Understanding pcb prototyping
PCB prototyping is the process of creating a small batch of printed circuit boards for testing and validation purposes. It involves designing the circuit schematic, laying out the PCB, fabricating the board, and assembling the components. Prototyping helps you refine your design, optimize performance, and ensure compatibility between different components.
Benefits of PCB Prototyping
- Verifies the functionality of your circuit design
- Identifies potential issues and allows for design improvements
- Provides a physical representation of your electronic device
- Enables testing and debugging before mass production
- Saves time and money by catching errors early in the development process
Designing the PCB
The first step in creating a PCB prototype is designing the circuit. This involves creating a schematic diagram that represents the electrical connections and components of your device.
Circuit Design Software
To design your PCB, you’ll need to use circuit design software. Some popular options include:
- KiCad
- Eagle
- Altium Designer
- OrCAD
These software tools allow you to create schematic diagrams, layout the PCB, and generate manufacturing files.
Schematic Design
When designing the schematic, consider the following:
- Component selection: Choose the appropriate components for your circuit based on their specifications and ratings.
- Power supply: Determine the power requirements of your circuit and select a suitable power supply.
- Signal integrity: Ensure proper signal routing and avoid interference by considering factors like trace width, spacing, and impedance matching.
- Connectors and interfaces: Select the appropriate connectors and interfaces for your device, such as USB, HDMI, or GPIO pins.
PCB Layout
Once you have completed the schematic design, you can move on to laying out the PCB. The PCB layout involves arranging the components and routing the traces on the board. Consider the following factors:
- Component placement: Place components in a logical and efficient manner, considering factors like signal flow, heat dissipation, and mechanical constraints.
- Trace routing: Route the traces between components, ensuring proper spacing and avoiding cross-talk and signal integrity issues.
- Ground plane: Include a ground plane to provide a low-impedance return path for signals and reduce noise.
- Manufacturability: Adhere to the design rules and guidelines provided by your PCB fabrication service to ensure your board can be manufactured successfully.
Fabricating the PCB
Once you have completed the PCB design, you need to fabricate the physical board. There are several options for PCB fabrication:
In-House Fabrication
If you have access to a PCB fabrication facility, you can manufacture the board yourself. This requires specialized equipment and expertise but allows for greater control over the process.
PCB Fabrication Services
Many companies offer PCB fabrication services, allowing you to outsource the manufacturing process. Some popular PCB fabrication services include:
- PCBWay
- JLCPCB
- OSHPark
- Seeed Studio
These services typically require you to provide the manufacturing files (Gerber files) generated by your PCB design software. They will then fabricate the board based on your specifications.
Fabrication Specifications
When ordering your PCB prototype, you’ll need to specify certain parameters, such as:
- Board material: FR-4 is a common choice for PCBs due to its durability and electrical properties.
- Copper weight: The thickness of the copper traces on the board, typically measured in ounces per square foot (oz/ft²).
- Solder mask color: The protective coating applied to the PCB to prevent accidental short circuits.
- Silkscreen: The text and symbols printed on the PCB for component identification and assembly instructions.
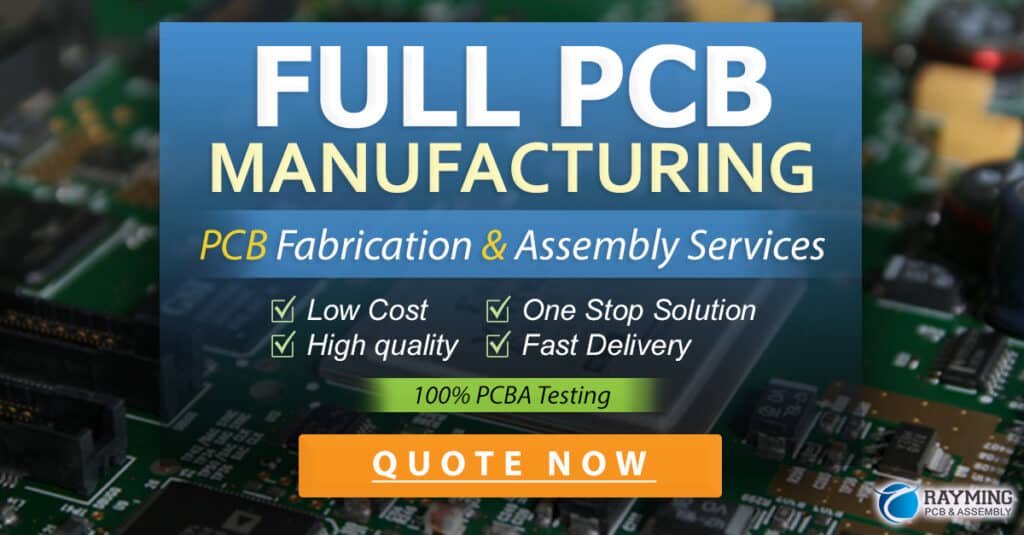
Assembling the PCB Prototype
Once you have received the fabricated PCB, you can proceed with assembling the components onto the board.
Soldering Techniques
There are two main soldering techniques used for PCB assembly:
- Through-hole soldering: Components with long leads are inserted through holes in the PCB and soldered on the opposite side.
- Surface-mount soldering: Components are mounted directly onto the surface of the PCB and soldered in place.
Choose the appropriate soldering technique based on the components used in your design.
Soldering Tools
To assemble your PCB prototype, you’ll need the following tools:
- Soldering iron: A tool that heats up to melt the solder and join components to the PCB.
- Solder: A metal alloy that melts to create electrical and mechanical connections between components and the PCB.
- Solder wick: A braided wire used to remove excess solder from the board.
- Flux: A chemical agent that helps the solder flow and adhere to the components and PCB pads.
- Tweezers: Used for handling small components during assembly.
Component Placement and Soldering
Follow these steps to assemble your PCB prototype:
- Place the components on the PCB according to the assembly instructions and silkscreen markings.
- Secure the components in place using tape or solder paste if necessary.
- Heat up the soldering iron and apply a small amount of solder to the tip to improve heat transfer.
- Touch the soldering iron to the component lead and PCB pad simultaneously, allowing the solder to melt and flow around the connection.
- Remove the soldering iron and let the solder cool and solidify.
- Repeat the process for all components on the board.
Inspection and Testing
After assembling the PCB prototype, it’s crucial to inspect the board for any soldering defects or errors. Use a magnifying glass or microscope to check for the following:
- Cold solder joints: Dull and grainy solder connections that may cause intermittent or poor electrical contact.
- Solder bridges: Unintended connections between adjacent pads or traces caused by excess solder.
- Misaligned or missing components: Ensure all components are placed correctly and securely soldered.
Once the visual inspection is complete, power up the board and perform functional testing to verify that the circuit operates as intended. Use test equipment like multimeters and oscilloscopes to measure voltages, currents, and signal waveforms.
Troubleshooting and Debugging
If your PCB prototype doesn’t function as expected, you may need to troubleshoot and debug the circuit. Here are some steps to follow:
- Recheck the schematic: Verify that the schematic design is correct and matches the physical assembly of the PCB.
- Check for short circuits: Use a multimeter to check for short circuits between power rails, ground, and signal traces.
- Verify component values: Double-check that the components used match the specified values in the schematic.
- Probe test points: Use an oscilloscope or multimeter to probe test points on the PCB and compare the readings with expected values.
- Isolate sections of the circuit: If the issue persists, try to isolate specific sections of the circuit by disconnecting or bypassing components to narrow down the problem area.
Once you have identified the issue, make the necessary modifications to the PCB design or replace faulty components. Repeat the fabrication and assembly process to create a revised prototype.
Best Practices for PCB Prototyping
To ensure a successful PCB prototyping process, consider the following best practices:
- Start with a clear and well-defined circuit schematic
- Use a modular design approach to break down complex circuits into smaller, manageable sections
- Follow good PCB layout practices, such as proper grounding, signal routing, and component placement
- Choose reputable pcb fabrication and assembly services with a track record of quality and reliability
- Thoroughly test and validate your PCB prototype before moving to mass production
- Document your design process, including schematic revisions, PCB layouts, and test results, for future reference and improvements
Frequently Asked Questions (FAQ)
-
What is the difference between a PCB prototype and a production PCB?
A PCB prototype is a small batch of boards created for testing and validation purposes, while a production PCB is manufactured in large quantities for use in the final product. Prototypes may have looser tolerances and may not undergo the same rigorous testing as production PCBs. -
How long does it take to create a PCB prototype?
The time required to create a PCB prototype depends on factors like the complexity of the design, the fabrication method used, and the workload of the fabrication service. In general, it can take anywhere from a few days to a few weeks to receive a PCB prototype. -
What is the typical cost of creating a PCB prototype?
The cost of creating a PCB prototype varies based on the size of the board, the number of layers, the components used, and the fabrication and assembly services chosen. Expect to pay anywhere from a few tens of dollars to a few hundred dollars for a simple prototype, with costs increasing for more complex designs. -
Can I create a PCB prototype at home?
Yes, it is possible to create a PCB prototype at home using methods like etching or milling. However, these methods require specialized equipment and chemicals and may not produce results as professional as those from dedicated fabrication services. -
How many prototypes should I create before moving to production?
The number of prototypes needed depends on the complexity of your design and the level of testing and validation required. In general, it’s a good idea to create at least two or three prototypes to verify functionality, test different scenarios, and identify any potential issues before committing to mass production.
Conclusion
Creating a PCB prototype is a critical step in the development of electronic devices. By following the steps outlined in this article, you can design, fabricate, and assemble a functional PCB prototype to test and validate your circuit design. Remember to start with a clear schematic, use good PCB layout practices, and thoroughly test and debug your prototype before moving to production. With the right tools, techniques, and best practices, you can create a successful PCB prototype that brings your electronic design to life.
Step | Description |
---|---|
1 | Design the circuit schematic |
2 | Layout the PCB |
3 | Fabricate the PCB |
4 | Assemble the components |
5 | Inspect and test the prototype |
6 | Troubleshoot and debug if necessary |
7 | Revise and iterate the design |
By following this step-by-step process and adhering to best practices, you can create a reliable and functional PCB prototype that meets your design requirements and paves the way for successful mass production.
Leave a Reply