Introduction to Solder profiles
Solder profiles are essential for achieving optimal results in electronic assembly processes, particularly when using reflow ovens like the eC-reflow-mate. A solder profile is a temperature curve that defines the heating and cooling rates, as well as the time spent at specific temperatures during the reflow soldering process. Proper solder profiles ensure that the solder paste melts evenly, forms reliable connections, and minimizes the risk of defects such as tombstoning, bridging, or insufficient wetting.
Key Elements of a Solder Profile
A typical solder profile consists of four main stages:
-
Preheat: The assembly is gradually heated to activate the flux and remove any moisture from the PCB and components. This stage helps prevent thermal shock and minimizes the risk of component cracking or delamination.
-
Soak: The temperature is maintained within a specific range to allow the flux to clean the surfaces and prepare them for soldering. The soak stage also helps equalize the temperature across the assembly, ensuring even heating.
-
Reflow: The temperature is rapidly increased to melt the solder paste and form the solder joints. The peak temperature and time above liquidus (TAL) are critical factors in achieving proper wetting and intermetallic compound formation.
-
Cooling: The assembly is cooled down at a controlled rate to solidify the solder joints and prevent defects such as cold joints or excessive intermetallic growth.
Oven Parameters for the eC-reflow-mate
The eC-reflow-mate is a versatile reflow oven designed for small-scale electronic assembly and prototyping. To achieve optimal soldering results, it is crucial to set the appropriate oven parameters based on the solder paste specifications and the assembly characteristics.
Temperature Zones
The eC-reflow-mate features multiple temperature zones that can be independently controlled to create the desired solder profile:
Zone | Typical Temperature Range |
---|---|
Zone 1 | 100°C – 150°C |
Zone 2 | 150°C – 200°C |
Zone 3 | 200°C – 250°C |
Zone 4 | 250°C – 300°C |
By adjusting the temperature setpoints for each zone, you can fine-tune the solder profile to meet the specific requirements of your assembly.
Conveyor Speed
The conveyor speed determines the time the assembly spends in each temperature zone and, consequently, the overall profile duration. A slower conveyor speed results in a longer profile, while a faster speed leads to a shorter profile. The eC-reflow-mate allows you to adjust the conveyor speed to achieve the desired profile characteristics:
Conveyor Speed | Typical Profile Duration |
---|---|
Slow | 6-8 minutes |
Medium | 4-6 minutes |
Fast | 2-4 minutes |
It is essential to select a conveyor speed that provides sufficient time for the solder paste to melt and wet the surfaces, while avoiding excessive heating that could damage the components or the PCB.
Creating Solder Profiles for the eC-reflow-mate
To create a solder profile for the eC-reflow-mate, follow these steps:
-
Determine the solder paste specifications: Consult the solder paste datasheet to identify the recommended temperature profile, including the peak temperature, time above liquidus (TAL), and ramp rates.
-
Consider the assembly characteristics: Take into account factors such as the PCB thickness, component density, and thermal mass, as they can influence the heating and cooling rates.
-
Set the initial oven parameters: Begin by setting the temperature setpoints for each zone based on the solder paste recommendations and the assembly characteristics. Start with a slower conveyor speed to allow for profile adjustment.
-
Run a test profile: Place a test assembly with thermocouples attached to critical areas (e.g., large components, high-density regions) and run the reflow process using the initial oven parameters.
-
Analyze the profile data: Use a profiling software or data logger to record the temperature data from the thermocouples. Compare the measured profile to the recommended profile and identify any deviations.
-
Adjust the oven parameters: If necessary, adjust the temperature setpoints and conveyor speed to bring the measured profile closer to the target profile. Repeat steps 4-6 until the desired profile is achieved.
-
Validate the profile: Once the optimal profile is established, run multiple test assemblies to verify the soldering quality and consistency. Inspect the solder joints for proper wetting, fillets, and the absence of defects.
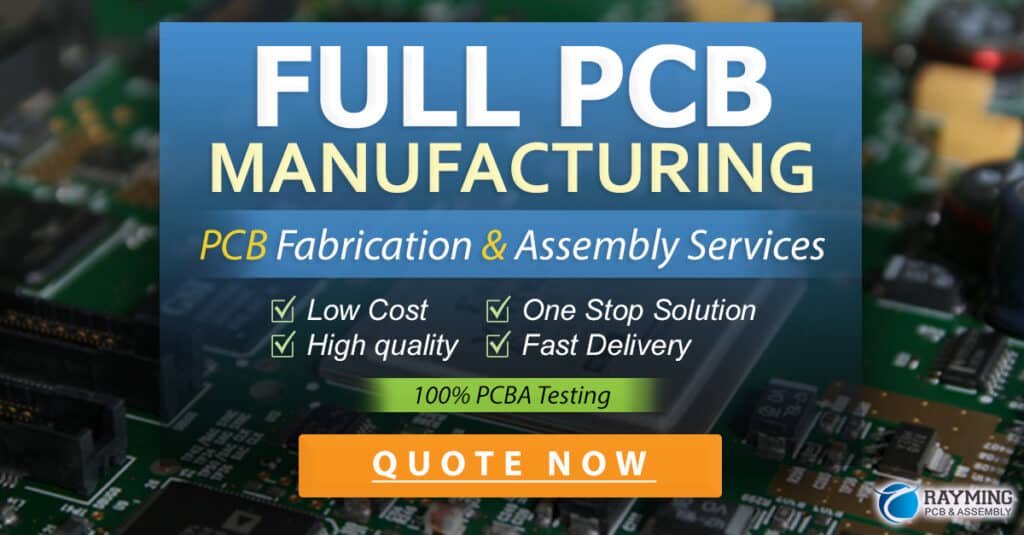
Example Solder Profile for SAC305 Solder Paste
Let’s consider an example solder profile for a commonly used lead-free solder paste, SAC305 (Sn96.5Ag3.0Cu0.5). The typical recommended profile for SAC305 is as follows:
Profile Parameter | Value |
---|---|
Preheat Ramp Rate | 0.5-1.5°C/s |
Soak Temperature | 150-180°C |
Soak Time | 60-120 seconds |
Reflow Ramp Rate | 1-2°C/s |
Peak Temperature | 235-245°C |
Time Above Liquidus (TAL) | 30-90 seconds |
Cooling Ramp Rate | 1-4°C/s |
To achieve this profile on the eC-reflow-mate, you could start with the following oven parameters:
Zone | Temperature Setpoint |
---|---|
Zone 1 | 120°C |
Zone 2 | 180°C |
Zone 3 | 230°C |
Zone 4 | 250°C |
Set the conveyor speed to medium (4-6 minutes) and run a test profile. Analyze the measured profile and make adjustments to the temperature setpoints and conveyor speed as needed to meet the target profile requirements.
Frequently Asked Questions (FAQ)
-
What is the purpose of a solder profile?
A solder profile is a temperature curve that defines the heating and cooling rates, as well as the time spent at specific temperatures during the reflow soldering process. Its purpose is to ensure that the solder paste melts evenly, forms reliable connections, and minimizes the risk of defects. -
How do I determine the appropriate solder profile for my assembly?
To determine the appropriate solder profile, consult the solder paste datasheet for the recommended temperature profile and consider the assembly characteristics such as PCB thickness, component density, and thermal mass. Use these guidelines to set the initial oven parameters and then fine-tune the profile based on test results. -
Can I use the same solder profile for different assemblies?
While it is possible to use the same solder profile for similar assemblies, it is recommended to create a specific profile for each assembly to account for variations in components, PCB design, and thermal requirements. Using a tailored profile helps ensure optimal soldering quality and reliability. -
What are the consequences of an incorrect solder profile?
An incorrect solder profile can lead to various soldering defects, such as tombstoning, bridging, insufficient wetting, cold joints, or excessive intermetallic growth. These defects can compromise the electrical and mechanical integrity of the solder joints, leading to reduced reliability and potential failures. -
How often should I validate my solder profile?
It is good practice to validate your solder profile periodically, especially when there are changes in the assembly design, components, or solder paste. Regular validation helps ensure that the profile remains optimal and consistent over time. The specific validation frequency depends on factors such as production volume, quality requirements, and process stability.
Conclusion
Creating and optimizing solder profiles for the eC-reflow-mate is crucial for achieving high-quality soldering results in electronic assembly processes. By understanding the key elements of a solder profile, setting appropriate oven parameters, and following a systematic approach to profile development, you can ensure reliable and consistent solder joint formation.
Remember to consult the solder paste specifications, consider the assembly characteristics, and validate the profile through testing and inspection. With proper solder profile management, you can minimize the risk of defects, improve process efficiency, and enhance the overall reliability of your electronic assemblies.
Leave a Reply