Introduction to Gold-Plating Connectors
Gold plating is a widely used technique in the electronics industry for enhancing the performance and durability of electrical connectors, particularly edge connectors. Edge connectors are commonly found in various electronic devices, such as printed circuit boards (PCBs), computer peripherals, and consumer electronics. The primary purpose of gold plating on these connectors is to ensure reliable electrical contact, prevent corrosion, and extend the lifespan of the device.
In this article, we will explore the fundamentals of gold plating for edge connectors, including the benefits, processes, and considerations involved in gold-plating connectors. We will also discuss the various applications of Gold-Plated Edge Connectors and their importance in the electronics industry.
Benefits of Gold Plating Edge Connectors
Gold plating offers several key benefits when applied to edge connectors:
-
Excellent Conductivity: Gold is an exceptional conductor of electricity, ensuring minimal resistance and optimal signal transmission between the connector and the mating surface.
-
Corrosion Resistance: Gold is highly resistant to corrosion, even in harsh environments. This property helps maintain the integrity of the electrical connection over time, preventing signal degradation or failure due to corrosion.
-
Low Contact Resistance: Gold-Plated Connectors exhibit low contact resistance, which is essential for maintaining signal integrity and minimizing power loss.
-
Durability: Gold plating enhances the durability of edge connectors by providing a hard, wear-resistant surface that can withstand repeated insertion and removal cycles.
-
Improved Solderability: Gold-plated contacts are easier to solder compared to bare metal surfaces, as the gold layer prevents oxidation and ensures a reliable solder joint.
Gold Plating Processes for Edge Connectors
There are several methods used for gold plating edge connectors, each with its own advantages and limitations. The choice of the plating process depends on factors such as the substrate material, desired thickness, and production volume.
Electroplating
Electroplating is the most common method for gold plating edge connectors. In this process, the connector is submerged in a gold plating solution, and an electric current is applied to deposit a layer of gold onto the surface. The thickness of the gold layer can be precisely controlled by adjusting the current density and plating time.
Advantages of electroplating include:
– Uniform thickness distribution
– High deposition rates
– Suitable for large-scale production
Limitations of electroplating:
– Requires a conductive substrate
– May require pre-treatment steps for certain materials
Electroless Plating
Electroless plating is a chemical deposition process that does not require an external electric current. Instead, the gold layer is deposited through an autocatalytic reaction between the plating solution and the substrate surface. This method is suitable for plating non-conductive substrates or complex geometries.
Advantages of electroless plating:
– Can plate non-conductive substrates
– Uniform coverage, even on complex shapes
– No electrical contact required
Limitations of electroless plating:
– Slower deposition rates compared to electroplating
– Limited thickness control
Immersion Plating
Immersion plating is a simple and cost-effective method for depositing a thin layer of gold onto edge connectors. In this process, the connector is immersed in a gold plating solution, and the gold ions in the solution displace the surface atoms of the substrate, forming a thin gold layer.
Advantages of immersion plating:
– Simple and cost-effective
– Suitable for small-scale production or prototyping
– Can plate non-conductive substrates
Limitations of immersion plating:
– Limited thickness control
– Thin gold layers (typically < 0.1 μm)
– May not provide sufficient wear resistance for high-cycles applications
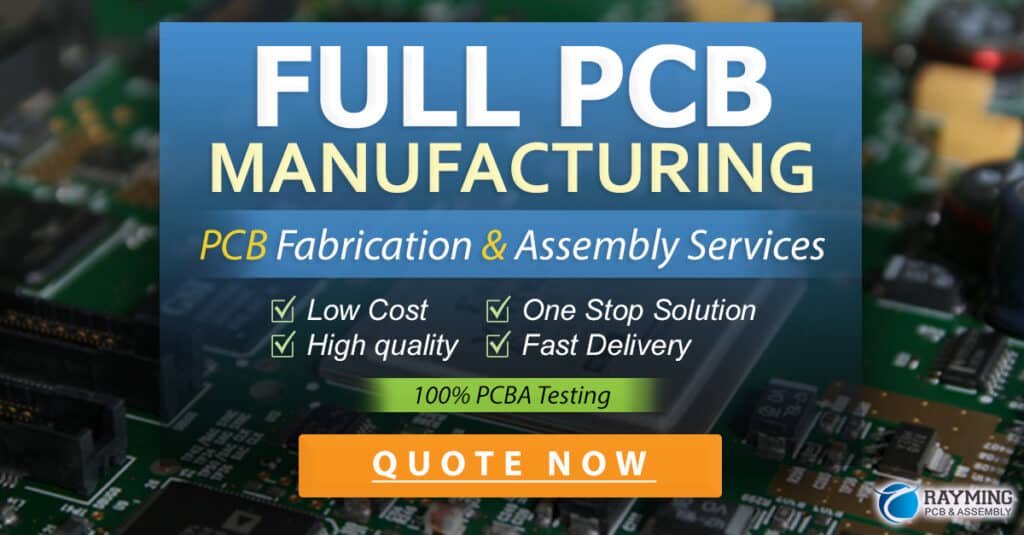
Considerations for Gold Plating Edge Connectors
When implementing gold plating for edge connectors, several factors must be considered to ensure optimal performance and reliability:
-
Gold Purity: The purity of the gold used for plating can impact the electrical and mechanical properties of the connector. High-purity gold (99.9% or higher) is often preferred for critical applications.
-
Gold Thickness: The thickness of the gold layer should be carefully selected based on the application requirements. Thicker gold layers offer better wear resistance and durability but may increase costs. Typical gold thicknesses range from 0.1 μm to 2 μm.
-
Underplating: In some cases, an underplating layer (e.g., nickel) is used to improve adhesion between the gold layer and the substrate, as well as to act as a diffusion barrier.
-
Substrate Material: The choice of substrate material can affect the adhesion and performance of the gold plating. Common substrate materials for edge connectors include copper alloys, stainless steel, and phosphor bronze.
-
Mating Cycles: The expected number of mating cycles (insertions and removals) should be considered when selecting the gold thickness and plating process. Higher mating cycles may require thicker gold layers or harder gold alloys.
-
Environmental Factors: The operating environment of the connector should be taken into account when specifying the gold plating. Harsh environments, such as those with high humidity or corrosive gases, may require additional protection.
Applications of Gold-Plated Edge Connectors
Gold-plated edge connectors find applications in various industries and devices, including:
-
Consumer Electronics: Gold-plated connectors are commonly used in smartphones, tablets, laptops, and other consumer electronic devices to ensure reliable electrical connections and long-term durability.
-
Automotive Electronics: In the automotive industry, gold-plated edge connectors are used in electronic control units (ECUs), sensors, and other critical systems that require high reliability and resistance to harsh environments.
-
Medical Devices: Gold plating is essential for edge connectors in medical devices, such as patient monitors, diagnostic equipment, and implantable devices, where reliable electrical connections are crucial for patient safety and device performance.
-
Industrial Equipment: Industrial applications, such as process control systems, automation equipment, and test and measurement devices, rely on gold-plated edge connectors for robust and reliable electrical interfaces.
-
Aerospace and Defense: Gold-plated connectors are used in aerospace and defense applications, where high reliability, durability, and resistance to extreme environmental conditions are paramount.
Frequently Asked Questions (FAQ)
-
Q: Why is gold preferred for plating edge connectors?
A: Gold is preferred for plating edge connectors due to its excellent electrical conductivity, corrosion resistance, low contact resistance, and durability. These properties ensure reliable electrical connections and long-term performance. -
Q: What is the typical thickness of gold plating on edge connectors?
A: The typical thickness of gold plating on edge connectors ranges from 0.1 μm to 2 μm, depending on the application requirements, expected mating cycles, and environmental factors. -
Q: Can gold plating be applied to non-conductive substrates?
A: Yes, gold plating can be applied to non-conductive substrates using electroless plating or immersion plating processes. These methods do not require an external electric current and can deposit gold onto non-conductive surfaces. -
Q: How does gold plating affect the solderability of edge connectors?
A: Gold plating improves the solderability of edge connectors by preventing oxidation and ensuring a reliable solder joint. The gold layer protects the underlying metal from oxidation and provides a wettable surface for solder to adhere to. -
Q: What factors should be considered when specifying gold plating for edge connectors?
A: When specifying gold plating for edge connectors, factors such as gold purity, thickness, underplating, substrate material, mating cycles, and environmental conditions should be considered. These factors influence the performance, reliability, and cost of the gold-plated connectors.
Conclusion
Gold plating is a critical process for enhancing the performance and reliability of edge connectors in various electronic applications. The benefits of gold plating, such as excellent conductivity, corrosion resistance, low contact resistance, and durability, make it an ideal choice for ensuring reliable electrical connections in demanding environments.
When implementing gold plating for edge connectors, it is essential to consider factors such as the plating process, gold purity, thickness, underplating, substrate material, mating cycles, and environmental conditions. By carefully selecting the appropriate gold plating specifications, manufacturers can optimize the performance and longevity of their electronic devices.
As the electronics industry continues to evolve, with increasing demands for miniaturization, high-speed data transmission, and reliability, the importance of gold-plated edge connectors will only continue to grow. By understanding the fundamentals and best practices of gold plating for edge connectors, engineers and manufacturers can design and produce electronic devices that meet the ever-increasing performance and reliability requirements of today’s market.
Leave a Reply