Introduction to PCB Laminate Materials
Printed Circuit Boards (PCBs) are essential components in modern electronic devices, providing a platform for mounting and interconnecting electronic components. The choice of PCB laminate material plays a crucial role in determining the performance, reliability, and cost of the final product. Two popular laminate materials used in PCB manufacturing are PTFE (Polytetrafluoroethylene) and FR4 (Flame Retardant 4). In this article, we will explore the differences between PTFE and FR4 PCB laminate materials, their properties, applications, and factors to consider when choosing between them.
What is PTFE?
PTFE, commonly known by the brand name Teflon, is a synthetic fluoropolymer known for its excellent dielectric properties, low dissipation factor, and high thermal stability. It is a popular choice for high-frequency and microwave applications due to its low dielectric constant and low loss tangent. PTFE PCBs offer superior electrical performance, making them ideal for applications that require high signal integrity and minimal signal loss.
Properties of PTFE PCB Laminate
- Low dielectric constant (2.1)
- Low dissipation factor (0.0002)
- High thermal stability (up to 260°C)
- Excellent chemical resistance
- Non-stick and hydrophobic surface
- Low moisture absorption
Advantages of PTFE PCB Laminate
- Superior electrical performance at high frequencies
- Minimal signal loss and distortion
- Excellent thermal stability and heat resistance
- Resistant to harsh chemicals and solvents
- Ideal for high-speed digital and RF applications
Disadvantages of PTFE PCB Laminate
- Higher cost compared to FR4
- More challenging to manufacture and process
- Limited options for multilayer designs
- Lower mechanical strength and dimensional stability
What is FR4?
FR4 is a glass-reinforced epoxy laminate material widely used in the PCB industry. It is a cost-effective and versatile option that offers good electrical and mechanical properties. FR4 PCBs are suitable for a wide range of applications, from consumer electronics to industrial control systems.
Properties of FR4 PCB Laminate
- Dielectric constant (4.5 at 1 MHz)
- Dissipation factor (0.02 at 1 MHz)
- Glass transition temperature (Tg) around 135°C
- Good mechanical strength and dimensional stability
- Flame retardant properties
- Moderate moisture absorption
Advantages of FR4 PCB Laminate
- Cost-effective and widely available
- Good balance of electrical and mechanical properties
- Suitable for a wide range of applications
- Easier to manufacture and process compared to PTFE
- Supports multilayer designs and high-density interconnects
Disadvantages of FR4 PCB Laminate
- Higher dielectric constant and dissipation factor compared to PTFE
- Limited performance at high frequencies and microwave applications
- Lower thermal stability and heat resistance compared to PTFE
- Susceptible to moisture absorption, which can affect electrical properties
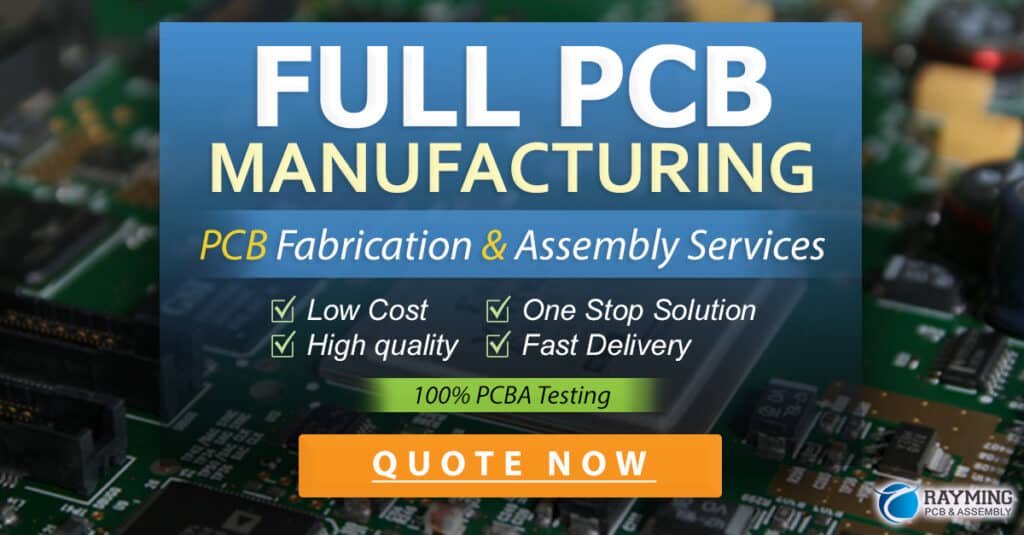
Comparing PTFE and FR4 PCB Laminate Materials
Property | PTFE | FR4 |
---|---|---|
Dielectric Constant | 2.1 | 4.5 (at 1 MHz) |
Dissipation Factor | 0.0002 | 0.02 (at 1 MHz) |
Thermal Stability | Up to 260°C | Glass transition at 135°C |
Moisture Absorption | Low | Moderate |
Chemical Resistance | Excellent | Good |
Mechanical Strength | Lower than FR4 | Good |
Ease of Manufacturing | More challenging | Easier |
Cost | Higher | Lower |
Applications of PTFE PCB Laminate
- High-frequency and microwave circuits
- Radar and satellite communication systems
- Aerospace and defense electronics
- Medical imaging equipment (MRI, CT scanners)
- High-speed digital signaling
- RF and wireless applications
Applications of FR4 PCB Laminate
- Consumer electronics (smartphones, laptops, TVs)
- Industrial control systems and automation
- Automotive electronics
- Telecommunications equipment
- Medical devices and instrumentation
- General-purpose PCBs
Factors to Consider When Choosing Between PTFE and FR4 PCB Laminate
- Electrical performance requirements (frequency, signal integrity)
- Thermal stability and heat dissipation needs
- Chemical and environmental exposure
- Mechanical strength and dimensional stability
- Manufacturing complexity and cost constraints
- Compliance with industry standards and regulations
Best Practices for Designing and Manufacturing PTFE and FR4 PCBs
PTFE PCB Design Considerations
- Optimize the dielectric thickness to minimize signal loss
- Use copper cladding with low surface roughness for better high-frequency performance
- Employ proper grounding and shielding techniques to reduce EMI and crosstalk
- Consider the thermal expansion mismatch between PTFE and other materials
FR4 PCB Design Considerations
- Choose the appropriate FR4 grade based on the application requirements
- Employ proper trace width and spacing to minimize crosstalk and impedance mismatch
- Use appropriate via design and placement to ensure signal integrity
- Consider the impact of moisture absorption on the electrical properties of FR4
Manufacturing Considerations for PTFE PCBs
- Use specialized equipment and processes for handling PTFE laminates
- Employ precise temperature control during the lamination process
- Use compatible adhesives and surface treatments for improved bonding
- Implement strict quality control measures to ensure consistent performance
Manufacturing Considerations for FR4 PCBs
- Optimize the lamination process to minimize voids and delamination
- Use appropriate drill bits and parameters for clean and accurate hole drilling
- Employ proper etching and plating techniques to ensure reliable copper traces
- Implement quality control measures to detect and prevent manufacturing defects
Conclusion
PTFE and FR4 are two widely used PCB laminate materials, each with its own unique properties and applications. PTFE excels in high-frequency and microwave applications, offering superior electrical performance and thermal stability. On the other hand, FR4 is a cost-effective and versatile option suitable for a wide range of general-purpose PCBs. When choosing between PTFE and FR4, it is essential to consider the specific requirements of the application, including electrical performance, thermal stability, chemical resistance, and cost constraints. By understanding the strengths and limitations of each material and following best practices in design and manufacturing, engineers can create high-quality and reliable PCBs that meet the demands of their applications.
Frequently Asked Questions (FAQ)
1. What is the main difference between PTFE and FR4 PCB laminate materials?
The main difference between PTFE and FR4 PCB laminate materials lies in their electrical properties. PTFE has a lower dielectric constant and dissipation factor, making it suitable for high-frequency and microwave applications. FR4, on the other hand, has a higher dielectric constant and dissipation factor but offers a good balance of electrical and mechanical properties at a lower cost.
2. Can PTFE PCBs be used for multilayer designs?
While PTFE PCBs can be used for multilayer designs, the options are more limited compared to FR4. The manufacturing process for multilayer PTFE PCBs is more complex and challenging, which can increase the cost and lead time.
3. Is FR4 suitable for high-frequency applications?
FR4 is not the best choice for high-frequency applications due to its higher dielectric constant and dissipation factor. As the frequency increases, the signal loss and distortion become more significant with FR4. For high-frequency applications, PTFE or other low-loss materials are preferred.
4. How does moisture absorption affect FR4 PCBs?
Moisture absorption can affect the electrical properties of FR4 PCBs, leading to changes in dielectric constant and dissipation factor. This can result in signal integrity issues and reduced performance, particularly in high-humidity environments. Proper design and manufacturing techniques, such as using conformal coatings or moisture barriers, can help mitigate the effects of moisture absorption.
5. What are the key considerations when designing PTFE PCBs?
When designing PTFE PCBs, some key considerations include optimizing the dielectric thickness to minimize signal loss, using copper cladding with low surface roughness for better high-frequency performance, employing proper grounding and shielding techniques to reduce EMI and crosstalk, and accounting for the thermal expansion mismatch between PTFE and other materials. Careful attention to these factors can help ensure the optimal performance of PTFE PCBs in high-frequency applications.
Leave a Reply