Introduction to High Frequency PCB Design
High frequency PCB design is a critical aspect of modern electronics, particularly in the realm of wireless communication, high-speed digital systems, and RF applications. As the demand for faster data transmission and higher bandwidth continues to grow, designers must understand the unique challenges associated with high frequency PCB design to ensure optimal performance and reliability.
What is High Frequency?
In the context of PCB design, high frequency typically refers to signals with frequencies above 100 MHz. At these frequencies, the behavior of electronic components and the PCB itself begins to differ from low frequency applications. Some key factors that come into play at high frequencies include:
- Signal integrity
- Electromagnetic interference (EMI)
- Impedance matching
- Parasitic effects
- Skin effect
- Dielectric losses
Importance of High Frequency PCB Design
Proper high frequency PCB design is essential for several reasons:
- Ensuring signal integrity: At high frequencies, signals are more susceptible to distortion, reflection, and crosstalk. Careful design practices help maintain signal integrity and minimize these issues.
- Reducing EMI: High frequency signals can generate electromagnetic interference, which can disrupt the operation of nearby electronic devices. Proper design techniques help contain EMI and ensure compliance with regulatory standards.
- Optimizing performance: Well-designed high frequency PCBs enable faster data transmission, lower power consumption, and improved overall system performance.
- Enhancing reliability: By addressing the unique challenges of high frequency design, designers can create PCBs that are more reliable and less prone to failure.
Key Considerations for High Frequency PCB Design
Material Selection
The choice of PCB material is crucial for high frequency applications. The material’s dielectric constant (Dk) and dissipation factor (Df) directly impact signal propagation and losses. Some popular high frequency PCB materials include:
Material | Dielectric Constant (Dk) | Dissipation Factor (Df) |
---|---|---|
FR-4 | 4.5 | 0.02 |
Rogers RO4350B | 3.48 | 0.0037 |
Isola I-Tera MT | 3.45 | 0.0031 |
PTFE (Teflon) | 2.1 | 0.0002 |
When selecting a material, consider the following factors:
- Dielectric constant: A lower Dk results in faster signal propagation and reduced signal distortion.
- Dissipation factor: A lower Df means less energy loss and better signal integrity.
- Thermal stability: Materials with stable Dk and Df over temperature variations are preferred for high frequency applications.
- Cost: High-performance materials can be more expensive than standard FR-4, so consider the cost implications for your project.
Trace Width and Spacing
Trace width and spacing play a critical role in high frequency PCB design. Properly designed traces help maintain characteristic impedance, minimize crosstalk, and reduce EMI. Consider the following guidelines:
- Use controlled impedance traces: Determine the target characteristic impedance (typically 50Ω or 75Ω) and use a PCB stackup and trace geometry that achieves this impedance.
- Minimize trace length: Shorter traces reduce signal propagation delay and minimize the potential for signal integrity issues.
- Maintain consistent trace width: Avoid abrupt changes in trace width, as they can cause impedance discontinuities and signal reflections.
- Provide adequate spacing: Ensure sufficient spacing between traces to minimize crosstalk and maintain signal integrity.
Ground Planes and Shielding
Proper grounding and shielding are essential for high frequency PCB design. A well-designed ground plane provides a low-impedance return path for high frequency signals and helps minimize EMI. Consider the following practices:
- Use unbroken ground planes: Maintain a continuous ground plane beneath high frequency traces to provide a consistent reference plane and minimize radiated emissions.
- Implement ground stitching: Use vias to stitch ground planes together across multiple layers, reducing impedance and improving EMI performance.
- Employ shielding techniques: Use shielding cans, enclosures, or guard traces to contain EMI and prevent interference with nearby components.
Component Placement and Routing
Component placement and routing strategies are critical for high frequency PCB design. Proper placement and routing help minimize signal path length, reduce crosstalk, and improve overall performance. Consider the following guidelines:
- Place components strategically: Position high frequency components close to their associated connectors or peripherals to minimize trace length and signal propagation delay.
- Route high frequency traces carefully: Keep high frequency traces as short and direct as possible, avoiding unnecessary bends or vias.
- Separate high frequency and low frequency traces: Physically separate high frequency traces from low frequency traces to minimize crosstalk and interference.
- Use microstrip or stripline routing: Implement microstrip (traces on the outer layer) or stripline (traces sandwiched between ground planes) routing techniques for controlled impedance and improved signal integrity.
Decoupling and Filtering
Decoupling and filtering components are essential for maintaining signal integrity and reducing noise in high frequency PCB designs. Consider the following practices:
- Use decoupling capacitors: Place decoupling capacitors close to the power pins of high frequency components to minimize power supply noise and ensure stable operation.
- Implement power plane segmentation: Divide power planes into separate segments for different frequency domains, using ferrite beads or inductors to isolate the segments and prevent noise coupling.
- Apply filtering techniques: Use low-pass, high-pass, or band-pass filters to remove unwanted frequency components and improve signal quality.
Simulation and Verification
Simulating and verifying high frequency PCB designs is crucial for identifying and addressing potential issues before fabrication. Consider the following tools and techniques:
Signal Integrity Simulation
Use signal integrity simulation software, such as Mentor Graphics HyperLynx or Cadence Sigrity, to analyze the behavior of high frequency signals on your PCB. These tools can help you:
- Evaluate the impact of trace geometry, terminations, and routing on signal integrity.
- Identify potential issues, such as reflections, crosstalk, and impedance mismatches.
- Optimize your design for better signal quality and performance.
Electromagnetic Simulation
Employ electromagnetic simulation tools, like Ansys HFSS or CST Studio Suite, to study the electromagnetic behavior of your high frequency PCB. These simulations can help you:
- Assess the radiation characteristics of your design and identify potential EMI issues.
- Evaluate the effectiveness of shielding and grounding techniques.
- Optimize antenna placement and performance for wireless applications.
Design Rule Checking (DRC)
Perform design rule checks using your PCB design software to ensure that your high frequency design adheres to best practices and manufacturing constraints. DRC can help you:
- Verify trace width and spacing requirements.
- Check for proper grounding and shielding.
- Identify potential signal integrity and EMI issues.
Prototype Testing
Once your high frequency PCB design is complete, fabricate a prototype and perform thorough testing to validate its performance. Use high frequency test equipment, such as vector network analyzers (VNAs) and spectrum analyzers, to:
- Measure s-parameters and evaluate signal integrity.
- Detect and analyze EMI emissions.
- Verify the performance of filters, amplifiers, and other high frequency components.
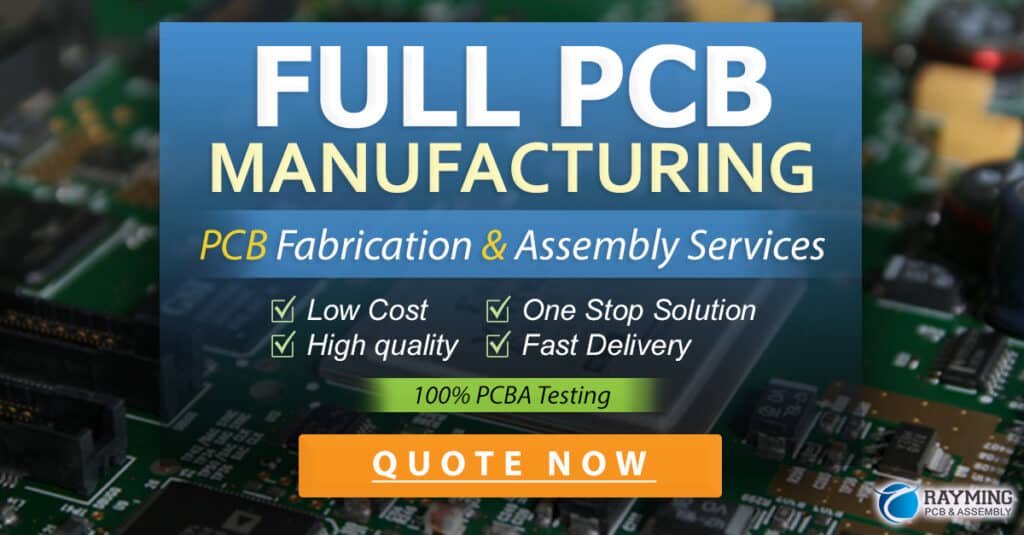
Best Practices for High Frequency PCB Layout
In addition to the key considerations discussed above, follow these best practices for successful high frequency PCB layout:
- Keep it simple: Strive for a clean, uncluttered layout with minimal trace lengths and component counts.
- Minimize vias: Vias can cause impedance discontinuities and signal reflections. Use blind or buried vias when necessary, and avoid vias in high frequency signal paths whenever possible.
- Use smooth curves: When routing high frequency traces, use smooth curves instead of sharp bends to maintain constant impedance and minimize reflections.
- Terminate traces properly: Use appropriate termination techniques, such as series or parallel termination, to match trace impedance and prevent signal reflections.
- Avoid stubs: Stubs, or unterminated trace branches, can cause signal reflections and degrade signal integrity. Keep stubs as short as possible or eliminate them entirely.
Frequently Asked Questions (FAQ)
- What is the difference between microstrip and stripline routing?
- Microstrip routing involves traces on the outer layer of the PCB, with a ground plane beneath. Stripline routing involves traces sandwiched between two ground planes. Microstrip is easier to fabricate but more susceptible to EMI, while stripline provides better isolation but is more complex to design and manufacture.
- How do I determine the appropriate trace width for my high frequency design?
- Trace width is determined by the desired characteristic impedance, the PCB material’s dielectric constant, and the thickness of the dielectric layer. Use a trace width calculator or consult your PCB manufacturer’s design guidelines to determine the appropriate width for your specific design requirements.
- What are some common EMI shielding techniques for high frequency PCBs?
- Common EMI shielding techniques include using shielding cans or enclosures, implementing guard traces around sensitive signals, and using ground stitching vias to create a Faraday cage around high frequency components.
- How do I select the appropriate decoupling capacitor values for my high frequency design?
- Decoupling capacitor values are chosen based on the frequency range of the signals being decoupled and the impedance requirements of the power distribution network. Use a combination of bulk, ceramic, and low-ESL capacitors to provide effective decoupling across a wide frequency range.
- What are some common materials used for high frequency PCB substrates?
- Common high frequency PCB substrate materials include Rogers RO4000 series, Isola I-Tera, and PTFE (Teflon). These materials offer low dielectric loss, stable dielectric constant, and excellent high frequency performance compared to standard FR-4 material.
Conclusion
Designing PCBs for high frequency applications requires careful consideration of material selection, trace geometry, grounding, shielding, component placement, and routing. By following best practices and using appropriate simulation and verification tools, designers can create high performance, reliable PCBs that meet the demanding requirements of modern high frequency electronics.
As the demand for faster data transmission and higher bandwidth continues to grow, a solid understanding of high frequency PCB design principles will become increasingly important for electronics engineers and PCB designers. By staying up-to-date with the latest techniques and technologies, designers can overcome the challenges of high frequency design and create innovative solutions for a wide range of applications.
Leave a Reply