Introduction to PCB Phototools
Printed Circuit Boards (PCBs) are essential components in modern electronics, forming the backbone of countless devices we use every day. The process of creating these complex circuits involves transferring a designed pattern onto a copper-clad board. One of the most critical steps in this process is the use of phototools, which are high-resolution photographic films or masks used to transfer the circuit pattern onto the PCB substrate. In this article, we will delve into the world of PCB phototools, exploring their types, characteristics, and the role they play in the PCB manufacturing process.
What are PCB Phototools?
PCB phototools, also known as photomasks or artwork films, are transparent sheets with a precise, high-resolution image of the circuit pattern printed on them. These tools are used in the photolithography process, where the circuit design is transferred onto the photosensitive layer (photoresist) of the copper-clad PCB substrate. The photoresist is exposed to UV light through the phototool, causing it to harden in the areas where the light passes through the transparent parts of the phototool. The unexposed areas of the photoresist are then removed during the development process, leaving behind a precise replica of the circuit pattern on the copper layer.
Importance of High-Quality Phototools
The quality of the phototool directly affects the accuracy and reliability of the resulting PCB. High-quality phototools ensure that the circuit pattern is transferred onto the PCB substrate with minimal distortions, sharp edges, and accurate feature sizes. Poor-quality phototools can lead to issues such as:
- Inconsistent line widths
- Broken or incomplete traces
- Short circuits or open circuits
- Reduced manufacturing yield
- Increased production costs
To avoid these problems, it is crucial to use high-quality phototools that meet the required specifications for your PCB design.
Types of PCB Phototools
There are several types of PCB phototools available, each with its own advantages and disadvantages. The choice of phototool depends on factors such as the complexity of the circuit design, the desired resolution, and the production volume. Let’s explore the most common types of PCB phototools:
1. Film Phototools
Film phototools are the most widely used type of phototool in the PCB industry. They are created by printing the circuit pattern onto a transparent film using a high-resolution photoplotter or imagesetter. The film is typically made of polyester or acetate and has a silver halide emulsion layer that produces high-contrast, sharp images when exposed to light. Film phototools offer several advantages:
- High resolution (up to 50,000 dpi)
- Excellent dimensional stability
- Good UV light transmission
- Relatively low cost for small to medium production volumes
However, film phototools also have some limitations:
- Limited lifespan due to wear and tear
- Susceptible to scratches and contamination
- Requires careful handling and storage
- Not suitable for high-volume production
2. Glass Phototools
Glass phototools are a more durable alternative to film phototools. They are created by etching the circuit pattern onto a glass substrate coated with a chrome layer. The chrome layer is selectively removed to create the transparent areas of the phototool. Glass phototools offer several advantages over film phototools:
- Excellent durability and longevity
- High resolution (up to 100,000 dpi)
- Excellent dimensional stability
- Resistant to scratches and contamination
- Suitable for high-volume production
However, glass phototools also have some drawbacks:
- Higher cost compared to film phototools
- Longer lead times for production
- More fragile and prone to breakage if mishandled
- Requires specialized equipment for creation
3. Laser Direct Imaging (LDI)
Laser Direct Imaging (LDI) is a relatively new technology that eliminates the need for physical phototools altogether. In LDI, a laser beam directly writes the circuit pattern onto the photoresist-coated PCB substrate. This process offers several advantages:
- Eliminates the need for physical phototools, reducing costs and lead times
- Enables quick design changes and corrections
- Suitable for high-volume production
- Offers high resolution and accuracy
However, LDI also has some limitations:
- Requires specialized and expensive equipment
- May not be cost-effective for low-volume production
- Requires skilled operators and maintenance
Characteristics of High-Quality Phototools
To ensure the best results in PCB manufacturing, it is essential to use high-quality phototools that meet the following characteristics:
1. High Resolution
The resolution of a phototool refers to the smallest feature size that can be accurately reproduced. Higher resolutions enable the creation of finer traces, smaller vias, and more intricate designs. The resolution of a phototool is typically measured in dots per inch (dpi) or micrometers (μm). For most PCB applications, a resolution of at least 10,000 dpi (2.5 μm) is recommended.
2. High Contrast
High contrast is crucial for producing sharp, well-defined images on the PCB substrate. The contrast of a phototool is determined by the difference in optical density between the transparent and opaque areas. A high-contrast phototool should have a density difference of at least 3.0, ensuring that the UV light is effectively blocked in the opaque areas while allowing maximum transmission in the transparent areas.
3. Dimensional Stability
Dimensional stability refers to the ability of a phototool to maintain its size and shape under varying environmental conditions, such as temperature and humidity changes. Any dimensional changes in the phototool can lead to misalignment or distortion of the circuit pattern on the PCB. High-quality phototools should have minimal dimensional changes, typically less than 0.1% over the expected range of operating conditions.
4. Low Defect Density
Defects in a phototool, such as pinholes, scratches, or dust particles, can cause unwanted features or discontinuities in the transferred circuit pattern. High-quality phototools should have a low defect density, typically less than 0.1 defects per square inch. Careful handling, storage, and cleaning of phototools can help minimize the occurrence of defects.
5. Proper Alignment and Registration
In multi-layer PCBs, accurate alignment and registration of the phototools for each layer are critical for ensuring proper electrical connections between layers. High-quality phototools should have precise alignment marks or fiducials that enable accurate registration during the exposure process. The alignment tolerance should be within the specified limits for the PCB design, typically less than 25 μm (1 mil).
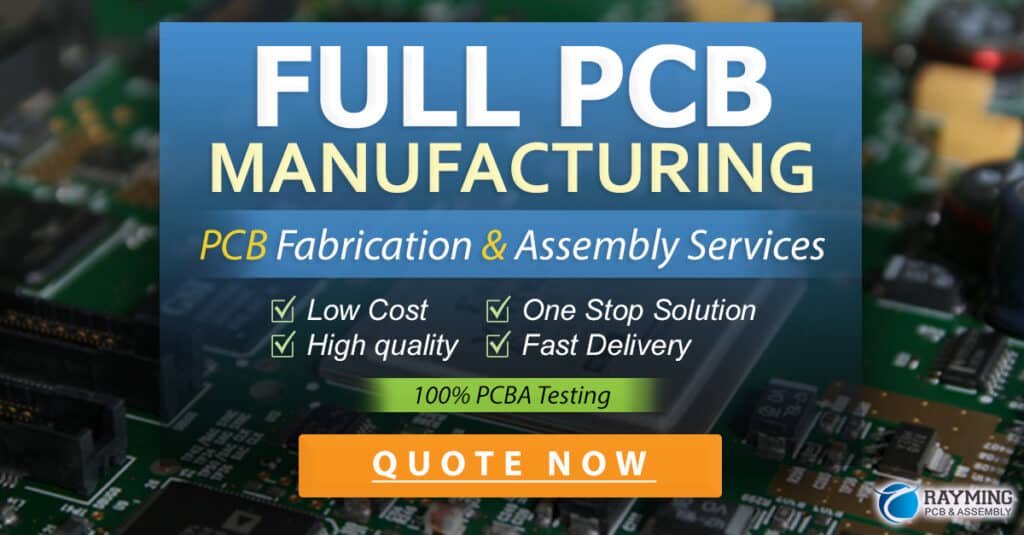
Phototool Creation Process
The process of creating a high-quality phototool involves several steps, each of which contributes to the final quality of the tool. Let’s break down the phototool creation process:
1. Design Preparation
The first step in creating a phototool is to prepare the PCB design files. The design should be carefully reviewed and optimized for manufacturability, ensuring that all features meet the minimum size and spacing requirements for the chosen fabrication process. The design files are typically created using Electronic Design Automation (EDA) software and exported in a format compatible with the photoplotter or imagesetter, such as Gerber or DXF.
2. Film Selection
The choice of film for the phototool depends on the desired resolution, contrast, and durability. High-quality films, such as polyester or acetate, with a silver halide emulsion layer, are commonly used for their excellent imaging properties and dimensional stability. The film thickness and base material should be selected based on the requirements of the exposure equipment and the expected handling conditions.
3. Photoplotter or Imagesetter Setup
The photoplotter or imagesetter is a specialized device that exposes the film to light based on the input design files. The device must be properly calibrated and maintained to ensure consistent and accurate imaging. Key parameters, such as exposure settings, focus, and alignment, should be optimized for the specific film type and design requirements.
4. Exposure and Development
Once the film is loaded into the photoplotter or imagesetter, the device exposes the film to light, creating a latent image of the circuit pattern. The exposed film is then developed using a chemical process that converts the latent image into a visible, high-contrast image. The development process must be carefully controlled to ensure proper image formation and to minimize the occurrence of defects.
5. Inspection and Quality Control
After development, the phototool must be thoroughly inspected for defects, dimensional accuracy, and image quality. Automated inspection systems or manual visual inspection can be used to identify any issues, such as pinholes, scratches, or misaligned features. Phototools that do not meet the required specifications should be rejected and remade to ensure the best possible results in PCB fabrication.
6. Packaging and Storage
High-quality phototools should be properly packaged and stored to prevent damage during handling and transport. Phototools should be placed in clean, dust-free containers and stored in a controlled environment with stable temperature and humidity conditions. Proper labeling and identification of the phototools are essential for easy retrieval and use in the PCB manufacturing process.
Phototool Maintenance and Handling
To ensure the longevity and consistent performance of PCB phototools, proper maintenance and handling practices must be followed:
1. Cleaning
Phototools should be regularly cleaned to remove any dust, debris, or fingerprints that may affect the image quality. Use a soft, lint-free cloth and a specialized cleaning solution designed for photographic films or glass substrates. Avoid using abrasive materials or harsh chemicals that can damage the phototool surface.
2. Handling
When handling phototools, always wear clean, lint-free gloves to prevent fingerprints and contamination. Hold the phototool by the edges to minimize contact with the image area. Avoid bending, folding, or scratching the phototool, as this can cause permanent damage and affect the image quality.
3. Storage
Store phototools in a clean, dust-free environment with controlled temperature and humidity conditions. Use appropriate storage containers or envelopes designed for photographic films or glass substrates. Avoid exposing the phototools to direct sunlight or extreme temperatures, as this can cause dimensional changes or degradation of the image quality.
4. Inspection
Regularly inspect the phototools for any signs of wear, damage, or contamination. Check for scratches, pinholes, or debris that may affect the image quality. Replace or repair damaged phototools as needed to ensure consistent performance in the PCB manufacturing process.
Frequently Asked Questions (FAQ)
-
What is the difference between a film phototool and a glass phototool?
Film phototools are created by printing the circuit pattern onto a transparent film, while glass phototools are created by etching the pattern onto a chrome-coated glass substrate. Glass phototools offer higher durability, resolution, and stability, but are more expensive and fragile compared to film phototools. -
What is the recommended resolution for PCB phototools?
For most PCB applications, a resolution of at least 10,000 dpi (2.5 μm) is recommended to ensure accurate reproduction of fine features and traces. -
How can I minimize the occurrence of defects in my phototools?
To minimize defects, handle phototools with care using clean, lint-free gloves, store them in a controlled environment, and regularly inspect them for any signs of damage or contamination. Proper cleaning and maintenance practices can also help reduce the occurrence of defects. -
What is Laser Direct Imaging (LDI), and how does it differ from traditional phototools?
Laser Direct Imaging (LDI) is a technology that eliminates the need for physical phototools by directly writing the circuit pattern onto the photoresist-coated PCB substrate using a laser beam. LDI offers high resolution, accuracy, and quick design changes, but requires specialized equipment and may not be cost-effective for low-volume production. -
How often should I replace my PCB phototools?
The lifespan of a phototool depends on various factors, such as the type of phototool, handling conditions, and usage frequency. Film phototools generally have a shorter lifespan due to wear and tear, while glass phototools can last longer with proper care. Regularly inspect your phototools for any signs of damage or degradation, and replace them as needed to ensure consistent performance in PCB manufacturing.
Conclusion
PCB phototools play a critical role in the accurate and reliable transfer of circuit patterns onto PCB substrates. By understanding the types, characteristics, and creation process of high-quality phototools, PCB manufacturers can ensure the best possible results in their fabrication processes. Proper maintenance and handling of phototools are also essential for consistent performance and longevity.
As PCB designs continue to evolve and become more complex, the demand for high-quality phototools will only increase. Innovations in phototool technology, such as Laser Direct Imaging (LDI), offer new possibilities for faster, more accurate, and cost-effective PCB manufacturing. By staying informed about the latest developments in phototool technology and best practices, PCB manufacturers can remain competitive and deliver high-quality products to their customers.
Leave a Reply