What is RoHS and Why is RoHS Compliance Important?
The Restriction of Hazardous Substances (RoHS) Directive is a set of regulations that restricts the use of certain hazardous materials in the manufacture of electronic and electrical equipment. The directive was first introduced by the European Union in 2003, and has since been adopted by many other countries around the world.
RoHS compliance is important for several reasons:
-
Environmental Protection: The hazardous substances restricted by RoHS can cause serious environmental damage if not disposed of properly. By limiting their use in electronics, RoHS helps protect the environment.
-
Human Health: Many of the substances restricted by RoHS are toxic and can have harmful effects on human health, especially for workers involved in electronics manufacturing. RoHS compliance helps protect these workers.
-
Market Access: RoHS compliance is a legal requirement for selling electronic products in many markets, including the EU. Non-compliance can result in products being banned from sale.
-
Corporate Social Responsibility: Demonstrating RoHS compliance shows that a company takes its environmental and social responsibilities seriously, which can improve its reputation with customers, investors, and the public.
What Substances are Restricted by RoHS?
The original RoHS Directive (2002/95/EC) restricted the use of six hazardous substances in electronics:
Substance | Maximum Concentration Value |
---|---|
Lead (Pb) | 0.1% |
Mercury (Hg) | 0.1% |
Cadmium (Cd) | 0.01% |
Hexavalent Chromium (Cr6+) | 0.1% |
Polybrominated Biphenyls (PBB) | 0.1% |
Polybrominated Diphenyl Ethers (PBDE) | 0.1% |
In 2015, the directive was updated (2011/65/EU) to include four additional substances:
Substance | Maximum Concentration Value |
---|---|
Bis(2-Ethylhexyl) phthalate (DEHP) | 0.1% |
Benzyl butyl phthalate (BBP) | 0.1% |
Dibutyl phthalate (DBP) | 0.1% |
Diisobutyl phthalate (DIBP) | 0.1% |
These maximum concentration values apply to homogeneous materials, i.e., materials that cannot be mechanically disjointed into different materials.
How to Achieve RoHS Compliance
Achieving RoHS compliance requires a comprehensive approach that involves all stages of the product lifecycle, from design and procurement to manufacturing and disposal.
Design for RoHS Compliance
The first step in achieving RoHS compliance is to design products with compliance in mind from the outset. This involves:
- Selecting components and materials that are RoHS compliant
- Avoiding the use of restricted substances where possible
- Designing for ease of disassembly and recycling at end-of-life
Procurement and Supply Chain Management
Ensuring RoHS compliance requires working closely with suppliers to ensure that all components and materials used in the product are compliant. This involves:
- Requiring suppliers to provide RoHS compliance data for their products
- Conducting due diligence on suppliers to verify their compliance claims
- Establishing and maintaining a database of compliant parts and suppliers
Manufacturing Process Control
RoHS compliance must be maintained throughout the manufacturing process to avoid contamination of the product with restricted substances. This involves:
- Implementing process controls to prevent contamination
- Training workers on RoHS requirements and best practices
- Conducting regular audits and inspections to ensure compliance
Testing and Verification
To ensure that the finished product meets RoHS requirements, it must be tested and verified using appropriate analytical methods. The most common methods are:
- X-Ray Fluorescence (XRF) Spectroscopy
- Scanning Electron Microscopy (SEM)
- Atomic Absorption Spectroscopy (AAS)
- Inductively Coupled Plasma (ICP) Analysis
Documentation and Reporting
RoHS compliance must be documented throughout the product lifecycle, from design to disposal. This documentation includes:
- Material declarations from suppliers
- Test reports and certificates of compliance
- Process control records
- Traceability data for materials and components
This documentation must be maintained and made available to customers and regulatory authorities upon request.
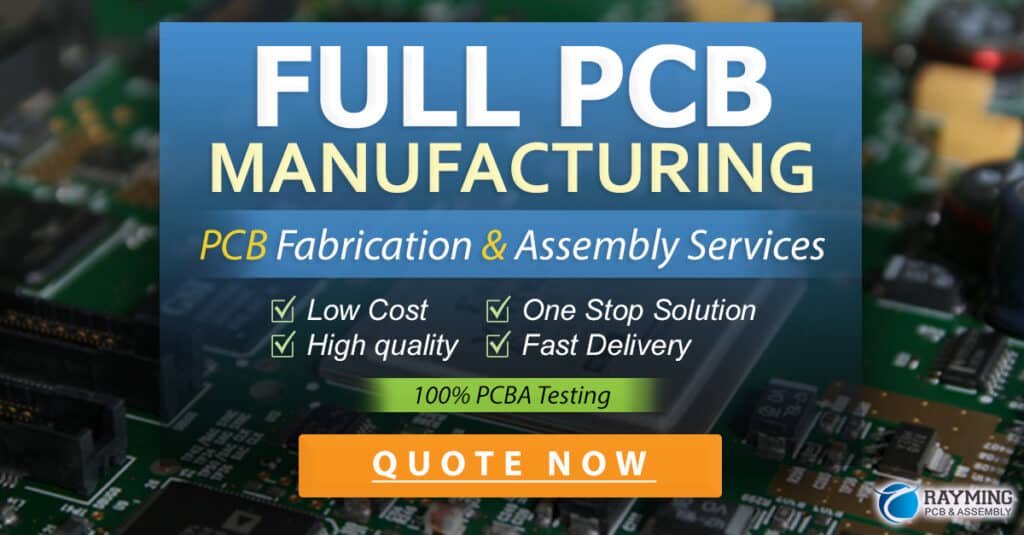
The Benefits of Lead-free Electronics
One of the key substances restricted by RoHS is lead, which was widely used in electronics soldering until the introduction of lead-free alternatives. Lead-free electronics offer several benefits over their leaded counterparts:
Environmental Benefits
Lead is a toxic heavy metal that can have severe impacts on the environment if not disposed of properly. Lead can contaminate soil and water, and can accumulate in plants and animals. By eliminating lead from electronics, lead-free soldering helps protect the environment from these harmful effects.
Health Benefits
Lead exposure can have serious health effects, particularly for children and pregnant women. Lead can damage the nervous system, kidneys, and reproductive system, and can cause learning and behavior problems in children. By eliminating lead from electronics manufacturing, lead-free soldering helps protect workers and consumers from these health risks.
Improved Reliability
Despite initial concerns about the reliability of lead-free solders, studies have shown that lead-free solders can provide equal or better reliability compared to leaded solders. Lead-free solders have higher melting points and better mechanical strength, which can improve the durability and longevity of electronic products.
Compliance with Regulations
As mentioned earlier, RoHS compliance is a legal requirement for selling electronic products in many markets. By using lead-free solders and components, manufacturers can ensure that their products meet these regulatory requirements and can be sold in these markets.
Challenges of Lead-free Soldering
While lead-free soldering offers many benefits, it also presents some challenges compared to traditional leaded soldering:
Higher Melting Point
Lead-free solders typically have higher melting points than leaded solders, which can require changes to the soldering process. This may involve using higher Soldering Temperatures, different flux materials, and adjusting the soldering profile.
Different Wetting Characteristics
Lead-free solders have different wetting characteristics than leaded solders, which can affect the formation of the solder joint. This may require adjustments to the soldering process, such as using different tip geometries or changing the solder feed rate.
Potential for Tin Whiskers
Some lead-free solders, particularly those with high tin content, can be prone to the formation of tin whiskers. These are thin, needle-like growths of tin that can cause short circuits and other reliability issues. Mitigating the risk of tin whiskers may require changes to the component finishes or the use of conformal coatings.
Supply Chain Challenges
Transitioning to lead-free soldering can present challenges for the electronics supply chain, particularly for smaller manufacturers and those in developing countries. Ensuring a reliable supply of RoHS-compliant components and materials can be difficult and may require changes to procurement practices.
Despite these challenges, the benefits of lead-free soldering and RoHS compliance far outweigh the costs. By adopting lead-free soldering and other RoHS-compliant practices, electronics manufacturers can help protect the environment, safeguard human health, and ensure the long-term reliability and competitiveness of their products.
Frequently Asked Questions (FAQ)
What is RoHS compliance?
RoHS compliance refers to meeting the requirements of the Restriction of Hazardous Substances (RoHS) Directive, which restricts the use of certain hazardous materials in the manufacture of electronic and electrical equipment.
What are the substances restricted by RoHS?
The original RoHS Directive restricted the use of six substances: lead, mercury, cadmium, hexavalent chromium, polybrominated biphenyls (PBB), and polybrominated diphenyl ethers (PBDE). The directive was later updated to include four additional substances: bis(2-ethylhexyl) phthalate (DEHP), benzyl butyl phthalate (BBP), dibutyl phthalate (DBP), and diisobutyl phthalate (DIBP).
How can I ensure that my products are RoHS compliant?
Ensuring RoHS compliance requires a comprehensive approach that involves all stages of the product lifecycle, from design and procurement to manufacturing and testing. This includes selecting RoHS-compliant components and materials, implementing process controls to prevent contamination, conducting testing and verification, and maintaining proper documentation.
What are the benefits of using lead-free solders?
Lead-free solders offer several benefits over traditional leaded solders, including reduced environmental impact, improved worker and consumer health, better reliability and durability, and compliance with RoHS and other regulations.
What challenges are associated with lead-free soldering?
Lead-free soldering can present some challenges compared to leaded soldering, including higher melting points, different wetting characteristics, the potential for tin whiskers, and supply chain challenges. However, these challenges can be overcome with proper process adjustments and risk mitigation strategies.
Leave a Reply