Introduction to Drill-Slot-Classification
Drill-Slot-Classification is a critical process in manufacturing and engineering industries that involves categorizing and organizing data related to drills and slots. This process helps streamline production, improve efficiency, and ensure the accuracy of machining operations. In this article, we will delve into the intricacies of Drill-Slot-Classification, exploring its importance, methods, and best practices.
What is Drill-Slot-Classification?
Drill-Slot-Classification is the process of categorizing and organizing data related to drills and slots used in manufacturing and engineering. This data includes information such as:
- Drill and slot dimensions
- Material properties
- Cutting parameters
- Tool geometries
- Surface finishes
By classifying this data, manufacturers can optimize their machining processes, reduce errors, and improve overall product quality.
Why is Drill-Slot-Classification important?
Drill-Slot-Classification plays a crucial role in various industries, including:
- Aerospace
- Automotive
- Medical devices
- Electronics
- Heavy machinery
Proper classification of drill and slot data helps manufacturers:
- Streamline production processes
- Reduce machining errors
- Improve product quality and consistency
- Optimize tool selection and usage
- Facilitate data-driven decision making
Methods of Drill-Slot-Classification
There are several methods used for Drill-Slot-Classification, each with its own advantages and limitations. Some of the most common methods include:
1. Manual Classification
Manual classification involves manually categorizing drill and slot data based on predefined criteria. This method is often used in smaller-scale manufacturing operations or when dealing with unique or custom components.
Advantages:
– Flexibility in handling unique or custom components
– No special software or equipment required
Limitations:
– Time-consuming and labor-intensive
– Prone to human error
– Difficult to scale for larger operations
2. Automated Classification using Machine Learning
Automated classification using machine learning involves training algorithms to recognize patterns and classify drill and slot data based on predefined categories. This method is becoming increasingly popular due to its efficiency and accuracy.
Advantages:
– High accuracy and consistency
– Faster than manual classification
– Scalable for large datasets
– Continuously improves with more data
Limitations:
– Requires significant upfront investment in software and infrastructure
– Needs a large, diverse dataset for training
– May struggle with unique or custom components
3. Hybrid Approach
A hybrid approach combines manual and automated classification methods, leveraging the strengths of both. This method is often used when dealing with a mix of standard and custom components.
Advantages:
– Balances the flexibility of manual classification with the efficiency of automation
– Suitable for operations with a mix of standard and custom components
Limitations:
– Requires a combination of skilled human operators and machine learning infrastructure
– May be more complex to implement and maintain
Best Practices for Drill-Slot-Classification
To ensure the effectiveness and accuracy of Drill-Slot-Classification, manufacturers should follow these best practices:
- Establish clear classification criteria
- Use standardized nomenclature and terminology
- Regularly review and update classification systems
- Invest in employee training and education
- Leverage technology and automation where appropriate
- Continuously monitor and improve classification processes
Best Practice | Description |
---|---|
Clear Classification Criteria | Establish well-defined, unambiguous criteria for categorizing drill and slot data |
Standardized Nomenclature | Use consistent terminology and naming conventions across the organization |
Regular Review and Updates | Periodically review and update classification systems to accommodate new technologies and requirements |
Employee Training | Invest in training and education to ensure employees understand and adhere to classification standards |
Leverage Technology | Utilize machine learning and automation to improve classification efficiency and accuracy |
Continuous Improvement | Continuously monitor and refine classification processes based on performance metrics and feedback |
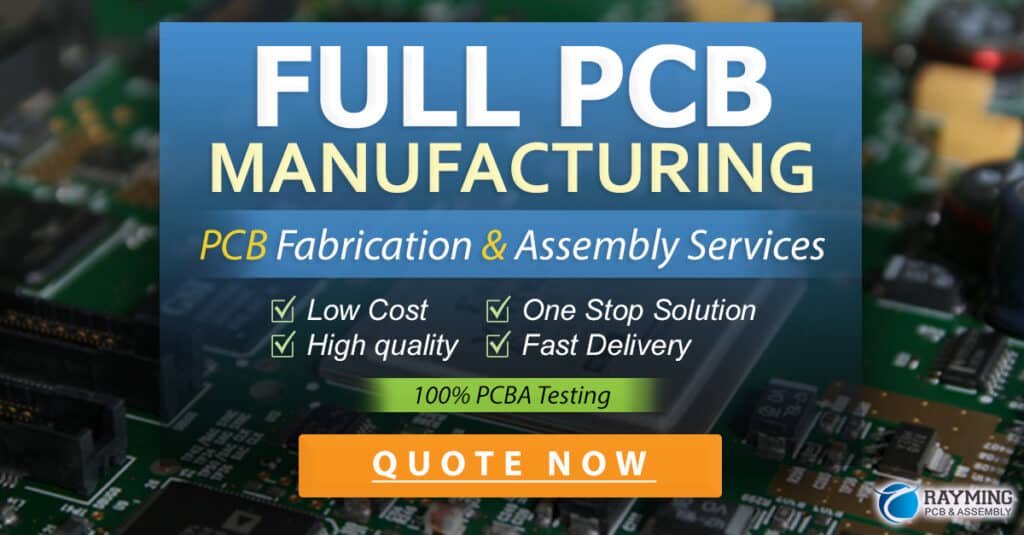
Frequently Asked Questions (FAQ)
1. What are the most common criteria used for Drill-Slot-Classification?
The most common criteria used for Drill-Slot-Classification include:
– Drill and slot dimensions (e.g., diameter, depth, length)
– Material properties (e.g., hardness, tensile strength)
– Cutting parameters (e.g., feed rate, spindle speed)
– Tool geometries (e.g., point angle, helix angle)
– Surface finishes (e.g., roughness, tolerance)
2. How can machine learning improve Drill-Slot-Classification?
Machine learning can improve Drill-Slot-Classification by:
– Automating the classification process, reducing human error and increasing efficiency
– Continuously learning and adapting to new data, improving accuracy over time
– Identifying complex patterns and relationships that may be difficult for humans to discern
– Scaling to handle large datasets and complex classification tasks
3. What are the challenges in implementing an automated Drill-Slot-Classification system?
Some of the challenges in implementing an automated Drill-Slot-Classification system include:
– Significant upfront investment in software, hardware, and infrastructure
– Collecting and curating a large, diverse dataset for training machine learning models
– Ensuring the system can handle unique or custom components that may not fit predefined categories
– Integrating the automated system with existing manufacturing processes and workflows
4. How often should Drill-Slot-Classification systems be reviewed and updated?
Drill-Slot-Classification systems should be reviewed and updated regularly, typically every 6-12 months or whenever significant changes occur in:
– Manufacturing processes and technologies
– Product designs and specifications
– Industry standards and regulations
– Organizational structure and priorities
Regular reviews and updates ensure that classification systems remain relevant, accurate, and effective.
5. What are the benefits of standardizing nomenclature and terminology in Drill-Slot-Classification?
Standardizing nomenclature and terminology in Drill-Slot-Classification offers several benefits, including:
– Improving communication and collaboration across different departments and teams
– Reducing confusion and ambiguity in classification processes
– Facilitating data integration and analysis across multiple systems and platforms
– Enhancing the accuracy and consistency of classification results
– Simplifying employee training and onboarding processes
Conclusion
Drill-Slot-Classification is a vital process in manufacturing and engineering industries, enabling organizations to optimize their machining operations, improve product quality, and streamline production. By understanding the various methods and best practices associated with Drill-Slot-Classification, manufacturers can make informed decisions about how to implement and maintain effective classification systems.
As technology continues to advance, the role of machine learning and automation in Drill-Slot-Classification will likely grow, offering new opportunities for efficiency and accuracy. However, the importance of human expertise and judgment should not be overlooked, as a hybrid approach combining manual and automated methods may often yield the best results.
Ultimately, the key to successful Drill-Slot-Classification lies in establishing clear criteria, leveraging the right technologies, and fostering a culture of continuous improvement. By embracing these principles, manufacturers can unlock the full potential of their machining operations and stay competitive in an ever-evolving industry landscape.
Leave a Reply