What is FR4?
FR4 (Flame Retardant 4) is a composite material composed of woven fiberglass cloth impregnated with an epoxy resin binder. The “FR” designation indicates that the material is flame retardant, while the “4” refers to the specific grade of the material. FR4 is known for its high strength-to-weight ratio, excellent electrical insulation properties, and good resistance to moisture and chemicals.
Composition of FR4
The typical composition of FR4 is as follows:
Component | Percentage |
---|---|
Epoxy Resin | 40-60% |
Glass Fiber | 40-60% |
Brominated Flame Retardant | 10-20% |
Other Additives | <1% |
The exact composition may vary depending on the manufacturer and the specific requirements of the application.
Key Properties of FR4
To understand the importance of FR4 Quality, it is essential to know the key properties that make this material suitable for PCB manufacturing.
Mechanical Properties
FR4 exhibits excellent mechanical properties, which are crucial for the structural integrity of the PCB. Some of the important mechanical properties include:
- High flexural strength
- Good impact resistance
- Low coefficient of thermal expansion (CTE)
- Excellent dimensional stability
These properties ensure that the PCB can withstand the stresses encountered during manufacturing, assembly, and operation.
Electrical Properties
As a PCB substrate, FR4 must provide excellent electrical insulation to prevent short circuits and signal interference. The key electrical properties of FR4 include:
- High dielectric strength
- Low dielectric constant (Dk)
- Low dissipation factor (Df)
- Good insulation resistance
These properties allow for reliable signal transmission and minimize signal loss, which is essential for high-speed and high-frequency applications.
Thermal Properties
FR4 also exhibits good thermal properties, which are important for managing heat dissipation in the PCB. The main thermal properties of FR4 include:
- Good thermal conductivity
- High glass transition temperature (Tg)
- Flame retardancy
These properties help to prevent thermal damage to the PCB and ensure reliable operation under various temperature conditions.
FR4 Quality Standards
To ensure consistent quality and performance, FR4 materials are manufactured according to various industry standards. Some of the most common standards include:
- IPC-4101: Specification for Base Materials for Rigid and Multilayer Printed Boards
- NEMA LI 1: Industrial Laminated Thermosetting Products
- MIL-I-24768: Insulation Material, Plastic, Laminated, Metal-Clad
- UL 94: Standard for Safety of Flammability of Plastic Materials
These standards specify the requirements for physical, mechanical, electrical, and thermal properties of FR4 materials, as well as the testing methods for verifying compliance.
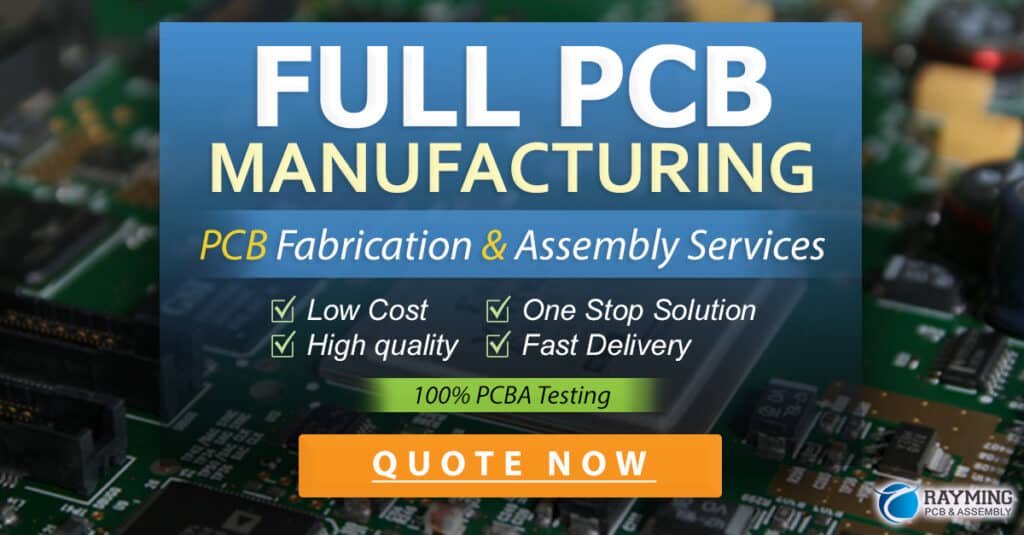
Factors Affecting FR4 Quality
Several factors can impact the quality of FR4 materials, which in turn affect the performance and reliability of the PCB. Some of the key factors include:
Raw Material Quality
The quality of the raw materials used in FR4 production, such as glass fibers and epoxy resins, directly influences the final properties of the laminate. Inconsistencies in raw material quality can lead to variations in mechanical strength, electrical insulation, and thermal stability.
Manufacturing Process
The manufacturing process of FR4 laminates involves several steps, including impregnation, layup, pressing, and curing. Any deviations or inconsistencies in these processes can result in defects or variations in the final product quality. Strict process control and monitoring are essential to maintain consistent FR4 quality.
Storage and Handling
Improper storage and handling of FR4 laminates can also affect their quality. Exposure to moisture, extreme temperatures, or chemical contaminants can degrade the material properties and lead to issues during PCB manufacturing. Proper storage conditions and handling procedures must be followed to maintain FR4 quality.
Impact of FR4 Quality on PCB Manufacturing
FR4 quality has a significant impact on the PCB manufacturing process and the final product performance. Poor FR4 quality can lead to various manufacturing defects and reliability issues.
Common Manufacturing Defects
Some of the common manufacturing defects associated with poor FR4 quality include:
- Delamination: Separation of the glass fiber layers from the epoxy resin, causing structural weakness and signal integrity issues.
- Warpage: Uneven shrinkage or expansion of the laminate, resulting in dimensional instability and assembly challenges.
- Voids: Air pockets or gaps within the laminate, which can cause signal interruption and reduce mechanical strength.
- Resin starvation: Insufficient resin flow, leading to poor bonding between layers and reduced insulation properties.
These defects can lead to reduced yield, increased manufacturing costs, and potential reliability issues in the final product.
Reliability Concerns
Poor FR4 quality can also impact the long-term reliability of the PCB. Some of the potential reliability issues include:
- Thermal cycling failures: Inconsistent CTE of the laminate can cause stress and cracking during temperature fluctuations.
- Moisture absorption: Excessive moisture uptake can degrade the electrical and mechanical properties of the PCB over time.
- Delamination under stress: Weak bonding between layers can lead to delamination under mechanical or thermal stress.
- Signal integrity issues: Variations in dielectric properties can cause signal distortion, crosstalk, and EMI problems.
These reliability issues can result in premature failure of the PCB, leading to costly repairs, replacements, and potential safety hazards.
Ensuring FR4 Quality in PCB Manufacturing
To minimize the impact of FR4 quality issues on PCB manufacturing and ensure reliable end-product performance, several best practices should be followed:
Supplier Qualification
Selecting reputable and qualified FR4 suppliers is crucial for maintaining consistent quality. Suppliers should be evaluated based on their manufacturing capabilities, quality control processes, and compliance with industry standards. Regular audits and performance monitoring can help ensure ongoing supplier quality.
Incoming Material Inspection
Implementing a robust incoming material inspection process is essential for identifying and rejecting substandard FR4 materials before they enter the production line. Visual inspection, dimensional checks, and electrical testing can help detect any quality issues early in the process.
Process Control and Monitoring
Strict process control and monitoring during PCB manufacturing can help minimize the impact of FR4 quality variations. This includes regular calibration of equipment, statistical process control (SPC) techniques, and in-process quality checks. Automated inspection systems can also help detect and correct any process deviations in real-time.
Design for Manufacturability (DFM)
Incorporating DFM principles during the PCB design phase can help mitigate the impact of FR4 quality issues. This includes selecting appropriate laminate thickness and copper weights, designing for proper signal routing and impedance control, and allowing for adequate manufacturing tolerances. Collaboration between the design and manufacturing teams can help optimize the design for the specific FR4 material and manufacturing process.
FAQ
What is the difference between FR4 and other PCB materials?
FR4 is a glass-reinforced epoxy laminate, which offers a balance of good mechanical, electrical, and thermal properties at a reasonable cost. Other PCB materials, such as polyimide or PTFE, may offer better performance in specific areas, such as higher temperature resistance or lower dielectric constant, but at a higher cost and with trade-offs in other properties.
How can I identify low-quality FR4 materials?
Low-quality FR4 materials may exhibit signs such as inconsistent thickness, surface defects, discoloration, or poor handling properties. Electrical testing, such as dielectric constant and dissipation factor measurements, can also help identify any deviations from the specified material properties. Purchasing from reputable suppliers and conducting incoming material inspections can help prevent the use of low-quality FR4 in PCB manufacturing.
Can FR4 quality issues be detected during PCB manufacturing?
Yes, various in-process quality checks and inspection techniques can help detect FR4 quality issues during PCB manufacturing. These include visual inspection, automated optical inspection (AOI), electrical testing, and cross-sectional analysis. Detecting and correcting quality issues early in the manufacturing process can help minimize their impact on the final product performance and reliability.
How does FR4 quality impact the end-product performance?
FR4 quality can have a significant impact on the end-product performance, particularly in high-frequency or high-reliability applications. Inconsistencies in dielectric properties can cause signal integrity issues, while variations in mechanical properties can lead to structural failures or thermal cycling problems. Poor FR4 quality can also result in manufacturing defects, such as delamination or warpage, which can affect the functionality and reliability of the final product.
What should I look for when selecting an FR4 supplier for my PCB project?
When selecting an FR4 supplier, consider factors such as their manufacturing capabilities, quality control processes, and compliance with industry standards. Look for suppliers with a proven track record of providing consistent, high-quality FR4 materials, and who can provide detailed material specifications and test reports. It is also important to consider the supplier’s technical support and responsiveness to any quality issues or concerns that may arise during the project.
Conclusion
FR4 quality is a critical factor in determining the performance, reliability, and manufacturability of PCBs. Understanding the key properties, quality standards, and factors affecting FR4 quality can help PCB manufacturers and designers make informed decisions and implement best practices to ensure consistent and reliable end-product performance. By selecting qualified suppliers, conducting thorough inspections, and maintaining strict process control, the impact of FR4 quality issues on PCB manufacturing can be minimized, leading to improved yield, reduced costs, and enhanced customer satisfaction.
Leave a Reply