Introduction to PCB Classification
Printed Circuit Boards (PCBs) are classified into different categories based on various factors such as the density of the circuitry, the minimum Track Width and spacing, the number of layers, and the size of holes drilled. Two important classifications used in the PCB industry are Pattern Class and Drill Class. These classifications provide guidelines for PCB designers and manufacturers to ensure the manufacturability, reliability, and functionality of the boards.
In this article, we will delve into the details of Pattern Class and Drill Class, understanding their definitions, categories, and the factors that determine the classification of a PCB. We will also explore the importance of adhering to these classifications and the benefits they offer in terms of quality, cost, and time-to-market.
What is Pattern Class?
Pattern Class, also known as Feature Class or Track Class, is a classification system that defines the minimum track width and spacing allowed on a PCB. It is a measure of the density of the circuitry on the board. The pattern class is determined by the smallest track width and spacing used in the design.
The pattern class is crucial because it directly affects the manufacturing process, the cost, and the reliability of the PCB. A higher pattern class indicates a denser board with finer tracks and spaces, which requires more advanced manufacturing capabilities and stricter tolerances. On the other hand, a lower pattern class allows for wider tracks and spaces, making the board easier and cheaper to manufacture.
Pattern Class Categories
The IPC (Association Connecting Electronics Industries) has defined standard pattern classes in the IPC-2221 generic standard on printed board design. The standard specifies three primary pattern classes:
Pattern Class | Minimum Track Width | Minimum Spacing |
---|---|---|
Class 1 | 0.20 mm (8 mil) | 0.20 mm (8 mil) |
Class 2 | 0.15 mm (6 mil) | 0.15 mm (6 mil) |
Class 3 | 0.10 mm (4 mil) | 0.10 mm (4 mil) |
-
Class 1: This is the lowest pattern class and is suitable for general-purpose electronics with larger components and lower circuit density. Class 1 boards have a minimum track width and spacing of 0.20 mm (8 mil).
-
Class 2: Class 2 is the most common pattern class used in the industry. It offers a good balance between manufacturability and circuit density. Class 2 boards have a minimum track width and spacing of 0.15 mm (6 mil).
-
Class 3: This is the highest pattern class and is used for high-density designs with fine-pitch components and complex circuitry. Class 3 boards have a minimum track width and spacing of 0.10 mm (4 mil) and require advanced manufacturing capabilities.
It is essential to choose the appropriate pattern class based on the requirements of the design, the components used, and the intended application of the PCB. Overspecifying the pattern class can lead to unnecessary manufacturing costs, while underspecifying it can result in reduced reliability and functionality.
What is Drill Class?
Drill Class is a classification system that defines the smallest hole diameter allowed on a PCB. It is a measure of the precision and accuracy required in the drilling process. The drill class is determined by the smallest hole size used in the design.
Drilling is a critical process in PCB manufacturing, as it creates the holes for through-hole components, vias, and mounting. The drill class affects the manufacturability, cost, and reliability of the PCB. A higher drill class indicates smaller hole sizes, which require more precise and expensive drilling equipment and stricter tolerances. On the other hand, a lower drill class allows for larger hole sizes, making the drilling process easier and cheaper.
Drill Class Categories
The IPC has defined standard drill classes in the IPC-2222 sectional standard on rigid organic printed boards. The standard specifies three primary drill classes:
Drill Class | Minimum Hole Diameter |
---|---|
Class 1 | 0.80 mm (31 mil) |
Class 2 | 0.50 mm (20 mil) |
Class 3 | 0.20 mm (8 mil) |
-
Class 1: This is the lowest drill class and is suitable for general-purpose electronics with larger through-hole components and less dense circuitry. Class 1 boards have a minimum hole diameter of 0.80 mm (31 mil).
-
Class 2: Class 2 is the most common drill class used in the industry. It offers a good balance between manufacturability and hole density. Class 2 boards have a minimum hole diameter of 0.50 mm (20 mil).
-
Class 3: This is the highest drill class and is used for high-density designs with small through-hole components, fine-pitch vias, and complex circuitry. Class 3 boards have a minimum hole diameter of 0.20 mm (8 mil) and require advanced drilling capabilities.
Like pattern class, it is crucial to choose the appropriate drill class based on the requirements of the design, the components used, and the intended application of the PCB. Overspecifying the drill class can lead to unnecessary manufacturing costs, while underspecifying it can result in reduced reliability and functionality.
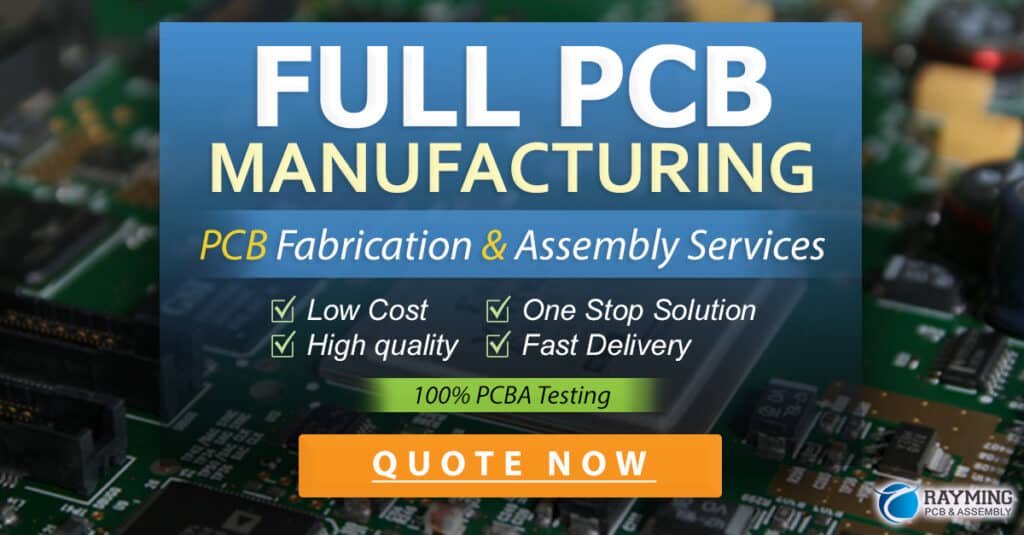
Importance of PCB Classification
Adhering to PCB classification standards, such as Pattern Class and Drill Class, offers several benefits for PCB designers, manufacturers, and end-users:
-
Manufacturability: By following the guidelines for pattern class and drill class, designers can ensure that their boards are manufacturable using standard processes and equipment. This reduces the risk of manufacturing issues, delays, and defects.
-
Reliability: PCBs that adhere to the appropriate pattern class and drill class are more reliable and have a lower risk of failures due to manufacturing defects or environmental stresses. This is because the classification standards take into account factors such as copper thickness, hole wall quality, and thermal management.
-
Cost Optimization: Choosing the right pattern class and drill class helps optimize the manufacturing cost of the PCB. Overspecifying the classes can lead to unnecessary expenses, while underspecifying them can result in defects and rework, which also increases costs.
-
Time-to-Market: By designing PCBs that conform to standard pattern and drill classes, designers can reduce the time required for prototyping, testing, and production. This is because the manufacturing processes for standard classes are well-established and optimized for efficiency.
-
Communication: PCB classification provides a common language for communication between designers, manufacturers, and other stakeholders. It helps ensure that everyone involved in the project has a clear understanding of the requirements and expectations for the board.
Factors Affecting PCB Classification
Several factors influence the choice of pattern class and drill class for a PCB:
-
Component Density: The number and types of components used on the board affect the required pattern class. Higher-density designs with smaller components require a higher pattern class to accommodate the finer tracks and spaces.
-
Circuit Complexity: The complexity of the circuitry, including the number of layers, the routing topology, and the signal integrity requirements, influences the choice of pattern class. More complex boards may require a higher pattern class to ensure adequate space for routing and to minimize crosstalk and signal integrity issues.
-
Hole Density: The number and sizes of holes required for through-hole components, vias, and mounting determine the appropriate drill class. Higher hole density and smaller hole sizes necessitate a higher drill class.
-
Board Size: The overall size of the PCB can affect the choice of pattern class and drill class. Larger boards may allow for a lower pattern class and drill class, as they have more space for routing and larger holes. Smaller boards, on the other hand, may require higher classes to accommodate the required components and circuitry within the limited space.
-
Manufacturing Capabilities: The available manufacturing capabilities and equipment of the PCB fabricator influence the choice of pattern class and drill class. Some manufacturers may have more advanced capabilities that allow for higher classes, while others may be limited to lower classes.
-
Cost Constraints: The budget allocated for the PCB project can affect the choice of pattern class and drill class. Higher classes generally involve more advanced manufacturing processes and tighter tolerances, which can increase the cost of the board. Designers must balance the cost constraints with the technical requirements of the design.
-
Application Requirements: The intended application and operating environment of the PCB influence the choice of pattern class and drill class. Boards used in harsh environments, such as high temperatures or vibrations, may require higher classes to ensure reliability and durability. Safety-critical applications may also demand higher classes to minimize the risk of failures.
FAQ
1. What happens if I choose a higher pattern class or drill class than necessary for my PCB?
Choosing a higher pattern class or drill class than required can lead to unnecessary manufacturing costs. Higher classes involve more advanced processes, tighter tolerances, and specialized equipment, which can increase the overall cost of the PCB. It is important to select the appropriate class based on the actual requirements of the design to optimize cost and manufacturability.
2. Can I mix different pattern classes or drill classes on the same PCB?
Yes, it is possible to use different pattern classes or drill classes on different layers or regions of the same PCB. This is called a hybrid design. For example, you can use a higher pattern class for the dense circuitry on the outer layers and a lower pattern class for the inner layers with less dense routing. Similarly, you can use different drill classes for different hole sizes on the same board. However, it is essential to clearly communicate the hybrid design requirements to the manufacturer to ensure proper fabrication.
3. How do I determine the appropriate pattern class and drill class for my PCB design?
To determine the appropriate pattern class and drill class, you need to consider factors such as the component density, circuit complexity, hole density, board size, manufacturing capabilities, cost constraints, and application requirements. Start by analyzing the smallest track width, spacing, and hole size required in your design. Then, refer to the IPC standards (IPC-2221 for pattern class and IPC-2222 for drill class) to select the corresponding class that meets or exceeds your requirements. It is also advisable to consult with your PCB manufacturer to ensure that they can accommodate the chosen classes.
4. Are there any additional costs associated with higher pattern classes or drill classes?
Yes, higher pattern classes and drill classes typically involve additional costs due to the need for more advanced manufacturing processes, tighter tolerances, and specialized equipment. For example, Class 3 boards with very fine tracks and spaces may require higher-resolution imaging, more precise etching, and stricter quality control, which can increase the manufacturing cost compared to Class 2 boards. Similarly, Class 3 drill sizes may require more expensive and precise drilling machines, leading to higher drilling costs. It is important to consider these additional costs when selecting the appropriate class for your PCB design.
5. Can I change the pattern class or drill class after the design is completed?
Changing the pattern class or drill class after the design is completed can be challenging and may require significant modifications to the PCB layout. Increasing the class may necessitate reducing track widths, spacings, or hole sizes, which can affect the routing and component placement. Decreasing the class, on the other hand, may result in over-designed boards with unnecessary costs. Therefore, it is crucial to determine the appropriate pattern class and drill class early in the design process and ensure that the layout adheres to the chosen class guidelines. If changes are necessary, it is best to consult with the PCB manufacturer to assess the feasibility and impact of the modifications.
Conclusion
PCB classification, particularly Pattern Class and Drill Class, plays a vital role in ensuring the manufacturability, reliability, and functionality of printed circuit boards. By understanding and adhering to these classification standards, PCB designers can create boards that are optimized for cost, quality, and time-to-market.
Choosing the appropriate pattern class and drill class involves considering various factors, such as component density, circuit complexity, hole density, board size, manufacturing capabilities, cost constraints, and application requirements. Designers must strike a balance between the technical requirements of the design and the practical constraints of manufacturing.
By following the guidelines for pattern class and drill class, designers can communicate effectively with manufacturers, reduce the risk of manufacturing issues and defects, and ensure that their PCBs meet the desired performance and reliability standards. This, in turn, helps streamline the PCB development process, minimize costly rework, and deliver high-quality products to end-users.
As PCB technology continues to evolve, with increasing miniaturization and complexity, the importance of PCB classification will only grow. Staying up-to-date with the latest standards and best practices in PCB design and manufacturing will be crucial for success in the ever-changing landscape of electronics.
Leave a Reply