What is PCB Impedance?
PCB impedance refers to the opposition to the flow of electrical current through the traces on a printed circuit board. It is a complex quantity that includes both resistance and reactance, and is measured in ohms (Ω). The impedance of a PCB trace depends on several factors, including:
- Trace width
- Trace thickness
- Dielectric constant of the PCB material
- Thickness of the dielectric layer
- Presence of ground or power planes
Maintaining consistent and controlled impedance throughout the PCB is essential for several reasons:
- Signal integrity: Matched impedance minimizes reflections and distortions, ensuring clean and reliable signal transmission.
- Power efficiency: Proper impedance matching allows for maximum power transfer from the source to the load.
- Electromagnetic compatibility (EMC): Controlled impedance reduces electromagnetic interference (EMI) and improves EMC compliance.
Types of PCB Impedance
There are two main types of PCB impedance:
- Characteristic impedance (Z0): This is the impedance of a transmission line with an infinite length. It is determined by the geometry and materials of the PCB trace and its surrounding environment.
- Differential impedance (Zdiff): This is the impedance between two coupled traces, such as in a differential pair. It is important for high-speed differential signaling, such as USB, HDMI, and Ethernet.
Factors Affecting PCB Impedance
Several factors influence the impedance of a PCB trace:
Trace Geometry
The width, thickness, and spacing of the traces play a significant role in determining the impedance. Wider traces have lower impedance, while narrower traces have higher impedance. The trace thickness also affects impedance, with thicker traces having lower impedance.
Dielectric Material
The dielectric constant (Er) of the PCB material impacts the impedance. Higher Er values result in lower impedance, while lower Er values lead to higher impedance. Common PCB materials and their dielectric constants include:
Material | Dielectric Constant (Er) |
---|---|
FR-4 | 4.0 – 4.5 |
Rogers RO4003C | 3.38 |
Rogers RO4350B | 3.66 |
Isola IS410 | 4.11 |
Dielectric Thickness
The thickness of the dielectric layer between the trace and the reference plane (ground or power) affects the impedance. A thicker dielectric layer results in higher impedance, while a thinner layer leads to lower impedance.
Reference Planes
The presence and proximity of ground or power planes influence the impedance. Closer reference planes result in lower impedance, while more distant planes lead to higher impedance.
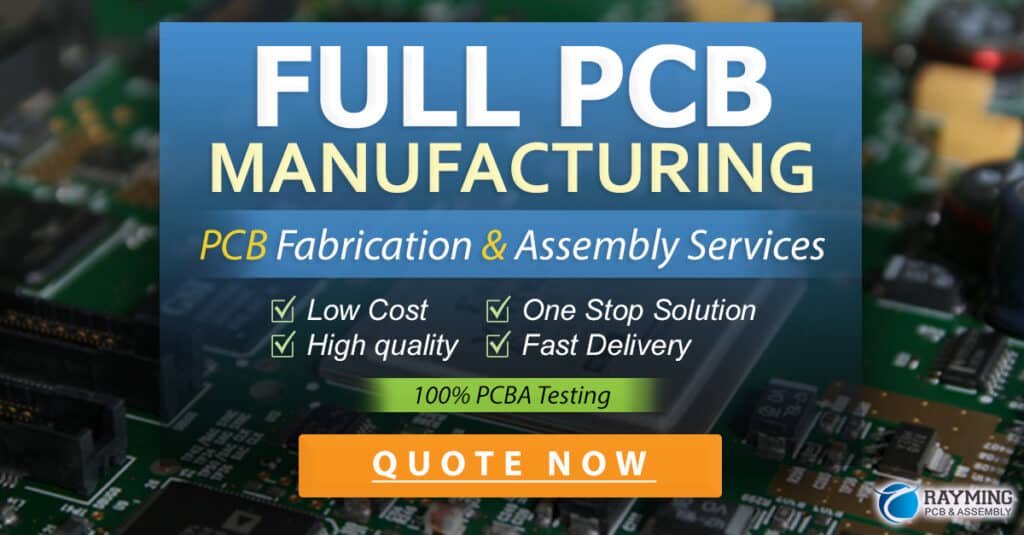
PCB Impedance Calculator
To calculate the impedance of a PCB trace, you can use a PCB impedance calculator. These calculators take into account the various factors affecting impedance and provide an estimated value based on the input parameters.
Here’s an example of how to use a PCB impedance calculator:
- Select the trace type (microstrip, stripline, or coplanar waveguide).
- Input the trace width and thickness.
- Input the dielectric constant and thickness of the PCB material.
- Specify the desired characteristic impedance (e.g., 50Ω or 100Ω).
- Click “Calculate” to obtain the estimated impedance value.
Some popular online PCB impedance calculators include:
- EEWeb PCB Impedance Calculator
- Saturn PCB Toolkit Impedance Calculator
- Multi-Teknik PCB Impedance Calculator
It’s important to note that these calculators provide approximate values based on simplified models. For more accurate results, you should use a full-wave electromagnetic (EM) simulation tool, such as Ansys HFSS or Keysight ADS.
PCB Stack-up and Impedance
The PCB stack-up, which refers to the arrangement of layers in a multi-layer board, plays a crucial role in impedance control. A well-designed stack-up ensures consistent impedance throughout the board and minimizes signal integrity issues.
When designing a PCB stack-up for impedance control, consider the following:
- Use dedicated signal and reference layers: Assign specific layers for signals and their corresponding reference planes (ground or power).
- Maintain symmetry: Ensure that the stack-up is symmetrical, with equal dielectric thicknesses on either side of the signal layers.
- Minimize dielectric thickness: Thinner dielectric layers result in lower impedance and better signal integrity.
- Use high-quality dielectric materials: Choose low-loss, high-frequency dielectric materials for improved performance.
Here’s an example of a 6-layer PCB stack-up optimized for impedance control:
Layer | Material | Thickness (mil) | Purpose |
---|---|---|---|
1 | FR-4 | 1.3 | Signal |
2 | FR-4 | 6.7 | Ground |
3 | FR-4 | 13.4 | Signal |
4 | FR-4 | 13.4 | Signal |
5 | FR-4 | 6.7 | Power |
6 | FR-4 | 1.3 | Signal |
Impedance Matching Techniques
To ensure proper impedance matching between the source, transmission line, and load, various techniques can be employed:
- Termination resistors: Use series or parallel termination resistors at the source or load end to match the impedance.
- Impedance matching networks: Implement L-C or R-C networks to match the impedance over a specific frequency range.
- Tapered transmission lines: Gradually change the width of the trace to match the impedance between two different sections.
- Differential signaling: Use differential pairs with controlled impedance to minimize noise and improve signal integrity.
Measuring PCB Impedance
While PCB impedance calculators provide estimated values, it’s essential to measure the actual impedance of the manufactured pcb to ensure compliance with the design specifications. There are two primary methods for measuring PCB impedance:
- Time Domain Reflectometry (TDR): TDR measures the impedance by sending a fast-rise-time pulse through the trace and analyzing the reflections. It provides an impedance profile along the length of the trace.
- Vector Network Analyzer (VNA): A VNA measures the S-parameters of the PCB trace over a wide frequency range. The S-parameters can be used to calculate the characteristic impedance and reflection coefficients.
Best Practices for PCB Impedance Control
To achieve optimal impedance control in your PCB design, follow these best practices:
- Define impedance requirements early in the design process.
- Use a PCB impedance calculator to estimate the required trace dimensions.
- Design a symmetrical and well-balanced PCB stack-up.
- Route critical signals on dedicated layers with proper reference planes.
- Maintain consistent trace width and spacing throughout the board.
- Use ground pours and stitching vias to minimize discontinuities.
- Simulate critical traces using a full-wave EM simulator.
- Specify impedance requirements and tolerances in the PCB fabrication notes.
- Measure the actual impedance of the manufactured PCB to verify compliance.
Frequently Asked Questions (FAQ)
-
What is the typical impedance value for a PCB trace?
A: The most common characteristic impedance values for PCB traces are 50Ω and 100Ω. However, other values such as 75Ω or 90Ω may be used depending on the application and interface requirements. -
How does PCB impedance affect signal integrity?
A: Mismatched impedances cause reflections and distortions in the signal, leading to signal integrity issues like overshoot, undershoot, ringing, and crosstalk. Controlled impedance ensures clean and reliable signal transmission. -
What is the difference between characteristic impedance and differential impedance?
A: Characteristic impedance (Z0) is the impedance of a single trace with respect to a reference plane. Differential impedance (Zdiff) is the impedance between two coupled traces, such as in a differential pair. -
How accurate are PCB impedance calculators?
A: PCB impedance calculators provide approximate values based on simplified models. They are useful for initial estimates, but for more accurate results, a full-wave electromagnetic (EM) simulation tool should be used. -
What is the impact of PCB impedance on EMC?
A: Controlled PCB impedance helps in reducing electromagnetic interference (EMI) and improving electromagnetic compatibility (EMC) compliance. Mismatched impedances can lead to increased EMI, compromising the device’s EMC performance.
Conclusion
Calculating and controlling PCB impedance is crucial for ensuring signal integrity, power efficiency, and EMC compliance in high-speed digital and RF designs. By understanding the factors affecting impedance, using PCB impedance calculators, and following best practices for impedance control, designers can create reliable and high-performance PCBs.
Remember to consider the PCB stack-up, trace geometry, dielectric materials, and reference planes when designing for impedance control. Simulating critical traces and measuring the actual impedance of the manufactured PCB are essential steps in verifying compliance with the design specifications.
By mastering the art of PCB impedance calculation and control, you can optimize your designs for superior signal quality and robustness in today’s demanding electronic applications.
Leave a Reply