Introduction to rf pcb Design
Radio Frequency (RF) PCB design is a specialized area of printed circuit board design that focuses on the layout and construction of boards for high-frequency applications. RF PCB design requires careful consideration of various factors such as signal integrity, impedance matching, electromagnetic interference (EMI), and power dissipation. Designing an RF PCB can be challenging, but with the right knowledge and tools, it is possible to create a high-performance board that meets the specific requirements of your application.
Key Considerations in RF PCB Design
When designing an RF PCB, there are several key considerations to keep in mind:
-
Signal Integrity: Maintaining signal integrity is crucial in RF PCB design. This involves minimizing signal distortion, reflections, and crosstalk. Proper impedance matching, trace routing, and ground plane design are essential for ensuring good signal integrity.
-
Impedance Matching: Impedance matching is the process of ensuring that the impedance of the signal path matches the impedance of the source and load. This is important for minimizing reflections and ensuring maximum power transfer. Impedance matching can be achieved through careful trace width and spacing, as well as the use of impedance-controlled materials.
-
EMI: Electromagnetic interference (EMI) can be a major problem in RF PCB design. EMI can cause signal degradation, false triggering, and other issues. To minimize EMI, it is important to use proper shielding, grounding, and filtering techniques. This may involve the use of ground planes, shielding cans, and EMI filters.
-
Power Dissipation: RF circuits can generate significant amounts of heat, which can lead to performance degradation and reliability issues. Proper power dissipation is essential for ensuring the long-term reliability of the board. This may involve the use of heat sinks, thermal vias, and other cooling techniques.
RF pcb design process
The RF PCB design process typically involves the following steps:
1. Schematic Design
The first step in the RF PCB design process is to create a schematic of the circuit. This involves selecting the appropriate components, defining the interconnections between them, and specifying the required performance parameters. The schematic should be carefully reviewed to ensure that it meets the design requirements and is free of errors.
2. Layout Design
Once the schematic is complete, the next step is to create the layout of the board. This involves placing the components on the board, routing the traces, and defining the layer stackup. The layout should be optimized for signal integrity, impedance matching, and EMI suppression. This may involve the use of specialized layout techniques such as microstrip, stripline, and coplanar waveguide.
3. Simulation and Analysis
Before fabricating the board, it is important to simulate and analyze the design to ensure that it meets the required performance specifications. This may involve the use of specialized RF simulation tools such as Ansys HFSS, Keysight ADS, or Cadence Allegro. These tools can help to identify potential issues such as impedance mismatches, signal reflections, and EMI.
4. Fabrication and Assembly
Once the design has been simulated and verified, the next step is to fabricate and assemble the board. This involves selecting the appropriate PCB materials, specifying the layer stackup, and defining the manufacturing process. The board should be carefully inspected and tested to ensure that it meets the required quality standards.
5. Testing and Validation
The final step in the RF PCB design process is to test and validate the board to ensure that it meets the required performance specifications. This may involve the use of specialized RF test equipment such as network analyzers, spectrum analyzers, and signal generators. The board should be tested under various operating conditions to ensure that it performs reliably and meets the design requirements.
RF PCB Design Guidelines
To ensure the success of your RF PCB design, it is important to follow some key design guidelines:
1. Use Appropriate Materials
The choice of PCB materials can have a significant impact on the performance of an RF circuit. It is important to select materials with the appropriate dielectric constant, loss tangent, and thermal properties. Common RF PCB materials include Rogers, Taconic, and Isola.
2. Minimize Trace Length
Long traces can introduce unwanted inductance and capacitance, which can degrade signal quality and cause reflections. It is important to minimize trace length wherever possible, especially for high-frequency signals.
3. Use Ground Planes
Ground planes are essential for providing a low-impedance return path for high-frequency signals. They can also help to reduce EMI and improve signal integrity. It is important to use a continuous ground plane wherever possible, and to ensure that it is properly connected to the components and traces.
4. Use Proper Shielding
Shielding is essential for minimizing EMI and preventing signal leakage. Shielding can be achieved through the use of ground planes, shielding cans, and other techniques. It is important to ensure that the shielding is properly grounded and covers all sensitive areas of the board.
5. Use Impedance Matching
Impedance matching is essential for ensuring maximum power transfer and minimizing reflections. It is important to use the appropriate trace width and spacing to achieve the desired impedance. Impedance matching can also be achieved through the use of impedance-controlled materials and specialized layout techniques.
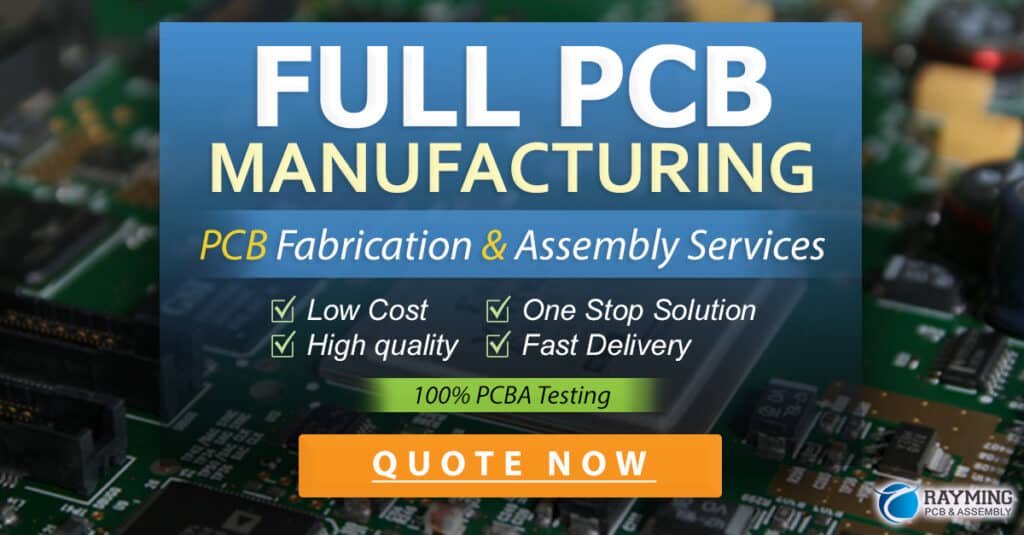
RF PCB Design Tools
There are several specialized tools available for RF PCB design, including:
Tool | Description |
---|---|
Ansys HFSS | A 3D electromagnetic simulation tool for RF and microwave applications |
Keysight ADS | A comprehensive RF and microwave design tool for circuit simulation and layout |
Cadence Allegro | A PCB design tool with specialized features for RF and high-speed design |
Altium Designer | A PCB design tool with integrated 3D modeling and simulation capabilities |
Mentor Graphics HyperLynx | A signal integrity and power integrity analysis tool for PCB design |
These tools can help to streamline the RF PCB design process and ensure that the board meets the required performance specifications.
RF PCB Manufacturing Considerations
When manufacturing an RF PCB, there are several key considerations to keep in mind:
1. Layer Stackup
The layer stackup of an RF PCB can have a significant impact on its performance. It is important to use the appropriate number of layers and materials to achieve the desired impedance and signal integrity. The layer stackup should also be optimized for manufacturability and cost.
2. Via Design
Vias are used to connect traces on different layers of the board. In RF PCB design, it is important to minimize the use of vias wherever possible, as they can introduce unwanted inductance and capacitance. When vias are necessary, it is important to use the appropriate size and spacing to minimize their impact on signal quality.
3. Copper Thickness
The thickness of the copper traces can have a significant impact on the performance of an RF circuit. Thicker traces can help to reduce resistance and improve power handling, but they can also increase the cost and complexity of the board. It is important to select the appropriate copper thickness based on the specific requirements of the application.
4. Surface Finish
The surface finish of an RF PCB can also impact its performance. Common surface finishes for RF PCBs include ENIG (Electroless Nickel Immersion Gold), HASL (Hot Air Solder Leveling), and OSP (Organic Solderability Preservative). The choice of surface finish should be based on the specific requirements of the application, as well as the cost and manufacturability of the board.
FAQs
What is the difference between RF PCB design and regular PCB design?
RF PCB design is a specialized area of PCB design that focuses on the layout and construction of boards for high-frequency applications. Unlike regular PCB design, RF PCB design requires careful consideration of factors such as signal integrity, impedance matching, EMI, and power dissipation. RF PCB design also typically involves the use of specialized materials, layout techniques, and simulation tools.
What are some common RF PCB materials?
Common RF PCB materials include Rogers, Taconic, and Isola. These materials are chosen for their specific dielectric constant, loss tangent, and thermal properties, which are important for maintaining signal integrity and minimizing losses at high frequencies.
Why is impedance matching important in RF PCB design?
Impedance matching is important in RF PCB design because it ensures maximum power transfer and minimizes reflections. When the impedance of the signal path matches the impedance of the source and load, the maximum amount of power is transferred and reflections are minimized. This is important for maintaining signal integrity and preventing signal distortion.
What are some common techniques for minimizing EMI in RF PCB design?
Common techniques for minimizing EMI in RF PCB design include the use of ground planes, shielding cans, and EMI filters. Ground planes provide a low-impedance return path for high-frequency signals and can help to reduce EMI. Shielding cans can be used to enclose sensitive areas of the board and prevent signal leakage. EMI filters can be used to attenuate high-frequency noise and prevent it from entering or leaving the board.
What are some common tools used for RF PCB simulation and analysis?
Common tools used for RF PCB simulation and analysis include Ansys HFSS, Keysight ADS, and Cadence Allegro. These tools can help to identify potential issues such as impedance mismatches, signal reflections, and EMI, and can be used to optimize the design for maximum performance. Other tools such as Altium Designer and Mentor Graphics HyperLynx can also be used for PCB design and signal integrity analysis.
Conclusion
RF PCB design is a complex and specialized area of PCB design that requires careful consideration of various factors such as signal integrity, impedance matching, EMI, and power dissipation. By following key design guidelines, using specialized tools and techniques, and carefully selecting materials and manufacturing processes, it is possible to create high-performance RF PCBs that meet the specific requirements of your application. With the right knowledge and approach, RF PCB design can be a rewarding and exciting field that enables the development of cutting-edge wireless technologies.
Leave a Reply