Understanding Copper Thickness and Its Importance in PCB Manufacturing
Printed Circuit Boards (PCBs) are the backbone of modern electronic devices, connecting and supporting various components to ensure proper functionality. One crucial aspect of PCB manufacturing is the copper thickness, which plays a vital role in determining the board’s electrical and thermal properties. This article will delve into the concept of Copper Thickness Tolerances on PCBs, exploring their significance, measurement techniques, and the factors that influence them.
What is Copper Thickness in PCBs?
Copper thickness, also known as copper weight or copper density, refers to the amount of copper deposited on the surface of a PCB substrate. It is typically measured in ounces per square foot (oz/ft²) or microns (μm). The most common copper thicknesses used in PCB manufacturing are 1 oz/ft² (35 μm) and 2 oz/ft² (70 μm), although thicker or thinner copper layers may be used depending on the specific requirements of the application.
The copper layer serves several critical functions in a PCB:
- Conducting electrical signals between components
- Providing a heat dissipation path for temperature-sensitive components
- Offering mechanical support for the components mounted on the board
The Significance of Copper Thickness Tolerances
Maintaining accurate copper thickness tolerances is essential for ensuring the proper functioning and reliability of electronic devices. Deviations from the specified copper thickness can lead to various issues, such as:
-
Altered electrical characteristics: Copper thickness directly affects the resistance and current-carrying capacity of the PCB traces. If the copper is too thin, it may not be able to handle the required current, leading to overheating and potential failure. On the other hand, if the copper is too thick, it can cause impedance mismatches and signal integrity issues.
-
Thermal management challenges: Copper plays a crucial role in dissipating heat generated by components on the PCB. Insufficient copper thickness can result in inadequate heat dissipation, causing components to overheat and potentially fail prematurely.
-
Manufacturing difficulties: Copper thickness tolerances also impact the manufacturability of PCBs. Excessive copper thickness can make it challenging to etch fine features accurately, while insufficient thickness may lead to poor adhesion between the copper and the substrate.
Factors Influencing Copper Thickness Tolerances
Several factors can influence the copper thickness tolerances on a PCB, including:
PCB Manufacturing Process
The PCB manufacturing process itself can introduce variations in copper thickness. The two primary methods for depositing copper on a PCB substrate are electroplating and foil lamination.
-
Electroplating: In this process, copper is deposited onto the substrate through an electrolytic process. Factors such as the composition of the plating solution, current density, and plating time can affect the uniformity and thickness of the deposited copper layer.
-
Foil lamination: This method involves bonding a pre-formed copper foil to the substrate using heat and pressure. The thickness of the copper foil is determined by the manufacturer and is generally more consistent than electroplated copper. However, the lamination process can still introduce some variations in thickness.
Substrate Material and Thickness
The choice of substrate material and its thickness can also impact copper thickness tolerances. Common PCB substrate materials include:
-
FR-4: A glass-reinforced epoxy laminate, FR-4 is the most widely used PCB substrate material. It offers good mechanical and electrical properties, making it suitable for a wide range of applications.
-
High-frequency materials: For applications requiring high-frequency operation, such as RF and microwave devices, specialized substrate materials like Rogers, Teflon, or ceramic-based laminates are used. These materials have different dielectric constants and loss tangents compared to FR-4, which can affect the copper thickness tolerances.
-
Flexible substrates: Flexible PCBs, made from materials like polyimide or polyester, have different thermal expansion properties compared to rigid substrates. This can lead to variations in copper thickness during the manufacturing process.
The thickness of the substrate can also influence copper thickness tolerances. Thinner substrates may be more susceptible to warping or deformation during the copper deposition process, leading to non-uniform copper thickness distribution.
Design Features and Complexity
The design features and complexity of the PCB can also impact copper thickness tolerances. Some of the design-related factors include:
-
Trace width and spacing: Narrow traces and tight spacing between features can make it more challenging to maintain consistent copper thickness. The etching process used to define the traces can introduce variations in copper thickness, particularly in areas with high feature density.
-
Via holes and plated through-holes: The copper plating process used to create via holes and plated through-holes can result in non-uniform copper thickness distribution. The aspect ratio (depth to diameter) of the holes can affect the uniformity of the plating, with higher aspect ratios being more challenging to plate consistently.
-
Copper balancing: In multi-layer PCBs, it is essential to balance the copper distribution across the layers to minimize warping and ensure flatness. Uneven copper distribution can lead to variations in thickness tolerances.
Measuring and Controlling Copper Thickness Tolerances
To ensure that copper thickness tolerances are within acceptable limits, various measurement and control techniques are employed during the PCB manufacturing process.
Measurement Techniques
-
X-ray fluorescence (XRF): XRF is a non-destructive method that uses X-rays to measure the thickness of the copper layer. It works by exciting the atoms in the copper layer and measuring the energy of the emitted X-rays, which is proportional to the thickness of the layer. XRF is widely used for its accuracy and ability to measure copper thickness on both bare and assembled PCBs.
-
Cross-sectional analysis: This destructive method involves cutting a small section of the PCB and examining the cross-section under a microscope. The copper thickness can be measured directly from the cross-sectional image. While this method provides accurate results, it is destructive and not suitable for 100% inspection.
-
Electrical resistance measurement: This technique involves measuring the electrical resistance of a known length of a copper trace. The resistance is proportional to the cross-sectional area of the trace, which is determined by its width and thickness. By comparing the measured resistance to the expected value based on the design specifications, the copper thickness can be estimated. This method is non-destructive but less accurate than XRF or cross-sectional analysis.
Control Techniques
-
Process control: Maintaining tight control over the PCB manufacturing process parameters is essential for minimizing variations in copper thickness. This includes monitoring and controlling factors such as the composition of the plating solution, current density, plating time, and lamination pressure and temperature.
-
Design for manufacturing (DFM): Incorporating DFM principles during the PCB design phase can help minimize copper thickness variations. This involves following guidelines for minimum trace widths, spacing, and via hole sizes, as well as balancing copper distribution across layers in multi-layer boards.
-
Statistical process control (SPC): SPC techniques, such as control charts and process capability analysis, can be used to monitor the copper thickness tolerances and identify any trends or anomalies in the manufacturing process. By analyzing the data collected from measurement techniques like XRF, manufacturers can make necessary adjustments to keep the process within the specified tolerances.
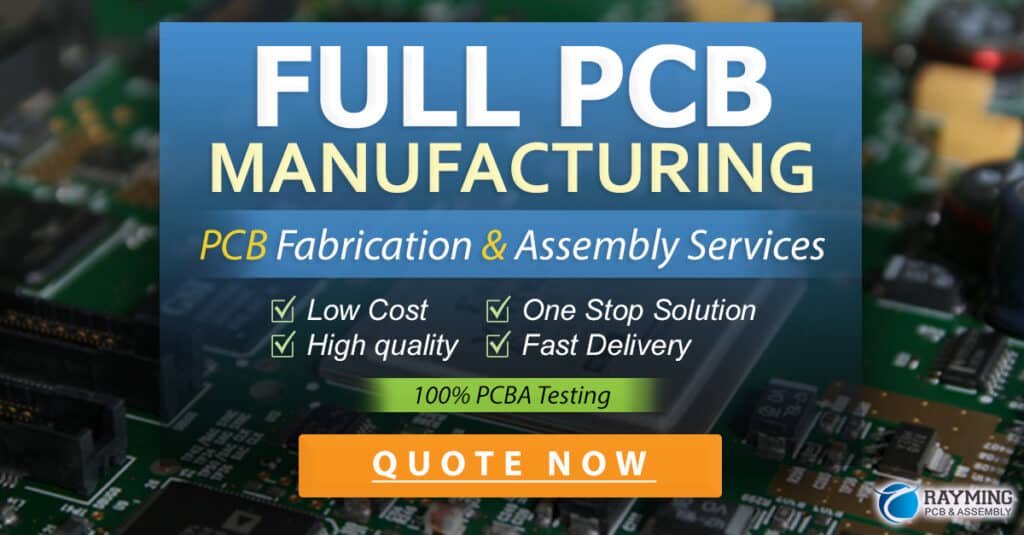
Industry Standards and Specifications
Several industry standards and specifications provide guidelines for copper thickness tolerances on PCBs. Some of the most widely used standards include:
-
IPC-6012: This standard, published by the Association Connecting Electronics Industries (IPC), specifies the requirements for the qualification and performance of rigid printed boards. It includes provisions for copper thickness tolerances based on the class of the PCB and the copper thickness specified.
-
IPC-A-600: This standard provides acceptability criteria for printed circuit boards, including guidelines for copper thickness tolerances. It defines the acceptable range of copper thickness deviations for different copper weights and PCB classes.
-
IPC-4101: This standard specifies the requirements for base materials used in the manufacture of PCBs, including copper foils. It defines the thickness tolerances for copper foils used in PCB manufacturing.
-
MIL-PRF-31032: This specification, published by the US Department of Defense, sets the requirements for printed circuit board and printed wiring board manufacturing for military and aerospace applications. It includes stringent requirements for copper thickness tolerances to ensure reliability and performance in harsh environments.
Copper Thickness and High-Current Applications
In high-current applications, such as power electronics or automotive systems, copper thickness plays a critical role in ensuring the reliable operation of the PCB. Thicker copper layers are often used to accommodate the higher current densities and to provide better thermal management.
For these applications, copper thicknesses can range from 2 oz/ft² (70 μm) to 10 oz/ft² (350 μm) or even higher. The increased copper thickness helps to:
- Reduce the electrical resistance of the traces, minimizing power loss and voltage drop.
- Improve the current-carrying capacity of the traces, allowing them to handle higher currents without overheating.
- Enhance the thermal conductivity of the PCB, helping to dissipate heat more effectively from power-generating components.
However, using thicker copper layers also presents some challenges in terms of manufacturing and design:
-
Etching thicker copper layers requires more time and can lead to undercut profiles, affecting the accuracy of the trace dimensions.
-
Thicker copper can make it more difficult to achieve fine feature resolution, such as narrow traces or small via holes.
-
The increased weight of the thicker copper layers can impact the mechanical properties of the PCB, such as flexibility or vibration resistance.
To address these challenges, PCB manufacturers may employ specialized processes, such as heavy copper plating or sequential lamination, to achieve the desired copper thickness while maintaining acceptable tolerances and feature resolution.
Copper Thickness and High-Frequency Applications
In high-frequency applications, such as RF and microwave devices, the copper thickness on a PCB can have a significant impact on the signal integrity and performance of the circuit. At high frequencies, the skin effect causes the electrical current to flow primarily on the surface of the conductor, rather than through its entire cross-section.
The skin depth, which is the depth at which the current density drops to 1/e (about 37%) of its value at the surface, is inversely proportional to the square root of the frequency. As the frequency increases, the skin depth decreases, and the effective cross-sectional area of the conductor is reduced.
To minimize the impact of the skin effect and ensure good signal integrity, PCBs for high-frequency applications often use thinner copper layers, typically in the range of 0.5 oz/ft² (17 μm) to 1 oz/ft² (35 μm). The thinner copper layer helps to:
-
Reduce the conductor losses, which are proportional to the square root of the frequency and the conductor thickness.
-
Improve the impedance control of the traces, as the characteristic impedance is affected by the trace dimensions and the dielectric properties of the substrate material.
-
Minimize the impact of the skin effect on the signal propagation and reduce the dispersion of the signals.
However, using thinner copper layers also has some drawbacks:
-
Thinner copper has higher electrical resistance, which can lead to increased power loss and voltage drop in the circuit.
-
The current-carrying capacity of the traces is reduced, which can limit the power-handling capability of the PCB.
-
Thinner copper layers are more susceptible to mechanical damage and may require additional protection during handling and assembly.
To address these limitations, PCB designers may use wider traces to compensate for the higher resistance of the thinner copper or employ specialized substrate materials with lower dielectric loss to minimize the overall signal attenuation.
Frequently Asked Questions (FAQ)
-
What is the most common copper thickness used in PCB manufacturing?
The most common copper thicknesses used in PCB manufacturing are 1 oz/ft² (35 μm) and 2 oz/ft² (70 μm). These thicknesses provide a good balance between electrical performance, thermal management, and manufacturability for a wide range of applications. -
How does copper thickness affect the electrical properties of a PCB?
Copper thickness directly affects the electrical resistance and current-carrying capacity of the PCB traces. Thicker copper layers have lower resistance and can handle higher currents without overheating, while thinner copper layers have higher resistance and may be more suitable for high-frequency applications where skin effect is a concern. -
What are the challenges in manufacturing PCBs with thick copper layers?
Manufacturing PCBs with thick copper layers can present challenges such as longer etching times, undercut trace profiles, and difficulty achieving fine feature resolution. Specialized processes, such as heavy copper plating or sequential lamination, may be required to maintain acceptable tolerances and feature accuracy. -
How can PCB designers minimize the impact of copper thickness variations?
PCB designers can minimize the impact of copper thickness variations by following design for manufacturing (DFM) guidelines, such as specifying minimum trace widths and spacing, balancing copper distribution across layers, and considering the limitations of the manufacturing process when selecting copper thicknesses for different applications. -
What industry standards govern copper thickness tolerances on PCBs?
Several industry standards, such as IPC-6012, IPC-A-600, IPC-4101, and MIL-PRF-31032, provide guidelines and specifications for copper thickness tolerances on PCBs. These standards define acceptable ranges of copper thickness deviations based on the PCB class, copper weight, and application requirements.
Conclusion
Copper thickness tolerances play a crucial role in determining the electrical, thermal, and mechanical properties of PCBs. Maintaining tight control over copper thickness is essential for ensuring the proper functioning, reliability, and performance of electronic devices across a wide range of applications, from consumer electronics to high-power and high-frequency systems.
By understanding the factors that influence copper thickness tolerances, employing appropriate measurement and control techniques, and adhering to industry standards and guidelines, PCB manufacturers can consistently produce boards that meet the specific requirements of each application. As electronic devices continue to advance in complexity and performance, the importance of copper thickness tolerances in PCB manufacturing will only continue to grow.
[Table 1: Common Copper Thicknesses and Their Applications]
Copper Thickness | Typical Applications |
---|---|
0.5 oz/ft² (17 μm) | High-frequency, RF, and microwave devices |
1 oz/ft² (35 μm) | General-purpose electronics, digital circuits |
2 oz/ft² (70 μm) | Power electronics, automotive, industrial control |
3 oz/ft² (105 μm) | High-current applications, heavy copper boards |
4 oz/ft² (140 μm) | High-power electronics, solar inverters, electric vehicles |
[Table 2: IPC-6012 Copper Thickness Tolerances for Different PCB Classes]
Copper Weight | Class 1 | Class 2 | Class 3 |
---|---|---|---|
0.5 oz/ft² | ± 20% | ± 10% | ± 10% |
1 oz/ft² | ± 10% | ± 10% | ± 5% |
2 oz/ft² | ± 10% | ± 10% | ± 5% |
3 oz/ft² | ± 10% | ± 10% | ± 5% |
4 oz/ft² | ± 10% | ± 10% | ± 5% |
Note: Class 1 is for general electronic products, Class 2 is for dedicated service electronic products, and Class 3 is for high-reliability electronic products.
Leave a Reply