Understanding the basics of PCB design
Before diving into the pcb design process, it is essential to understand the basics of PCB design. A PCB consists of the following components:
- Substrate: The base material that provides mechanical support and electrical insulation for the components and connections.
- Copper layers: Thin layers of copper foil laminated onto the substrate, which form the conductive pathways for electrical signals.
- Solder mask: A protective layer applied over the copper layers to prevent short circuits and provide insulation.
- Silkscreen: A printed layer on top of the solder mask that contains text and symbols for component identification and assembly instructions.
PCBs can be classified based on the number of copper layers:
PCB Type | Number of Copper Layers |
---|---|
Single-sided | 1 |
Double-sided | 2 |
Multi-layer | 3 or more |
Choosing the right pcb design software
To design your own PCB, you will need to use specialized PCB design software. There are several options available, ranging from free open-source tools to commercial software packages. Some popular PCB design software include:
- KiCad (free and open-source)
- Eagle (free for non-commercial use, paid versions available)
- Altium Designer (commercial)
- OrCAD (commercial)
When choosing a PCB design software, consider the following factors:
- Ease of use and learning curve
- Availability of component libraries and design templates
- Compatibility with your operating system
- Price and licensing options
Creating the schematic diagram
The first step in PCB design is to create a schematic diagram, which represents the electrical connections between components. A schematic diagram consists of symbols representing the components and lines representing the connections.
To create a schematic diagram:
- Open your chosen PCB design software and start a new project.
- Place the component symbols on the schematic canvas, using the software’s built-in libraries or creating custom symbols if necessary.
- Connect the components using wires or nets, following the desired electrical connections.
- Assign unique reference designators to each component (e.g., R1 for a resistor, C1 for a capacitor).
- Add power and ground symbols to the schematic, connecting them to the appropriate components.
- Verify the schematic for errors and inconsistencies, using the software’s built-in error checking tools.
Tips for creating a clear and accurate schematic:
- Use a consistent naming convention for components and nets
- Group related components together for better organization
- Add text labels and comments to clarify the purpose of each section
- Use hierarchical design techniques for complex schematics, breaking them down into smaller sub-circuits
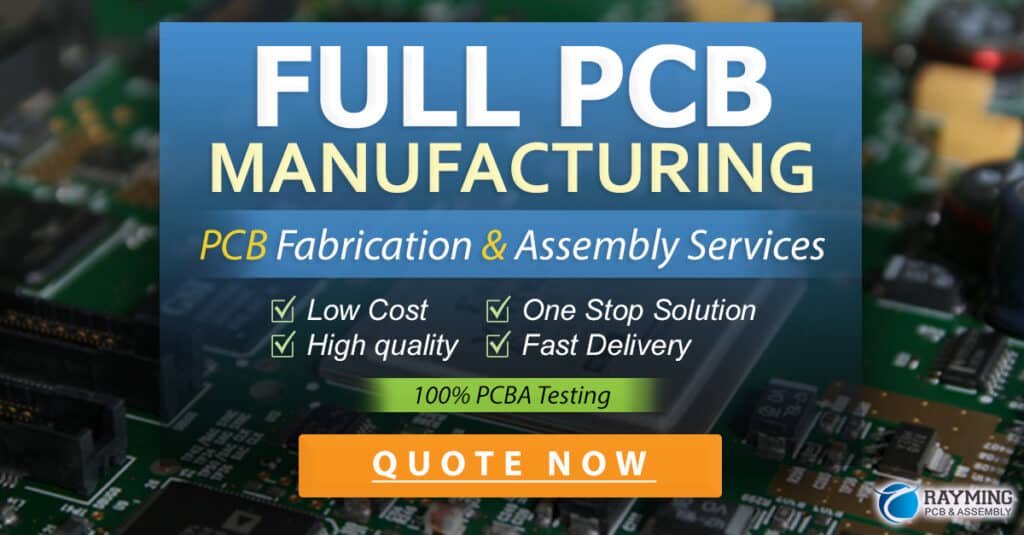
Designing the pcb layout
Once the schematic is complete, the next step is to design the physical layout of the PCB. The PCB layout determines the placement of components and the routing of the copper traces that connect them.
To design the PCB layout:
- Transfer the schematic to the PCB layout editor within your design software.
- Define the board outline and dimensions, considering the mechanical requirements of your project.
- Place the components on the board, following best practices for component placement (e.g., minimizing the distance between connected components, avoiding overlapping components).
- Route the copper traces between the components, following the electrical connections defined in the schematic.
- Apply the design rules specified by your pcb manufacturer, such as minimum trace width, clearance between traces, and hole sizes.
- Add copper pour (ground plane) to unused areas of the board to improve signal integrity and EMI performance.
- Generate the Gerber files, which are the standard file format for PCB manufacturing.
Best practices for PCB layout design:
- Keep the layout compact to minimize board size and cost
- Avoid sharp angles in traces to reduce signal reflections
- Use via stitching to connect ground planes on different layers
- Provide adequate clearance between components and the board edge
- Follow the manufacturer’s guidelines for trace width and spacing based on the desired current carrying capacity and voltage rating
Selecting the PCB manufacturing specifications
Before sending your PCB design for manufacturing, you need to specify the following parameters:
- Board thickness: Typically 0.8mm to 1.6mm for standard PCBs
- Copper weight: Expressed in ounces per square foot (oz/ft²), commonly 1oz or 2oz
- Solder mask color: Green, red, blue, or black
- Silkscreen color: White or black
- Surface finish: HASL (Hot Air Solder Leveling), ENIG (Electroless Nickel Immersion Gold), or others
- Minimum hole size: Dependent on the components and manufacturing capabilities
Factors to consider when choosing a PCB manufacturer:
- Manufacturing capabilities and quality standards
- Turnaround time and shipping options
- Pricing and minimum order quantities
- Customer support and communication
Testing and prototyping
After receiving the manufactured PCBs, it is essential to test and prototype your design before moving to mass production. Testing and prototyping help identify any issues with the PCB design or component selections.
To test and prototype your PCB:
- Visually inspect the PCBs for any manufacturing defects, such as missing or incorrect holes, damaged traces, or poor solder mask coverage.
- Assemble the components onto the PCB, either manually or using pick-and-place machines for surface-mount components.
- Perform a continuity test to verify that all the connections are correct and there are no short circuits.
- Power on the PCB and test its functionality, using appropriate test equipment such as oscilloscopes, multimeters, or logic analyzers.
- Debug any issues found during testing, making necessary revisions to the schematic or layout.
Tips for successful testing and prototyping:
- Start with a small batch of PCBs for initial testing
- Use DFM (Design for Manufacturability) techniques to minimize the risk of manufacturing defects
- Document the testing process and results for future reference
- Seek feedback from users or experts to identify potential improvements
Frequently Asked Questions (FAQ)
- What is the difference between a breadboard and a PCB?
-
A breadboard is a reusable prototyping board that allows you to quickly build and test circuits without soldering. PCBs are custom-designed boards that provide a permanent and reliable solution for your electronic projects.
-
Can I design a PCB without using specialized software?
-
While it is theoretically possible to design a PCB manually, using specialized PCB design software is highly recommended. These tools provide a more efficient and accurate way to create schematics and layouts, and they help ensure that your design meets manufacturing requirements.
-
How much does it cost to manufacture a custom pcb?
-
The cost of manufacturing a custom PCB depends on various factors, such as the board size, number of layers, quantity, and the manufacturer you choose. Small, simple PCBs can cost a few dollars each, while larger, more complex boards can cost several hundred dollars. Many PCB manufacturers offer online quoting tools to help estimate the cost of your project.
-
What are the most common mistakes in PCB design?
-
Some of the most common mistakes in PCB design include:
- Incorrect component footprints or pinouts
- Insufficient clearance between components or traces
- Incorrect trace width or spacing for the desired current and voltage ratings
- Lack of proper grounding or power distribution
- Failure to follow the manufacturer’s design guidelines
-
How long does it take to design and manufacture a custom PCB?
- The time required to design and manufacture a custom PCB varies depending on the complexity of the design and the chosen manufacturer. Simple designs can be completed in a few hours, while more complex projects may take several days or weeks. Manufacturing lead times typically range from a few days to several weeks, depending on the PCB specifications and the manufacturer’s workload.
Conclusion
Designing your own PCB can be a challenging but rewarding experience. By following the steps outlined in this article, you can create custom PCBs that meet your specific requirements and bring your electronic projects to life. Remember to start with a clear schematic, follow best practices for PCB layout design, and thoroughly test your prototypes before moving to mass production. With practice and persistence, you can become proficient in PCB design and unleash your creativity in the world of electronics.
Leave a Reply