Introduction to PCB Registration
Printed Circuit Board (PCB) registration is a critical process in the manufacturing of electronic devices. It ensures that the various layers of a PCB are aligned correctly, resulting in proper functionality and reliability of the final product. PCB registration also plays a crucial role in the application of solder paste using stencils, which is an essential step in the surface mount technology (SMT) assembly process.
In this article, we will delve into the details of registration systems for PCBs and stencils, discussing the various methods, technologies, and best practices involved in achieving accurate and consistent registration.
The Importance of Accurate PCB Registration
Accurate PCB registration is vital for several reasons:
-
Functional Integrity: Misaligned layers can lead to short circuits, open circuits, or improper connections between components, compromising the functionality of the electronic device.
-
Reliability: Poor registration can cause stress on the interconnections between layers, leading to reduced reliability and potential failures over time.
-
High-density Designs: As PCBs become more complex and feature-dense, the tolerance for registration errors decreases, making accurate registration even more critical.
-
Solder Paste Application: Precise registration between the PCB and stencil is necessary for the accurate application of solder paste, ensuring proper component placement and soldering.
PCB Registration Methods
There are several methods used to achieve accurate PCB registration during the manufacturing process:
Pin Registration
Pin registration is a common method that uses precisely located holes (fiducials) on the PCB and corresponding pins on the manufacturing equipment to align the layers. The PCB is placed onto the pins, ensuring accurate positioning. Pin registration is simple and cost-effective but may not be suitable for high-density designs with tight tolerances.
Optical Registration
Optical registration uses camera systems and image processing algorithms to align the PCB layers. Fiducial marks, such as crosshairs or circles, are etched onto the PCB layers. The camera system locates these fiducials and adjusts the position of the layers accordingly. Optical registration offers higher accuracy than pin registration and can accommodate high-density designs.
Combination Registration
Some manufacturing processes use a combination of pin and optical registration to achieve the best results. The pin registration provides initial alignment, while the optical registration fine-tunes the positioning for optimal accuracy.
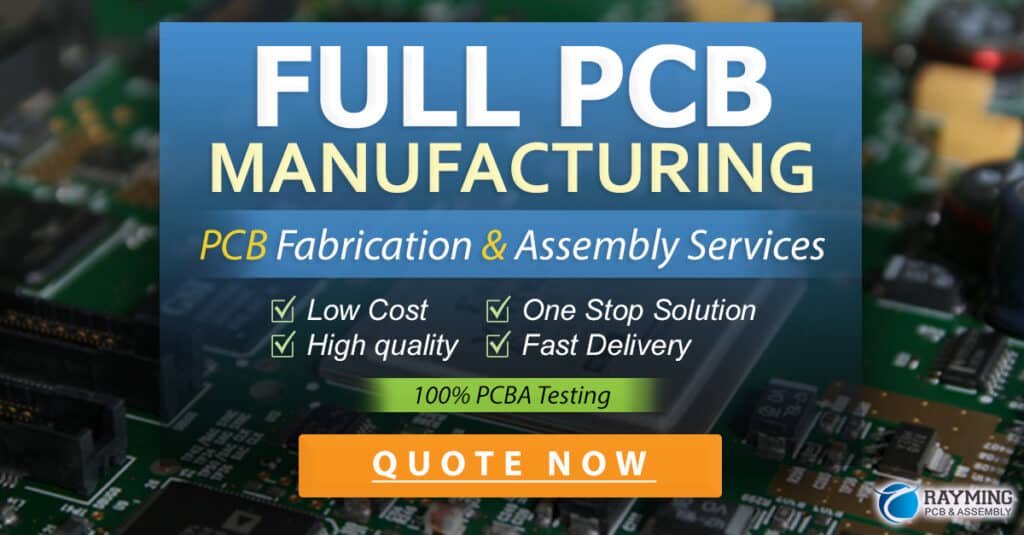
Stencil Registration
Stencil registration is the process of aligning the solder paste stencil with the PCB to ensure accurate solder paste application. Proper stencil registration is crucial for the following reasons:
-
Component Placement: Accurate solder paste deposit placement ensures that components are correctly positioned on the PCB during the pick-and-place process.
-
Solder Joint Quality: Precise solder paste volume and placement lead to reliable solder joints, reducing the risk of defects such as bridging or insufficient solder.
-
Manufacturing Efficiency: Good stencil registration minimizes the need for rework or repairs, improving overall production efficiency.
Stencil registration can be achieved using methods similar to those used for PCB registration, such as pin registration or optical registration. The stencil is aligned with the PCB using fiducial marks or pins, ensuring accurate solder paste application.
Registration Tolerances
Registration tolerances define the acceptable level of misalignment between PCB layers or between the PCB and stencil. The tolerances vary depending on the design requirements, manufacturing capabilities, and industry standards.
Typical registration tolerances for PCBs are:
Feature Size | Tolerance |
---|---|
>0.5mm | ±0.1mm |
0.25-0.5mm | ±0.05mm |
<0.25mm | ±0.025mm |
For stencil registration, the tolerances are typically tighter, ranging from ±0.025mm to ±0.05mm, depending on the pitch and size of the components being assembled.
Meeting these tolerances requires well-maintained equipment, skilled operators, and robust quality control processes.
Best Practices for PCB and Stencil Registration
To achieve optimal registration results, consider the following best practices:
-
Design for Manufacturing (DFM): Incorporate registration-friendly features, such as fiducial marks and adequate clearances, into the PCB design.
-
Equipment Maintenance: Regularly calibrate and maintain registration equipment to ensure consistent performance.
-
Operator Training: Provide thorough training to operators on the proper use of registration equipment and techniques.
-
Quality Control: Implement a robust quality control process that includes regular inspections and measurements to verify registration accuracy.
-
Environmental Control: Maintain a clean and stable environment in the manufacturing area to minimize the impact of factors such as temperature and humidity on registration.
Advanced Registration Technologies
As PCB designs become more complex and miniaturized, advanced registration technologies have emerged to meet the demands for higher accuracy and efficiency:
Direct Imaging (DI)
Direct imaging is a process that uses a high-resolution laser or LED light source to directly expose the desired pattern onto the PCB layers, eliminating the need for traditional photomasks. DI systems offer improved registration accuracy, reduced setup times, and the ability to accommodate rapid design changes.
Automated Optical Inspection (AOI)
AOI systems use high-resolution cameras and advanced image processing algorithms to inspect PCBs for registration errors and other defects. AOI can quickly identify registration issues, allowing for timely corrections and reducing the risk of defective products reaching the end-user.
Adaptive Registration
Adaptive registration systems use real-time feedback from sensors to continuously monitor and adjust the registration of PCB layers or stencils during the manufacturing process. This dynamic approach compensates for any variations or distortions, ensuring consistent registration throughout the production run.
Frequently Asked Questions (FAQ)
-
Q: What is the difference between pin registration and optical registration?
A: Pin registration uses physical pins and corresponding holes to align PCB layers, while optical registration uses camera systems and fiducial marks for alignment. Optical registration generally offers higher accuracy and is better suited for high-density designs. -
Q: Why is accurate stencil registration important?
A: Accurate stencil registration ensures that the solder paste is applied precisely on the PCB pads, which is crucial for proper component placement and soldering. Poor stencil registration can lead to defects such as bridging or insufficient solder joints. -
Q: What are the typical registration tolerances for PCBs?
A: Registration tolerances for PCBs depend on the feature size. For features larger than 0.5mm, the tolerance is typically ±0.1mm. For features between 0.25-0.5mm, the tolerance is ±0.05mm, and for features smaller than 0.25mm, the tolerance is ±0.025mm. -
Q: What is Design for Manufacturing (DFM) in the context of PCB registration?
A: DFM involves incorporating registration-friendly features into the PCB design, such as fiducial marks and adequate clearances. By considering registration requirements during the design phase, manufacturers can improve the accuracy and efficiency of the registration process. -
Q: How does Automated Optical Inspection (AOI) help with PCB registration?
A: AOI systems use high-resolution cameras and advanced image processing algorithms to inspect PCBs for registration errors and other defects. By quickly identifying registration issues, AOI allows for timely corrections and reduces the risk of defective products reaching the end-user.
Conclusion
PCB registration is a critical aspect of electronic device manufacturing, ensuring the proper alignment of PCB layers and the accurate application of solder paste using stencils. Accurate registration is essential for the functional integrity, reliability, and manufacturing efficiency of electronic products.
Various methods, such as pin registration and optical registration, are used to achieve precise alignment, each with its own advantages and limitations. Adhering to registration tolerances and implementing best practices, such as DFM, equipment maintenance, and quality control, are crucial for achieving optimal registration results.
As PCB designs continue to advance, innovative technologies like direct imaging, automated optical inspection, and adaptive registration are being developed to meet the increasing demands for accuracy and efficiency in PCB manufacturing.
By understanding the importance of registration systems and staying informed about the latest technologies and best practices, manufacturers can produce high-quality, reliable electronic products that meet the ever-evolving needs of the industry.
Leave a Reply