What is point by point soldering?
Point by point soldering, also known as touch soldering, is a technique where the soldering iron tip is used to heat both the component lead and the pad on the printed circuit board (PCB) simultaneously. The solder is then applied to the joint, creating a connection between the component and the board.
Advantages of point by point soldering
- Precise control over the soldering process
- Suitable for small-scale production or prototyping
- Requires minimal equipment (soldering iron, solder, and a steady hand)
- Ideal for soldering through-hole components
Disadvantages of point by point soldering
- Time-consuming for large-scale production
- Requires a skilled operator to ensure consistent results
- Not suitable for surface mount components
What is mini-wave soldering?
Mini-wave soldering is a technique that uses a small wave of molten solder to create connections between components and the PCB. The board is passed over a mini-wave fountain, which applies solder to the bottom side of the board, creating a connection between the component leads and the pads.
Advantages of mini-wave soldering
- Faster than point by point soldering for larger production runs
- Consistent results, as the process is automated
- Suitable for both through-hole and surface mount components
- Reduces the risk of human error
Disadvantages of mini-wave soldering
- Requires specialized equipment (mini-wave soldering machine)
- Higher initial investment compared to point by point soldering
- Not ideal for prototyping or small-scale production
Comparison of point by point and mini-wave soldering techniques
Characteristic | Point by Point Soldering | Mini-Wave Soldering |
---|---|---|
Speed | Slow | Fast |
Consistency | Operator-dependent | Automated |
Equipment | Minimal | Specialized |
Component Type | Through-hole | Through-hole and SMD |
Production Scale | Small | Large |
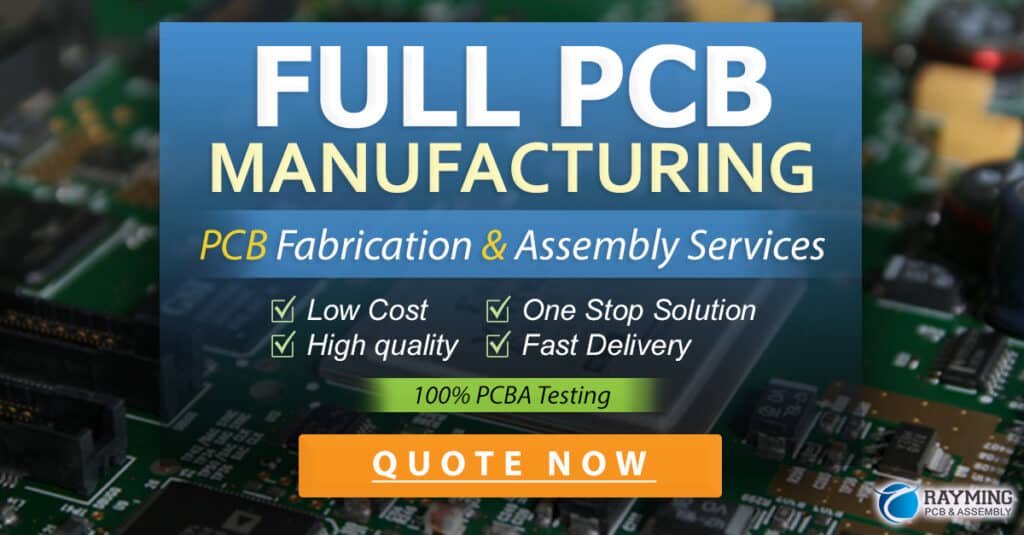
FAQ
1. What is the best soldering technique for beginners?
For beginners, point by point soldering is often the best technique to start with. It requires minimal equipment and allows for precise control over the soldering process, making it easier to learn the basics of soldering.
2. Can I use mini-wave soldering for prototyping?
While mini-wave soldering can be used for prototyping, it’s not the most efficient method. Point by point soldering is better suited for prototyping and small-scale production, as it allows for more flexibility and requires less specialized equipment.
3. What type of components can be soldered using mini-wave soldering?
Mini-wave soldering can be used for both through-hole and surface mount components. The small wave of molten solder can effectively create connections between the component leads and the pads on the PCB.
4. How can I ensure consistent results with point by point soldering?
To ensure consistent results with point by point soldering, it’s essential to have a skilled operator with a steady hand. Proper training and practice can help improve consistency and reduce the risk of errors.
5. Is mini-wave soldering more expensive than point by point soldering?
Initially, mini-wave soldering requires a higher investment due to the specialized equipment needed. However, for larger production runs, mini-wave soldering can be more cost-effective in the long run, as it is faster and more consistent than point by point soldering.
Conclusion
Both point by point and mini-wave soldering techniques have their advantages and disadvantages. The choice between the two depends on factors such as production scale, component type, and available resources. For small-scale production and prototyping, point by point soldering is often the preferred method, while mini-wave soldering is better suited for larger production runs and applications involving both through-hole and surface mount components.
Regardless of the technique chosen, proper training and practice are essential for achieving consistent, high-quality solder joints. By understanding the strengths and limitations of each technique, electronics professionals can make informed decisions and optimize their soldering processes for the best possible results.
Leave a Reply