Introduction to PCB Assembly and the Importance of BOM and CPL
Printed Circuit Board (PCB) assembly is a crucial process in the manufacturing of electronic devices. It involves the placement and soldering of electronic components onto a PCB according to a specific design. The success of the PCB assembly process heavily relies on the accuracy and completeness of two essential documents: the Bill of Materials (BOM) and the Component Placement List (CPL).
What is a Bill of Materials (BOM)?
A Bill of Materials, or BOM, is a comprehensive list of all the components required to assemble a PCB. It includes details such as the part number, description, quantity, and manufacturer for each component. The BOM serves as a guide for the procurement team to ensure that all necessary components are available before the assembly process begins.
What is a Component Placement List (CPL)?
A Component Placement List, or CPL, is a document that provides the exact location and orientation of each component on the PCB. It is used by the assembly team to accurately place components during the PCB assembly process. The CPL typically includes information such as the component reference designator, X and Y coordinates, and the rotation angle.
The Role of BOM and CPL in PCB Assembly
The BOM and CPL play critical roles in the PCB assembly process. Let’s explore their significance in more detail.
Ensuring Accurate Component Procurement
The BOM is the foundation for component procurement. It provides a clear and concise list of all the components needed for the PCB assembly. By referring to the BOM, the procurement team can ensure that the correct components are ordered in the right quantities. This helps to avoid delays caused by missing or incorrect components.
Facilitating Efficient PCB Assembly
The CPL is essential for the efficient and accurate placement of components on the PCB. It provides the assembly team with precise instructions on where each component should be placed and how it should be oriented. This information is crucial for automated assembly processes, where pick-and-place machines rely on the CPL data to accurately position components on the PCB.
Reducing Assembly Errors and Rework
Accurate BOM and CPL data help to minimize assembly errors and the need for rework. When the procurement team has the correct BOM, they can order the right components, reducing the risk of assembly issues caused by incorrect or incompatible parts. Similarly, a well-prepared CPL ensures that components are placed correctly on the PCB, minimizing the chances of misalignment or incorrect orientation.
Best Practices for Creating BOM and CPL
To ensure the success of the PCB assembly process, it is important to follow best practices when creating the BOM and CPL. Here are some key considerations:
Accuracy and Completeness
The BOM and CPL must be accurate and complete. Every component required for the PCB assembly should be listed in the BOM, with the correct part number, description, and quantity. The CPL should include the precise location and orientation of each component, leaving no room for ambiguity.
Consistency and Clarity
Consistency and clarity are essential when creating the BOM and CPL. Use a standardized format and naming convention for components to avoid confusion. Provide clear instructions and use appropriate units of measurement (e.g., metric or imperial) to ensure that the assembly team can easily interpret the information.
Revision Control
PCB designs often undergo revisions during the development process. It is crucial to maintain revision control for both the BOM and CPL. Clearly label each revision and keep track of the changes made. This helps to ensure that the assembly team is always working with the most up-to-date information.
Collaboration and Communication
Creating accurate BOM and CPL requires collaboration and communication between different teams, such as design, procurement, and assembly. Establish clear communication channels and involve all relevant stakeholders in the process. Regularly review and validate the BOM and CPL to catch any errors or discrepancies early in the process.
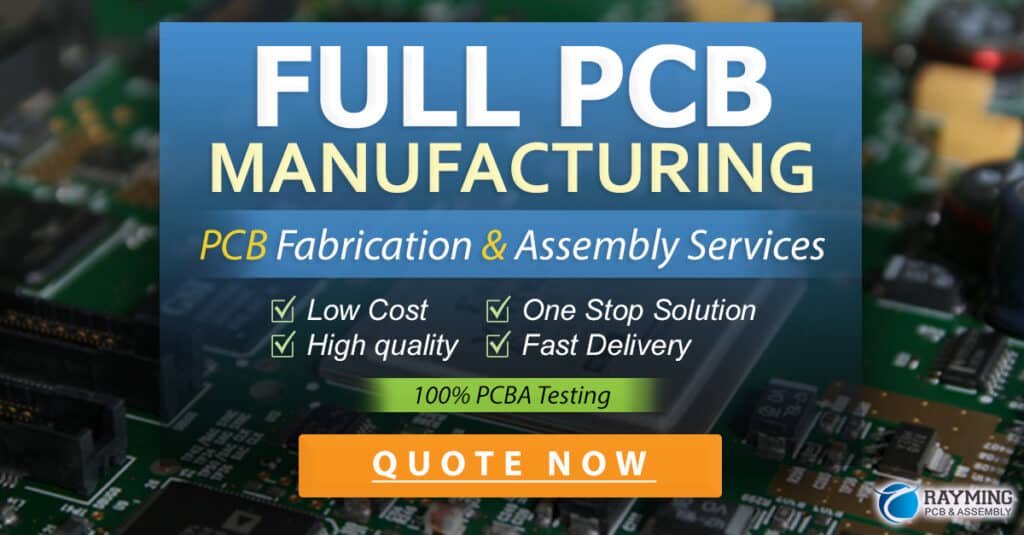
Common Challenges and Solutions
Despite the importance of BOM and CPL, there are some common challenges that can arise during the PCB assembly process. Let’s discuss a few of these challenges and potential solutions.
Incomplete or Inaccurate BOM
Challenge: An incomplete or inaccurate BOM can lead to missing or incorrect components being ordered, causing delays in the assembly process.
Solution: Implement a thorough review process for the BOM. Have multiple team members, including designers and procurement specialists, cross-check the BOM against the schematic and PCB layout to ensure completeness and accuracy.
Inconsistent Component Naming
Challenge: Inconsistent component naming can cause confusion and lead to ordering the wrong components.
Solution: Establish a standardized naming convention for components and ensure that it is followed consistently throughout the BOM and CPL. Use unique identifiers, such as manufacturer part numbers, to avoid ambiguity.
Incorrect CPL Data
Challenge: Incorrect CPL data, such as wrong component locations or orientations, can result in assembly errors and require rework.
Solution: Implement a robust verification process for the CPL. Use automated tools to compare the CPL data against the PCB layout and conduct visual inspections to catch any discrepancies. Perform a trial assembly run to validate the CPL before mass production.
The Impact of BOM and CPL on PCB Assembly Quality and Efficiency
The quality and efficiency of the PCB assembly process are directly influenced by the accuracy and completeness of the BOM and CPL. Let’s explore the impact of these documents on various aspects of PCB assembly.
Component Availability and Lead Times
An accurate BOM ensures that the procurement team can order the correct components in a timely manner. This helps to avoid delays caused by long lead times or component shortages. By having a clear understanding of the required components and their availability, the procurement team can plan accordingly and minimize the risk of production delays.
Assembly Throughput and Cycle Time
A well-prepared CPL enables efficient component placement during the PCB assembly process. By providing precise location and orientation information, the CPL allows automated assembly equipment to operate at optimal speeds and accuracy. This results in higher assembly throughput and reduced cycle times, ultimately improving overall production efficiency.
First-Pass Yield and Rework Reduction
Accurate BOM and CPL data contribute to a higher first-pass yield in PCB assembly. When the correct components are used and placed accurately on the PCB, the chances of assembly errors and defects are minimized. This reduces the need for rework and troubleshooting, saving time and resources in the production process.
Cost Optimization
Proper BOM and CPL management can lead to cost optimization in PCB assembly. By ensuring that the correct components are ordered in the right quantities, the procurement team can avoid overstocking or running out of components. This helps to minimize inventory costs and reduce the risk of obsolete components. Additionally, accurate CPL data reduces the need for manual intervention and rework, further optimizing production costs.
Best Practices for Managing BOM and CPL in the PCB Assembly Process
To effectively manage BOM and CPL in the PCB assembly process, consider the following best practices:
-
Establish a robust data management system: Implement a centralized system to store and manage BOM and CPL data. This system should allow for version control, access control, and data integrity checks to ensure the accuracy and consistency of the information.
-
Conduct regular audits and reviews: Perform periodic audits and reviews of the BOM and CPL to identify any discrepancies or areas for improvement. Involve cross-functional teams in these reviews to gather insights from different perspectives and ensure a comprehensive evaluation.
-
Implement automated data validation: Utilize software tools and scripts to automatically validate the BOM and CPL data against the PCB design files. This helps to catch errors and inconsistencies early in the process, reducing the risk of assembly issues downstream.
-
Foster collaboration and communication: Encourage open communication and collaboration among the design, procurement, and assembly teams. Regularly share updates and feedback to ensure that everyone is working with the most up-to-date information and to address any concerns or challenges promptly.
-
Continuously monitor and improve: Treat BOM and CPL management as an ongoing process rather than a one-time task. Continuously monitor the assembly process, gather feedback from the production team, and identify opportunities for improvement. Regularly update and refine the BOM and CPL based on lessons learned and best practices.
Frequently Asked Questions (FAQ)
-
What is the difference between a BOM and a CPL?
A BOM (Bill of Materials) is a comprehensive list of all the components required to assemble a PCB, including part numbers, descriptions, quantities, and manufacturers. A CPL (Component Placement List) provides the exact location and orientation of each component on the PCB, used by the assembly team for accurate placement. -
Why is it important to have accurate BOM and CPL data?
Accurate BOM and CPL data are essential for the success of the PCB assembly process. They ensure that the correct components are procured and placed accurately on the PCB, minimizing assembly errors, reducing rework, and optimizing production efficiency. -
What are some common challenges in managing BOM and CPL?
Common challenges in managing BOM and CPL include incomplete or inaccurate BOMs, inconsistent component naming, and incorrect CPL data. These challenges can lead to delays, assembly errors, and increased production costs. -
How can I ensure the accuracy and completeness of my BOM and CPL?
To ensure the accuracy and completeness of your BOM and CPL, follow best practices such as conducting thorough reviews, implementing automated data validation, establishing standardized naming conventions, and fostering collaboration and communication among teams. -
What are the benefits of effective BOM and CPL management in PCB assembly?
Effective BOM and CPL management in PCB assembly offers several benefits, including improved component availability, reduced lead times, higher assembly throughput, increased first-pass yield, reduced rework, and cost optimization.
Conclusion
In conclusion, accurate and complete BOM and CPL data are crucial for the success of the PCB assembly process. These documents ensure that the correct components are procured and placed accurately on the PCB, minimizing errors, reducing rework, and optimizing production efficiency. By following best practices in creating and managing BOM and CPL, such as ensuring accuracy and completeness, maintaining revision control, and fostering collaboration, companies can streamline their PCB assembly process and achieve high-quality results.
Effective BOM and CPL management not only improves the quality and efficiency of PCB assembly but also contributes to cost optimization and faster time-to-market. By investing in robust data management systems, conducting regular audits and reviews, and continuously monitoring and improving the process, companies can unlock the full potential of their PCB assembly operations.
As the electronics industry continues to evolve, with increasing complexity and shorter product life cycles, the importance of accurate and well-managed BOM and CPL data becomes even more critical. By prioritizing BOM and CPL management as an integral part of the PCB assembly process, companies can position themselves for success in today’s competitive market.
Leave a Reply