Understanding BOM and CPL
A Bill of Materials (BOM) and a Component Parts List (CPL) are essential tools used in manufacturing and engineering to keep track of the components and materials required to produce a product. They provide a comprehensive list of all the items needed, along with their quantities, specifications, and sometimes even their costs. Understanding how to create, maintain, and utilize BOMs and CPLs effectively can greatly improve a company’s production process and overall efficiency.
What is a Bill of Materials (BOM)?
A Bill of Materials (BOM) is a structured list of all the components, subassemblies, and raw materials required to manufacture a product. It serves as a blueprint for the production process, ensuring that all necessary parts are accounted for and available when needed. The BOM typically includes the following information for each item:
- Part number or unique identifier
- Description of the part
- Quantity required per unit of the final product
- Unit of measure (e.g., pieces, liters, kilograms)
- References to any subassemblies or higher-level assemblies
BOMs can be created using various formats, such as spreadsheets, databases, or specialized software solutions. They are often hierarchical, with the final product at the top and the individual components and subassemblies listed below in a tree-like structure.
What is a Component Parts List (CPL)?
A Component Parts List (CPL) is similar to a BOM but focuses more on the individual components rather than the entire assembly. It provides a detailed list of all the parts required to build a product, along with their specifications and sometimes even their costs. The CPL is often used in conjunction with the BOM to provide a more granular view of the components needed for production.
A typical CPL includes the following information for each component:
- Part number or unique identifier
- Description of the part
- Specifications (e.g., dimensions, material, color)
- Manufacturer or supplier information
- Cost per unit
- Lead time for procurement
CPLs are essential for effectively managing inventory, ensuring that the right components are available when needed, and keeping track of costs associated with each part.
Creating and Maintaining BOMs and CPLs
Creating and maintaining accurate BOMs and CPLs is crucial for streamlining the production process and avoiding costly mistakes. Here are some tips and best practices for creating and managing these important documents:
1. Use a consistent naming convention
Establish a consistent naming convention for all parts and components to avoid confusion and ensure that everyone in the organization is using the same terminology. This can include using a specific format for part numbers, such as a combination of letters and numbers that indicate the type of part, its size, or its function.
2. Keep BOMs and CPLs updated
As products evolve and change over time, it’s essential to keep BOMs and CPLs up to date to reflect any modifications or improvements. Regularly review and update these documents to ensure that they accurately represent the current state of the product and its components.
3. Collaborate with cross-functional teams
Creating and maintaining BOMs and CPLs should be a collaborative effort involving various departments, such as engineering, procurement, and manufacturing. Encourage open communication and feedback from all stakeholders to ensure that the information in these documents is accurate, complete, and up to date.
4. Use software solutions
Consider using specialized software solutions, such as Product Lifecycle Management (PLM) or Enterprise Resource Planning (ERP) systems, to create and manage BOMs and CPLs. These tools can help automate the process, reduce errors, and ensure that everyone has access to the most current information.
5. Conduct regular audits
Perform regular audits of BOMs and CPLs to verify their accuracy and completeness. This can involve physically checking inventory levels, reviewing supplier information, and comparing the documents against actual production processes to identify any discrepancies or areas for improvement.
Utilizing BOMs and CPLs in Production
Once you have created accurate and up-to-date BOMs and CPLs, it’s important to effectively utilize them in the production process. Here are some ways to leverage these documents to improve efficiency and reduce costs:
1. Materials Requirements Planning (MRP)
Use BOMs and CPLs as inputs for Materials Requirements Planning (MRP) systems to determine the quantities and timing of materials needed for production. MRP systems can help optimize inventory levels, reduce lead times, and minimize the risk of stockouts or overstocking.
Example MRP table:
Part Number | Description | Quantity Required | Lead Time (weeks) | Inventory on Hand | Planned Order Release |
---|---|---|---|---|---|
ABC123 | Component A | 100 | 2 | 50 | Week 3 |
DEF456 | Component B | 200 | 3 | 75 | Week 2 |
GHI789 | Component C | 150 | 1 | 200 | Week 5 |
2. Supplier management
Use CPLs to manage relationships with suppliers, ensuring that they can provide the necessary components in the required quantities and timeframes. Share CPLs with suppliers to communicate your needs and expectations clearly, and work collaboratively to address any issues or concerns.
3. Cost analysis
Utilize BOMs and CPLs to perform cost analysis and identify opportunities for cost savings. By understanding the costs associated with each component and subassembly, you can make informed decisions about sourcing, negotiating with suppliers, or redesigning products to reduce costs.
Example cost analysis table:
Part Number | Description | Quantity per Unit | Cost per Unit | Total Cost |
---|---|---|---|---|
ABC123 | Component A | 2 | $5.00 | $10.00 |
DEF456 | Component B | 1 | $8.00 | $8.00 |
GHI789 | Component C | 3 | $3.00 | $9.00 |
Total Cost per Unit | $27.00 |
4. Quality control
Use BOMs and CPLs as reference documents for quality control processes, ensuring that the correct components are used and that the final product meets the required specifications. By comparing the actual components and quantities used in production against the BOM and CPL, you can identify and address any quality issues or deviations from the intended design.
5. Continuous improvement
Regularly review and analyze BOMs and CPLs to identify opportunities for continuous improvement in the production process. This can involve streamlining the number of components used, standardizing parts across multiple products, or identifying alternative suppliers or materials that can improve quality or reduce costs.
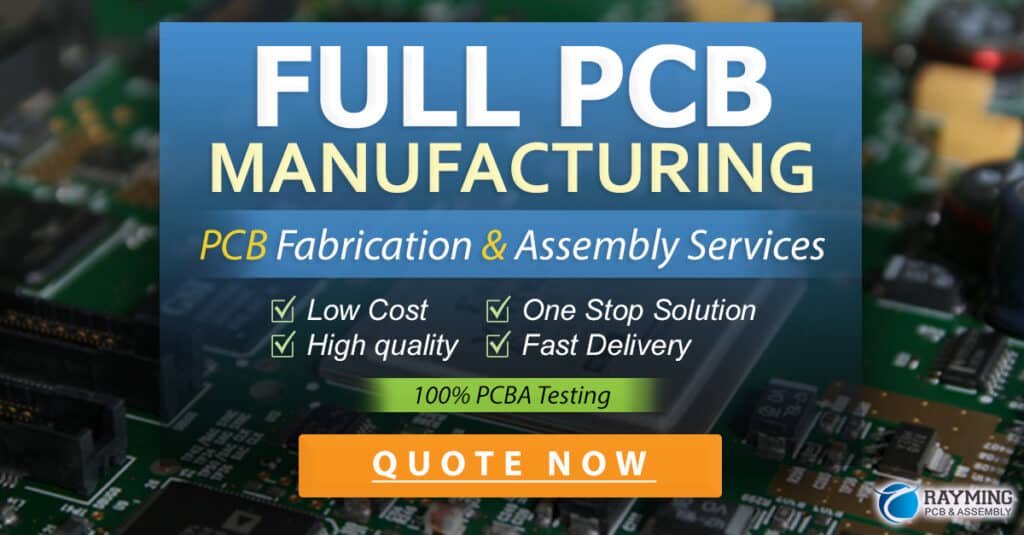
Frequently Asked Questions (FAQ)
- What is the difference between a BOM and a CPL?
-
A BOM is a comprehensive list of all the components, subassemblies, and raw materials required to produce a product, while a CPL focuses more on the individual components and their specifications.
-
How often should BOMs and CPLs be updated?
-
BOMs and CPLs should be updated whenever there are changes to the product design, components, or suppliers. It’s important to regularly review and update these documents to ensure they remain accurate and up to date.
-
What are the benefits of using software solutions for managing BOMs and CPLs?
-
Software solutions can help automate the process of creating and maintaining BOMs and CPLs, reduce errors, and ensure that everyone has access to the most current information. They can also facilitate collaboration among cross-functional teams and provide real-time visibility into the production process.
-
How can BOMs and CPLs be used for cost analysis?
-
By understanding the costs associated with each component and subassembly listed in the BOM and CPL, companies can make informed decisions about sourcing, negotiating with suppliers, or redesigning products to reduce costs. Cost analysis using BOMs and CPLs can help identify opportunities for cost savings and optimize the production process.
-
What role do BOMs and CPLs play in quality control?
- BOMs and CPLs serve as reference documents for quality control processes, ensuring that the correct components are used and that the final product meets the required specifications. By comparing the actual components and quantities used in production against the BOM and CPL, quality control teams can identify and address any issues or deviations from the intended design.
Conclusion
BOMs and CPLs are critical tools for managing the complexity of modern manufacturing and engineering processes. By providing a comprehensive and detailed list of all the components and materials required to produce a product, these documents serve as the foundation for effective planning, procurement, and production.
Creating and maintaining accurate BOMs and CPLs requires collaboration among cross-functional teams, the use of consistent naming conventions, and regular updates and audits. Leveraging software solutions can help streamline the process and ensure that everyone has access to the most current information.
Utilizing BOMs and CPLs in production processes, such as Materials Requirements Planning, supplier management, cost analysis, quality control, and continuous improvement, can lead to significant benefits for companies. These include optimized inventory levels, reduced lead times, cost savings, improved quality, and increased efficiency.
By understanding the importance of BOMs and CPLs and implementing best practices for their creation, maintenance, and utilization, companies can gain a competitive edge in today’s fast-paced and ever-evolving manufacturing landscape.
Leave a Reply