Categories of DFM Tools
DFM tools can be broadly categorized into the following types:
- CAD-integrated DFM tools
- Standalone DFM software
- Web-based DFM platforms
- Specialized DFM tools for specific manufacturing processes
CAD-integrated DFM Tools
CAD-integrated DFM tools are built into popular computer-aided design (CAD) software packages, such as SolidWorks, Autodesk Inventor, and PTC Creo. These tools allow designers to perform DFM analysis directly within their CAD environment, streamlining the design process and reducing the need for additional software.
Key features of CAD-integrated DFM tools include:
- Design rule checks (DRC) to ensure compliance with manufacturing constraints
- Automated feature recognition for identifying and resolving potential manufacturing issues
- Cost estimation and comparison of alternative designs
- Integration with CAM software for seamless transition to manufacturing
Examples of CAD-integrated DFM tools:
Tool | CAD Platform | Key Features |
---|---|---|
DFMXpress | SolidWorks | Automated DFM checks, design guidance, and real-time feedback |
Design Advisor | Autodesk Inventor | Rule-based DFM analysis, customizable design rules, and reporting |
DFM Concurrent Costing | PTC Creo | Real-time cost estimation, manufacturing process comparison |
Standalone DFM Software
Standalone DFM software applications are independent tools that can be used alongside various CAD systems. These tools offer more comprehensive DFM analysis capabilities and can handle multiple CAD file formats.
Key features of standalone DFM software include:
- Support for a wide range of CAD file formats
- Extensive libraries of manufacturing processes and materials
- Detailed cost breakdown and manufacturability reports
- Collaboration tools for sharing and reviewing DFM results
Examples of standalone DFM software:
Tool | Key Features |
---|---|
DFMPro | Supports 20+ CAD formats, 30+ manufacturing processes, and customizable rules |
DFMA | Comprehensive DFM and DFA (Design for Assembly) analysis, cost reduction advice |
Geometric DFMPro | 3D model analysis, automatic design correction, and process-specific guidelines |
Web-based DFM Platforms
Web-based DFM platforms offer a cloud-based approach to DFM analysis, allowing users to access the tools from any device with an internet connection. These platforms often provide a collaborative environment for teams to work together on DFM optimization.
Key features of web-based DFM platforms include:
- Cloud-based access from any device
- Collaboration tools for team-based DFM optimization
- Scalable computing resources for handling complex designs
- Integration with popular CAD systems and PLM platforms
Examples of web-based DFM platforms:
Platform | Key Features |
---|---|
3DX DFM | Cloud-based DFM analysis, real-time collaboration, and AI-powered design guidance |
Fusion 360 Manufacturer | Integrated CAD/CAM/CAE platform with built-in DFM tools and cloud collaboration |
Specialized DFM Tools for Specific Manufacturing Processes
Some DFM tools are designed to cater to specific manufacturing processes, such as injection molding, sheet metal fabrication, or 3D printing. These specialized tools offer process-specific design guidelines and analysis capabilities to ensure optimal manufacturability for the chosen process.
Examples of specialized DFM tools:
Tool | Manufacturing Process | Key Features |
---|---|---|
Moldflow Adviser | Injection Molding | Plastic flow simulation, gate location optimization, and moldability analysis |
EDEM | Sheet Metal Fabrication | Bending simulation, nesting optimization, and tool wear analysis |
Materialise Magics | 3D Printing | Build preparation, support generation, and print optimization for various 3D printing technologies |
Implementing DFM Tools in the Product Development Process
To effectively leverage DFM tools in the product development process, organizations should follow these best practices:
- Integrate DFM analysis early in the design process to identify and resolve potential issues before committing to a final design.
- Establish a standardized DFM workflow that incorporates the chosen DFM tools and ensures consistent application across the organization.
- Train engineers and designers on the proper use of DFM tools and the interpretation of analysis results.
- Foster collaboration between design and manufacturing teams to ensure that DFM insights are effectively communicated and implemented.
- Continuously monitor and update DFM guidelines and best practices based on evolving manufacturing technologies and lessons learned from previous projects.
Frequently Asked Questions (FAQ)
1. What are the benefits of using DFM tools in product development?
DFM tools offer several benefits in product development, including:
- Reduced manufacturing costs by optimizing designs for ease of manufacturing
- Shortened time-to-market by identifying and resolving potential issues early in the design process
- Improved product quality and reliability by ensuring designs meet manufacturing best practices
- Enhanced collaboration between design and manufacturing teams
2. Can DFM tools be used for all types of manufacturing processes?
While some DFM tools are designed for specific manufacturing processes, such as injection molding or sheet metal fabrication, there are also general-purpose DFM tools that can be applied to a wide range of manufacturing processes. These tools typically offer customizable design rules and guidelines that can be adapted to suit different manufacturing requirements.
3. How do I choose the right DFM tool for my organization?
When selecting a DFM tool, consider the following factors:
- Compatibility with your existing CAD systems and design workflows
- Support for the manufacturing processes and materials used in your products
- Ease of use and learning curve for your design and engineering teams
- Scalability and collaboration features for handling complex projects and team-based work
- Integration with other tools in your product development ecosystem, such as PLM or CAM software
4. Can DFM tools be used for sustainable product design?
Yes, DFM tools can contribute to sustainable product design by optimizing designs for minimal material usage, reduced waste, and improved recyclability. Some DFM tools also offer features for analyzing the environmental impact of different manufacturing processes and materials, helping designers make more eco-friendly choices.
5. How do DFM tools handle the increasing complexity of modern product designs?
Modern DFM tools are designed to handle the complexity of contemporary product designs by offering advanced features such as:
- Automated feature recognition and design rule checks for identifying potential issues in complex geometries
- Simulation capabilities for analyzing the behavior of complex parts and assemblies during manufacturing
- AI and machine learning algorithms for optimizing designs based on historical data and best practices
- Cloud-based computing resources for processing large and complex datasets efficiently
As product designs continue to evolve and increase in complexity, DFM tool developers are constantly innovating to keep pace with the latest manufacturing technologies and design trends.
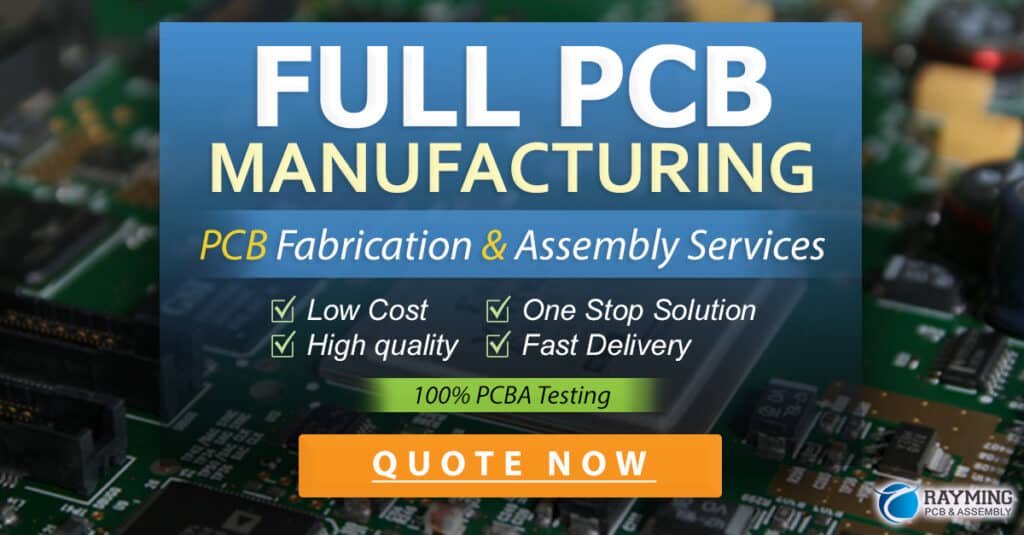
Conclusion
DFM tools play a crucial role in modern product development, helping organizations optimize their designs for efficient and cost-effective manufacturing. With a wide range of tools available, from CAD-integrated solutions to standalone software and web-based platforms, there is a DFM tool to suit every organization’s needs.
By implementing DFM tools early in the design process and following best practices for their use, companies can realize significant benefits, including reduced costs, faster time-to-market, and improved product quality. As manufacturing technologies continue to advance, the importance of DFM tools in product development will only continue to grow.
Leave a Reply