Introduction to PCB Manufacturing
Printed Circuit Boards (PCBs) are the backbone of modern electronics. They provide a platform for connecting electronic components and creating complex circuits. If you’re interested in electronics and want to learn how to design and manufacture your own PCBs, this comprehensive guide will walk you through the process step by step.
What is a PCB?
A PCB is a flat board made of insulating material, such as fiberglass or composite epoxy, with conductive copper traces printed on one or both sides. These traces connect various electronic components, such as resistors, capacitors, and integrated circuits (ICs), to form a functional electronic circuit.
PCBs come in various types, including:
Type | Description |
---|---|
Single-sided | Copper traces on one side of the board |
Double-sided | Copper traces on both sides of the board |
Multi-layer | Multiple layers of copper traces separated by insulating material |
Flexible | Made of flexible materials for use in compact or movable devices |
Rigid-Flex | Combination of rigid and flexible sections for complex designs |
Planning Your PCB Design
Before you start designing your PCB, it’s essential to plan your project carefully. This involves several key steps:
1. Define Your Circuit Requirements
Determine the purpose and functionality of your electronic circuit. Consider factors such as:
- Power requirements
- Input and output signals
- Required components
- Size constraints
2. Create a Schematic Diagram
A schematic diagram is a visual representation of your electronic circuit. It shows the connections between components using standardized symbols. You can create a schematic diagram using electronic design automation (EDA) software or by drawing it by hand.
3. Choose Your PCB Software
There are many PCB design software options available, ranging from free open-source tools to professional-grade packages. Some popular choices include:
- KiCad (open-source)
- Eagle (free for non-commercial use)
- Altium Designer (professional)
- OrCAD (professional)
Choose a software that fits your needs, budget, and skill level.
Designing Your PCB Layout
Once you have your schematic diagram and have chosen your PCB software, you can start designing the physical layout of your PCB.
1. Create a Component Footprint Library
A footprint is the physical representation of a component on the PCB. Create a library of footprints for all the components in your circuit. Most PCB software packages include built-in footprint libraries, but you may need to create custom footprints for unique components.
2. Place Components on the PCB
Arrange the components on the PCB according to your schematic diagram. Consider factors such as:
- Component orientation
- Spacing between components
- Thermal considerations
- Mechanical constraints
3. Route the Connections
Use the PCB software to route the copper traces between the components according to your schematic diagram. Consider factors such as:
- Trace width
- Trace spacing
- Via placement
- Impedance matching (for high-speed signals)
4. Add Silkscreen and Solder Mask Layers
The silkscreen layer adds text and graphics to the PCB for labeling purposes. The solder mask layer protects the copper traces from accidental short circuits during soldering. Most PCB software packages allow you to easily add these layers to your design.
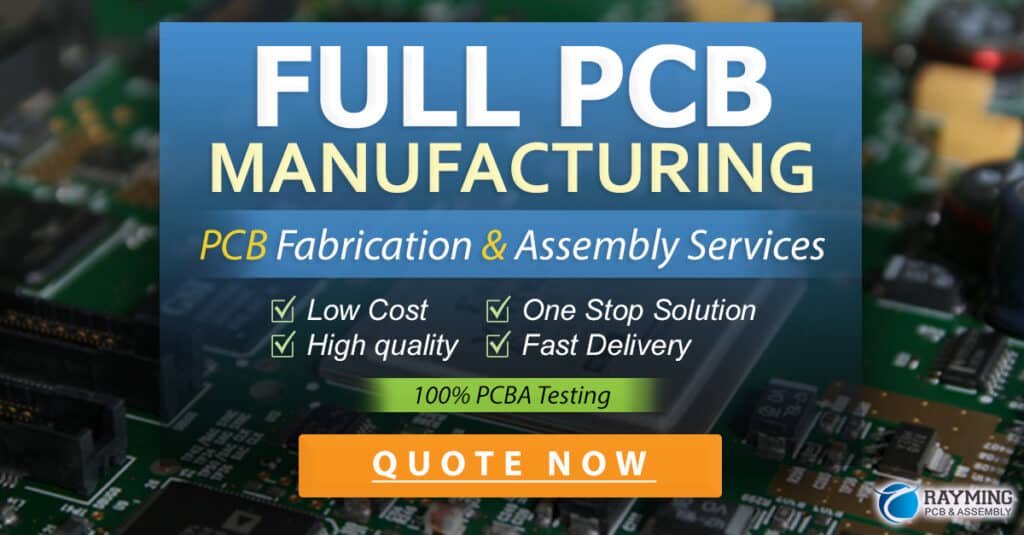
Manufacturing Your PCB
After completing your PCB layout, you’re ready to manufacture your board.
1. Generate Manufacturing Files
Export the necessary manufacturing files from your PCB software. These typically include:
- Gerber files (for each PCB layer)
- Drill files (for hole locations and sizes)
- Pick-and-place files (for automated assembly)
- Bill of Materials (BOM)
2. Choose a PCB Manufacturer
Select a PCB manufacturer based on factors such as:
- Cost
- Turnaround time
- Minimum order quantity
- Manufacturing capabilities (e.g., layer count, material options)
Some popular PCB manufacturers include:
- JLCPCB
- PCBWay
- OSH Park
- Seeed Studio
3. Place Your Order
Upload your manufacturing files to the chosen PCB manufacturer’s website and place your order. Specify any additional requirements, such as surface finish, soldermask color, and silkscreen color.
Assembling Your PCB
After receiving your manufactured PCB, you can proceed with assembling the components.
1. Gather Your Components
Collect all the necessary components for your PCB based on your BOM. Ensure that you have the correct values, packages, and quantities.
2. Solder the Components
Solder the components onto the PCB using a soldering iron or a reflow oven. If you’re hand-soldering, follow these steps:
- Apply a small amount of solder to one pad of a component footprint.
- Place the component on the footprint, holding it in place with tweezers.
- Touch the soldering iron to the pad and the component lead simultaneously.
- Apply solder to the other pads and leads.
- Trim any excess component leads.
3. Inspect Your Assembled PCB
Visually inspect your assembled PCB for any soldering defects, such as bridging (short circuits) or poor solder joints. Use a multimeter to check for continuity and correct component placement.
Testing and Debugging Your PCB
After assembling your PCB, it’s crucial to test and debug it to ensure proper functionality.
1. Power Up Your PCB
Apply power to your PCB, starting with a low voltage and current to avoid damaging components in case of short circuits. Gradually increase the voltage and current to the desired levels.
2. Test Functional Blocks
Test individual functional blocks of your circuit, such as power supply, input/output stages, and signal processing sections. Use an oscilloscope or logic analyzer to observe signals and verify their correctness.
3. Debug and Troubleshoot
If you encounter issues during testing, use systematic debugging techniques to identify and resolve problems. Some common debugging steps include:
- Checking for proper power supply voltages
- Verifying component values and orientations
- Inspecting solder joints for defects
- Probing signals with an oscilloscope or multimeter
- Comparing observed behavior with expected results
Advanced PCB Design Techniques
As you gain experience in PCB design and manufacturing, you can explore advanced techniques to improve your designs.
1. High-Speed Design Considerations
When designing PCBs for high-speed applications, consider factors such as:
- Impedance matching
- Signal integrity
- Crosstalk reduction
- Proper grounding and shielding
2. Thermal Management
For PCBs with high-power components, thermal management is crucial. Consider techniques such as:
- Using larger copper areas (pours) for heat dissipation
- Incorporating thermal vias to transfer heat to other layers
- Using heatsinks or fans for active cooling
3. Design for Manufacturing (DFM)
To ensure your PCBs are easily manufacturable, follow DFM guidelines, such as:
- Adhering to minimum trace width and spacing requirements
- Avoiding acute angles in traces
- Using standard component packages and footprints
- Providing adequate clearances for assembly and soldering
Frequently Asked Questions (FAQ)
1. What is the minimum trace width and spacing for a PCB?
The minimum trace width and spacing depend on the PCB manufacturer and the desired PCB specifications. Typically, for a standard 2-layer PCB, the minimum trace width and spacing are around 6-8 mils (0.15-0.20 mm). However, for high-density designs or advanced manufacturing capabilities, these values can be as low as 3-4 mils (0.075-0.10 mm).
2. Can I make double-sided PCBs at home?
Yes, it is possible to make double-sided PCBs at home using a process called “through-hole riveting” or “through-hole plating.” This involves drilling holes in the PCB, inserting wires or rivets through the holes, and soldering them on both sides to create connections between the two layers. However, this process is more time-consuming and less reliable than professional PCB manufacturing.
3. What is the difference between surface mount (SMD) and through-hole (THT) components?
Surface mount (SMD) components are mounted directly on the surface of the PCB, with their leads soldered to pads on the same side. They are typically smaller and better suited for high-density designs. Through-hole (THT) components have long leads that are inserted through holes in the PCB and soldered on the opposite side. They are generally larger and easier to hand-solder but require more PCB space.
4. How can I reduce electromagnetic interference (EMI) in my PCB design?
To reduce EMI in your PCB design, consider the following techniques:
- Use proper grounding and shielding
- Minimize loop areas in high-frequency signal paths
- Separate analog and digital grounds
- Use decoupling capacitors near ICs
- Incorporate EMI filters on power and signal lines
5. What is the typical turnaround time for PCB manufacturing?
The turnaround time for PCB manufacturing varies depending on the manufacturer, complexity of the design, and chosen shipping method. Typical turnaround times range from 24 hours to 2 weeks. Some manufacturers offer expedited services for an additional cost, which can reduce the turnaround time to a few days.
Conclusion
Designing and manufacturing your own PCBs can be a rewarding and educational experience. By following the steps outlined in this guide, you can start creating custom PCBs for your electronic projects. Remember to plan your design carefully, choose the right tools and components, and adhere to best practices for PCB layout and manufacturing. With practice and persistence, you’ll be able to create professional-quality PCBs and bring your electronic ideas to life.
Leave a Reply