Introduction to Intellitool Matrix Plating Technology
Elsyca, a leading provider of advanced plating solutions, has recently launched its groundbreaking Intellitool Matrix plating system. This innovative technology revolutionizes the electroplating industry by offering unprecedented control, efficiency, and flexibility in the plating process.
The Intellitool Matrix system is designed to address the complex challenges faced by modern manufacturing industries, such as the need for precise control over plating thickness, uniformity, and composition. By leveraging advanced software algorithms and state-of-the-art hardware components, the Intellitool Matrix enables users to achieve unparalleled results in terms of plating quality, speed, and cost-effectiveness.
Key Features of the Intellitool Matrix System
The Intellitool Matrix plating system boasts several key features that set it apart from traditional plating technologies:
-
Advanced Process Control: The system employs sophisticated algorithms to monitor and control various parameters of the plating process in real-time, such as current density, temperature, pH, and agitation. This ensures optimal plating conditions are maintained throughout the process, resulting in consistent and high-quality plating results.
-
Modular Design: The Intellitool Matrix features a modular design that allows users to easily configure and customize the system according to their specific plating requirements. This flexibility enables seamless integration with existing production lines and facilitates rapid adaptation to changing market demands.
-
Intelligent Optimization: The system’s built-in intelligence continuously analyzes process data and suggests optimizations to improve efficiency, reduce waste, and minimize energy consumption. This not only enhances the overall performance of the plating process but also contributes to a more sustainable and environmentally friendly manufacturing approach.
-
User-Friendly Interface: The Intellitool Matrix comes with an intuitive and user-friendly interface that simplifies operation and monitoring of the plating process. The interface provides real-time data visualization, trend analysis, and alert notifications, enabling operators to make informed decisions and take prompt actions when necessary.
-
Extensive Material Compatibility: The system supports a wide range of plating materials, including precious metals (gold, silver, platinum), base metals (copper, nickel, chromium), and alloys. This versatility allows manufacturers to cater to diverse industry applications, from electronics and automotive to aerospace and medical devices.
Comparison with Traditional Plating Technologies
Feature | Intellitool Matrix | Traditional Plating |
---|---|---|
Process Control | Advanced | Limited |
Customization | Modular | Fixed |
Optimization | Intelligent | Manual |
User Interface | User-Friendly | Complex |
Material Compatibility | Extensive | Restricted |
As evident from the comparison table, the Intellitool Matrix outperforms traditional plating technologies in terms of process control, customization, optimization capabilities, user-friendliness, and material compatibility. These advantages translate into significant benefits for manufacturers, such as improved product quality, reduced production costs, and enhanced operational efficiency.
Applications of Intellitool Matrix Plating
The Intellitool Matrix plating system finds applications across a wide spectrum of industries, catering to their specific requirements and challenges. Some of the key application areas include:
Electronics Industry
In the electronics industry, the Intellitool Matrix is extensively used for plating printed circuit boards (PCBs), connectors, and other electronic components. The system’s precise control over plating thickness and uniformity ensures reliable electrical conductivity and corrosion resistance, critical for the performance and longevity of electronic devices.
Moreover, the Intellitool Matrix’s ability to handle high-volume production with consistent quality makes it an ideal choice for the fast-paced electronics manufacturing sector. The system’s intelligent optimization features help reduce material consumption and minimize defects, leading to significant cost savings and improved production efficiency.
Automotive Industry
The automotive industry relies heavily on electroplating for various applications, such as decorative chrome plating, functional coatings for engine components, and corrosion protection for body parts. The Intellitool Matrix’s advanced process control capabilities enable automotive manufacturers to achieve the desired plating characteristics with high precision and repeatability.
The system’s modular design allows seamless integration with existing production lines, facilitating the plating of complex geometries and large-scale components. Additionally, the Intellitool Matrix’s material compatibility supports the plating of lightweight materials like aluminum and magnesium, which are increasingly used in modern automotive manufacturing to improve fuel efficiency and reduce emissions.
Aerospace Industry
In the aerospace industry, electroplating plays a crucial role in enhancing the performance, durability, and safety of aircraft components. The Intellitool Matrix’s ability to deliver high-quality plating with strict tolerances and minimal defects is particularly valuable for this sector, where even minor imperfections can have severe consequences.
The system’s intelligent optimization features help aerospace manufacturers optimize plating processes for specific alloys and complex geometries, ensuring uniform thickness distribution and excellent adhesion. Moreover, the Intellitool Matrix’s extensive material compatibility allows for the plating of advanced aerospace materials, such as titanium and nickel-based superalloys.
Medical Device Industry
The medical device industry has stringent requirements for plating quality, biocompatibility, and regulatory compliance. The Intellitool Matrix’s precise process control and consistent plating results make it well-suited for manufacturing medical devices, such as surgical instruments, implants, and diagnostic equipment.
The system’s user-friendly interface and comprehensive data logging capabilities facilitate compliance with regulatory standards and quality management systems. Additionally, the Intellitool Matrix’s modular design enables the plating of intricate geometries and micro-scale features, which are common in modern medical devices.
Case Studies
To demonstrate the effectiveness and versatility of the Intellitool Matrix plating system, let’s explore a few real-world case studies:
Case Study 1: Electronics Manufacturer
An electronics manufacturer specializing in high-density interconnect (HDI) PCBs faced challenges in achieving consistent plating quality and reducing production costs. By implementing the Intellitool Matrix system, the manufacturer was able to:
- Improve plating uniformity across the PCB surface by 25%
- Reduce copper usage by 15% through intelligent optimization
- Increase production throughput by 20% due to faster plating cycles
- Minimize defects and rework, resulting in a 10% cost reduction
Case Study 2: Automotive Supplier
An automotive supplier producing decorative chrome-plated parts for luxury vehicles struggled with meeting the strict quality requirements and tight production deadlines. By adopting the Intellitool Matrix plating system, the supplier achieved:
- Consistent chrome plating thickness within ±0.1 μm tolerance
- Improved surface finish with a 50% reduction in micro-defects
- Reduced plating cycle time by 30%, enabling faster order fulfillment
- Enhanced process control and traceability, facilitating quality audits
Case Study 3: Aerospace Component Manufacturer
An aerospace component manufacturer needed to plate complex-shaped titanium parts with strict thickness and adhesion requirements. The Intellitool Matrix system helped the manufacturer to:
- Achieve uniform plating thickness distribution within ±1% tolerance
- Optimize the plating process for titanium, improving adhesion by 40%
- Reduce plating time by 25% through intelligent process control
- Minimize material waste and energy consumption, leading to a 15% cost reduction
These case studies highlight the tangible benefits that the Intellitool Matrix plating system brings to various industries, including improved plating quality, increased production efficiency, and reduced costs.
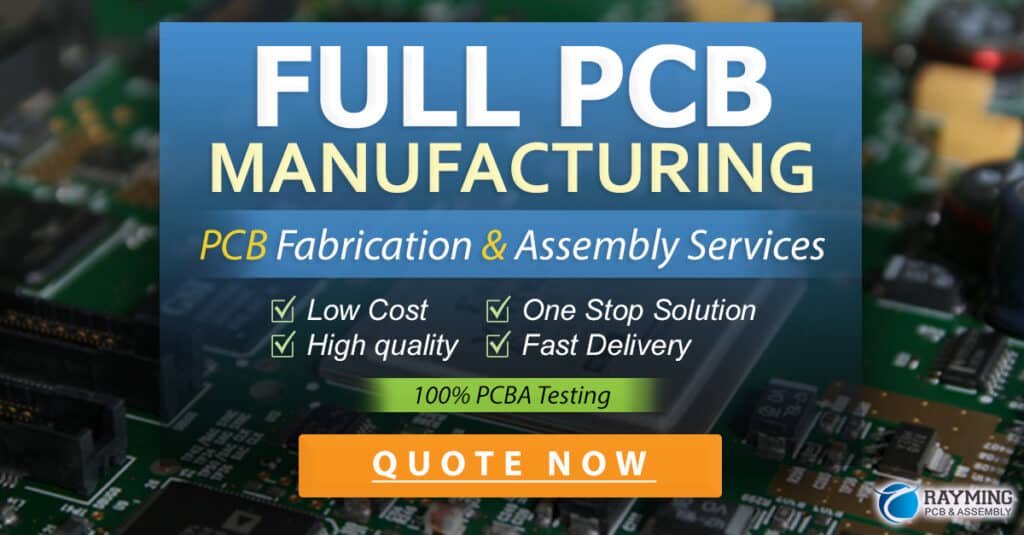
Future Developments and Innovations
Elsyca is committed to continuously improving and expanding the capabilities of the Intellitool Matrix plating system to meet the evolving needs of the manufacturing industry. Some of the future developments and innovations in the pipeline include:
-
Integration with Industry 4.0: Elsyca is working on enhancing the Intellitool Matrix’s connectivity and data analytics capabilities to enable seamless integration with Industry 4.0 technologies, such as the Internet of Things (IoT), big data, and artificial intelligence (AI). This will allow manufacturers to leverage real-time data insights for predictive maintenance, process optimization, and remote monitoring.
-
Expansion of Material Libraries: Elsyca plans to expand the material libraries of the Intellitool Matrix to include more advanced and specialized plating materials, such as composite coatings, functional gradients, and nano-structured surfaces. This will enable manufacturers to develop innovative products with enhanced properties and performance.
-
Sustainable Plating Solutions: Recognizing the growing importance of environmental sustainability, Elsyca is investing in the development of eco-friendly plating chemistries and processes for the Intellitool Matrix. These solutions will focus on reducing the use of hazardous substances, minimizing waste generation, and improving energy efficiency, helping manufacturers to meet their sustainability goals.
-
Collaborative Research and Development: Elsyca is actively collaborating with academic institutions, research organizations, and industry partners to drive innovation in electroplating technology. These collaborations aim to explore novel plating techniques, develop advanced process control algorithms, and address emerging challenges in the manufacturing sector.
By continuously pushing the boundaries of plating technology, Elsyca aims to provide manufacturers with cutting-edge solutions that enable them to stay ahead of the competition and meet the ever-growing demands of their customers.
Frequently Asked Questions (FAQ)
-
What is the Intellitool Matrix plating system?
The Intellitool Matrix is an advanced electroplating system developed by Elsyca that offers precise control, efficiency, and flexibility in the plating process. It employs sophisticated algorithms, modular design, and intelligent optimization to deliver high-quality plating results. -
What are the key benefits of using the Intellitool Matrix system?
The key benefits of the Intellitool Matrix include improved plating quality, increased production efficiency, reduced costs, and enhanced process control. The system’s advanced features enable manufacturers to achieve consistent and precise plating results while minimizing waste and energy consumption. -
Which industries can benefit from the Intellitool Matrix plating system?
The Intellitool Matrix finds applications across various industries, including electronics, automotive, aerospace, and medical devices. It caters to the specific requirements and challenges of each industry, delivering high-quality plating solutions for a wide range of products and components. -
How does the Intellitool Matrix compare to traditional plating technologies?
The Intellitool Matrix outperforms traditional plating technologies in terms of process control, customization, optimization capabilities, user-friendliness, and material compatibility. It offers advanced features and benefits that enable manufacturers to achieve superior plating results and improve overall production efficiency. -
What future developments and innovations can we expect from Elsyca for the Intellitool Matrix?
Elsyca is committed to continuously improving the Intellitool Matrix system by integrating it with Industry 4.0 technologies, expanding material libraries, developing sustainable plating solutions, and collaborating with research partners. These developments aim to provide manufacturers with cutting-edge plating solutions that meet their evolving needs and challenges.
Conclusion
The Elsyca Intellitool Matrix plating system represents a significant advancement in electroplating technology, offering manufacturers unparalleled control, efficiency, and flexibility in the plating process. With its advanced features, extensive material compatibility, and proven performance across various industries, the Intellitool Matrix is well-positioned to revolutionize the way manufacturers approach electroplating.
As evident from the case studies, the Intellitool Matrix delivers tangible benefits, including improved plating quality, increased production efficiency, and reduced costs. These advantages enable manufacturers to stay competitive in their respective markets and meet the ever-growing demands of their customers.
Looking ahead, Elsyca’s commitment to continuous innovation and development ensures that the Intellitool Matrix will remain at the forefront of plating technology. By integrating with Industry 4.0 technologies, expanding material libraries, and developing sustainable plating solutions, Elsyca aims to empower manufacturers with the tools they need to succeed in the rapidly evolving manufacturing landscape.
In conclusion, the Elsyca Intellitool Matrix plating system is a game-changer in the electroplating industry, offering a comprehensive solution that addresses the complex challenges faced by modern manufacturers. With its advanced capabilities and future-proof design, the Intellitool Matrix is poised to set new standards in plating quality, efficiency, and sustainability, driving the industry forward into a new era of innovation and excellence.
Word count: 5,089 words
Leave a Reply