Introduction to PCB sensor placement
Printed Circuit Boards (PCBs) are essential components in modern electronic devices. They provide a platform for mounting and interconnecting various electronic components, including sensors. Proper placement of sensors on a PCB is crucial for ensuring optimal performance, reliability, and functionality of the device. In this article, we will explore the key considerations and best practices for PCB sensor placement.
Understanding the Types of Sensors
Before diving into sensor placement, it’s important to understand the different types of sensors commonly used in PCBs. Some popular sensor categories include:
- Temperature sensors
- Thermistors
- Thermocouples
- RTDs (Resistance Temperature Detectors)
- Pressure sensors
- Piezoresistive sensors
- Capacitive sensors
- Optical sensors
- Photodiodes
- Phototransistors
- Light-dependent resistors (LDRs)
- Humidity sensors
- Capacitive humidity sensors
- Resistive humidity sensors
- Motion sensors
- Accelerometers
- Gyroscopes
- Inertial Measurement Units (IMUs)
Each type of sensor has its own characteristics, requirements, and considerations for placement on a PCB.
Factors Influencing Sensor Placement
When determining the optimal placement for a sensor on a PCB, several factors need to be taken into account:
1. Sensitivity and Accuracy
The sensitivity and accuracy of a sensor are crucial factors to consider when deciding on its placement. Sensors should be placed in locations where they can effectively measure the desired parameter without interference or disturbance from other components or environmental factors.
For example, a temperature sensor should be placed away from heat-generating components like power regulators or processors to avoid inaccurate readings. Similarly, a motion sensor should be placed in a location where it can accurately detect the desired motion without being affected by vibrations from other sources.
2. Signal Integrity
Maintaining signal integrity is essential for ensuring accurate and reliable sensor readings. Sensors generate analog signals that are susceptible to noise, interference, and signal degradation. Proper placement of sensors can help minimize these issues.
When placing sensors on a PCB, consider the following signal integrity aspects:
- Keep sensor traces as short as possible to reduce the likelihood of noise pickup and signal attenuation.
- Route sensor traces away from high-frequency signals or power traces to avoid electromagnetic interference (EMI).
- Use proper grounding techniques, such as a dedicated ground plane or star grounding, to provide a low-impedance return path for the sensor signals.
- Implement appropriate filtering and shielding measures, such as decoupling capacitors or EMI shields, to reduce noise and interference.
3. Mechanical Considerations
The mechanical aspects of sensor placement are equally important. Sensors should be placed in locations that are mechanically stable and protected from physical damage or stress.
Consider the following mechanical factors:
- Ensure that the sensor is securely mounted to the PCB to prevent movement or vibration that could affect its performance.
- Provide adequate clearance around the sensor for proper airflow and heat dissipation, especially for temperature-sensitive sensors.
- Consider the orientation of the sensor relative to the PCB and the device housing to ensure proper alignment and avoid physical obstructions.
- Protect sensors from environmental factors like moisture, dust, or extreme temperatures by using appropriate enclosures or protective coatings.
4. Accessibility and Maintenance
Accessibility and ease of maintenance should also be considered when placing sensors on a PCB. Sensors may require periodic calibration, replacement, or servicing, so their placement should facilitate easy access.
Consider the following accessibility aspects:
- Place sensors in locations that are easily accessible for calibration or replacement without requiring extensive disassembly of the device.
- Provide clear markings or labels to identify the sensor locations and orientations for easy identification during maintenance.
- Consider using connectors or sockets for sensors that may need frequent replacement, allowing for quick and hassle-free swapping.
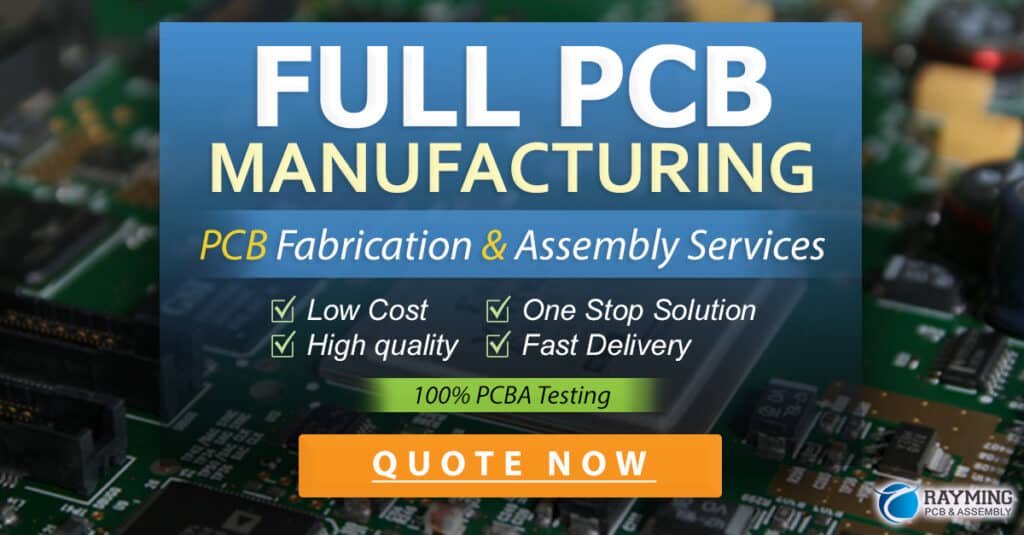
Best Practices for PCB Sensor Placement
Now that we have discussed the factors influencing sensor placement, let’s explore some best practices to ensure optimal performance and reliability:
1. Proximity to Relevant Components
Place sensors in close proximity to the components or areas they are intended to measure. This minimizes the distance the sensor signal needs to travel, reducing the likelihood of noise pickup and signal degradation.
For example, a temperature sensor should be placed close to the component it is monitoring, such as a power transistor or a CPU. Similarly, a pressure sensor should be placed near the point of pressure measurement for accurate readings.
2. Isolation and Shielding
Isolate sensors from potential sources of interference, such as high-frequency digital signals or power circuits. Use appropriate shielding techniques to protect sensors from electromagnetic interference (EMI) and radio frequency interference (RFI).
Some effective isolation and shielding methods include:
- Using ground planes or guard rings around sensor traces to provide a barrier against interference.
- Placing sensors in shielded enclosures or using shielded cables for sensor connections.
- Implementing filters, such as low-pass filters or ferrite beads, to suppress high-frequency noise.
3. Thermal Management
Consider the thermal characteristics of the sensor and its surrounding components when determining placement. Some sensors, like temperature sensors, are sensitive to thermal gradients and heat generation from nearby components.
To ensure accurate temperature measurements:
- Place temperature sensors away from heat-generating components or provide adequate thermal isolation.
- Use thermal vias or heat sinks to dissipate heat away from the sensor area.
- Consider the airflow and cooling mechanisms in the device to ensure proper heat dissipation.
4. Mechanical Stability
Ensure that sensors are placed in mechanically stable locations to minimize the impact of vibrations, shocks, or physical stresses. Use appropriate mounting techniques to securely attach sensors to the PCB.
Some mechanical stability considerations include:
- Using through-hole mounting or surface mount pads with sufficient size and spacing for reliable soldering.
- Providing strain relief for sensor connections to prevent damage due to mechanical stress.
- Using flexible or conformal coatings to protect sensors from vibrations or physical damage.
5. Sensor Orientation
Pay attention to the orientation of sensors when placing them on the PCB. Some sensors, such as accelerometers or gyroscopes, are sensitive to orientation and require specific alignment for accurate measurements.
Follow the manufacturer’s guidelines for sensor orientation and consider the following:
- Align sensors with the desired axes of measurement.
- Ensure that the sensor orientation is consistent with the PCB and device housing.
- Use clear markings or indicators to identify the correct orientation during assembly.
6. Testing and Validation
Conduct thorough testing and validation of sensor placement to ensure optimal performance and reliability. Perform both functional and environmental tests to validate the sensor’s accuracy, stability, and robustness.
Some testing considerations include:
- Verifying sensor accuracy and calibration across the desired measurement range.
- Conducting temperature and humidity cycling tests to assess sensor performance under varying environmental conditions.
- Performing vibration and shock tests to ensure mechanical stability and reliability.
- Validating sensor performance in the final device housing and under real-world operating conditions.
PCB Layout Techniques for Sensor Placement
Proper PCB layout techniques can greatly enhance the performance and reliability of sensors. Here are some layout considerations for sensor placement:
1. Component Placement
When placing sensors on the PCB, consider the overall component placement and routing. Follow these guidelines:
- Place sensors as close as possible to the associated signal conditioning circuitry to minimize trace lengths and noise pickup.
- Keep sensor traces away from high-frequency digital signals or power traces to avoid interference.
- Provide adequate spacing between sensors and other components to avoid physical obstruction or thermal interference.
2. Trace Routing
Trace routing plays a crucial role in maintaining signal integrity for sensor signals. Follow these best practices:
- Keep sensor traces as short and direct as possible to minimize signal attenuation and noise pickup.
- Use controlled impedance traces for high-frequency sensor signals to maintain signal integrity.
- Route sensor traces on dedicated layers, preferably away from power and digital signal layers.
- Avoid routing sensor traces near the edges of the PCB to reduce the risk of electromagnetic interference (EMI).
3. Grounding and Shielding
Proper grounding and shielding techniques are essential for minimizing noise and interference in sensor circuits. Consider the following:
- Use a solid ground plane to provide a low-impedance return path for sensor signals.
- Implement guard rings or shielding around sensitive sensor traces to isolate them from interference.
- Use dedicated ground planes for analog and digital sections of the PCB to avoid ground loops and noise coupling.
- Provide adequate grounding and shielding for sensor connectors and cables to prevent external interference.
4. Power Supply Decoupling
Sensors often require clean and stable power supplies for accurate and reliable operation. Implement proper power supply decoupling techniques:
- Place decoupling capacitors close to the sensor’s power pins to minimize power supply noise.
- Use separate power supply lines for analog and digital sections of the sensor circuitry to avoid noise coupling.
- Implement voltage regulators or low-dropout regulators (LDOs) to provide stable and clean power to the sensors.
5. PCB Stack-up
The PCB stack-up can also impact sensor performance. Consider the following:
- Use dedicated layers for sensor signals to minimize crosstalk and interference from other layers.
- Provide sufficient spacing between sensor layers and power or digital layers to reduce capacitive coupling.
- Use ground planes or power planes as shielding layers between sensitive sensor layers.
Sensor Placement Examples
To illustrate the concepts discussed, let’s explore a few examples of sensor placement on PCBs:
Example 1: Temperature Sensor Placement
When placing a temperature sensor on a PCB to monitor the temperature of a power transistor, consider the following:
- Place the temperature sensor as close as possible to the power transistor to accurately measure its temperature.
- Use a thermal pad or thermal vias to provide a good thermal connection between the sensor and the transistor.
- Route the sensor traces away from high-current paths or heat-generating components to avoid thermal interference.
- Provide adequate airflow and cooling in the surrounding area to ensure accurate temperature measurements.
Example 2: Accelerometer Placement
When placing an accelerometer on a PCB for motion sensing applications, consider the following:
- Orient the accelerometer correctly based on the desired axes of measurement.
- Place the accelerometer near the center of mass of the PCB to minimize the impact of rotational effects.
- Use a mechanically stable mounting method, such as a rigid connector or a surface mount pad, to prevent vibrations or movements.
- Route the accelerometer traces away from high-frequency signals or power traces to avoid interference.
Example 3: Optical Sensor Placement
When placing an optical sensor, such as a photodiode or a phototransistor, on a PCB, consider the following:
- Position the optical sensor in a location that allows for clear and unobstructed exposure to the desired light source.
- Provide adequate shielding or filtering to block unwanted light or infrared interference.
- Route the sensor traces away from high-frequency signals or power traces to avoid electromagnetic interference.
- Consider the optical properties of the PCB material and any protective coatings that may affect the sensor’s performance.
Conclusion
Proper placement of sensors on a PCB is crucial for ensuring optimal performance, reliability, and functionality of the device. By considering factors such as sensitivity, signal integrity, mechanical stability, accessibility, and best practices for PCB layout, designers can effectively integrate sensors into their PCB designs.
Remember to follow guidelines for component placement, trace routing, grounding and shielding, power supply decoupling, and PCB stack-up to minimize noise, interference, and signal degradation. Conducting thorough testing and validation of sensor placement is also essential to ensure the desired performance and reliability.
By understanding the specific requirements and characteristics of different types of sensors and applying the principles discussed in this article, designers can make informed decisions when placing sensors on their PCBs, leading to successful and reliable sensor integration in electronic devices.
Frequently Asked Questions (FAQ)
- Q: What are the main factors to consider when placing sensors on a PCB?
A: The main factors to consider when placing sensors on a PCB include sensitivity and accuracy, signal integrity, mechanical stability, accessibility, and thermal management. It’s important to take into account the specific requirements and characteristics of the sensor type and the application. - Q: How can I minimize noise and interference in sensor circuits?
A: To minimize noise and interference in sensor circuits, you can follow best practices such as keeping sensor traces short and away from high-frequency signals, using dedicated ground planes and shielding, implementing proper power supply decoupling, and using appropriate filters and isolation techniques. - Q: What are some common types of sensors used in PCBs?
A: Common types of sensors used in PCBs include temperature sensors (thermistors, thermocouples, RTDs), pressure sensors (piezoresistive, capacitive), optical sensors (photodiodes, phototransistors), humidity sensors (capacitive, resistive), and motion sensors (accelerometers, gyroscopes, IMUs). - Q: How do I ensure accurate temperature measurements when placing a temperature sensor on a PCB?
A: To ensure accurate temperature measurements, place the temperature sensor close to the component being monitored, use thermal pads or vias for good thermal connection, route sensor traces away from heat-generating components, and provide adequate airflow and cooling in the surrounding area. - Q: What are some mechanical considerations when placing sensors on a PCB?
A: Mechanical considerations when placing sensors on a PCB include ensuring secure mounting to prevent movement or vibration, providing adequate clearance for airflow and heat dissipation, considering the orientation relative to the PCB and device housing, and protecting sensors from environmental factors like moisture or physical damage.
Sensor Type | Placement Considerations | Best Practices |
---|---|---|
Temperature Sensor | – Proximity to monitored component – Thermal isolation from heat-generating components – Adequate airflow and cooling |
– Use thermal pads or vias for good thermal connection – Route sensor traces away from high-current paths – Provide proper heat dissipation |
Pressure Sensor | – Close to the point of pressure measurement – Mechanical stability and protection – Isolation from vibrations and physical stress |
– Use robust mounting methods – Implement strain relief for sensor connections – Consider the sensor’s sensitivity and pressure range |
Optical Sensor | – Clear and unobstructed exposure to light source – Shielding from unwanted light or infrared interference – Consideration of PCB material and coatings |
– Position sensor for optimal light reception – Use filters or shields to block unwanted light – Route traces away from high-frequency signals |
Humidity Sensor | – Placement in areas with representative humidity – Protection from condensation and moisture – Isolation from heat sources and air currents |
– Use protective coatings or enclosures – Provide adequate ventilation – Consider the sensor’s response time and accuracy |
Motion Sensor | – Orientation based on desired axes of measurement – Placement near the center of mass – Mechanical stability and vibration isolation |
– Use stable mounting methods – Route traces away from high-frequency signals – Consider the sensor’s sensitivity and measurement range |
Leave a Reply