Introduction to PCB Heat Dissipation
Printed Circuit Boards (PCBs) are essential components in modern electronics, forming the backbone of devices ranging from smartphones to industrial equipment. As electronic components become more powerful and compact, managing heat dissipation becomes a critical factor in ensuring the reliability and longevity of PCBs. Excessive heat can lead to component failure, reduced performance, and even complete system breakdown.
In this article, we will explore various strategies and techniques for effective PCB heat dissipation. By understanding the principles of heat transfer and implementing appropriate design considerations, engineers can optimize their PCBs to manage thermal challenges effectively.
The Importance of PCB Heat Dissipation
Why is Heat Dissipation Crucial for PCBs?
Heat dissipation is a vital aspect of PCB design for several reasons:
-
Component Reliability: Excessive heat can cause electronic components to degrade or fail prematurely. High temperatures accelerate the aging process and can lead to reduced performance or complete failure.
-
System Stability: As components heat up, their electrical characteristics may change, leading to unstable behavior or malfunctions. Proper heat dissipation helps maintain stable operating conditions.
-
User Safety: In some cases, poorly managed heat can pose a safety risk to users. Overheating can cause burns or even fire hazards if left unchecked.
-
Product Longevity: Effective heat dissipation contributes to the overall longevity of the product. By preventing thermal stress on components, the PCB can operate reliably for an extended period.
Factors Affecting PCB Heat Generation
Several factors contribute to heat generation in PCBs:
-
Power Dissipation: The amount of power consumed by electronic components directly influences the heat generated. Higher power consumption leads to increased heat generation.
-
Component Density: As PCBs become more compact, the density of components increases. Tightly packed components can trap heat and make dissipation more challenging.
-
Operating Frequency: High-frequency circuits generate more heat due to increased switching losses and power consumption.
-
Ambient Temperature: The surrounding environment’s temperature affects the PCB’s ability to dissipate heat. Higher ambient temperatures make it more difficult to remove heat effectively.
Heat Transfer Mechanisms in PCBs
To effectively dissipate heat from PCBs, it is essential to understand the three primary mechanisms of heat transfer: conduction, convection, and radiation.
Conduction
Conduction is the transfer of heat through direct contact between materials. In PCBs, heat conducts from the electronic components to the PCB substrate and then to the surrounding environment. The thermal conductivity of the materials used in the PCB, such as the substrate, copper traces, and solder joints, plays a crucial role in conductive heat transfer.
Convection
Convection involves the transfer of heat through the movement of fluids or gases. In PCBs, convection occurs when air or other fluids circulate around the board, carrying heat away from the components. Natural convection relies on the buoyancy of hot air, while forced convection uses fans or other mechanical means to enhance airflow.
Radiation
Radiation is the emission of heat in the form of electromagnetic waves. In PCBs, radiation occurs when hot components emit infrared radiation to cooler surroundings. The effectiveness of radiative heat transfer depends on factors such as the emissivity of the surfaces and the temperature difference between the component and the environment.
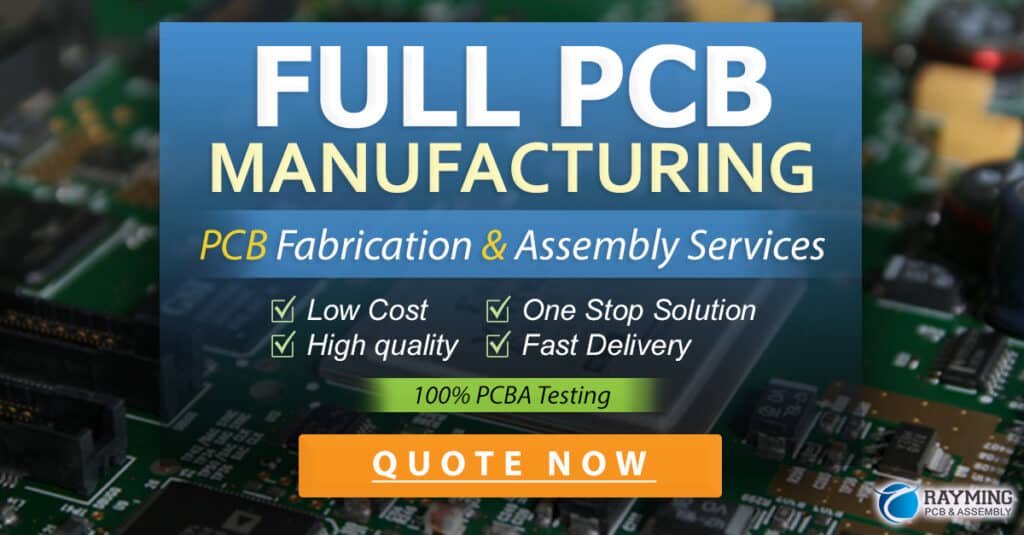
PCB Design Considerations for Heat Dissipation
Effective heat dissipation in PCBs requires careful consideration during the design phase. Several design techniques can be employed to optimize thermal management:
Component Placement and Spacing
Strategic component placement and spacing can significantly impact heat dissipation. Consider the following guidelines:
- Place high-power components, such as processors and power regulators, away from heat-sensitive components to minimize thermal interaction.
- Provide adequate spacing between components to allow for airflow and heat dissipation.
- Arrange components in a way that promotes natural convection, with hot components placed higher on the board.
Thermal Vias and Copper Pours
Thermal vias and copper pours are effective techniques for enhancing heat conduction in PCBs:
- Thermal vias are plated through-holes that provide a low-resistance path for heat to transfer from components to the PCB substrate or other layers.
- Copper pours are large areas of copper on the PCB that act as heat spreaders. They help distribute heat evenly across the board and improve overall thermal conductivity.
Heatsinks and Thermal Interface Materials
Heatsinks and thermal interface materials (TIMs) are commonly used to enhance heat dissipation in PCBs:
- Heatsinks are metal structures attached to high-power components to increase the surface area for heat dissipation. They facilitate convective and radiative heat transfer.
- TIMs, such as thermal grease or thermal pads, are used to improve the thermal contact between components and heatsinks. They fill air gaps and reduce thermal resistance.
Board Material Selection
The choice of PCB substrate material can significantly impact heat dissipation:
- High-performance materials like aluminum or copper-based substrates offer excellent thermal conductivity compared to standard FR-4 substrates.
- Metal core PCBs (MCPCBs) incorporate a metal layer within the substrate to enhance heat spreading and dissipation.
Advanced Cooling Techniques
In addition to basic design considerations, several advanced cooling techniques can be employed for more demanding thermal management requirements:
Liquid Cooling
Liquid cooling involves the use of fluids to remove heat from PCBs:
- Liquid cold plates are attached to high-power components, and a coolant is circulated through channels to absorb and transfer heat away from the PCB.
- Immersion cooling involves submerging the entire PCB in a dielectric liquid, which provides excellent heat transfer and allows for high-density component packaging.
Thermoelectric Cooling
Thermoelectric cooling uses the Peltier effect to actively pump heat away from components:
- Thermoelectric coolers (TECs) are solid-state devices that create a temperature difference when an electric current is applied.
- TECs can be attached to specific components or integrated into the PCB to provide localized cooling.
Phase Change Materials
Phase change materials (PCMs) absorb heat by undergoing a phase transition, typically from solid to liquid:
- PCMs are encapsulated and placed in contact with high-power components.
- As the component generates heat, the PCM absorbs the heat and melts, maintaining a constant temperature until the phase change is complete.
Thermal Simulation and Analysis
Thermal simulation and analysis tools are valuable resources for predicting and optimizing the thermal performance of PCBs:
- Computational Fluid Dynamics (CFD) software allows engineers to simulate heat transfer and airflow in PCBs, identifying hot spots and evaluating cooling solutions.
- Finite Element Analysis (FEA) tools enable the modeling of thermal stress and deformation in PCBs, helping to ensure structural integrity under thermal loads.
Testing and Validation
After implementing thermal management techniques, it is crucial to test and validate the PCB’s thermal performance:
- Thermal imaging cameras can be used to visualize the temperature distribution across the PCB, identifying hot spots and areas of concern.
- Temperature sensors, such as thermocouples or resistance temperature detectors (RTDs), can be placed at critical locations to monitor temperatures during operation.
- Stress testing involves subjecting the PCB to extreme thermal conditions to assess its resilience and identify any weaknesses in the thermal design.
Conclusion
Effective heat dissipation is a critical aspect of PCB design that ensures the reliability, stability, and longevity of electronic systems. By understanding the principles of heat transfer and implementing appropriate design techniques, engineers can optimize their PCBs to manage thermal challenges effectively.
From strategic component placement and the use of thermal vias and copper pours to advanced cooling techniques like liquid cooling and phase change materials, a wide range of options are available to address the heat dissipation needs of PCBs.
Thermal simulation, analysis, and testing are essential tools in the thermal management process, allowing engineers to predict, optimize, and validate the thermal performance of their designs.
By prioritizing heat dissipation considerations throughout the PCB design process, engineers can create robust and reliable electronic systems that can withstand the thermal demands of modern applications.
FAQs
Q1: What is the most effective way to dissipate heat from high-power components on a PCB?
A1: The most effective way to dissipate heat from high-power components is to use a combination of techniques. This can include using heatsinks and thermal interface materials to enhance heat transfer, incorporating thermal vias and copper pours to spread heat across the PCB, and employing advanced cooling techniques like liquid cooling or thermoelectric cooling for demanding applications.
Q2: Can I use standard FR-4 substrates for PCBs with high thermal requirements?
A2: While standard FR-4 substrates can be used in many PCB designs, they may not be suitable for applications with high thermal requirements. In such cases, it is recommended to consider high-performance materials like aluminum or copper-based substrates, or even metal core PCBs (MCPCBs) that offer better thermal conductivity and heat spreading capabilities.
Q3: How do I identify hot spots on my PCB during the design phase?
A3: Thermal simulation and analysis tools, such as Computational Fluid Dynamics (CFD) software, can be used to identify hot spots on a PCB during the design phase. These tools allow engineers to simulate heat transfer and airflow, visualizing temperature distributions and identifying areas of concern before the PCB is manufactured.
Q4: What is the role of thermal vias in PCB heat dissipation?
A4: Thermal vias are plated through-holes that provide a low-resistance path for heat to transfer from components to the PCB substrate or other layers. They help conduct heat away from hot components and spread it across the board. By strategically placing thermal vias near high-power components, engineers can enhance heat dissipation and prevent localized hot spots.
Q5: How do I choose the right heatsink for my PCB components?
A5: When selecting a heatsink for PCB components, consider factors such as the component’s power dissipation, the available space on the PCB, and the desired thermal performance. Heatsinks with larger surface areas and more fins generally offer better heat dissipation. It’s also important to ensure proper thermal contact between the component and the heatsink using thermal interface materials like thermal grease or thermal pads.
Cooling Technique | Advantages | Disadvantages |
---|---|---|
Heatsinks | Simple and passive, no power required | Limited cooling capacity, requires airflow |
Copper Pours | Spreads heat evenly across the PCB | Increases PCB weight and cost |
Liquid Cooling | Excellent heat transfer, high cooling capacity | Complex setup, requires pumps and reservoirs |
Thermoelectric Cooling | Active cooling, can cool below ambient | High power consumption, limited cooling capacity |
Phase Change Materials | Passive cooling, absorbs heat during phase change | Limited heat absorption capacity, adds weight |
Leave a Reply