Introduction to PCB-DM
PCB-DM, short for Printed Circuit Board Design and Manufacturing, is a comprehensive process that involves the creation and production of electronic circuits on a flat insulating surface. This technology has revolutionized the electronics industry by enabling the development of compact, reliable, and cost-effective electronic devices. In this article, we will delve into the various aspects of PCB-DM, including its history, design process, manufacturing techniques, and applications.
History of PCB-DM
The concept of printed circuit boards dates back to the early 20th century when inventors began experimenting with methods to create electrical connections on a flat surface. However, it wasn’t until the 1940s that the first practical PCBs were developed for use in military equipment during World War II. These early PCBs were made using a subtractive process, where a layer of copper was etched away to create the desired circuit pattern.
In the decades that followed, PCB technology continued to evolve, with the introduction of new materials, manufacturing techniques, and design software. The development of through-hole technology in the 1950s allowed for the creation of double-sided PCBs, while the introduction of surface-mount technology (SMT) in the 1980s enabled the production of smaller, more densely packed boards.
PCB Design Process
The PCB design process is a critical step in the creation of electronic devices. It involves the use of specialized software to create a virtual representation of the circuit layout, which is then used to manufacture the physical board. The design process typically involves the following steps:
Schematic Design
The first step in the PCB design process is to create a schematic diagram of the electronic circuit. This diagram represents the electrical connections between components using standardized symbols and notation. The schematic is created using electronic design automation (EDA) software, such as Altium Designer, Eagle, or KiCad.
Component Selection
Once the schematic is complete, the next step is to select the components that will be used in the circuit. This involves choosing the appropriate resistors, capacitors, integrated circuits, and other components based on their electrical characteristics and physical dimensions. The component selection process also takes into account factors such as cost, availability, and reliability.
PCB Layout
With the schematic and components in place, the next step is to create the physical layout of the PCB. This involves arranging the components on the board and routing the electrical connections between them. The layout process is typically done using the same EDA software used for schematic design, and it requires careful consideration of factors such as signal integrity, electromagnetic compatibility, and thermal management.
Design Rule Check (DRC)
Before the PCB design can be sent for manufacturing, it must undergo a design rule check (DRC) to ensure that it meets the necessary manufacturing and assembly requirements. The DRC process checks for issues such as minimum trace widths, clearances between components, and drill hole sizes. Any errors or violations detected during the DRC must be corrected before the design can be finalized.
PCB Manufacturing Techniques
Once the PCB design is complete, it is sent to a manufacturing facility for production. There are several different manufacturing techniques used to create PCBs, each with its own advantages and limitations.
Subtractive Manufacturing
Subtractive manufacturing is the traditional method of PCB production, where a layer of copper is selectively removed from a substrate material to create the desired circuit pattern. This process typically involves the following steps:
- A substrate material, such as FR-4, is coated with a layer of copper on one or both sides.
- A photoresist layer is applied to the copper and exposed to UV light through a photomask, which contains the circuit pattern.
- The unexposed photoresist is removed, leaving behind a protective layer in the shape of the circuit pattern.
- The exposed copper is etched away using a chemical solution, leaving behind the desired circuit traces.
- The remaining photoresist is removed, and the board is cleaned and inspected.
Subtractive manufacturing is a well-established and reliable method of PCB production, but it has some limitations in terms of minimum feature sizes and waste generation.
Additive Manufacturing
Additive manufacturing, also known as 3D printing, is a newer method of PCB production that involves the selective deposition of conductive materials onto a substrate. This process typically involves the following steps:
- A substrate material is coated with a layer of insulating material, such as plastic or ceramic.
- A print head deposits conductive material, such as silver or copper, onto the substrate in the desired circuit pattern.
- The deposited material is cured or sintered to create a solid circuit trace.
- The process is repeated to build up multiple layers of circuitry as needed.
Additive manufacturing has the potential to create more complex and customized PCB designs than traditional subtractive methods, but it is still an emerging technology with some limitations in terms of speed and material properties.
PCB Assembly
Once the PCB has been manufactured, it must be assembled with the necessary components to create a functional electronic device. There are two main methods of PCB assembly: through-hole and surface-mount.
Through-Hole Assembly
Through-hole assembly involves inserting component leads through drilled holes in the PCB and soldering them in place on the opposite side. This method is well-suited for larger components and provides a strong mechanical connection, but it requires more manual labor and takes up more space on the board.
Surface-Mount Assembly
Surface-mount assembly involves placing components directly onto pads on the surface of the PCB and soldering them in place using a reflow oven. This method allows for smaller components and higher component density, but it requires more precise placement and can be more susceptible to thermal stress.
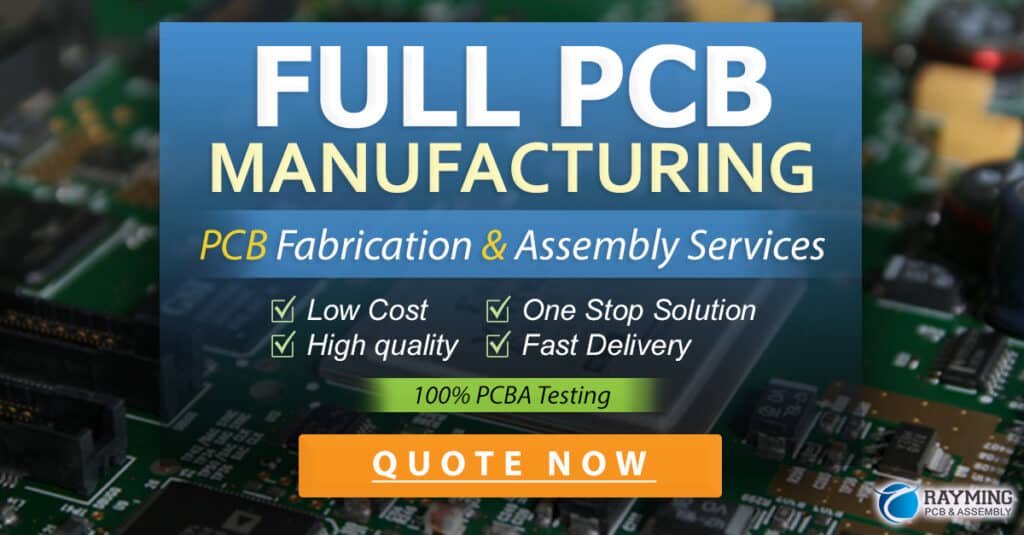
Applications of PCB-DM
PCB-DM technology is used in a wide range of electronic devices and systems, from consumer electronics to industrial control systems. Some common applications include:
Consumer Electronics
PCBs are found in virtually all modern consumer electronic devices, including smartphones, tablets, laptops, televisions, and home appliances. The compact size and reliability of PCBs have enabled the development of increasingly sophisticated and feature-rich devices.
Automotive Electronics
PCBs are used extensively in modern vehicles for applications such as engine control, infotainment systems, and advanced driver assistance systems (ADAS). The harsh operating environment and strict reliability requirements of automotive electronics require specialized PCB design and manufacturing techniques.
Medical Devices
PCBs are used in a wide range of medical devices, from diagnostic equipment to implantable devices such as pacemakers and insulin pumps. The high reliability and small size of PCBs are critical for these applications, where failure could have serious consequences for patient health.
Industrial Control Systems
PCBs are used in industrial control systems for applications such as process control, automation, and robotics. These systems require rugged and reliable PCBs that can withstand harsh operating conditions and provide long-term reliability.
Aerospace and Defense
PCBs are used extensively in aerospace and defense applications, where reliability and performance are critical. Specialized PCB design and manufacturing techniques are used to create boards that can withstand extreme temperatures, vibration, and radiation.
Future Trends in PCB-DM
As electronic devices continue to become smaller, more complex, and more integrated, the demands on PCB design and manufacturing are also increasing. Some of the key trends shaping the future of PCB-DM include:
High-Density Interconnect (HDI)
HDI technology involves the use of smaller vias, finer pitch components, and thinner substrates to create PCBs with higher component density and improved signal integrity. HDI is becoming increasingly important for applications such as 5G wireless, where high-frequency signals require shorter signal paths and reduced crosstalk.
Flexible and Stretchable PCBs
Flexible and stretchable PCBs are emerging as a key technology for wearable electronics and other applications where conformability and durability are critical. These PCBs use specialized materials and manufacturing techniques to create circuits that can bend, stretch, and twist without breaking.
Embedded Components
Embedded components, such as resistors and capacitors, are increasingly being integrated directly into the PCB substrate to save space and improve performance. This technology requires specialized manufacturing techniques and materials, but it has the potential to enable even smaller and more integrated electronic devices.
Sustainable Manufacturing
As concerns about environmental sustainability continue to grow, there is increasing pressure on the electronics industry to adopt more sustainable manufacturing practices. This includes the use of renewable energy, the reduction of waste and hazardous materials, and the development of more recyclable and biodegradable PCB materials.
Frequently Asked Questions (FAQ)
What is the difference between a PCB and a PCBA?
A PCB (printed circuit board) is the bare board with the copper traces and pads, while a PCBA (printed circuit board assembly) is the board with all the components soldered onto it. In other words, a PCBA is a fully assembled and functional electronic circuit, while a PCB is just the substrate on which the circuit is built.
What are the different types of PCBs?
There are several different types of PCBs, including:
- Single-sided PCBs, which have components and traces on only one side of the board.
- Double-sided PCBs, which have components and traces on both sides of the board.
- Multi-layer PCBs, which have multiple layers of traces and insulating material sandwiched together.
- Flexible PCBs, which use flexible substrates to allow for bending and folding.
- Rigid-flex PCBs, which combine rigid and flexible sections for added durability and conformability.
What is the typical turnaround time for PCB manufacturing?
The turnaround time for PCB manufacturing can vary depending on the complexity of the design, the manufacturing process used, and the workload of the manufacturer. In general, simple PCBs can be manufactured in as little as 24 hours, while more complex designs may take several weeks. Rush services are often available for an additional fee.
What are some common PCB manufacturing defects?
Some common PCB manufacturing defects include:
- Short circuits, where two or more traces are unintentionally connected.
- Open circuits, where a trace is broken or disconnected.
- Incorrect hole sizes or locations.
- Incorrect component placement or orientation.
- Solder bridges, where solder inadvertently connects two or more pads.
How can I ensure the reliability of my PCB design?
There are several steps you can take to ensure the reliability of your PCB design, including:
- Following best practices for component selection and placement.
- Using appropriate trace widths and spacings for the expected current and voltage levels.
- Incorporating redundancy and failsafe mechanisms where appropriate.
- Performing thorough testing and validation of the design before manufacturing.
- Choosing a reputable and experienced PCB manufacturer with a track record of quality and reliability.
By following these guidelines and staying up-to-date with the latest trends and technologies in PCB-DM, you can create electronic devices that are reliable, efficient, and cost-effective.
Conclusion
PCB-DM is a critical technology that underlies the modern electronics industry. From consumer devices to industrial control systems, PCBs enable the creation of compact, reliable, and high-performance electronic circuits that power our world. As the demands on electronic devices continue to increase, the field of PCB-DM is also evolving, with new materials, manufacturing techniques, and design tools emerging to meet these challenges. By staying informed about these developments and working with experienced professionals in the field, companies can create innovative and competitive electronic products that meet the needs of today’s consumers and businesses.
Layer Count | Typical Applications | Manufacturing Complexity | Cost |
---|---|---|---|
Single | Simple circuits, hobbyist projects | Low | Low |
Double | Most consumer electronics, Arduino boards | Medium | Medium |
4-8 | Complex devices, industrial controls | High | High |
10+ | High-performance computing, aerospace | Very High | Very High |
Table 1: Comparison of different PCB layer counts and their typical applications, manufacturing complexity, and cost.
Manufacturing Process | Advantages | Disadvantages |
---|---|---|
Subtractive | Well-established, reliable, cost-effective | Limited feature size, waste generation |
Additive | Enables complex geometries, less waste | Slower, limited material options |
Table 2: Comparison of subtractive and additive PCB manufacturing processes, including their advantages and disadvantages.
Leave a Reply