What are RF PCBs?
Radio Frequency (RF) PCBs are specialized circuit boards designed to carry high-frequency signals, typically in the range of 100 MHz to 100 GHz. These PCBs are crucial components in various applications, such as:
- Wireless communication devices
- Radar systems
- Satellite communication
- Medical equipment
- Aerospace and defense systems
RF PCBs require precise design and manufacturing techniques to ensure optimal signal integrity and minimize signal loss, reflection, and interference.
Mixed-Signal and Microwave PCBs
Mixed-Signal PCBs
Mixed-signal PCBs incorporate both analog and digital components on a single board. These PCBs are designed to handle a combination of low-frequency analog signals and high-speed digital signals. Some key considerations for mixed-signal PCB design include:
- Proper grounding and shielding techniques
- Minimizing crosstalk between analog and digital sections
- Optimizing component placement and routing
- Selecting appropriate materials and layer stackups
Microwave PCBs
Microwave PCBs are designed to operate at frequencies above 1 GHz, typically in the range of 1 GHz to 100 GHz. These PCBs require specialized materials and design techniques to minimize signal loss and maintain signal integrity. Some critical aspects of microwave PCB design include:
- Selecting low-loss dielectric materials
- Implementing controlled impedance techniques
- Minimizing discontinuities and reflections
- Utilizing advanced simulation tools for design optimization
RayMing Technology’s RF PCB Manufacturing Capabilities
RayMing Technology offers a comprehensive range of RF PCB manufacturing services, catering to the unique needs of mixed-signal and microwave applications. Some of our key capabilities include:
1. Advanced Material Selection
We work with a wide range of high-performance materials, including:
- Rogers RO4000 series
- Isola I-Tera MT40
- Taconic RF-35
- Arlon AD250
These materials offer excellent dielectric properties, low loss tangents, and stable performance across a wide frequency range.
2. Precision Fabrication Techniques
Our state-of-the-art manufacturing facilities employ advanced fabrication techniques to ensure the highest quality RF PCBs:
- Controlled impedance routing
- Blind and buried vias
- Microvias and HDI technology
- Tight tolerance drilling and plating
- Precision controlled etching
3. Rigorous Quality Control
We adhere to strict quality control measures throughout the manufacturing process, including:
- 100% electrical testing
- Automated optical inspection (AOI)
- X-ray inspection
- Time-domain reflectometry (TDR) testing
- Thermal stress testing
These measures ensure that every RF PCB meets our customers’ specifications and performs reliably in the field.
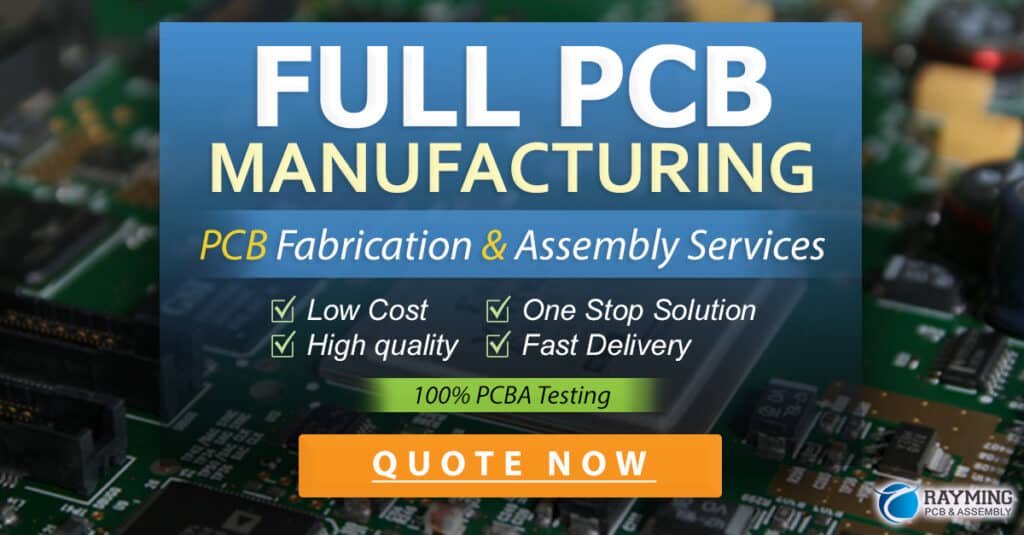
RF PCB Design Considerations
Designing RF PCBs requires careful consideration of several key factors to ensure optimal performance and reliability. Some essential design considerations include:
1. Material Selection
Choosing the right dielectric material is crucial for RF PCBs. The material should have a low dielectric constant (Dk) and a low loss tangent (Df) to minimize signal loss and maintain signal integrity. The material’s thermal stability and mechanical properties should also be considered based on the application’s requirements.
2. Controlled Impedance
Maintaining a consistent characteristic impedance throughout the RF signal path is essential to prevent signal reflections and ensure proper matching between components. Controlled impedance techniques involve precisely calculating the trace width, thickness, and spacing based on the dielectric material’s properties and the desired impedance.
3. Grounding and Shielding
Proper grounding and shielding techniques are critical in RF PCB design to minimize electromagnetic interference (EMI), crosstalk, and signal coupling. Some common techniques include:
- Implementing ground planes and ground vias
- Using guard traces and shielding cans
- Separating sensitive signal traces from potential noise sources
- Employing strip line or coplanar waveguide (CPW) transmission line structures
4. Component Placement and Routing
Optimizing component placement and routing is essential to minimize signal path lengths, reduce parasitics, and maintain signal integrity. Some best practices include:
- Placing components as close to each other as possible
- Minimizing trace lengths and avoiding unnecessary bends
- Using symmetrical and balanced layouts for differential signals
- Avoiding stubs and unterminated traces
5. Simulation and Verification
Utilizing advanced simulation tools, such as electromagnetic (EM) simulators and circuit simulators, is crucial for optimizing RF PCB designs and verifying their performance before fabrication. These tools help engineers analyze signal integrity, impedance matching, and electromagnetic compatibility (EMC) issues, enabling them to make necessary design adjustments and avoid costly redesigns.
RayMing Technology’s RF PCB Manufacturing Process
At RayMing Technology, we follow a streamlined RF PCB manufacturing process to ensure the highest quality products and timely delivery:
- Design Review and DFM Analysis
-
Our experienced engineers review the customer’s design files and conduct a Design for Manufacturability (DFM) analysis to identify potential issues and suggest improvements.
-
Material Selection and Procurement
-
We work with the customer to select the most suitable materials based on their application’s requirements and procure the necessary raw materials from trusted suppliers.
-
PCB Fabrication
-
Our state-of-the-art manufacturing facilities fabricate the RF PCBs using advanced techniques, such as controlled impedance routing, blind and buried vias, and precision drilling and plating.
-
Assembly and Component Mounting
-
We offer both through-hole and surface-mount assembly services, using automated pick-and-place machines and reflow soldering processes to ensure accurate and reliable component placement.
-
Testing and Quality Control
-
Every RF PCB undergoes rigorous testing and quality control measures, including electrical testing, AOI, X-ray inspection, and TDR testing, to ensure compliance with the customer’s specifications and industry standards.
-
Packaging and Shipping
- The finished RF PCBs are carefully packaged using ESD-safe materials and shipped to the customer’s designated location using reliable logistics partners.
RF PCB Manufacturing Standards and Certifications
RayMing Technology adheres to various industry standards and certifications to ensure the quality and reliability of our RF PCBs:
- IPC-A-600: Acceptability of Printed Boards
- IPC-6012: Qualification and Performance Specification for Rigid Printed Boards
- IPC-2221: Generic Standard on Printed Board Design
- ISO 9001: Quality Management Systems
- IATF 16949: Quality Management System for Automotive Industry
- AS9100D: Quality Management Systems – Requirements for Aviation, Space, and Defense Organizations
- UL 94: Standard for Safety of Flammability of Plastic Materials
Why Choose RayMing Technology for Your RF PCB Manufacturing Needs?
RayMing Technology is your trusted partner for high-quality RF PCB manufacturing services. Here are some reasons why you should choose us for your mixed-signal and microwave PCB needs:
- Extensive Experience and Expertise
-
With years of experience in RF PCB manufacturing, our team of skilled engineers and technicians has the knowledge and expertise to handle even the most complex projects.
-
Advanced Manufacturing Facilities
-
We invest in state-of-the-art manufacturing equipment and technologies to ensure the highest quality and precision in our RF PCB fabrication processes.
-
Comprehensive Services
-
From design support and material selection to fabrication, assembly, and testing, we offer a complete range of services to meet your RF PCB manufacturing needs.
-
Strict Quality Control
-
Our rigorous quality control measures and adherence to industry standards ensure that every RF PCB we produce meets the highest standards of quality and reliability.
-
Competitive Pricing and Fast Turnaround
- We offer competitive pricing without compromising on quality, and our streamlined manufacturing process enables us to deliver your RF PCBs within the shortest possible lead times.
Frequently Asked Questions (FAQ)
- What is the minimum feature size that RayMing Technology can achieve for RF PCBs?
-
We can achieve a minimum feature size of 50 µm (0.002″) for trace width and spacing, and 100 µm (0.004″) for via diameter.
-
What is the maximum frequency range that your RF PCBs can support?
-
Our RF PCBs can support frequencies up to 100 GHz, depending on the materials and design techniques used.
-
Can you provide controlled impedance routing for RF PCBs?
-
Yes, we offer controlled impedance routing services with a tolerance of ±5% for various impedance values, such as 50 Ω, 75 Ω, and 100 Ω.
-
What are your typical lead times for RF PCB manufacturing?
-
Our lead times vary depending on the complexity of the project and the customer’s requirements. Typically, we can deliver RF PCBs within 2-4 weeks from the receipt of the order.
-
Do you offer design support services for RF PCBs?
- Yes, our experienced engineers can provide design support services, including schematic review, layout optimization, and signal integrity analysis, to help you achieve the best possible performance for your RF PCBs.
Conclusion
RayMing Technology is your reliable rf pcb manufacturer for mixed-signal and microwave PCBs. With our advanced manufacturing capabilities, strict quality control measures, and commitment to customer satisfaction, we deliver high-quality RF PCBs that meet your most demanding requirements. Contact us today to discuss your RF PCB manufacturing needs and experience the RayMing Technology difference.
Leave a Reply