Introduction to PCB Classification
Printed Circuit Boards (PCBs) are essential components in modern electronics, providing a platform for mounting and connecting electronic components. To ensure the proper functioning and reliability of PCBs, it is crucial to classify them based on various criteria. Two important aspects of PCB classification are Pattern Class and Drill Class. These classifications help manufacturers, designers, and end-users understand the capabilities and limitations of a particular PCB, ensuring the right board is selected for the intended application.
In this article, we will delve into the details of PCB Pattern Class and Drill Class, exploring their definitions, standards, and the factors that influence these classifications. By understanding these concepts, you will be better equipped to make informed decisions when designing, manufacturing, or utilizing PCBs in your projects.
What is PCB Pattern Class?
PCB Pattern Class, also known as PCB Feature Class, refers to the level of precision and complexity of the conductive patterns on a PCB. It takes into account factors such as line width, spacing, and feature size. The pattern class determines the achievable resolution and density of the PCB layout, which directly impacts the board’s functionality and performance.
IPC Standards for Pattern Class
The IPC (Institute for Printed Circuits) is a global trade association that develops and publishes standards for the electronics industry. IPC-6011, IPC-6012, and IPC-6013 are the primary standards that define the requirements for PCB Pattern Class.
These standards classify PCBs into three main pattern classes:
Pattern Class | Description |
---|---|
Class 1 | General electronic products, where function is the primary concern |
Class 2 | Dedicated service electronic products, where extended life and continued performance are required |
Class 3 | High-reliability electronic products, where continued performance or performance-on-demand is critical |
Each pattern class has specific requirements for minimum line width, spacing, and feature size, as outlined in the IPC standards.
Factors Affecting Pattern Class
Several factors influence the achievable pattern class of a PCB:
-
Manufacturing technology: The capabilities of the PCB manufacturing process, such as etching, plating, and lamination, determine the minimum feature sizes and tolerances that can be achieved.
-
Material properties: The choice of substrate material, copper thickness, and surface finish can impact the resolution and accuracy of the conductive patterns.
-
Design complexity: The complexity of the PCB layout, including the number of layers, via density, and component placement, can affect the achievable pattern class.
-
Cost considerations: Higher pattern classes typically require more advanced manufacturing processes and tighter tolerances, which can increase the overall cost of the PCB.
What is PCB Drill Class?
PCB Drill Class refers to the precision and accuracy of the drilled holes on a PCB. These holes serve various purposes, such as mounting through-hole components, providing electrical connections between layers (vias), and allowing for mechanical fastening. The drill class determines the minimum hole size, positional accuracy, and hole quality that can be achieved on a PCB.
IPC Standards for Drill Class
The IPC standards, particularly IPC-6011, IPC-6012, and IPC-6013, also define the requirements for PCB Drill Class. These standards classify drilled holes into three main categories:
Drill Class | Description |
---|---|
Class 1 | Drilled holes with standard tolerances, suitable for general electronic products |
Class 2 | Drilled holes with tighter tolerances, suitable for dedicated service electronic products |
Class 3 | Drilled holes with the tightest tolerances, suitable for high-reliability electronic products |
Each drill class has specific requirements for hole size, positional accuracy, and hole quality, as outlined in the IPC standards.
Factors Affecting Drill Class
Several factors influence the achievable drill class of a PCB:
-
Drilling technology: The capabilities of the drilling equipment, such as the spindle speed, feed rate, and drill bit quality, determine the precision and accuracy of the drilled holes.
-
Material properties: The choice of substrate material, copper thickness, and the presence of reinforcing materials can impact the drilling process and the resulting hole quality.
-
Hole density: The number and proximity of drilled holes can affect the achievable drill class, as closely spaced holes may require more precise positioning and smaller diameters.
-
Aspect ratio: The ratio of the hole depth to its diameter, known as the aspect ratio, can influence the drilling process and the achievable drill class. Higher aspect ratios typically require more advanced drilling techniques.
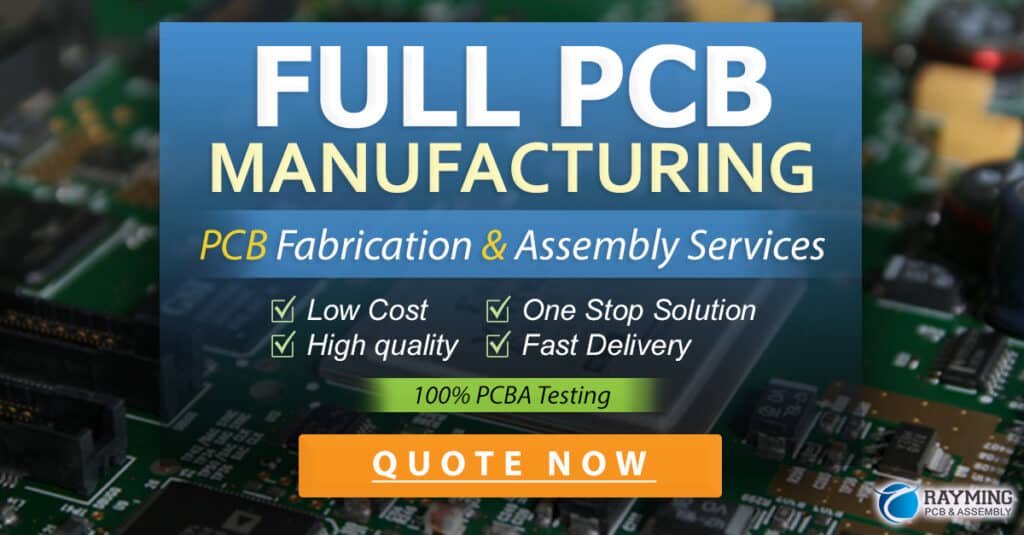
Importance of Selecting the Appropriate Pattern and Drill Class
Choosing the appropriate pattern and drill class for a PCB is crucial for ensuring the board’s functionality, reliability, and cost-effectiveness. Here are some key reasons why selecting the right classes matters:
-
Functionality: The pattern and drill classes directly impact the PCB’s ability to accommodate the required components, routing, and interconnections. Selecting a class that is too low may result in suboptimal performance or even failure.
-
Reliability: Higher pattern and drill classes offer increased precision and tighter tolerances, which can enhance the reliability of the PCB. This is particularly important for applications that demand extended life and continued performance.
-
Cost optimization: Overspecifying the pattern or drill class can lead to unnecessary manufacturing costs. By selecting the appropriate class based on the application requirements, you can optimize the cost of the PCB without compromising functionality or reliability.
-
Manufacturing feasibility: The chosen pattern and drill classes must be compatible with the available manufacturing technologies and processes. Selecting a class that is too high may result in manufacturing challenges or even impossibility.
How to Determine the Appropriate Pattern and Drill Class
To determine the appropriate pattern and drill class for your PCB, follow these steps:
-
Understand the application requirements: Consider the intended use, operating environment, and expected lifetime of the PCB. Determine the level of functionality, reliability, and performance required for the application.
-
Review the PCB layout: Analyze the PCB layout, including the component placement, routing, and via density. Identify the minimum feature sizes, spacing, and hole sizes required to accommodate the design.
-
Consult IPC standards: Refer to the relevant IPC standards (IPC-6011, IPC-6012, and IPC-6013) to understand the requirements for each pattern and drill class. Compare your PCB layout and application requirements with the standard specifications.
-
Consider manufacturing capabilities: Discuss your requirements with the PCB manufacturer to ensure they can accommodate the desired pattern and drill classes. Consider their manufacturing technologies, material options, and cost implications.
-
Balance cost and performance: Evaluate the trade-offs between cost and performance when selecting the pattern and drill classes. Aim to choose the classes that meet your application requirements while optimizing the overall cost of the PCB.
FAQ
-
Q: What happens if I choose a pattern or drill class that is too low for my application?
A: Choosing a pattern or drill class that is too low can result in suboptimal performance, reduced reliability, or even failure of the PCB. It may not accommodate the required components, routing, or interconnections, compromising the board’s functionality. -
Q: Can I always choose the highest pattern and drill classes for my PCBs?
A: While selecting the highest pattern and drill classes may ensure the best performance and reliability, it may not always be necessary or cost-effective. Overspecifying the classes can lead to increased manufacturing costs without providing any significant benefits for the intended application. -
Q: How do I know if my PCB manufacturer can accommodate the desired pattern and drill classes?
A: Discuss your requirements with the PCB manufacturer and provide them with your PCB layout and application details. They will assess their manufacturing capabilities and advise you on the feasibility of achieving the desired pattern and drill classes. -
Q: Are there any additional costs associated with higher pattern and drill classes?
A: Yes, higher pattern and drill classes typically require more advanced manufacturing processes, tighter tolerances, and specialized equipment. This can result in increased manufacturing costs compared to lower classes. However, the cost impact should be weighed against the performance and reliability requirements of the application. -
Q: Can I mix different pattern and drill classes within the same PCB?
A: In some cases, it may be possible to mix different pattern and drill classes within the same PCB, depending on the specific requirements of different regions or components on the board. However, this should be discussed with the PCB manufacturer to ensure feasibility and to understand any potential impact on the manufacturing process and cost.
Conclusion
PCB classification based on Pattern Class and Drill Class is a critical aspect of ensuring the proper functionality, reliability, and cost-effectiveness of printed circuit boards. By understanding the definitions, standards, and factors influencing these classifications, designers, manufacturers, and end-users can make informed decisions when selecting the appropriate classes for their specific applications.
Consulting the relevant IPC standards, analyzing the PCB layout, and considering the manufacturing capabilities are essential steps in determining the suitable pattern and drill classes. Balancing cost and performance is also crucial to optimize the overall value of the PCB.
By carefully evaluating the requirements and choosing the appropriate PCB Pattern Class and Drill Class, you can ensure that your PCBs meet the demands of your application while maintaining a cost-effective solution. This knowledge empowers you to design, manufacture, and utilize PCBs that are fit for purpose and deliver the desired performance and reliability.
Leave a Reply