Types of PCB Materials
There are several types of PCB materials available, each with its own unique properties and characteristics. The most common PCB materials include:
- FR-4
- High Tg FR-4
- Polyimide
- Teflon
- Ceramic
- Aluminum
- Copper
Let’s take a closer look at each of these materials and their applications.
FR-4
FR-4 is the most widely used PCB material. It is a composite material made of woven fiberglass cloth with an epoxy resin binder. FR-4 is known for its excellent mechanical and electrical properties, making it suitable for a wide range of applications.
Property | Value |
---|---|
Dielectric Constant | 4.2 – 4.6 |
Dissipation Factor | 0.02 |
Thermal Conductivity | 0.3 W/mK |
Glass Transition Temperature (Tg) | 130°C – 140°C |
Dimensional Stability | Good |
Flame Retardancy | UL94 V-0 |
FR-4 is commonly used in consumer electronics, telecommunications equipment, and industrial control systems.
High Tg FR-4
High Tg FR-4 is a variant of the standard FR-4 material with a higher glass transition temperature (Tg). This property makes it more suitable for applications that require higher thermal stability and reliability.
Property | Value |
---|---|
Dielectric Constant | 4.2 – 4.6 |
Dissipation Factor | 0.02 |
Thermal Conductivity | 0.3 W/mK |
Glass Transition Temperature (Tg) | 170°C – 180°C |
Dimensional Stability | Excellent |
Flame Retardancy | UL94 V-0 |
High Tg FR-4 is often used in automotive electronics, aerospace applications, and high-reliability industrial systems.
Polyimide
Polyimide is a high-performance polymer material known for its excellent thermal stability, chemical resistance, and mechanical strength. It is often used in applications that require operation at high temperatures or exposure to harsh environments.
Property | Value |
---|---|
Dielectric Constant | 3.5 |
Dissipation Factor | 0.002 |
Thermal Conductivity | 0.2 W/mK |
Glass Transition Temperature (Tg) | 260°C – 400°C |
Dimensional Stability | Excellent |
Flame Retardancy | UL94 V-0 |
Polyimide is commonly used in aerospace, military, and high-temperature applications.
Teflon
Teflon, also known as polytetrafluoroethylene (PTFE), is a low-loss dielectric material with excellent chemical resistance and a wide operating temperature range. It is often used in high-frequency and microwave applications.
Property | Value |
---|---|
Dielectric Constant | 2.1 |
Dissipation Factor | 0.0002 |
Thermal Conductivity | 0.25 W/mK |
Glass Transition Temperature (Tg) | 327°C |
Dimensional Stability | Excellent |
Flame Retardancy | UL94 V-0 |
Teflon PCBs are used in radar systems, satellite communications, and high-frequency test equipment.
Ceramic
Ceramic PCBs are made from inorganic materials, such as alumina or beryllia. They offer excellent thermal conductivity, high dielectric strength, and low loss at high frequencies. Ceramic PCBs are often used in high-power and high-frequency applications.
Property | Alumina (Al2O3) | Beryllia (BeO) |
---|---|---|
Dielectric Constant | 9.8 | 6.7 |
Dissipation Factor | 0.0001 | 0.0004 |
Thermal Conductivity | 20 W/mK | 260 W/mK |
Dimensional Stability | Excellent | Excellent |
Flame Retardancy | Non-flammable | Non-flammable |
Ceramic PCBs are used in high-power LED lighting, RF power amplifiers, and laser systems.
Aluminum
Aluminum PCBs consist of an aluminum substrate with a dielectric layer and copper traces. They provide excellent thermal dissipation and mechanical stability, making them suitable for high-power and heat-sensitive applications.
Property | Value |
---|---|
Dielectric Constant | 4.5 – 4.9 |
Dissipation Factor | 0.02 |
Thermal Conductivity | 1.0 – 2.0 W/mK |
Dimensional Stability | Excellent |
Flame Retardancy | Non-flammable |
Aluminum PCBs are commonly used in power electronics, automotive lighting, and high-brightness LED applications.
Copper
Copper PCBs are made entirely of copper, offering the highest thermal conductivity among all PCB materials. They are often used in applications that require extreme heat dissipation, such as high-power electronics and laser diodes.
Property | Value |
---|---|
Thermal Conductivity | 400 W/mK |
Dimensional Stability | Excellent |
Flame Retardancy | Non-flammable |
Copper PCBs are used in high-power motor drives, welding equipment, and high-energy physics experiments.
PCB Services Based on Material Choice
PCB fabrication services vary depending on the chosen material. Some materials require specialized processing techniques, while others can be handled using standard manufacturing methods. Let’s explore the services associated with each material.
FR-4 and High Tg FR-4 Services
- Standard PCB fabrication: FR-4 and High Tg FR-4 can be processed using standard PCB manufacturing techniques, such as drilling, plating, and etching.
- Multilayer PCBs: Both materials are suitable for fabricating multilayer PCBs with up to 40 layers or more.
- Surface finishes: Various surface finishes, such as HASL, ENIG, and OSP, can be applied to FR-4 and High Tg FR-4 PCBs.
- Soldermask and silkscreen: Standard soldermask and silkscreen printing techniques are compatible with these materials.
Polyimide Services
- Flexible PCBs: Polyimide is the primary material used in the fabrication of flexible PCBs.
- Rigid-flex PCBs: Polyimide can be combined with rigid materials like FR-4 to create rigid-flex PCBs.
- High-temperature assembly: Polyimide PCBs can withstand high-temperature soldering processes, such as reflow and wave soldering.
- Specialized surface finishes: High-temperature tolerant surface finishes, such as gold and silver, can be applied to polyimide PCBs.
Teflon Services
- High-frequency PCB fabrication: Teflon PCBs are fabricated using specialized techniques to maintain their low-loss properties at high frequencies.
- Microwave PCBs: Teflon is the material of choice for microwave PCBs operating at frequencies up to 100 GHz.
- Controlled impedance: Teflon PCBs can be fabricated with tightly controlled impedance for optimal signal integrity.
- Low-profile surface finishes: Thin surface finishes, such as immersion silver and immersion tin, are used to minimize signal loss on Teflon PCBs.
Ceramic Services
- Thick-film processing: Ceramic PCBs can be fabricated using thick-film processing techniques, such as screen printing and firing.
- Thin-film processing: For high-precision applications, thin-film processing methods like sputtering and evaporation can be used on ceramic substrates.
- Brazed assembly: Ceramic PCBs can be assembled using high-temperature brazing processes for improved reliability.
- Hermetic packaging: Ceramic PCBs can be hermetically sealed for operation in extreme environments.
Aluminum Services
- Insulated Metal Substrate (IMS) PCBs: Aluminum PCBs are often referred to as IMS PCBs, which consist of an aluminum substrate, a dielectric layer, and copper traces.
- Thermal management: Aluminum PCBs are designed to efficiently dissipate heat from power components.
- Metal Core PCBs (MCPCB): MCPCBs are a type of aluminum PCB with a thicker aluminum core for enhanced thermal performance.
- High-current handling: Aluminum PCBs can be fabricated with thick copper layers for high-current applications.
Copper Services
- Heavy copper PCBs: Copper PCBs can be fabricated with copper thicknesses up to several millimeters for extreme high-power applications.
- Direct Bonded Copper (DBC) substrates: DBC substrates consist of a ceramic base with copper layers directly bonded to both sides for excellent thermal performance.
- Skived heatsinks: Copper PCBs can be fabricated with integrated skived heatsinks for improved heat dissipation.
- Specialized assembly techniques: Copper PCBs require specialized assembly techniques, such as soldering or brazing, to ensure reliable connections.
FAQ
-
Q: What is the most common PCB material?
A: FR-4 is the most widely used PCB material due to its excellent balance of mechanical, electrical, and thermal properties, as well as its cost-effectiveness. -
Q: Which PCB material is best for high-frequency applications?
A: Teflon (PTFE) is the preferred material for high-frequency and microwave applications due to its low dielectric constant and dissipation factor, which minimize signal loss at high frequencies. -
Q: Can aluminum PCBs replace heatsinks?
A: Aluminum PCBs can provide excellent thermal dissipation, reducing the need for additional heatsinks in some applications. However, they may not completely replace heatsinks in high-power applications that generate excessive heat. -
Q: Are ceramic PCBs more expensive than FR-4?
A: Yes, ceramic PCBs are generally more expensive than FR-4 due to the higher material costs and specialized processing techniques required for their fabrication. -
Q: What is the main advantage of using copper PCBs?
A: The main advantage of using copper PCBs is their unparalleled thermal conductivity, which makes them ideal for applications that generate extreme amounts of heat, such as high-power electronics and laser systems.
In conclusion, the choice of PCB material is a critical factor in determining the performance, reliability, and cost of a PCB. Each material has its own unique properties and characteristics that make it suitable for specific applications. By understanding the different PCB materials and their associated services, designers and engineers can make informed decisions when selecting the appropriate material for their projects.
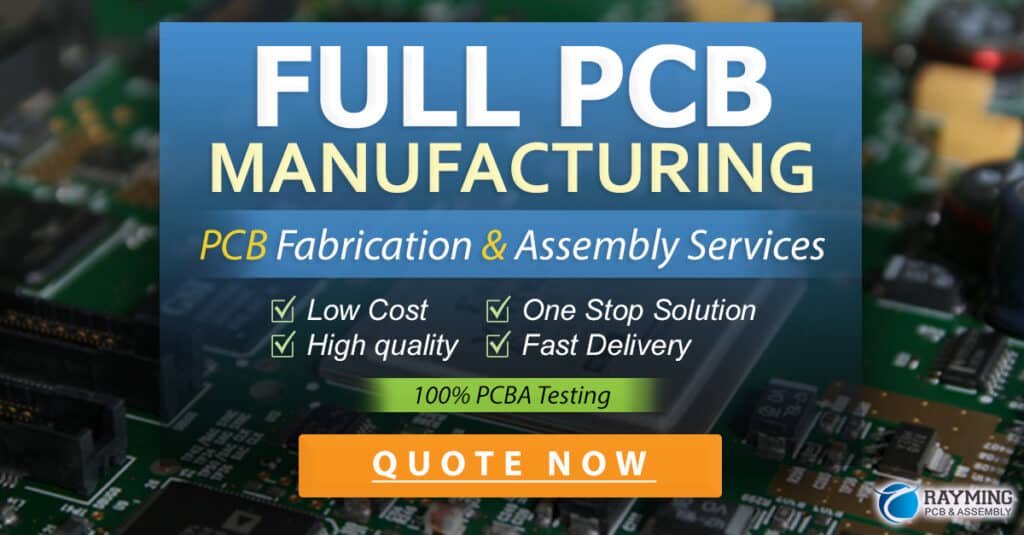
Leave a Reply