What is a PCB?
A printed circuit board (PCB) is a flat board made of insulating material, such as fiberglass or plastic, with conductive copper traces printed on its surface. These traces connect various electronic components, such as resistors, capacitors, and integrated circuits (ICs), to form a complete electronic circuit.
PCBs are used in virtually all electronic devices, from smartphones and laptops to industrial equipment and medical devices. They provide a reliable and efficient way to connect electronic components and enable the miniaturization of electronic devices.
Why DIY PCB?
There are several reasons why you might want to create your own PCBs at home:
-
Cost savings: Commercial PCB fabrication services can be expensive, especially for small quantities or prototypes. By making your own PCBs, you can save money on fabrication costs.
-
Customization: When you create your own PCBs, you have complete control over the design and layout of the board. This allows you to optimize the circuit for your specific needs and requirements.
-
Learning experience: DIY PCB fabrication is a great way to learn about electronics and gain hands-on experience with circuit design and fabrication techniques.
-
Faster turnaround: Commercial PCB fabrication services can take several days or even weeks to deliver your boards. By making your own PCBs, you can have a working prototype in a matter of hours.
Materials and Tools Required
Before you start creating your own PCBs, you’ll need to gather the necessary materials and tools. Here’s a list of the essential items you’ll need:
Material/Tool | Description |
---|---|
Copper clad board | A fiberglass or plastic board with a layer of copper on one or both sides. This will serve as the base for your PCB. |
Etchant solution | A chemical solution used to remove unwanted copper from the board, leaving only the desired traces. Ferric chloride is a common etchant used for DIY PCB fabrication. |
Resist pen or transfer paper | Used to draw or transfer the circuit design onto the copper clad board. A resist pen contains ink that resists the etchant, while transfer paper allows you to print the design and iron it onto the board. |
Drill or drill press | Used to drill holes in the PCB for through-hole components and mounting. |
Soldering iron and solder | Used to solder electronic components to the PCB. |
Safety equipment | Protective gloves, goggles, and a well-ventilated work area are essential for safe PCB fabrication. |
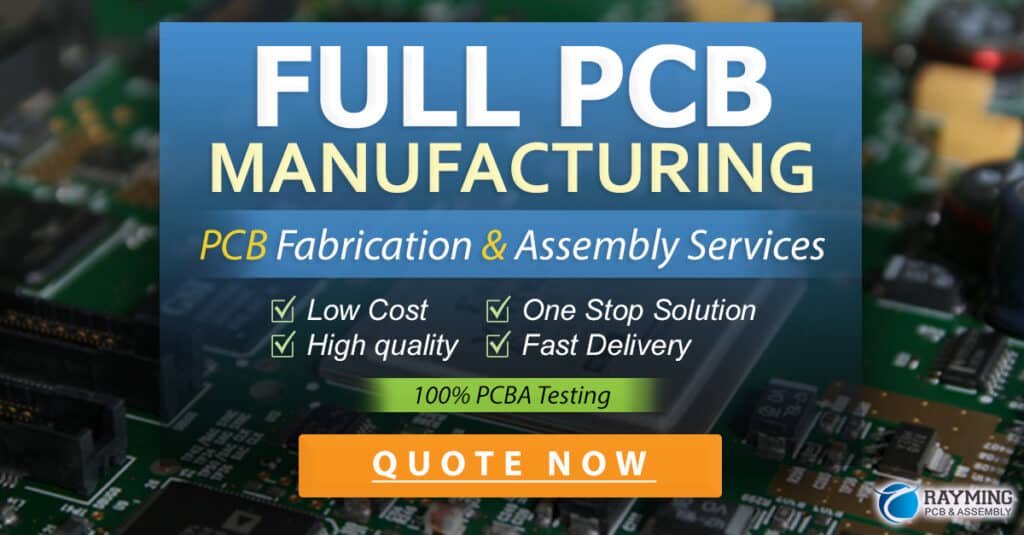
Step-by-Step Guide to DIY PCB Fabrication
Now that you have all the necessary materials and tools, let’s walk through the process of creating your own PCB at home.
Step 1: Design Your Circuit
The first step in DIY PCB fabrication is to design your electronic circuit. You can use various software tools, such as KiCad, Eagle, or EasyEDA, to create a schematic diagram and PCB layout. When designing your circuit, consider the following factors:
- Component selection: Choose components that are suitable for your project requirements and available in through-hole or surface-mount packages.
- Circuit layout: Arrange the components and traces on the PCB in a logical and efficient manner, minimizing the distance between connected components and avoiding overlapping traces.
- Trace width: Ensure that the traces are wide enough to carry the required current without overheating or introducing excessive resistance.
- Ground plane: Consider adding a ground plane to your PCB to reduce electromagnetic interference (EMI) and improve signal integrity.
Once you have completed your circuit design, export the PCB layout as a high-resolution image or PDF file.
Step 2: Transfer the Design to the Copper Clad Board
There are two main methods for transferring your PCB design onto the copper clad board: using a resist pen or using transfer paper.
Using a Resist Pen
- Clean the copper surface of the board with steel wool or fine sandpaper to remove any oxidation or dirt.
- Print the PCB layout onto plain paper and place it under the copper clad board.
- Trace the PCB layout onto the copper surface using a resist pen, ensuring that the lines are thick and continuous.
- Remove the paper and inspect the traced design for any gaps or inconsistencies. Touch up the design with the resist pen if necessary.
Using Transfer Paper
- Clean the copper surface of the board with steel wool or fine sandpaper to remove any oxidation or dirt.
- Print the PCB layout onto the transfer paper using a laser printer. Ensure that the design is printed in reverse (mirrored) so that it transfers correctly onto the copper surface.
- Cut out the printed design, leaving a small margin around the edges.
- Place the transfer paper onto the copper surface, with the printed side facing down.
- Iron the transfer paper onto the copper surface using a hot iron. Apply firm, even pressure for several minutes to ensure that the design is transferred properly.
- Allow the board to cool, then carefully peel off the transfer paper. The PCB layout should now be visible on the copper surface.
Step 3: Etch the PCB
Now that your PCB design is transferred onto the copper clad board, it’s time to etch away the unwanted copper using an etchant solution.
- Prepare the etchant solution according to the manufacturer’s instructions. Ferric chloride is a common etchant used for DIY PCB fabrication.
- Place the copper clad board into a plastic or glass container and pour the etchant solution over it. Ensure that the board is completely submerged.
- Agitate the solution occasionally to help the etching process. The etching time will depend on the strength of the solution and the thickness of the copper layer. Typically, etching takes between 10 to 45 minutes.
- Once the etching is complete, remove the board from the solution and rinse it thoroughly with water.
- Use steel wool or fine sandpaper to remove any remaining resist ink or transfer paper from the board.
Step 4: Drill Holes and Clean the Board
With the etching process complete, you’ll need to drill holes in the PCB for through-hole components and mounting.
- Use a drill or drill press to carefully drill holes at the marked locations on the PCB. Ensure that the drill bit size matches the component lead diameter.
- Clean the PCB with isopropyl alcohol to remove any debris or fingerprints.
Step 5: Solder Components
The final step in DIY PCB fabrication is to solder the electronic components onto the board.
- Place the components onto the PCB, ensuring that they are correctly oriented and seated in their designated locations.
- Use a soldering iron and solder to attach the component leads to the PCB pads. Apply heat to the pad and lead simultaneously, then feed solder into the joint until it flows evenly around the connection.
- Trim any excess component leads with wire cutters.
- Inspect the soldered joints for any bridges, cold joints, or poor connections. Rework any problematic joints as necessary.
Tips and Tricks for Successful DIY PCB Fabrication
Here are some additional tips and tricks to help you achieve the best results when creating your own PCBs at home:
- Use a high-quality printer: When printing your PCB layout onto transfer paper, use a high-quality laser printer to ensure that the design is clear and sharp.
- Maintain consistent resist pen pressure: When tracing your PCB layout with a resist pen, apply consistent pressure to ensure that the lines are thick and continuous. Thin or broken lines may result in incomplete etching.
- Monitor the etching process: Keep an eye on the etching process and remove the board from the solution as soon as the unwanted copper has been removed. Over-etching can lead to damaged or broken traces.
- Use a well-ventilated area: Etchant solutions can produce harmful fumes, so it’s essential to work in a well-ventilated area and wear protective gloves and goggles.
- Practice good soldering techniques: To ensure reliable connections, use a clean, well-tinned soldering iron tip and apply heat to both the pad and the component lead simultaneously. Avoid overheating the components or applying too much solder.
Frequently Asked Questions (FAQ)
-
What is the best software for designing PCBs?
There are several popular software options for designing PCBs, including KiCad, Eagle, and EasyEDA. The best choice depends on your specific needs, experience level, and budget. KiCad is a free, open-source option that offers a comprehensive set of tools for schematic capture and PCB layout. Eagle is a widely-used commercial software with a free version available for small projects. EasyEDA is a web-based platform that allows you to design and share PCBs easily. -
Can I use any type of paper for printing the PCB layout?
When using the toner transfer method, it’s best to use special PCB transfer paper designed for this purpose. Regular paper may not transfer the design effectively, resulting in poor-quality traces or incomplete etching. If you’re using a resist pen, you can print the design onto plain paper and trace it onto the copper clad board. -
How do I choose the right etchant solution?
Ferric chloride is the most common etchant solution used for DIY PCB fabrication. It is relatively safe and easy to use, and it produces good results. Other options include ammonium persulfate and copper chloride. When choosing an etchant solution, consider factors such as etching speed, safety, and disposal requirements. -
What should I do if the etching process takes too long or doesn’t work properly?
If the etching process is taking too long, the etchant solution may be too weak or the copper layer may be too thick. Try using a fresh batch of etchant solution or agitating the solution more frequently. If the etching process doesn’t work properly, ensure that the resist ink or transfer paper has been applied correctly and that there are no gaps or inconsistencies in the PCB layout. -
How can I make my DIY PCBs look more professional?
To give your DIY PCBs a more professional appearance, consider applying a solder mask and silkscreen. A solder mask is a protective layer that covers the copper traces, leaving only the pads exposed for soldering. Silkscreen is a printed layer that adds labels, logos, and other markings to the PCB surface. You can apply solder mask and silkscreen using specialized products and techniques, such as UV-curable solder mask and laser-printed silkscreen transfer paper.
Conclusion
Creating your own PCBs at home can be a fun, rewarding, and cost-effective way to bring your electronic projects to life. By following this step-by-step guide and using the right materials and tools, you can design, etch, and solder high-quality PCBs in your own workshop.
Remember to prioritize safety, use high-quality materials, and practice good design and fabrication techniques. With time and experience, you’ll be able to create increasingly complex and professional-looking PCBs for your projects.
Happy PCB making!
Leave a Reply