Introduction to Nickel-Gold surface finish
Nickel-Gold (Ni-Au) surface finish is a popular choice in the electronics industry for its excellent properties, including high corrosion resistance, good solderability, and compatibility with wire bonding processes. This finish is widely used in applications such as printed circuit boards (PCBs), connectors, and semiconductor packaging.
The Nickel-Gold surface finish typically consists of a thin layer of gold (Au) deposited over a layer of nickel (Ni). The nickel layer serves as a barrier to prevent the diffusion of copper (Cu) from the substrate into the gold layer, while the gold layer provides excellent oxidation resistance and enhances the solderability of the surface.
Advantages of Nickel-Gold surface finish
- High corrosion resistance
- Excellent solderability
- Compatibility with wire bonding processes
- Good electrical conductivity
- Attractive appearance
Traditional Nickel-Gold surface finish processes
The traditional Nickel-Gold surface finish processes involve electroless nickel immersion gold (ENIG) and electroless nickel electroless palladium immersion gold (ENEPIG).
Electroless Nickel Immersion Gold (ENIG)
ENIG is a popular choice for PCBs due to its simplicity and cost-effectiveness. The process involves the following steps:
- Cleaning and activation of the copper surface
- Electroless deposition of a nickel layer (typically 3-6 µm thick)
- Immersion deposition of a thin gold layer (0.05-0.2 µm thick)
Advantages of ENIG
- Simple and cost-effective process
- Provides good solderability and corrosion resistance
- Suitable for both leaded and lead-free soldering processes
Disadvantages of ENIG
- Limited shelf life due to the thin gold layer
- Potential for “black pad” formation during soldering
- Not suitable for wire bonding applications
Electroless Nickel Electroless Palladium Immersion Gold (ENEPIG)
ENEPIG is an advanced surface finish that offers improved performance compared to ENIG. The process involves the following steps:
- Cleaning and activation of the copper surface
- Electroless deposition of a nickel layer (typically 3-6 µm thick)
- Electroless deposition of a thin palladium layer (0.05-0.2 µm thick)
- Immersion deposition of a thin gold layer (0.05-0.2 µm thick)
Advantages of ENEPIG
- Excellent solderability and corrosion resistance
- Compatible with wire bonding processes
- Longer shelf life compared to ENIG
- Reduced risk of “black pad” formation
Disadvantages of ENEPIG
- More complex and expensive process compared to ENIG
- Potential for palladium corrosion in harsh environments
New options for Chemical Nickel-Gold surface finish
Recent advancements in chemical Nickel-Gold surface finish processes have led to the development of new options that offer improved performance and cost-effectiveness.
Electroless Nickel Electroless Gold (ENEG)
ENEG is a new surface finish that eliminates the need for immersion gold deposition, resulting in a more uniform and stable gold layer. The process involves the following steps:
- Cleaning and activation of the copper surface
- Electroless deposition of a nickel layer (typically 3-6 µm thick)
- Electroless deposition of a gold layer (0.05-0.2 µm thick)
Advantages of ENEG
- Uniform and stable gold layer
- Excellent solderability and corrosion resistance
- Compatible with wire bonding processes
- Longer shelf life compared to ENIG
- Reduced risk of “black pad” formation
Disadvantages of ENEG
- More expensive than ENIG due to the electroless gold deposition process
- Requires strict process control to ensure consistent results
Electroless Nickel Immersion Silver Immersion Gold (ENISIG)
ENISIG is another new surface finish that combines the benefits of immersion silver and immersion gold. The process involves the following steps:
- Cleaning and activation of the copper surface
- Electroless deposition of a nickel layer (typically 3-6 µm thick)
- Immersion deposition of a thin silver layer (0.05-0.2 µm thick)
- Immersion deposition of a thin gold layer (0.05-0.2 µm thick)
Advantages of ENISIG
- Excellent solderability and corrosion resistance
- Compatible with wire bonding processes
- Longer shelf life compared to ENIG
- Reduced risk of “black pad” formation
- Cost-effective compared to ENEPIG
Disadvantages of ENISIG
- Potential for silver migration in high-humidity environments
- Requires strict process control to ensure consistent results
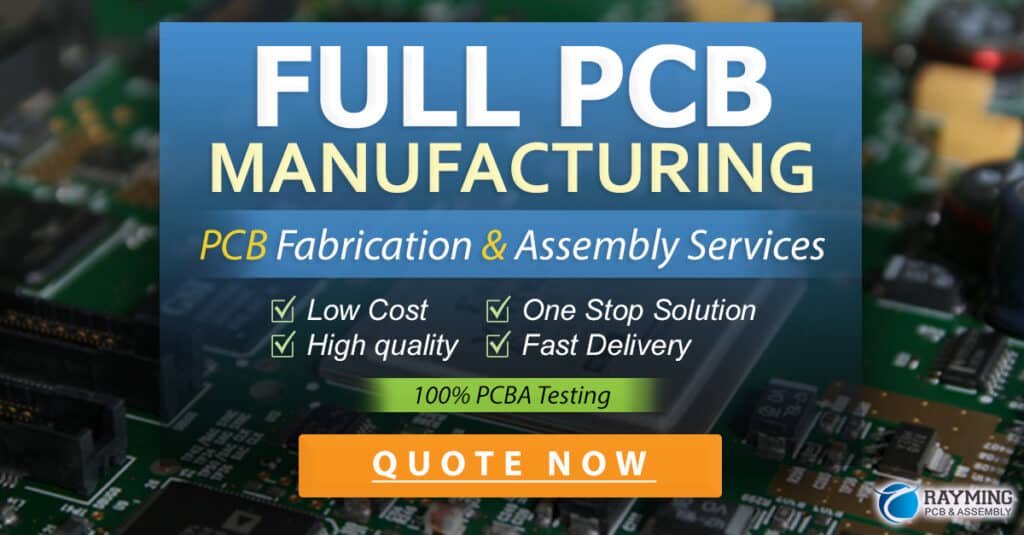
Comparison of Nickel-Gold surface finish options
Surface Finish | Solderability | Corrosion Resistance | Wire Bonding Compatibility | Shelf Life | Cost |
---|---|---|---|---|---|
ENIG | Good | Good | Not suitable | Limited | Low |
ENEPIG | Excellent | Excellent | Compatible | Long | High |
ENEG | Excellent | Excellent | Compatible | Long | Medium |
ENISIG | Excellent | Excellent | Compatible | Long | Medium |
Applications of Nickel-Gold surface finish
Nickel-Gold surface finish is widely used in various applications across the electronics industry, including:
- Printed Circuit Boards (PCBs)
- High-density interconnect (HDI) boards
- Flexible and rigid-flex PCBs
-
Multilayer boards
-
Connectors
- High-reliability connectors for automotive and aerospace applications
- USB and HDMI connectors
-
Board-to-board connectors
-
Semiconductor Packaging
- Ball Grid Array (BGA) packages
- Quad Flat Packages (QFP)
-
Chip Scale Packages (CSP)
-
Radio Frequency (RF) and Microwave Components
- Antennas
- Filters
-
Amplifiers
-
Medical Devices
- Implantable devices
- Diagnostic equipment
- Surgical instruments
Future trends in Nickel-Gold surface finish
As the electronics industry continues to evolve, there is a growing demand for advanced surface finishes that can meet the requirements of emerging technologies and applications. Some of the future trends in Nickel-Gold surface finish include:
-
Thinner gold layers: The trend towards miniaturization and cost reduction is driving the development of surface finishes with thinner gold layers, which can help reduce material costs without compromising performance.
-
Alternative barrier layers: Researchers are exploring the use of alternative barrier layers, such as palladium or ruthenium, to replace or complement the nickel layer in Nickel-Gold surface finishes. These materials may offer improved performance and compatibility with advanced packaging technologies.
-
Environmentally friendly processes: There is a growing emphasis on developing eco-friendly surface finish processes that minimize the use of hazardous chemicals and reduce waste generation. This includes the development of low-temperature and low-pressure deposition processes, as well as the use of biodegradable and non-toxic chemicals.
-
Integration with advanced manufacturing techniques: The integration of Nickel-Gold surface finish processes with advanced manufacturing techniques, such as 3D printing and laser-assisted deposition, can enable the creation of complex geometries and novel device structures with enhanced functionality and performance.
Frequently Asked Questions (FAQs)
- What is the primary function of the nickel layer in a Nickel-Gold surface finish?
-
The nickel layer serves as a barrier to prevent the diffusion of copper from the substrate into the gold layer, which can lead to the formation of intermetallic compounds that degrade solderability and reliability.
-
What are the main differences between ENIG and ENEPIG surface finishes?
-
ENEPIG includes an additional electroless palladium layer between the nickel and gold layers, which provides improved wire bonding compatibility and longer shelf life compared to ENIG. However, ENEPIG is a more complex and expensive process than ENIG.
-
What is the “black pad” problem associated with ENIG surface finish?
-
“Black pad” is a defect that can occur during the soldering process on ENIG-finished surfaces, where the nickel layer becomes oxidized and forms a brittle, black compound that compromises the solder joint integrity. This problem can be mitigated by optimizing the ENIG process parameters and using appropriate soldering techniques.
-
Can Nickel-Gold surface finishes be used for lead-free soldering processes?
-
Yes, Nickel-Gold surface finishes are compatible with both leaded and lead-free soldering processes, making them a versatile choice for a wide range of applications.
-
How does the thickness of the gold layer affect the performance of a Nickel-Gold surface finish?
- The thickness of the gold layer can influence the solderability, wire bonding compatibility, and shelf life of the surface finish. Thicker gold layers generally provide better oxidation resistance and longer shelf life, but they also increase the material cost. The optimal gold thickness depends on the specific application requirements and the chosen Nickel-Gold surface finish process.
Conclusion
Nickel-Gold surface finish is a critical technology for the electronics industry, offering excellent solderability, corrosion resistance, and compatibility with wire bonding processes. As the demand for advanced electronic devices continues to grow, new options for chemical Nickel-Gold surface finish, such as ENEG and ENISIG, are emerging to address the limitations of traditional processes and meet the evolving requirements of the industry.
By understanding the advantages, disadvantages, and applications of different Nickel-Gold surface finish options, engineers and manufacturers can make informed decisions when selecting the most suitable surface finish for their products. As future trends in Nickel-Gold surface finish continue to unfold, it is essential to stay up-to-date with the latest developments and innovations in this field to ensure the reliability, performance, and cost-effectiveness of electronic devices.
Leave a Reply