Understanding the factors affecting PCB trace width
Several variables influence the optimal width of pcb traces, including:
- Current requirements
- Allowable temperature rise
- Copper thickness (weight)
- Trace length
- Ambient temperature
- Number of copper layers
Each of these factors contributes to the trace’s ability to carry current without excessive voltage drop or heating. A pcb trace width calculator takes these variables into account to determine the appropriate trace size for your specific application.
Current carrying capacity
The primary factor in determining PCB trace width is the amount of current the trace needs to carry. As current flows through the copper trace, it encounters resistance, which leads to a voltage drop and generates heat. The wider the trace, the lower its resistance, allowing it to carry more current with less voltage drop and heating.
To calculate the required trace width based on current, you can use the following formula:
I = k * ΔT^0.44 * A^0.725
Where:
– I = Current in amps (A)
– k = Constant (0.048 for external traces, 0.024 for internal traces)
– ΔT = Temperature rise above ambient in °C
– A = Cross-sectional area of the trace in mils^2 (1 mil = 0.001 inch)
By solving this equation for A, you can determine the necessary cross-sectional area of the trace for a given current and temperature rise.
Copper thickness (weight)
PCB copper thickness, also known as copper weight, is expressed in ounces per square foot (oz/ft²). Common copper weights include 0.5 oz/ft², 1 oz/ft², and 2 oz/ft², with 1 oz/ft² being the most widely used. The thicker the copper, the more current it can carry without excessive heating.
To convert copper weight to thickness in mils, use the following conversion:
1 oz/ft² = 1.37 mils
For example, a 1 oz/ft² copper trace has a thickness of 1.37 mils.
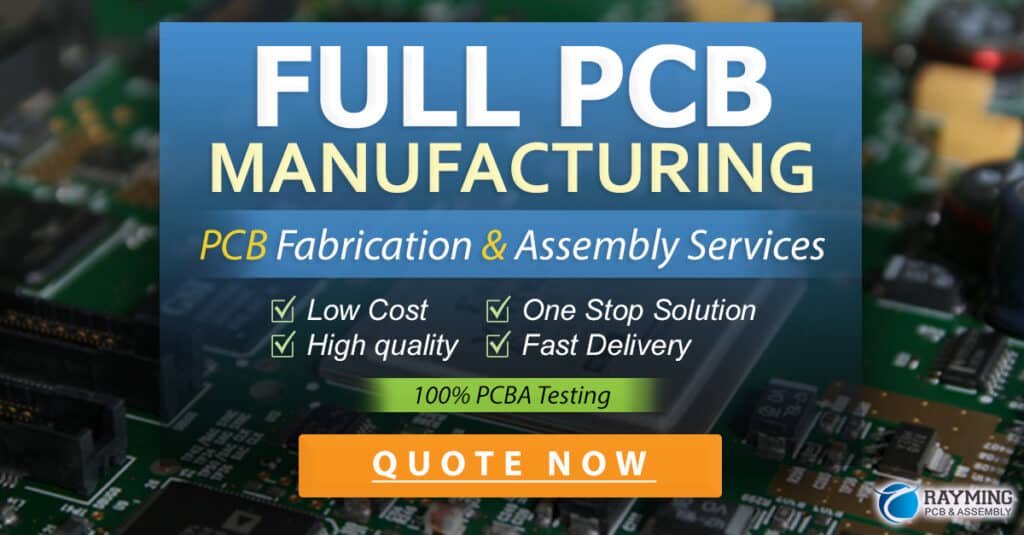
Temperature rise and ambient temperature
The allowable temperature rise is the maximum amount the trace temperature can increase above the ambient temperature without causing damage to the PCB or components. Factors such as the pcb material, component temperature ratings, and operating environment influence the allowable temperature rise.
Typical values for allowable temperature rise range from 10°C to 30°C. A lower temperature rise results in wider traces, while a higher temperature rise allows for narrower traces.
Ambient temperature also plays a role in trace width calculation. Higher ambient temperatures reduce the trace’s ability to dissipate heat, requiring wider traces to maintain the same current carrying capacity.
Trace length
Longer traces have higher resistance than shorter traces of the same width, leading to increased voltage drop and heating. To compensate for this, longer traces may require wider widths to maintain the desired current carrying capacity.
However, in most cases, trace length has a minimal impact on trace width calculation for typical PCB designs. The pcb trace width calculator usually accounts for trace length by assuming a conservative value that covers most scenarios.
Number of copper layers
Multi-layer PCBs offer the advantage of distributing current across multiple traces on different layers, effectively increasing the total cross-sectional area available for current flow. This allows for narrower traces on each individual layer while still meeting the overall current requirements.
When using a pcb trace width calculator for multi-layer boards, be sure to specify the number of layers and the current distribution among them to obtain accurate results.
Using a PCB trace width calculator
Now that we understand the factors affecting trace width let’s explore how to use a pcb trace width calculator to determine the appropriate size for your design.
- Gather the necessary information:
- Required current (A)
- Allowable temperature rise (°C)
- Copper weight (oz/ft²)
- Ambient temperature (°C)
-
Number of copper layers (if applicable)
-
Enter the data into the pcb trace width calculator. Many online calculators are available, such as the Saturn PCB Toolkit or the EEWeb PCB Trace Width Calculator.
-
The calculator will provide the minimum trace width required to meet your specifications. It may also offer additional information, such as the maximum current capacity for a given trace width and the resistance per unit length.
-
Verify that the calculated trace width is compatible with your PCB manufacturing capabilities and design rules. Adjust the input parameters if necessary to achieve a manufacturable trace size.
-
Apply the calculated trace width to your PCB design, ensuring consistent sizing for traces with similar current requirements.
Here’s an example of how to use a pcb trace width calculator:
Let’s say you need to size a trace to carry 2A of current on a 1 oz/ft² copper board with an allowable temperature rise of 20°C and an ambient temperature of 25°C.
Plugging these values into the Saturn PCB Toolkit calculator, we get the following results:
Current (A) | Copper Weight (oz/ft²) | Temperature Rise (°C) | Ambient Temperature (°C) | Trace Width (mm) | Trace Width (mils) |
---|---|---|---|---|---|
2 | 1 | 20 | 25 | 1.72 | 67.7 |
The calculator recommends a minimum trace width of 1.72mm (67.7 mils) to carry 2A with a 20°C temperature rise on a 1 oz/ft² copper board.
PCB trace width rules of thumb
While using a pcb trace width calculator provides the most accurate results, there are some general guidelines you can follow for common trace width scenarios:
- For signal traces carrying low currents (< 0.1A), a trace width of 0.2mm to 0.25mm (8-10 mils) is usually sufficient.
- Power traces carrying currents up to 1A can typically use trace widths of 0.5mm to 1mm (20-40 mils), depending on the allowable temperature rise and copper weight.
- For high-current traces (> 1A), use a pcb trace width calculator to determine the appropriate size, as the required width can vary significantly based on the specific design parameters.
Remember, these are just rough guidelines, and it’s always best to verify trace sizes using a calculator for your specific application.
Frequently asked questions (FAQ)
-
What happens if PCB traces are too narrow?
If PCB traces are too narrow for the required current, they can experience excessive voltage drop, leading to signal integrity issues or reduced performance. Narrow traces can also overheat, potentially causing damage to the PCB or components. -
Can I use different trace widths for the same net?
Yes, you can use different trace widths for the same net, especially if the current requirements vary along the net’s length. However, it’s essential to ensure that the transition between different trace widths is gradual to minimize signal reflections and maintain signal integrity. -
How does the PCB material affect trace width calculations?
The PCB material’s thermal conductivity influences how effectively the traces can dissipate heat. Materials with higher thermal conductivity, such as aluminum-backed PCBs, can allow for narrower traces compared to standard FR-4 material. However, the pcb trace width calculator usually assumes standard FR-4 material unless otherwise specified. -
What is the minimum trace width for PCB manufacturing?
The minimum trace width depends on the pcb manufacturer’s capabilities and the chosen fabrication technology. For standard pcb production, minimum trace widths typically range from 0.1mm to 0.15mm (4-6 mils). However, advanced technologies like HDI (High-Density Interconnect) can achieve trace widths as small as 0.05mm (2 mils) or less. -
Can I use a pcb trace width calculator for flexible pcbs?
Yes, you can use a pcb trace width calculator for flexible PCBs, but keep in mind that the calculator assumes a rigid PCB material like FR-4. Flexible PCB materials may have different thermal properties, so it’s essential to consult with your flexible PCB manufacturer to ensure the calculated trace widths are appropriate for your specific material and application.
Conclusion
Calculating the appropriate trace width is a critical step in PCB design to ensure proper current carrying capacity, minimize voltage drop, and prevent overheating. By understanding the factors that influence trace width and using a pcb trace width calculator, you can easily determine the optimal trace size for your specific design requirements.
Remember to consider current requirements, allowable temperature rise, copper weight, ambient temperature, and the number of copper layers when using a pcb trace width calculator. Always verify that the calculated trace widths are compatible with your PCB manufacturing capabilities and design rules.
By following these guidelines and using a pcb trace width calculator, you can create reliable, high-performance PCBs that meet your application’s needs.
Leave a Reply