What is Solder Paste Preparation?
Solder paste preparation, also known as SolderPastePrep, is the process of getting solder paste ready for application in electronics manufacturing, specifically for surface-mount technology (SMT). It involves several key steps to ensure the solder paste has the right properties and consistency for optimal results during the printing and reflow soldering processes.
Solder paste is a mixture of tiny solder alloy particles suspended in flux. The flux helps remove oxidation from metal surfaces, enhances solder wetting and promotes the formation of reliable solder joints. However, the solder paste needs to have specific rheological properties (related to its flow and deformation) to perform well. That’s where solder paste preparation comes in.
Key Steps in Solder Paste Prep
-
Storage and Handling – Proper storage of solder paste at the recommended temperature (usually refrigerated) and handling (to prevent contamination) is critical. The paste should be allowed to reach room temperature before use.
-
Mixing – The solder paste needs to be thoroughly mixed before use to ensure the solder particles are evenly distributed in the flux medium. This is typically done slowly by hand or with a mechanical mixer to avoid introducing air bubbles.
-
Test Printing – A test print is often performed on a test board or coupon to check the paste’s printability and ensure the desired results before actual production.
-
Viscosity Adjustment – If needed, the viscosity (thickness/thinness) of the paste can be adjusted by adding more flux medium or letting some solvent evaporate to thicken it. The ideal viscosity depends on the specific application.
-
Stencil Design – While not a direct solder paste preparation step, having a well-designed solder paste stencil is crucial. The stencil’s aperture sizes and shapes control the amount and placement of solder paste deposited.
By carefully preparing the solder paste and dialing in the right properties, manufacturers can achieve high-quality, reliable solder joints on SMT circuit boards.
Solder Paste Mixing Methods
Proper mixing is one of the most important steps in solder paste preparation. There are a few common methods used:
Manual Mixing
For small volumes of solder paste, manual mixing by hand is often used. The key is to stir slowly and gently to fully incorporate the solder particles into the flux without whipping in air bubbles. Special metal spatulas or stirrers are used.
Some tips for manual mixing:
– Allow refrigerated paste to reach room temp before mixing
– Stir smoothly in a figure-8 pattern
– Scrape down sides and bottom of jar to incorporate all paste
– Mix for 1-2 minutes until uniform consistency is reached
Mechanical Mixing
For larger paste volumes or in an automated setting, mechanical mixers are used. These can be pneumatic or electric mixers that rotate the paste container around a central axis at a controlled speed.
Advantages of mechanical mixing:
– More thorough, consistent mixing than manual
– Can keep paste at optimal temperature during mixing
– Programmable mixing profiles for different paste types
– Hands-free operation
The recommended mixing speed, time, and program varies by the specific paste and mixer model. Paste manufacturers will have guidelines to follow. Over-mixing can lead to air entrapment and compromised paste properties.
Centrifugal Mixing
Centrifugal force can also be used for solder paste mixing. With this method, the closed paste container is spun at high speeds (1000-3000 RPM) for a short time, which mixes the suspension without introducing air.
Centrifugal mixing is effective for:
– Quickly mixing paste with minimal air entrapment
– Bringing settled paste back into suspension
– Restoring paste that has started to separate
However, centrifugal force can also cause the flux medium and solder particles to separate radially if spun too fast or too long. Following the manufacturer’s recommendations is important.
Solder Paste Viscosity
Viscosity refers to a fluid’s resistance to flow – how thick or thin it is. For solder paste, viscosity is a crucial property that affects its printability, how well it releases from stencil apertures, and its slump resistance (ability to hold its printed shape).
Solder paste is a non-Newtonian fluid, meaning its viscosity changes with shear rate (how fast it’s flowing or being mixed). It exhibits shear-thinning behavior – as shear increases, viscosity decreases. This allows the paste to flow smoothly during printing but maintain its shape once deposited.
Factors Affecting Solder Paste Viscosity
Several factors can influence a solder paste’s viscosity:
Factor | Effect on Viscosity |
---|---|
Metal load (% of solder particles) | Higher metal load increases viscosity |
Solder particle size and shape | Smaller, more spherical particles lower viscosity |
Flux medium composition | Ratios of resin, solvent, thixotropes affect flow |
Temperature | Viscosity decreases as temperature increases |
Age of paste | Viscosity increases as flux medium evaporates over time |
Paste manufacturers formulate products to have the optimal starting viscosity for their intended applications. But viscosity can drift over time as the paste is stored and flux medium evaporates or separates. That’s why viscosity adjustment is sometimes a necessary solder paste prep step.
Measuring and Adjusting Viscosity
Viscosity is typically measured using a viscometer, which applies a shear force to the paste and measures the resulting flow. The units are centipoise (cP). Most solder pastes fall in the range of 100,000 – 1,000,000 cP.
If a paste’s viscosity is measured to be outside the acceptable range, adjustments can be made:
- To lower viscosity (thin the paste):
- Gently mix in a small amount of compatible solvent
-
Let paste sit at room temperature to allow natural thinning
-
To increase viscosity (thicken the paste):
- Allow some solvent to evaporate while mixing
- Chill the paste to quickly increase viscosity
The goal is to get the solder paste within its optimal viscosity window so it prints cleanly and performs well during the reflow process. Keeping detailed records of viscosity measurements and adjustments for each paste lot is good practice.
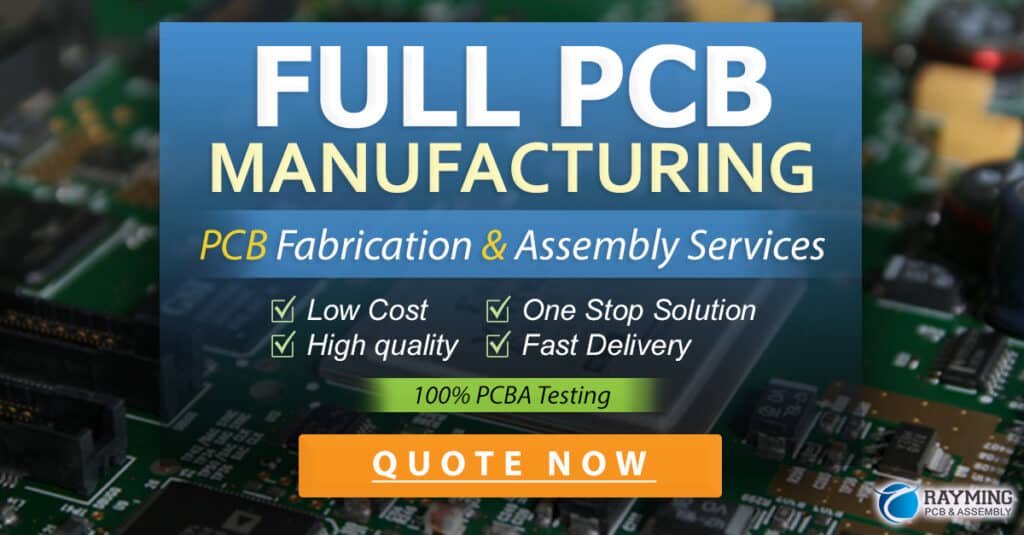
Solder Paste Test Printing
Before committing a batch of solder paste to a full production run, it’s wise to perform a test print. This involves printing the paste onto a test board or coupon using the same stencil and parameters that will be used in production.
The purpose of a test print is to:
– Verify the paste is printing cleanly and consistently
– Check paste deposits for the proper volume, shape, and placement
– Optimize printer settings if needed
– Ensure the paste interacts well with the board surface finish
Setting Up a Test Print
To run a test print, you’ll need:
1. A test board – usually a small PCB with various component footprints
2. The solder paste stencil that will be used in production
3. The solder paste, prepared and at the proper viscosity
4. A solder paste inspection (SPI) system to evaluate the print
Mount the test board in the printer and apply the solder paste as you would in normal production. Be sure to use the same print parameters – squeegee pressure, speed, separation speed, etc.
Evaluating Print Quality
After printing, the test board is inspected, either manually with a microscope or using an automated SPI machine. The key things to look for are:
– Paste volume – Is the amount of paste in each pad within acceptable limits?
– Paste shape – Are the paste deposits uniform and properly shaped?
– Paste placement – Is the paste accurately positioned on each pad?
– Bridging or slumping – Is there any solder paste bridging between pads or excessive slumping?
If any print quality issues are found, printer settings may need to be adjusted and the test repeated. Common adjustments include:
– Increasing/decreasing squeegee pressure
– Changing print speed
– Adjusting snap-off distance (stencil-to-board gap)
– Modifying stencil aperture size or shape
Once acceptable print quality is achieved on the test board, the solder paste and printer settings can be approved for production use. Regular test prints should still be performed periodically to monitor paste and print quality over time.
Test Print Troubleshooting Guide |
---|
Issue |
Low paste volume |
Inconsistent paste shape |
Bridging between pads |
Poor paste release |
Solder Paste Stencil Design
The solder paste stencil is a thin metal sheet, usually stainless steel, with laser-cut openings (apertures) that match the shape and location of solder pads on the PCB. It’s essentially a template for depositing solder paste in the precise amounts and positions needed.
Proper stencil design is critical for achieving optimal solder paste printing results. The stencil controls 3 key aspects of the paste deposit:
1. Volume – The amount of solder paste deposited on each pad
2. Area – The size and shape of the paste deposit
3. Positional accuracy – The placement of paste relative to the pad
Stencil Thickness
Stencil thickness is one of the main factors that determines paste deposit volume. A thicker stencil will deposit a higher volume of paste. The thickness is chosen based on the size of the components being assembled:
Component Type | Typical Stencil Thickness |
---|---|
Standard SMD | 0.100 – 0.150 mm |
Fine Pitch SMD | 0.100 – 0.125 mm |
Ultra Fine Pitch SMD | 0.075 – 0.100 mm |
Thicker stencils (up to 0.2 mm or more) may be used for some large components or connector pads. Step stencils, with multiple thicknesses, can be used when components of very different sizes are on the same board.
Aperture Design
The size and shape of the stencil apertures controls the area and shape of the printed solder paste deposits. As a general rule, the aperture size is slightly smaller than the PCB pad to allow for some paste spread.
Typical guidelines for aperture size reduction:
– Standard SMD: 10% smaller than pad
– Fine pitch SMD: 5% smaller
– Ultra fine pitch SMD: 0-5% smaller
The aperture shape usually matches the PCB pad, with rounded corners. Special aperture shapes may be used for unique components.
Proper aperture design ensures sufficient paste coverage on the pad without excessive spread that could cause bridging. The aspect ratio (width to thickness) of the aperture walls also affects paste release.
Other Stencil Design Considerations
- Fiducials – Add fiducial marks for vision alignment
- Stencil Foils – Use high-quality laser-cut or electroformed foils
- Mounting – Ensure the stencil is securely and flatly mounted in its frame
- Cleaning – Design for easy cleaning, with no enclosed areas to trap paste
- Markings – Include stencil identification markings and orientation indicators
Well-designed solder paste stencils are essential for reliable, high-yield SMT assembly. Close collaboration between PCB design, stencil fabrication, and assembly process engineering leads to optimal stencil designs.
Solder Paste Preparation FAQ
Q: How long can solder paste be stored before use?
A: Most solder pastes can be stored for 6-12 months from the date of manufacture when kept at the recommended conditions (usually 0-10°C). However, once the jar is opened, the paste should be used within a month or less to avoid changes in viscosity and print quality due to flux evaporation or separation.
Q: What’s the best way to bring refrigerated solder paste up to room temperature before use?
A: Remove the paste from the refrigerator and let it sit unopened at room temperature for 4-8 hours, depending on jar size. Avoid accelerated warming methods like heat guns, as these can locally overheat the paste and alter its properties. Bringing paste to room temp slowly ensures it will have consistent viscosity and print behavior.
Q: How often should solder paste viscosity be checked?
A: At a minimum, viscosity should be checked:
– When first opening a new jar of paste
– After the paste has been sitting out at room temperature for an extended period
– If print quality issues are noticed
– At the start of each shift or production run
More frequent checks (every few hours) are recommended for critical applications or when using paste that’s near the end of its open jar life.
Q: What causes solder paste to slump or spread excessively after printing?
A: Solder paste slump can be caused by:
– Paste being too thin/low viscosity
– Stencil apertures being too large
– Insufficient stencil-to-board gap (snap-off distance)
– Paste being too warm
– Excessive vibration or movement of the printed board
To address slump, try increasing paste viscosity, decreasing aperture size, increasing snap-off distance, or cooling the paste/board slightly.
Q: How should solder paste residue be cleaned off of stencils and equipment?
A: Most solder pastes can be effectively cleaned using isopropyl alcohol (IPA) and lint-free wipes. For tougher residues, a commercial stencil cleaner may be needed. Avoid using anything abrasive that could scratch the stencil surface.
It’s important to clean paste residue frequently, as dried flux can be difficult to remove and cause print quality issues. Stencils should be underside cleaned at least every 5 prints and fully cleaned at the end of each shift.
When cleaning the stencil, be sure to also wipe down the squeegee blades, spatulas, and any other surfaces that contact the paste. Keeping all tools clean helps ensure consistent solder paste performance.
Leave a Reply