Factors Affecting PCB Cost
The cost of a PCB depends on several key factors, including:
- Board Size and Complexity
- Number of Layers
- Material Selection
- Quantity and Economies of Scale
- Manufacturing Process and Turnaround Time
- Additional Features and Finishes
Let’s dive deeper into each of these factors to understand their impact on PCB cost.
Board Size and Complexity
The size and complexity of a PCB are among the most significant factors affecting its cost. Larger boards require more material and take longer to manufacture, resulting in higher costs. Additionally, complex designs with intricate traces, tight tolerances, and high component density can increase the cost due to the need for advanced manufacturing techniques and quality control measures.
Number of Layers
PCBs can have varying numbers of layers, ranging from single-layer to multi-layer boards. The number of layers directly impacts the cost, as each additional layer requires more material, processing, and assembly time. The table below provides a general overview of how the number of layers affects PCB cost:
Number of Layers | Relative Cost |
---|---|
Single-layer | Low |
Double-layer | Medium |
4-layer | High |
6-layer | Very High |
8-layer or more | Extremely High |
Material Selection
The choice of material for a PCB substrate can significantly influence its cost. The most common materials used in PCB manufacturing are:
- FR-4: A cost-effective, flame-retardant material suitable for most applications.
- High-Tg FR-4: An enhanced version of FR-4 with better thermal stability, ideal for high-temperature applications.
- Polyimide: A high-performance material with excellent thermal and chemical resistance, often used in aerospace and military applications.
- Aluminum: Used for PCBs that require excellent heat dissipation properties.
The table below compares the relative costs of these materials:
Material | Relative Cost |
---|---|
FR-4 | Low |
High-Tg FR-4 | Medium |
Polyimide | High |
Aluminum | Very High |
Quantity and Economies of Scale
The quantity of PCBs ordered can greatly impact the cost per unit. Manufacturers often offer discounts for larger orders due to economies of scale. As the quantity increases, the fixed costs associated with setup, tooling, and processing are spread across more units, resulting in a lower cost per PCB. The table below illustrates the relationship between quantity and relative cost per unit:
Quantity | Relative Cost per Unit |
---|---|
1-10 | Very High |
11-100 | High |
101-500 | Medium |
501-1000 | Low |
1000+ | Very Low |
Manufacturing Process and Turnaround Time
The manufacturing process and turnaround time can also affect PCB cost. Faster turnaround times often come with a premium price, as manufacturers need to prioritize and expedite the production process. Standard lead times can range from a few days to several weeks, depending on the complexity of the design and the manufacturer’s capacity.
Additionally, the choice of manufacturing process can impact cost. For example, using advanced techniques like high-density interconnect (HDI) or blind and buried vias can increase costs compared to standard through-hole or surface-mount processes.
Additional Features and Finishes
Incorporating additional features and finishes can also drive up PCB costs. Some common features and finishes that can affect pricing include:
- Solder mask color: While green is the standard color, custom colors may incur additional charges.
- Silkscreen: Adding text, logos, or other markings to the PCB surface can increase costs.
- Surface finish: Options like HASL (Hot Air Solder Leveling), ENIG (Electroless Nickel Immersion Gold), or OSP (Organic Solderability Preservative) can impact cost, with ENIG being the most expensive.
- Controlled impedance: Designing PCBs with controlled impedance for high-speed applications can increase costs due to the need for precise manufacturing and testing.
Estimating PCB Cost
To estimate the cost of a PCB, designers and engineers can use online PCB cost calculators provided by manufacturers or PCB design software. These tools typically require users to input various parameters such as board size, number of layers, material, quantity, and desired turnaround time. The calculator then generates an estimated cost based on these inputs.
However, it’s essential to note that these estimates may not always account for all the factors that can influence PCB cost. For a more accurate quote, it’s best to consult directly with the chosen PCB manufacturer and provide them with the complete design files and specifications.
Strategies for Managing PCB Cost
There are several strategies that designers and engineers can employ to manage and optimize PCB costs:
-
Design Optimization: By optimizing the PCB design for manufacturability, designers can reduce complexity, minimize the number of layers, and use standard materials and processes, all of which can help lower costs.
-
Panelization: Grouping multiple PCB designs onto a single panel can help reduce manufacturing costs by increasing efficiency and minimizing material waste.
-
Quantity Optimization: Ordering the optimal quantity of PCBs based on the project requirements and considering economies of scale can help strike a balance between cost and inventory management.
-
Early Collaboration with Manufacturers: Engaging with PCB manufacturers early in the design process can help identify potential cost-saving opportunities and ensure that the design is optimized for the specific manufacturing capabilities of the chosen supplier.
-
Design Reuse: Reusing proven PCB designs or design elements across multiple projects can help reduce design time and costs associated with prototyping and testing.
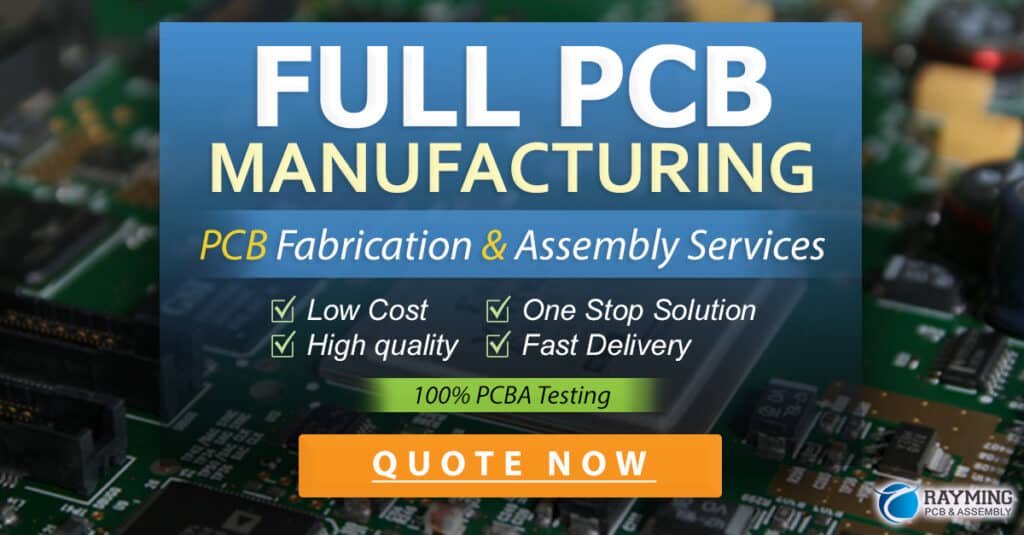
Frequently Asked Questions (FAQ)
- What is the average cost of a simple, two-layer PCB?
-
The cost of a simple, two-layer PCB can vary depending on factors such as board size, material, and quantity. On average, a small (less than 50 sq. cm), two-layer PCB in FR-4 material may cost between $10 to $50 per unit for low quantities (1-10 pieces), with prices decreasing as quantity increases.
-
How much does it cost to prototype a PCB?
-
Prototyping a PCB can cost anywhere from a few dollars to several hundred dollars, depending on the complexity of the design, the number of layers, and the chosen manufacturer. Many PCB manufacturers offer prototype services with quick turnaround times, but these often come at a premium price compared to standard lead times.
-
Can I reduce PCB costs by using a smaller board size?
-
Yes, using a smaller board size can help reduce PCB costs, as it requires less material and can often be manufactured more efficiently. However, it’s essential to ensure that the smaller size does not compromise the functionality or reliability of the design.
-
Are there any hidden costs associated with PCB manufacturing?
-
Some potential hidden costs in PCB manufacturing may include tooling charges, setup fees, or minimum order quantities (MOQs) imposed by the manufacturer. It’s essential to discuss all potential costs upfront with the manufacturer to avoid surprises and ensure accurate budgeting.
-
How can I ensure I’m getting the best price for my PCB project?
- To ensure you’re getting the best price for your PCB project, it’s recommended to compare quotes from multiple manufacturers, carefully review their capabilities and quality standards, and openly communicate your project requirements and budget constraints. Building long-term relationships with reliable manufacturers can also lead to cost savings over time.
Conclusion
Understanding the factors that influence PCB cost is crucial for designers, engineers, and project managers to effectively plan and budget for their electronic projects. By considering board size and complexity, number of layers, material selection, quantity, manufacturing process, turnaround time, and additional features, stakeholders can make informed decisions to optimize PCB costs.
Employing strategies such as design optimization, panelization, quantity optimization, early collaboration with manufacturers, and design reuse can further help manage and reduce PCB costs. Ultimately, finding the right balance between cost, quality, and project requirements is key to ensuring the success and profitability of any electronic product development endeavor.
Leave a Reply