Current Flow
The amount of current that will flow through a trace is the starting point for trace width calculations.
Know Your Current Requirements
- What are the current demands of the various components and ICs on your board? Reference component datasheets
- What are peak vs nominal currents? Size for peak when in doubt
- High current traces may need multiple vias to distribute heat
Use Trace Width Calculator
There are many online pcb trace width calculators that will help determine width based on current. Key inputs:
- Current (A)
- PCB copper thickness (oz)
- Acceptable temperature rise
Output trace width that can handle desired current without overheating.
Example trace width calculation:
Current: 3 A
Copper thickness: 1 oz
Temp rise: 20°C
Output trace width: 0.4 mm
Table of sample trace widths for common currents:
Current | 1 oz Copper Width | 2 oz Copper Width |
---|---|---|
1 A | 0.25 mm | 0.127 mm |
2 A | 0.4 mm | 0.2 mm |
5 A | 0.8 mm | 0.4 mm |
As current increases, wider traces required. Also notice thinner 1 oz copper requires wider traces than thicker 2 oz.
Temperature Rise and Heating Effects
In addition to simply handling peak current flows, pcb traces need to avoid excessive heating which can cause thermal damage or reliability issues.
Specify Allowable Temperature Rise
- How hot can traces reasonably get before risking problems?
- Common choice is 10-20°C rise over ambient
Consider Heating Effects
- Thicker copper traces handle more current without overheating
- Wider traces also spread heat better
- Keep high current traces short to localize heating
Use online trace width calculators to output size traces based on a selected temp rise spec such as 20°C.
pcb layout Rules & Constraints
In addition to electrical requirements, trace widths are often constrained by various board layout rules.
Know PCB Fab Capabilities
- What are your board house minimum/maximum trace capabilities?
- Common minimum: 0.15-0.2 mm
- Max before moving to copper pours: 0.5-1 mm
Account for Other Spacing Rules
- How close can traces be before risk of shorts?
- Typical design rules call for 0.1-0.2 mm between traces
Example:
Trace width: 0.4 mm
Spacing: 0.2 mm
Total pitch: 0.4 + 0.2 = 0.6 mm
Arrange traces based on width and spacing rules to route your connections.
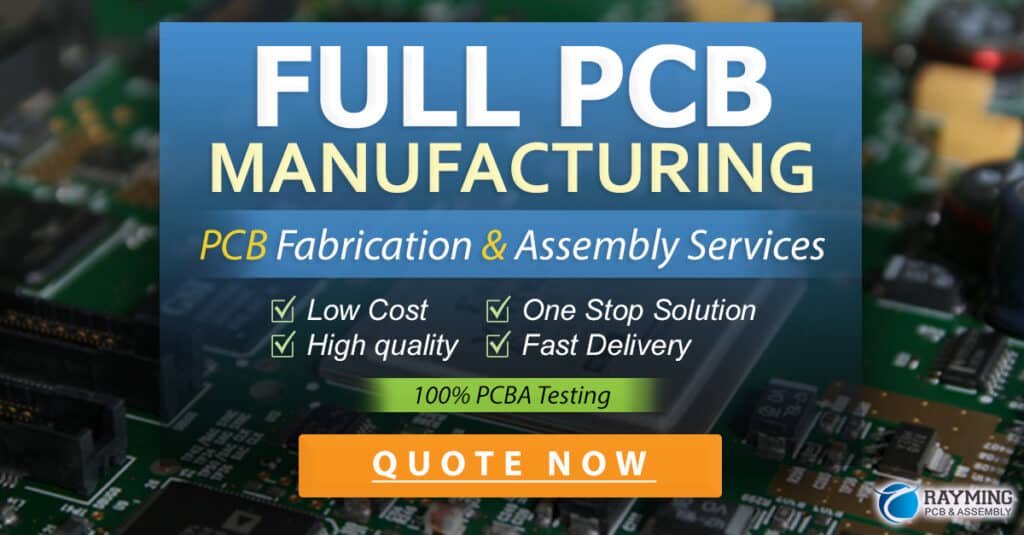
Matching Trace Widths
For signals like differential pairs, it is often important to match trace widths.
Set Rules for Matched Traces
- When are matched trace widths needed? Differential signals? Impedance matching?
- How close do widths need to match? 10% often acceptable
Enable Consistency with Design Standards
- Establish naming conventions and guidelines in your design system
- Create net classes for groups of traces needing consistency
Example:
Diff pair DP1: Target 0.5 mm trace width
0.4 - 0.6 mm range (20% tolerance)
Follow standards manual rules to keep trace widths balanced where needed.
Adjusting Trace Widths in Layout
Trace widths often need tuning while routing to optimize signal performance or ease PCB layout.
Strategies to Widen Traces
Options to increase trace widths:
- Reduce spacing between nearby traces
- Convert traces to copper pours where space available
- Use thermal reliefs when pouring large planes
Strategies to Narrow Traces
Ways to decease trace widths:
- Adjust routing angles to zig-zag through smaller spaces
- Drop down to next allowable width standard
- Rotate components to access more routing channels
When to Deviate from Standards
- First follow guidelines and requirements set in your design standards
- Make exceptions only where needed for layout or performance
Carefully consider impacts before significantly changing trace widths in layout.
Effects of High Frequency Signals
With signals above 50 MHz or so, controlled trace impedance becomes important factor for reflection control and signal integrity.
Know Your PCB Stackup
- Dielectric constant (Dk) and thickness for all layers
- Dk tolerance if material is “general purpose”
Use Transmission Line Modeling
- Model traces as transmission lines at higher frequencies
- Calculate target impedance based on stackup properties
- Output target trace widths to achieve desired impedance
Example:
FR4 Dielectric
Thickness: 0.063"
Dk: 4.5
Target Zo: 50 ohms
Calculated trace width: 0.3 mm
Follow transmission line modeling guidelines for optimal high speed performance.
Final Verification
Always validate PCB trace widths meet all electrical and physical design constraints through a thorough design review process before manufacturing boards.
Simulation Checks
Verify width selections through:
- Thermal modeling to confirm no overheating
- Signal integrity simulations checking for reflection noise or losses
Design Rule Checks
Run design rule checks confirming compliance with:
- Minimum spacing requirements
- Maximum trace width needs
- Impedance tolerance ranges
Adjust widths iteratively as needed based on verification checks.
FAQ
Why do wider PCB traces handle more current?
Wider copper traces have reduced resistance and can thus carry higher current levels without excessive resistive heating. For example, a 0.4 mm trace has roughly half the end-to-end resistance of a 0.2 mm trace width using the same copper thickness.
How accurate do trace widths need to be?
It’s rare pcb fabrication can hold extremely tight width tolerances. A good rule of thumb is to hold trace widths within +/- 10% to account for reasonable fabrication variance. Even allowing 20% variance is generally acceptable.
What PCB stackup details are needed?
The key parameters needed are copper thickness (1 oz vs 2 oz for example), dielectric materials used (FR4, Roger’s, Getek), dielectric thicknesses, and material dielectric constants. These stackup details drive construction of transmission line models.
When should I use a copper pour instead of traces?
Use coppers pours connected by thermal reliefs when more than approximately 0.5 mm trace widths are needed. Anything wider is difficult for most board fab processes. Pours help minimize etchant removal under traces during fabrication as an added benefit.
How do I account for high frequency edge effects?
At higher frequencies, electric fields become disrupted at trace edges, effectively altering impedance. Many trace width calculators or simulators can account for “edge effects” – either use these or budget 5-10% wider traces to compensate.
Leave a Reply