What is soldering?
Soldering is a process of joining two or more metal parts together by melting and applying a filler metal (solder) into the joint. The solder has a lower melting point than the adjoining metal, allowing it to flow into the joint and create a strong bond when cooled. Soldering is widely used in electronics, plumbing, and metalwork.
Why Solder manually?
While there are automated soldering methods, such as wave soldering and reflow soldering, manual soldering remains an essential skill for various reasons:
-
Repairs and modifications: Manual soldering allows for precise repairs and modifications to existing electronic circuits and components.
-
Prototyping: When creating prototypes or one-off projects, manual soldering is often the most efficient and cost-effective method.
-
Small-scale production: For low-volume production runs, manual soldering can be more practical than setting up automated soldering systems.
-
Flexibility: Manual soldering allows for working with a wide range of component sizes, shapes, and materials that may not be suitable for automated processes.
Tools and materials needed for manual soldering
To begin soldering manually, you will need the following tools and materials:
-
Soldering iron: A tool that heats up to melt the solder. Choose an iron with adjustable temperature control and a suitable wattage for your needs (typically 20-60 watts for electronics work).
-
Soldering tips: Interchangeable tips for the soldering iron, available in various shapes and sizes to suit different applications.
-
Solder: A metal alloy that melts and flows into the joint to create a bond. The most common types are lead-based and lead-free solder, available in different diameters and compositions.
-
Flux: A chemical cleaning agent that helps remove oxides from the metal surfaces and improves solder flow. Flux can be in the form of a paste, pen, or core within the solder wire.
-
Soldering iron stand: A stand to safely hold the hot soldering iron when not in use, often with a sponge or brass wool for cleaning the tip.
-
Sponge or brass wool: Used to clean the soldering iron tip by removing excess solder and oxidation.
-
Wire cutters: To trim component leads and wires before and after soldering.
-
Tweezers or pliers: For handling small components and wires during the soldering process.
-
Safety glasses: To protect your eyes from any solder splashes or fumes.
-
Ventilation: Ensure adequate ventilation in your work area to minimize exposure to soldering fumes.
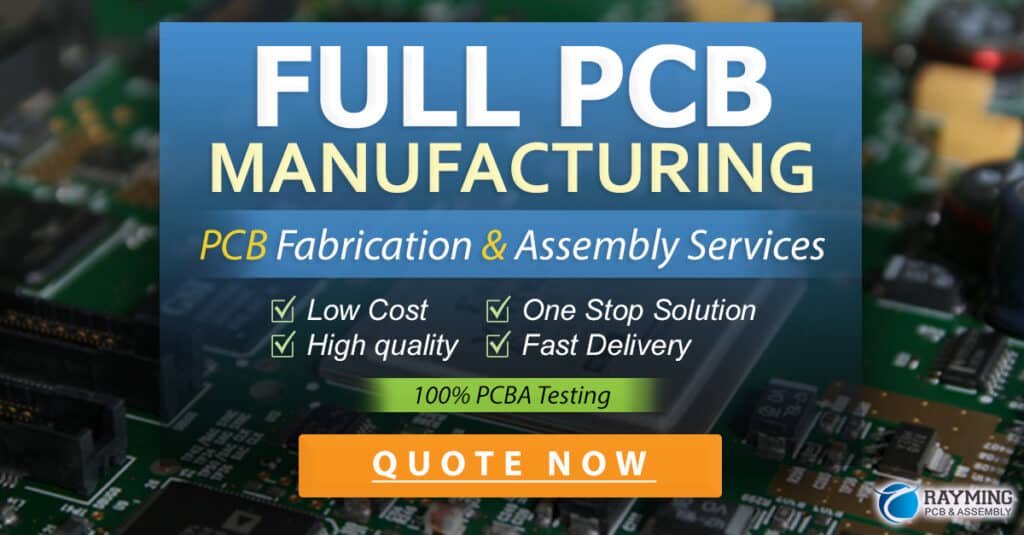
Preparing the soldering iron
Before you start soldering, it’s essential to properly set up and maintain your soldering iron:
-
Set the temperature: Adjust the soldering iron temperature according to the type of solder and the components you’ll be working with. Typical temperatures range from 300°C to 400°C (572°F to 752°F) for electronics work.
-
Tinning the tip: Before first use and periodically during use, “tin” the soldering iron tip by applying a small amount of solder to the clean, hot tip. This process helps protect the tip from oxidation and improves heat transfer.
-
Clean the tip: Regularly wipe the tip on a damp sponge or brass wool to remove excess solder and oxidation. A clean tip ensures better heat transfer and solder flow.
Soldering techniques
Tinning wires and component leads
Before soldering wires or component leads together, it’s often necessary to “tin” them first. Tinning involves applying a small amount of solder to the individual wires or leads before joining them together. This process helps ensure a stronger, more reliable connection.
To tin a wire:
-
Strip the wire insulation using wire strippers, exposing about 3-5mm of bare wire.
-
Clean the soldering iron tip and apply a small amount of solder to the tip to ensure good heat transfer.
-
Hold the wire with tweezers or pliers and touch the soldering iron tip to the exposed wire.
-
Apply solder to the wire, allowing it to melt and flow evenly around the strands. Avoid applying too much solder, as this can make the wire difficult to insert into tight spaces.
-
Remove the soldering iron and allow the solder to cool and solidify.
To tin component leads, follow the same process, applying solder to the lead where it will be connected to other components or wires.
Through-hole soldering
Through-hole soldering involves soldering components with leads that pass through holes in a printed circuit board (PCB). This method is used for larger components and provides a strong mechanical connection.
To solder a through-hole component:
-
Insert the component leads through the appropriate holes in the PCB, ensuring the component is seated properly.
-
Bend the leads slightly outward on the underside of the PCB to hold the component in place.
-
Clean and tin the soldering iron tip.
-
Touch the soldering iron tip to both the component lead and the PCB pad simultaneously.
-
Apply solder to the joint, allowing it to melt and flow around the lead and pad. Use just enough solder to create a concave fillet that looks like a volcano crater.
-
Remove the soldering iron and allow the solder to cool and solidify.
-
Trim the excess leads with wire cutters, leaving about 1-2mm of lead protruding from the solder joint.
Surface-mount soldering
Surface-mount soldering involves soldering components directly onto the surface of a PCB without leads passing through holes. This method is used for smaller, more compact components and allows for higher component density on the PCB.
To solder a surface-mount component:
-
Apply a small amount of solder paste or flux to the PCB pads where the component will be placed.
-
Position the component on the PCB using tweezers, ensuring proper alignment with the pads.
-
Clean and tin the soldering iron tip.
-
Touch the soldering iron tip to the component lead and PCB pad simultaneously.
-
Apply solder to the joint, allowing it to melt and flow around the lead and pad. Use just enough solder to create a small fillet between the lead and pad.
-
Remove the soldering iron and allow the solder to cool and solidify.
-
Repeat the process for the remaining leads.
Common soldering problems and solutions
-
Cold solder joint: A cold solder joint occurs when the solder does not melt completely, resulting in a dull, cracked, or lumpy appearance. This can happen if the soldering iron temperature is too low, the joint is not heated evenly, or the components move during cooling. To fix a cold solder joint, reheat the joint with the soldering iron and apply additional solder if needed.
-
Bridging: Bridging occurs when excess solder accidentally connects adjacent pads or leads, creating a short circuit. To remove a solder bridge, use solder wick (desoldering braid) and a clean soldering iron tip to absorb the excess solder. Alternatively, you can use a solder sucker (desoldering pump) to remove the excess solder.
-
Insufficient wetting: Insufficient wetting happens when the solder does not adhere properly to the components or PCB pads, resulting in a weak or unreliable connection. This can be caused by dirty or oxidized surfaces, insufficient heat, or inadequate flux. To improve wetting, clean the surfaces thoroughly, use fresh solder and flux, and ensure the soldering iron is at the correct temperature.
-
Overheating components: Applying too much heat or holding the soldering iron on a component for too long can damage sensitive parts. To avoid overheating, use the lowest effective temperature, apply heat for only the necessary duration, and use heat sinks or thermal shunts to protect sensitive components.
Safety precautions
-
Work in a well-ventilated area to avoid inhaling soldering fumes, which can be harmful to your health.
-
Wear safety glasses to protect your eyes from solder splashes or fumes.
-
Use a soldering iron with a grounded (3-prong) plug to prevent electric shock.
-
Always place the soldering iron in its stand when not in use to avoid accidentally touching the hot tip or causing a fire.
-
Keep flammable materials away from the soldering area to prevent fires.
-
Wash your hands thoroughly after soldering, especially before eating or drinking, to avoid ingesting any lead or other harmful substances.
Frequently Asked Questions (FAQ)
-
What is the difference between lead-based and lead-free solder?
Lead-based solder contains a mixture of tin and lead, typically in a 60/40 or 63/37 ratio. Lead-free solder, on the other hand, is made from a mixture of tin, copper, and silver. Lead-free solder has a higher melting point and requires slightly different soldering techniques, but is preferable due to the health and environmental concerns associated with lead. -
Can I use the same soldering iron for both lead-based and lead-free solder?
Yes, you can use the same soldering iron for both types of solder. However, it’s essential to use a higher temperature when working with lead-free solder due to its higher melting point. Additionally, be sure to clean the soldering iron tip thoroughly when switching between solder types to avoid contamination. -
How often should I replace my soldering iron tip?
Soldering iron tips can last for a long time with proper care and maintenance. However, if you notice that the tip is not tinning properly, has become deformed, or is not heating evenly, it may be time to replace it. The lifespan of a soldering iron tip depends on factors such as usage frequency, soldering temperature, and the type of solder used. -
What should I do if I accidentally create a solder bridge?
If you accidentally create a solder bridge between two pads or leads, you can remove it using solder wick (desoldering braid) or a solder sucker (desoldering pump). Place the solder wick on the bridge and apply heat with the soldering iron to absorb the excess solder. Alternatively, use the solder sucker to remove the excess solder by heating the bridge and quickly triggering the pump to suck up the molten solder. -
Can I solder without flux?
While it is possible to solder without flux, it is not recommended. Flux helps to remove oxides from the metal surfaces, promotes better solder flow, and results in a stronger, more reliable joint. Without flux, you may encounter issues such as poor wetting, weak joints, or excessive oxidation. If you are using solder wire with a flux core, you may not need to add additional flux. However, for bare wires or component leads, applying a small amount of flux before soldering is advisable.
Conclusion
Manual soldering is an essential skill for anyone working with electronics, whether for repairs, modifications, prototyping, or small-scale production. By understanding the basics of soldering tools, techniques, and safety precautions, you can create strong, reliable solder joints and bring your electronic projects to life.
Remember to always prioritize safety, maintain your soldering equipment, and practice regularly to refine your skills. With patience and persistence, manual soldering can become a valuable addition to your electronics toolkit.
Leave a Reply