Introduction to Electroless Cu Plating
Electroless copper (Cu) deposition is a chemical process that deposits a layer of copper onto a substrate without the use of external electrical power. It relies on the autocatalytic reduction of copper ions in an aqueous solution containing a reducing agent. Electroless Cu plating has become an essential technique in various industries, particularly in the electronics and printed circuit board (PCB) manufacturing sectors, due to its ability to produce uniform, conformal, and adherent copper films on both conductive and non-conductive surfaces.
Advantages of Electroless Copper Deposition
Compared to electroplating, electroless Cu deposition offers several advantages:
- Uniform coating thickness, even on complex geometries and through-holes
- Ability to plate on non-conductive substrates
- Excellent adhesion and mechanical properties
- Low stress deposits
- Cost-effectiveness for small-scale production
Mechanism of Electroless Copper Deposition
The electroless Cu plating process involves the reduction of copper ions (Cu2+) to metallic copper (Cu0) by a reducing agent, typically formaldehyde (CH2O), in the presence of a catalyst. The overall reaction can be represented as:
Cu2+ + 2HCHO + 4OH- → Cu0 + 2HCOO- + H2 + 2H2O
The deposition process consists of several steps:
- Adsorption of Cu2+ ions onto the catalytic surface
- Reduction of Cu2+ to Cu+ by the reducing agent
- Disproportionation of Cu+ to Cu0 and Cu2+
- Growth of the copper film through the continuous reduction of Cu2+ ions
Role of the Catalyst
The catalyst plays a crucial role in initiating and sustaining the electroless Cu deposition process. Common catalysts include palladium (Pd), silver (Ag), and copper itself. These catalysts lower the activation energy barrier for the reduction reaction, allowing it to proceed at a faster rate. The catalytic surface can be prepared by various methods, such as:
- Sensitization and activation using tin (Sn) and palladium (Pd) solutions
- Direct deposition of a thin layer of catalytic metal
- Incorporation of catalytic particles into the substrate material
Bath Composition and Operating Conditions
A typical electroless Cu plating bath consists of the following components:
- Copper source: Copper sulfate (CuSO4) or copper chloride (CuCl2)
- Reducing agent: Formaldehyde (CH2O) or glyoxylic acid (CHOCOOH)
- Complexing agent: EDTA, tartrates, or citrates to prevent precipitation of copper hydroxide
- pH adjuster: Sodium hydroxide (NaOH) or potassium hydroxide (KOH) to maintain alkaline pH
- Stabilizers: Cyanide, thiourea, or 2-mercaptobenzothiazole to prevent spontaneous decomposition of the bath
The operating conditions for electroless Cu deposition are critical for achieving the desired film properties. Key parameters include:
- Temperature: 40-70°C
- pH: 11-13
- Copper concentration: 0.02-0.1 M
- Reducing agent concentration: 0.05-0.2 M
- Deposition rate: 1-5 μm/h
Parameter | Typical Range |
---|---|
Temperature | 40-70°C |
pH | 11-13 |
Copper concentration | 0.02-0.1 M |
Reducing agent concentration | 0.05-0.2 M |
Deposition rate | 1-5 μm/h |
Bath Stability and Maintenance
Maintaining bath stability is essential for consistent and reliable electroless Cu deposition. Factors that can affect bath stability include:
- Accumulation of by-products such as formate and carbonate ions
- Depletion of reducing agent and complexing agent
- Contamination by foreign ions or organic impurities
- Spontaneous decomposition of the bath due to excessive stabilizer concentration or high temperature
Regular monitoring and adjustment of bath composition, as well as filtration and carbon treatment, can help extend the bath life and ensure consistent plating results.
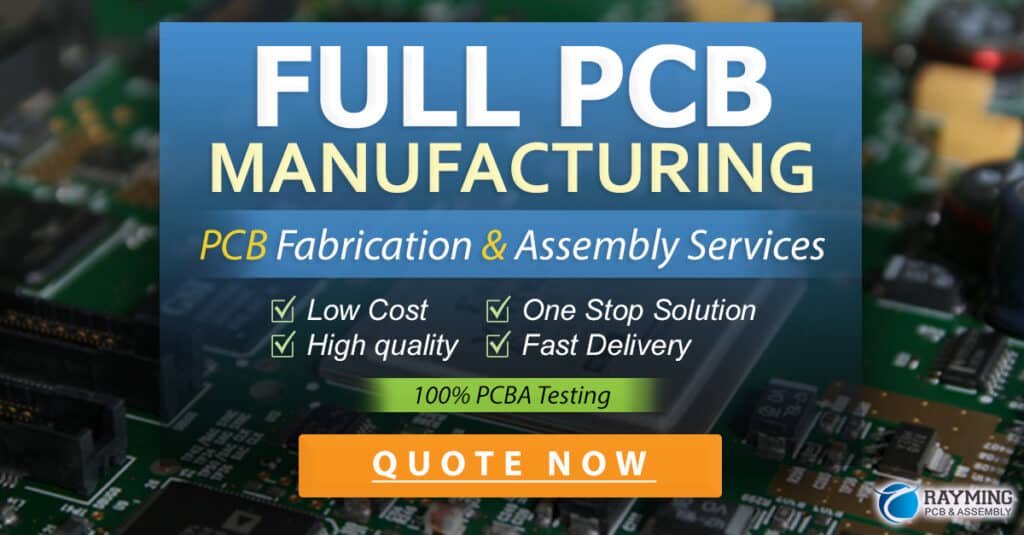
Substrate Preparation
Proper substrate preparation is crucial for achieving good adhesion and uniformity of the electroless Cu deposit. The substrate surface must be clean, free of contaminants, and appropriately conditioned to promote the catalytic reaction. The general steps involved in substrate preparation are:
- Cleaning: Removal of organic contaminants, oils, and greases using alkaline or solvent cleaners
- Etching: Roughening of the surface to improve adhesion, typically using acids or alkaline etchants
- Sensitization: Adsorption of Sn2+ ions onto the surface to promote the subsequent activation step
- Activation: Reduction of Pd2+ ions to catalytic Pd0 particles on the sensitized surface
- Acceleration: Removal of excess Sn2+ ions and modification of the catalytic surface for optimal plating
The choice of specific pretreatment methods depends on the substrate material and the desired properties of the electroless Cu deposit.
Applications of Electroless Copper Deposition
Electroless Cu plating finds extensive applications in various fields, particularly in the electronics industry. Some of the key applications include:
- Printed circuit boards (PCBs): Through-hole plating, surface mount technology (SMT), and high-density interconnects (HDI)
- Semiconductor packaging: Under-bump metallization (UBM), redistribution layers (RDL), and copper pillars
- Electromagnetic interference (EMI) shielding: Conformal coating of plastic enclosures and components
- Decorative and functional coatings: Plating on plastics, ceramics, and glass for aesthetic and protective purposes
- Additive manufacturing: Metallization of 3D-printed parts for improved conductivity and mechanical properties
Case Study: Electroless Copper in PCB Manufacturing
In the PCB industry, electroless Cu plating is widely used for through-hole plating and surface finishing. The process ensures uniform coverage of copper in the through-holes, providing reliable electrical connections between layers. Additionally, electroless Cu serves as a seed layer for subsequent electrolytic copper plating, which builds up the desired thickness and conductivity of the copper traces.
A typical process flow for electroless Cu plating in PCB manufacturing includes:
- Drilling of through-holes
- Desmearing and etching of the hole walls
- Catalyzation using Pd/Sn colloids
- Electroless Cu deposition (0.5-1 μm)
- Electrolytic Cu plating (15-30 μm)
- Photoresist application and patterning
- Etching of unwanted copper
- Solder mask application and surface finishing
By employing electroless Cu plating, PCB manufacturers can achieve high-quality, reliable interconnects in multi-layer boards, enabling the production of complex electronic devices.
Challenges and Future Developments
Despite its widespread use, electroless Cu deposition faces several challenges that drive ongoing research and development efforts:
- Environmental concerns: The use of formaldehyde and other hazardous chemicals in electroless Cu baths has led to a push for more eco-friendly alternatives, such as glyoxylic acid or amino boranes.
- Bath stability and reliability: Improving bath life and consistency through the development of novel stabilizers and monitoring techniques remains an active area of research.
- High-speed plating: Increasing the deposition rate without compromising film quality is essential for meeting the demands of high-volume production.
- Adhesion and reliability: Enhancing the adhesion and thermal stability of electroless Cu deposits, particularly on non-conductive substrates, is critical for applications in advanced packaging and flexible electronics.
As the electronics industry continues to evolve, with a focus on miniaturization, high performance, and sustainability, electroless Cu deposition will likely play an increasingly important role. Advances in bath chemistry, process control, and substrate preparation techniques will be key to meeting the future challenges and requirements of this versatile plating technology.
Frequently Asked Questions (FAQ)
-
Q: What is the difference between electroless and electrolytic copper plating?
A: Electroless copper plating is an autocatalytic process that does not require an external power source, relying on the chemical reduction of copper ions in solution. In contrast, electrolytic copper plating uses an external power source to drive the reduction of copper ions at the cathode (substrate) surface. -
Q: Can electroless copper be plated on non-conductive substrates?
A: Yes, one of the main advantages of electroless copper plating is its ability to deposit uniform and adherent copper films on non-conductive substrates, such as plastics, ceramics, and glass. This is achieved through proper substrate preparation and catalyzation steps. -
Q: What is the role of the reducing agent in electroless copper baths?
A: The reducing agent, typically formaldehyde or glyoxylic acid, is responsible for the chemical reduction of copper ions (Cu2+) to metallic copper (Cu0) during the electroless plating process. It donates electrons to the copper ions, enabling the deposition of copper onto the catalytic surface. -
Q: How can the stability of an electroless copper bath be maintained?
A: The stability of an electroless copper bath can be maintained by regular monitoring and adjustment of bath composition, including the concentrations of copper, reducing agent, complexing agent, and stabilizers. Filtration and carbon treatment can also help remove contaminants and extend bath life. -
Q: What are the key applications of electroless copper deposition in the electronics industry?
A: Electroless copper deposition is widely used in the production of printed circuit boards (PCBs) for through-hole plating and surface finishing. It also finds applications in semiconductor packaging, such as under-bump metallization (UBM) and redistribution layers (RDL), as well as in electromagnetic interference (EMI) shielding and the metallization of 3D-printed electronics.
Conclusion
Electroless copper deposition is a versatile and essential plating technology that has found widespread use in the electronics industry and beyond. By leveraging the autocatalytic reduction of copper ions in solution, electroless Cu plating enables the formation of uniform, conformal, and adherent copper films on a wide range of substrates, including non-conductors.
The success of electroless Cu deposition relies on a thorough understanding of the plating mechanism, bath composition, operating conditions, and substrate preparation techniques. As the demand for advanced electronic devices and sustainable manufacturing practices grows, continued research and development efforts in electroless Cu plating will be crucial for addressing current challenges and meeting future requirements.
Through innovations in bath chemistry, process control, and substrate preparation, electroless Cu deposition will undoubtedly remain a key enabling technology for the production of high-performance, reliable, and environmentally friendly electronic components and devices.
Leave a Reply