Introduction to Gold-Plated Edge Connectors
Gold-plated edge connectors are widely used in various electronic applications due to their superior conductivity, corrosion resistance, and durability. These connectors are designed to provide reliable electrical connections between printed circuit boards (PCBs) and other components in a system. In this article, we will explore the advantages, applications, and manufacturing processes of gold-plated edge connectors.
What are Gold-Plated Edge Connectors?
Gold-plated edge connectors are electrical connectors that feature a thin layer of gold plating on the contact surfaces. The gold plating is applied to the exposed edges of a PCB, which are then inserted into a corresponding socket or slot to establish an electrical connection. The gold plating ensures a low-resistance, stable connection that is resistant to oxidation and corrosion.
Advantages of Gold Plating in Edge Connectors
Gold plating offers several key advantages when used in edge connectors:
- Excellent Conductivity: Gold is an excellent conductor of electricity, ensuring minimal resistance and optimal signal integrity.
- Corrosion Resistance: Gold is highly resistant to corrosion and oxidation, maintaining a stable connection even in harsh environments.
- Durability: Gold-plated contacts can withstand numerous mating cycles without significant wear or degradation.
- Low Contact Resistance: The gold plating helps to minimize contact resistance, resulting in improved signal quality and reduced power loss.
Applications of Gold-Plated Edge Connectors
Gold-plated edge connectors find applications in various industries and electronic devices, including:
Consumer Electronics
- Smartphones and tablets
- Laptops and desktop computers
- Gaming consoles
- Digital cameras
Automotive Electronics
- Infotainment systems
- Engine control units (ECUs)
- Advanced driver assistance systems (ADAS)
- Telematics devices
Industrial Electronics
- Programmable logic controllers (PLCs)
- Human-machine interfaces (HMIs)
- Industrial automation systems
- Process control equipment
Medical Devices
- Patient monitoring systems
- Diagnostic equipment
- Imaging devices
- Wearable medical devices
Aerospace and Defense
- Avionics systems
- Satellite communications
- Military communication devices
- Radar and surveillance equipment
Manufacturing Process of Gold-Plated Edge Connectors
The manufacturing process of gold-plated edge connectors involves several steps to ensure high-quality and reliable connections. Let’s take a closer look at each step:
1. PCB Fabrication
The process begins with the fabrication of the printed circuit board (PCB) that will house the edge connector. The PCB is designed with exposed contact fingers along one or more edges, which will later be plated with gold.
2. Surface Preparation
Before applying the gold plating, the PCB surface must be properly prepared to ensure adequate adhesion and uniform coverage. This step typically involves cleaning the surface to remove any contaminants, followed by a micro-etching process to roughen the surface and improve adhesion.
3. Nickel Plating
A layer of nickel is often applied as an undercoat before the gold plating. Nickel serves as a barrier layer, preventing the diffusion of copper from the PCB into the gold layer. It also improves the overall durability and wear resistance of the connector.
4. Gold Plating
The final step involves applying a thin layer of gold onto the nickel-plated contact fingers. The gold plating is typically applied using an electroplating process, where the PCB is immersed in a gold plating solution and an electric current is applied. The thickness of the gold layer can vary depending on the specific application requirements, but it typically ranges from 0.1 to 2.0 micrometers.
5. Quality Control
Stringent quality control measures are implemented throughout the manufacturing process to ensure the consistency and reliability of the gold-plated edge connectors. This includes visual inspections, thickness measurements, adhesion tests, and electrical performance tests.
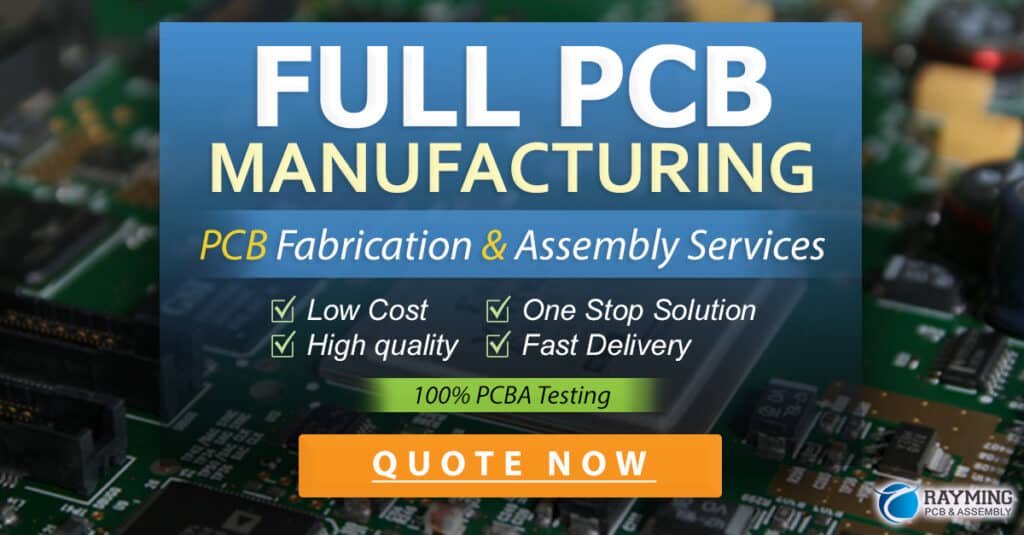
Design Considerations for Gold-Plated Edge Connectors
When designing gold-plated edge connectors, several factors must be considered to ensure optimal performance and reliability:
Contact Pitch
The contact pitch refers to the distance between the centers of adjacent contact fingers on the edge connector. A smaller pitch allows for higher density connections but may require more precise manufacturing processes. Common pitches for gold-plated edge connectors include 1.27 mm, 2.00 mm, and 2.54 mm.
Contact Thickness
The thickness of the gold plating on the contact fingers is a critical design parameter. Thicker gold layers provide better wear resistance and durability but may increase the overall cost of the connector. The appropriate thickness depends on the application requirements, such as the expected number of mating cycles and the operating environment.
Contact Shape and Geometry
The shape and geometry of the contact fingers can affect the electrical performance and mechanical stability of the edge connector. Common contact shapes include rectangular, round, and bifurcated contacts. The choice of contact shape depends on factors such as the required contact force, insertion and withdrawal forces, and the mating connector design.
PCB Material and Thickness
The choice of PCB material and thickness can impact the performance and reliability of the gold-plated edge connector. Factors to consider include the dielectric constant, thermal conductivity, and mechanical strength of the PCB material. The thickness of the PCB should be selected based on the required mechanical stability and the mating connector design.
Testing and Qualification of Gold-Plated Edge Connectors
To ensure the reliability and performance of gold-plated edge connectors, various testing and qualification procedures are employed:
Environmental Testing
Gold-plated edge connectors are subjected to environmental tests to evaluate their performance under different operating conditions. These tests may include:
- Temperature cycling
- Humidity exposure
- Salt spray corrosion
- Vibration and shock testing
Mechanical Testing
Mechanical tests are conducted to assess the durability and reliability of the edge connectors. Common mechanical tests include:
- Mating and unmating cycles
- Insertion and withdrawal force measurements
- Contact resistance measurements
- Solderability testing
Electrical Testing
Electrical tests are performed to verify the signal integrity and electrical performance of the gold-plated edge connectors. These tests may include:
- Impedance measurements
- Signal integrity analysis
- Crosstalk and noise measurements
- Insulation resistance testing
Standards and Specifications for Gold-Plated Edge Connectors
Several industry standards and specifications provide guidelines for the design, manufacturing, and testing of gold-plated edge connectors. Some of the relevant standards include:
- IEC 60603-2: Connectors for electronic equipment – Part 2: Detail specification for printed board connectors with assessed quality
- IPC-4101: Specification for Base Materials for Rigid and Multilayer Printed Boards
- IPC-6012: Qualification and Performance Specification for Rigid Printed Boards
- MIL-STD-810: Environmental Engineering Considerations and Laboratory Tests
Adhering to these standards ensures that gold-plated edge connectors meet the required performance and reliability criteria for their intended applications.
Frequently Asked Questions (FAQ)
1. What is the typical thickness of gold plating on edge connectors?
The thickness of gold plating on edge connectors typically ranges from 0.1 to 2.0 micrometers, depending on the specific application requirements. Thicker gold layers provide better wear resistance and durability but may increase the overall cost of the connector.
2. Can gold-plated edge connectors be used in high-temperature environments?
Yes, gold-plated edge connectors can be used in high-temperature environments, as gold is stable and resistant to oxidation at elevated temperatures. However, the maximum operating temperature may be limited by other factors, such as the PCB material and the design of the mating connector.
3. How do gold-plated edge connectors compare to other connector types in terms of cost?
Gold-plated edge connectors are generally more expensive than connectors with other plating materials, such as tin or nickel. The higher cost is due to the use of gold, which is a precious metal, and the additional manufacturing steps required for gold plating. However, the superior performance and reliability of gold-plated connectors often justify the added cost in critical applications.
4. Can gold-plated edge connectors be repaired or reworked?
Repairing or reworking gold-plated edge connectors can be challenging due to the precision required in the plating process. In most cases, if a gold-plated edge connector is damaged or worn, it is recommended to replace the entire connector rather than attempting to repair it. Proper handling and mating practices can help to minimize the need for repairs or replacements.
5. Are there any environmental concerns associated with the use of gold in edge connectors?
The use of gold in edge connectors does raise some environmental concerns, primarily related to the mining and extraction of gold. However, the electronics industry has been working to minimize the environmental impact of gold usage through initiatives such as recycling and the development of more sustainable manufacturing processes. Proper disposal and recycling of electronic components containing gold can help to mitigate these concerns.
Conclusion
Gold-plated edge connectors play a vital role in ensuring reliable and high-performance electrical connections in a wide range of electronic applications. The use of gold plating provides superior conductivity, corrosion resistance, and durability compared to other plating materials. Understanding the manufacturing process, design considerations, and testing requirements for gold-plated edge connectors is essential for selecting the appropriate connector for a given application.
As technology continues to advance, the demand for reliable and high-performance edge connectors will only increase. By staying informed about the latest developments in gold-plating techniques and industry standards, engineers and designers can ensure that their electronic devices meet the evolving needs of the market while maintaining the highest levels of quality and reliability.
Characteristic | Gold-Plated Edge Connectors |
---|---|
Conductivity | Excellent |
Corrosion Resistance | High |
Durability | Very Good |
Contact Resistance | Low |
Cost | Higher |
Table 1: Key characteristics of gold-plated edge connectors
Application | Pitch (mm) | Thickness (μm) |
---|---|---|
Consumer Electronics | 1.27 | 0.5 – 1.0 |
Automotive | 2.00 | 1.0 – 2.0 |
Industrial | 2.54 | 1.5 – 2.0 |
Medical Devices | 1.27 | 1.0 – 1.5 |
Table 2: Common pitch and thickness values for gold-plated edge connectors in different applications
Leave a Reply