What is a printed circuit board (PCB)?
A printed circuit board is a flat, insulating substrate made of fiberglass, composite epoxy, or other materials, with conductive copper traces printed onto its surface. These traces form the electrical connections between components, allowing for the creation of complex electronic circuits. PCBs are used in a wide range of applications, from consumer electronics to industrial equipment and aerospace technology.
Types of PCBs
There are several types of PCBs, each with its own unique characteristics and manufacturing processes:
Single-sided PCBs
Single-sided PCBs have conductive traces on only one side of the substrate. They are the simplest and most cost-effective type of PCB, suitable for basic electronic projects and low-density designs.
Double-sided PCBs
Double-sided PCBs have conductive traces on both sides of the substrate, allowing for more complex circuits and higher component density. The two sides are connected using through-hole vias, which are small holes drilled through the board and plated with conductive material.
Multi-layer PCBs
Multi-layer PCBs consist of multiple layers of conductive traces sandwiched between insulating layers. They offer the highest component density and are used in complex electronic devices, such as smartphones, computers, and medical equipment. Multi-layer PCBs can have anywhere from four to over twenty layers, depending on the complexity of the design.
Flexible PCBs
Flexible PCBs are made using a flexible substrate, such as polyimide, allowing the board to bend and conform to various shapes. They are often used in wearable electronics, medical devices, and applications where space is limited or flexibility is required.
PCB printing methods
There are several methods for printing PCBs, each with its own advantages and limitations. The choice of printing method depends on factors such as the complexity of the design, the desired production volume, and the available resources.
Traditional etching
Traditional etching is the most common method for producing PCBs. It involves the following steps:
- Designing the PCB layout using electronic design automation (EDA) software.
- Printing the design onto a transparent film or photomask.
- Coating the copper-clad substrate with a light-sensitive photoresist.
- Exposing the photoresist to UV light through the photomask, hardening the exposed areas.
- Developing the photoresist, removing the unexposed areas.
- Etching away the exposed copper using a chemical solution, leaving only the desired traces.
- Removing the remaining photoresist and applying a protective solder mask.
Traditional etching is suitable for both prototyping and high-volume production, but it requires specialized equipment and chemicals, and the process can be time-consuming.
Direct printing
Direct printing methods involve depositing conductive ink or toner directly onto the substrate, eliminating the need for etching. Some common direct printing methods include:
Inkjet printing
Inkjet printing uses specialized inkjet printers to deposit conductive ink onto the substrate. This method is suitable for low-volume production and rapid prototyping, as it allows for quick and easy design changes. However, the resolution and conductivity of inkjet-printed traces may be lower compared to other methods.
Screen printing
Screen printing involves forcing conductive ink through a fine mesh screen onto the substrate. This method is suitable for medium to high-volume production and can produce traces with good conductivity and resolution. However, it requires the creation of a separate screen for each layer of the PCB, which can be time-consuming and costly for complex designs.
Aerosol jet printing
Aerosol jet printing uses a high-precision nozzle to spray a fine mist of conductive ink onto the substrate. This method offers high resolution and can print on a variety of surfaces, including curved and uneven substrates. Aerosol jet printing is particularly useful for printing antennas, sensors, and other fine-feature components.
3D printing
3D printing is an emerging technology that allows for the creation of three-dimensional PCBs with embedded components. There are several 3D printing methods being explored for PCB fabrication, including:
Fused deposition modeling (FDM)
FDM 3D printers can be modified to print with conductive filaments, such as those containing copper or graphene. This method allows for the creation of simple, low-resolution PCBs, but the conductivity and reliability of the traces may be limited.
Stereolithography (SLA) and digital light processing (DLP)
SLA and DLP 3D printers use photopolymer resins that can be mixed with conductive materials, such as metal nanoparticles. These methods offer higher resolution and smoother surfaces compared to FDM, but the conductivity of the traces may still be lower than traditional PCBs.
Selective laser sintering (SLS)
SLS 3D printers use a laser to sinter powdered materials, such as metal or polymer powders, into solid structures. This method has the potential to create high-resolution, fully-functional PCBs with embedded components, but the technology is still in the research and development stage.
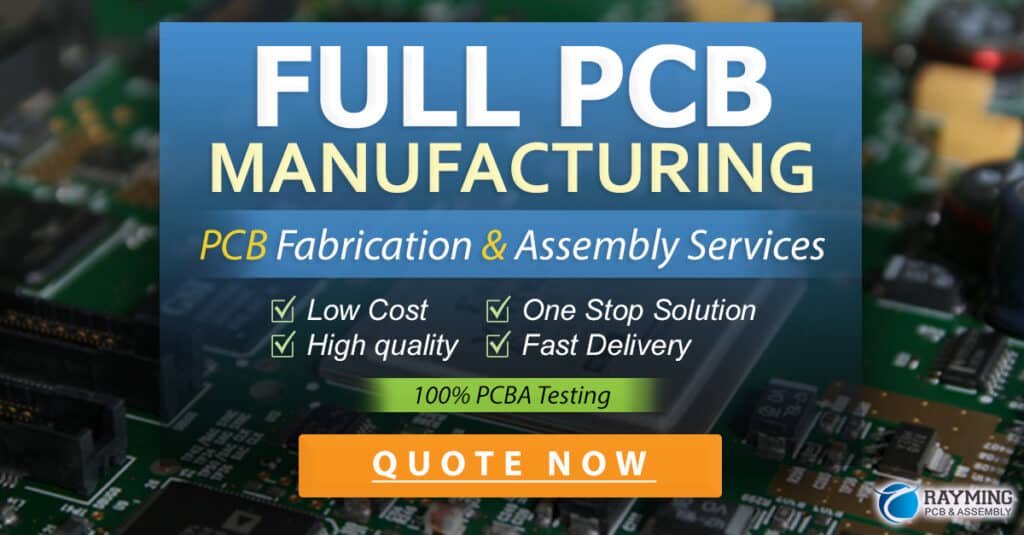
Materials for PCB printing
The choice of materials for PCB printing depends on the specific requirements of the application, such as the desired electrical properties, mechanical stability, and environmental resistance.
Substrates
The most common substrates for PCBs are:
- FR-4: A composite material made of fiberglass and epoxy resin, offering good mechanical and electrical properties, as well as resistance to heat and moisture.
- Polyimide: A flexible, heat-resistant polymer used for flexible PCBs and high-temperature applications.
- Aluminum: Used for metal-core PCBs, which offer excellent thermal dissipation for high-power applications.
- Ceramic: Used for high-frequency and high-temperature applications, offering low dielectric loss and good thermal stability.
Conductive materials
The most common conductive materials for PCB printing are:
- Copper: The standard choice for traditional PCBs, offering excellent electrical conductivity and solderability.
- Conductive inks: Used for direct printing methods, these inks typically contain metal nanoparticles (e.g., silver, gold, or copper) suspended in a polymer binder.
- Conductive filaments: Used for FDM 3D printing, these filaments are infused with conductive materials, such as copper or graphene.
Solder mask and silkscreen
After printing the conductive traces, a solder mask is applied to protect the traces from oxidation and prevent solder bridges during assembly. The solder mask is typically a green or other colored polymer coating that covers the entire PCB, except for the exposed pads where components will be soldered.
A silkscreen layer is then applied on top of the solder mask to add text, logos, and component identifiers. The silkscreen is typically white and helps with the assembly and troubleshooting of the PCB.
Designing for PCB printing
To ensure a successful PCB printing process, it’s essential to follow best practices and design guidelines:
- Use EDA software to create the PCB layout, ensuring proper trace width, spacing, and routing.
- Follow the design rules specified by the PCB manufacturer, such as minimum trace width, clearance, and hole size.
- Use standard component footprints and land patterns to ensure compatibility with automated assembly processes.
- Consider the specific requirements of the chosen printing method, such as the minimum feature size and the need for special coatings or treatments.
- Perform design rule checks (DRCs) and electrical rule checks (ERCs) to identify and correct any errors or potential issues.
- Create a comprehensive bill of materials (BOM) and assembly instructions to facilitate the manufacturing process.
Assembling and testing printed PCBs
After printing the PCB, the next steps are to assemble the components and test the board for proper functionality.
Assembly methods
There are two primary methods for assembling components onto a PCB:
-
Through-hole assembly (THA): Components with long leads are inserted through holes drilled in the PCB and soldered on the opposite side. This method is suitable for larger components and provides a strong mechanical connection, but it is slower and more labor-intensive than surface mount assembly.
-
Surface mount assembly (SMA): Components with small, flat leads are placed directly onto pads on the surface of the PCB and soldered in place. This method allows for higher component density, faster assembly, and better high-frequency performance, but it requires more precise placement and soldering techniques.
Soldering techniques
Soldering is the process of joining components to the PCB using a metal alloy (solder) that melts at a relatively low temperature. There are several soldering techniques used in PCB assembly:
-
Hand soldering: A soldering iron is used to manually apply heat and solder to individual components and pads. This method is suitable for low-volume production, prototyping, and rework, but it is slow and requires skilled operators.
-
Wave soldering: The PCB is passed over a molten solder wave, which selectively coats the exposed pads and through-holes. This method is suitable for high-volume production of through-hole components but is less suitable for surface mount components.
-
Reflow soldering: The PCB is coated with a solder paste (a mixture of powdered solder and flux) using a stencil or syringe, and then the components are placed onto the pads. The entire board is then heated in a reflow oven, melting the solder and bonding the components to the pads. This method is suitable for high-volume production of surface mount components.
Testing and quality control
After assembly, the PCB must be tested to ensure proper functionality and to identify any defects or issues. Some common testing methods include:
-
Visual inspection: The assembled PCB is visually checked for any obvious defects, such as missing or misaligned components, solder bridges, or damaged traces.
-
Automated optical inspection (AOI): An automated camera system scans the PCB and compares it to a reference image, identifying any deviations or defects.
-
In-circuit testing (ICT): The PCB is placed in a bed-of-nails fixture, which makes contact with specific test points on the board. Electrical tests are then performed to verify the presence, orientation, and functionality of each component.
-
Functional testing: The PCB is powered on and tested under real-world operating conditions to ensure that it performs as intended. This may involve running test software, measuring output signals, or simulating user interactions.
By implementing a comprehensive testing and quality control process, manufacturers can identify and correct defects early in the production cycle, reducing the risk of field failures and improving overall product quality.
Frequently Asked Questions (FAQ)
-
Q: What is the minimum trace width and spacing for a PCB?
A: The minimum trace width and spacing depend on the specific PCB manufacturing process and the design requirements. Typical values range from 0.1 mm to 0.25 mm for trace width and 0.1 mm to 0.2 mm for trace spacing, but smaller features are possible with advanced manufacturing techniques. -
Q: Can I print a PCB at home?
A: Yes, it is possible to print simple PCBs at home using methods like toner transfer or direct printing with conductive ink. However, the quality and reliability of home-printed PCBs may be lower compared to professionally manufactured boards, and the process can be time-consuming and require specialized materials. -
Q: What is the typical turnaround time for PCB printing?
A: The turnaround time for PCB printing varies depending on the complexity of the design, the chosen manufacturing process, and the production volume. For small-batch prototyping, turnaround times can range from a few days to a couple of weeks, while high-volume production may require several weeks or months. -
Q: How much does it cost to print a PCB?
A: The cost of printing a PCB depends on factors such as the board size, complexity, layer count, material choice, and production volume. Small, simple PCBs can cost a few dollars each, while complex, multi-layer boards can cost several hundred dollars or more per unit. Many PCB manufacturers offer online quoting tools to estimate the cost based on specific design requirements. -
Q: What are the environmental considerations for PCB printing?
A: Traditional PCB manufacturing processes can have significant environmental impacts, including the use of hazardous chemicals, the generation of waste materials, and the consumption of energy and water resources. To mitigate these impacts, many manufacturers are adopting eco-friendly practices, such as using lead-free solder, minimizing waste, and implementing closed-loop water treatment systems. Additionally, some newer PCB printing methods, such as 3D printing, may offer more sustainable alternatives by reducing material waste and enabling the use of biodegradable or recycled materials.
Conclusion
Printing PCBs is a complex process that involves a combination of design, materials, and manufacturing techniques. From traditional etching to advanced 3D printing methods, there are numerous options available for creating high-quality, reliable printed circuit boards. By understanding the various methods, materials, and design considerations involved in PCB printing, engineers and hobbyists can make informed decisions when developing and manufacturing electronic devices.
As technology continues to evolve, new PCB printing methods and materials are likely to emerge, offering even greater flexibility, efficiency, and sustainability in the production of electronic circuits. Staying up-to-date with these developments will be essential for anyone involved in the design and manufacture of PCBs, as well as for those seeking to push the boundaries of what is possible in the world of electronics.
Leave a Reply