure proper electrical connectivity between layers. Incorrect hole sizes can cause open circuits or short circuits, compromising the functionality of the PCB.
-
Manufacturing Efficiency: Consistent hole sizes throughout the PCB allow for smooth and efficient manufacturing processes, such as drilling, plating, and soldering. Inconsistent or out-of-tolerance holes can lead to production delays, increased costs, and reduced yield.
Factors Affecting PCB Hole Tolerances
Several factors can influence the finished hole size tolerances on a PCB:
Drilling Process
The drilling process is a critical step in PCB manufacturing that directly impacts hole tolerances. Factors such as drill bit size, spindle speed, feed rate, and the condition of the drilling equipment can all affect the accuracy and consistency of the drilled holes.
PCB Material
The type of PCB material can also influence hole tolerances. Different materials, such as FR-4, Rogers, or polyimide, have varying properties that can affect the drilling process. Some materials may be more prone to drill bit wandering or burring, leading to variations in hole sizes.
Plating Process
After drilling, the holes are typically plated with a conductive material, such as copper, to create electrical connections between layers. The plating process can also impact hole tolerances, as the plating thickness can vary depending on factors such as the plating chemistry, current density, and plating time.
Environmental Factors
Environmental conditions, such as temperature and humidity, can also affect PCB hole tolerances. Changes in temperature can cause the PCB material to expand or contract, leading to variations in hole sizes. High humidity can also impact the drilling and plating processes, potentially affecting hole tolerances.
Industry Standards for PCB Hole Tolerances
To ensure consistency and reliability in PCB manufacturing, various industry standards provide guidelines for acceptable hole tolerances. Two widely recognized standards are:
- IPC-6012: Generic Performance Specification for Rigid Printed Boards
- IPC-6013: Qualification and Performance Specification for Flexible/Rigid-Flexible Printed Boards
These standards specify the allowable hole size tolerances based on factors such as the hole diameter, PCB thickness, and the class of the PCB (Class 1, 2, or 3, depending on the intended application and reliability requirements).
IPC-6012 Hole Size Tolerances
IPC-6012 provides the following hole size tolerances for rigid PCBs:
Hole Diameter (mm) | Tolerance (mm) |
---|---|
0.25 – 0.40 | ±0.08 |
0.41 – 0.60 | ±0.10 |
0.61 – 0.80 | ±0.12 |
0.81 – 1.00 | ±0.15 |
1.01 – 1.50 | ±0.20 |
1.51 – 2.00 | ±0.25 |
2.01 – 3.00 | ±0.30 |
3.01 – 4.00 | ±0.35 |
4.01 – 5.00 | ±0.40 |
5.01 – 6.00 | ±0.45 |
IPC-6013 Hole Size Tolerances
IPC-6013 provides similar hole size tolerances for flexible and rigid-flexible PCBs:
Hole Diameter (mm) | Tolerance (mm) |
---|---|
0.25 – 0.40 | ±0.08 |
0.41 – 0.60 | ±0.10 |
0.61 – 0.80 | ±0.12 |
0.81 – 1.00 | ±0.15 |
1.01 – 1.50 | ±0.20 |
1.51 – 2.00 | ±0.25 |
2.01 – 3.00 | ±0.30 |
It’s essential for PCB designers and manufacturers to adhere to these industry standards to ensure the quality and reliability of the finished product.
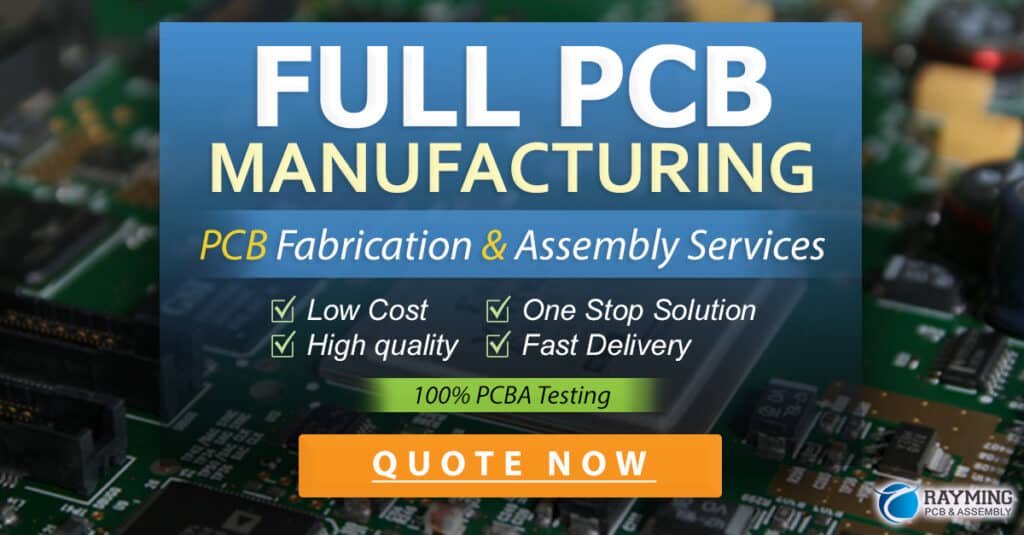
Managing PCB Hole Tolerances in Design and Manufacturing
To effectively manage PCB hole tolerances, designers and manufacturers should consider the following best practices:
Design Considerations
-
Specify appropriate hole sizes: When designing a PCB, ensure that the specified hole sizes are compatible with the components and manufacturing processes. Consider the tolerances provided by the industry standards and communicate them clearly in the PCB design files.
-
Provide adequate clearances: Allow for sufficient clearances around holes to accommodate any potential variations in hole sizes. This can help prevent issues such as component misalignment or shorts caused by hole size deviations.
-
Use standard drill sizes: Whenever possible, use standard drill sizes in your PCB design. This can help reduce the need for custom drill bits, improving manufacturing efficiency and minimizing the risk of hole size variations.
Manufacturing Considerations
-
Regular equipment maintenance: Ensure that the drilling and plating equipment is regularly maintained and calibrated to minimize hole size variations. This includes replacing worn drill bits, adjusting spindle speeds and feed rates, and monitoring the plating process parameters.
-
Quality control measures: Implement robust quality control measures throughout the manufacturing process to monitor and verify hole sizes. This can include using automated optical inspection (AOI) systems, conducting periodic hole size measurements, and performing cross-sectional analysis to assess plating thickness and uniformity.
-
Material selection: Choose PCB materials that are compatible with the drilling and plating processes, and have predictable behavior under different environmental conditions. This can help minimize hole size variations caused by material-related factors.
-
Process optimization: Continuously optimize the drilling and plating processes to improve hole size consistency. This may involve fine-tuning process parameters, implementing statistical process control (SPC) techniques, and conducting regular process capability studies.
Frequently Asked Questions (FAQ)
-
What is the importance of maintaining proper PCB hole tolerances?
Maintaining proper PCB hole tolerances is crucial for ensuring component compatibility, electrical connectivity, and manufacturing efficiency. Incorrect hole sizes can lead to issues such as component misfit, open or short circuits, and production delays. -
What factors can affect PCB hole tolerances?
Several factors can affect PCB hole tolerances, including the drilling process (drill bit size, spindle speed, feed rate), PCB material properties, plating process variations, and environmental conditions (temperature and humidity). -
What are the industry standards for PCB hole tolerances?
Two widely recognized industry standards for PCB hole tolerances are IPC-6012 (for rigid PCBs) and IPC-6013 (for flexible and rigid-flexible PCBs). These standards specify allowable hole size tolerances based on hole diameter, PCB thickness, and the class of the PCB. -
How can PCB designers manage hole tolerances?
PCB designers can manage hole tolerances by specifying appropriate hole sizes, providing adequate clearances around holes, and using standard drill sizes whenever possible. Clear communication of hole tolerances in the PCB design files is also essential. -
What can PCB manufacturers do to control hole size variations?
PCB manufacturers can control hole size variations by implementing regular equipment maintenance, robust quality control measures, careful material selection, and continuous process optimization. This includes monitoring drilling and plating processes, conducting periodic hole size measurements, and using statistical process control techniques.
Conclusion
Understanding and managing PCB hole tolerances is essential for ensuring the functionality, reliability, and manufacturability of printed circuit boards. By considering factors such as drilling processes, PCB materials, plating variations, and environmental conditions, designers and manufacturers can work together to minimize hole size variations and meet industry standards.
Effective management of PCB hole tolerances involves a combination of design considerations, such as specifying appropriate hole sizes and clearances, and manufacturing best practices, including regular equipment maintenance, quality control measures, and process optimization.
By adhering to industry standards like IPC-6012 and IPC-6013, and continuously improving design and manufacturing processes, the electronics industry can produce high-quality, reliable PCBs that meet the ever-increasing demands of modern applications.
Leave a Reply