Introduction to DRC in CAD
Design Rule Checking (DRC) is a critical step in the electronic design process that verifies a design meets all manufacturing specifications and will result in a functioning, manufacturable product. DRC identifies design errors, violations of manufacturing constraints, and potential reliability issues. Running DRC checks within a CAD tool before releasing files to manufacturing can save significant time and cost by catching problems early.
All major PCB CAD packages include automated DRC features to validate designs against a set of defined rules. While the specific implementation varies between tools, the fundamental concepts are the same. This article provides an overview of key DRC settings and guidelines that generally apply across CAD platforms.
Defining Manufacturing Constraints
The first step in leveraging DRC is to define the manufacturing constraints and requirements for your design. This information should be obtained from your fabrication partner early in the design process. Key specifications to collect include:
Manufacturing Constraint | Description |
---|---|
Minimum line width/space | The smallest trace width and spacing the fab can reliably produce |
Minimum drill size | The smallest mechanical drill hole size, typically for vias |
Minimum annular ring | The minimum copper ring around a drilled hole |
Solder mask tolerances | Minimum solder mask web and clearances around pads |
Hole-to-copper clearance | Minimum clearance from copper features to board edges and holes |
Additional constraints may apply depending on the PCB technology, number of layers, and materials used. Consult with your fab partner to fully define their manufacturing capabilities that your design must adhere to.
Setting Up a DRC Check
Once you have the manufacturing constraints defined, the next step is to set up DRC checks in your CAD tool to validate the design against those constraints. The exact process for this varies between tools, but the general flow is:
- Create or open a DRC rules file
- Define rules with scopes, constraints, and values
- Associate the DRC rules to the PCB design file
- Run a DRC check on the design
- Review and address any errors or warnings
Most CAD tools come with sample DRC rule files that can be used as a starting point. However, the rules should be carefully reviewed and updated to match your specific manufacturing constraints.
Example DRC Rules
Below are some examples of common DRC rules found in most PCB CAD packages:
Electrical Clearance
Verifies minimum spacing between copper features on the same layer.
Rule Name: Electrical Clearance
Scope: All Layers
Constraints: Min = 0.006"
Copper Width
Checks that traces and copper primitives meet a minimum width.
Rule Name: Copper Width
Scope: All Layers
Constraints: Min = 0.008"
Drill Size
Validates that drilled holes meet a specified minimum diameter.
Rule Name: Drill Size
Scope: All Through Holes
Constraints: Min = 0.020"
Annular Ring
Checks the minimum annular ring (copper pad) around drilled holes.
Rule Name: Annular Ring
Scope: All Through Holes
Constraints: Min = 0.010"
Many other DRC rule types exist, including clearances, solder mask, silk screen, plane pullbacks, same net spacing, and more. Consult your CAD tool’s documentation for a full list of supported rules and how to define them.
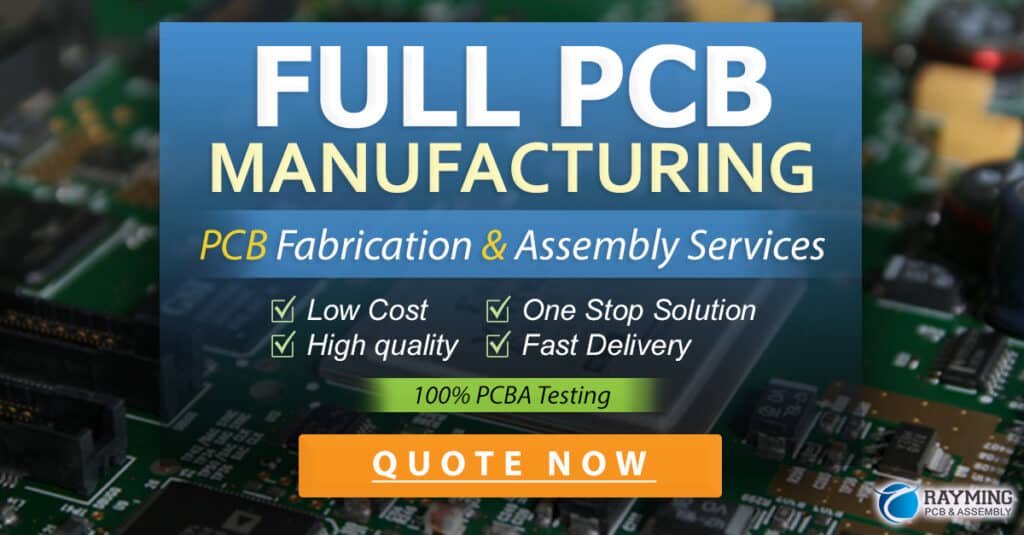
Running a DRC Check
With the DRC rules defined, running a check on your design is usually straightforward:
- Open or activate the PCB design file
- Open the DRC tool and select the rule file to use
- Configure options for the check (e.g. check scope, reporting)
- Run the DRC check
- Review the results in the DRC report viewer
If any DRC violations are found, the tool will report their location, layer, and the specific rule that was violated. You can then navigate to each error in the design, make corrections, and re-run DRC until the check passes with no errors.
Many CAD tools allow DRC checks to be run on an entire design or just a specific subset of layers or area. This can be useful for incremental checking during design rather than waiting until the end.
Reporting DRC Errors
When DRC violations are found, most tools provide several reporting and visualization options:
Reporting Option | Description |
---|---|
Report file | A text file listing all the DRC errors with details |
Error markers | Graphical markers placed at each error location in the design |
Error overlays | Colored overlay graphics highlighting DRC errors |
Cross-probing | Clicking an error in the report selects the corresponding object(s) |
These reporting features can help you quickly identify and correct DRC violations. Some CAD tools also include an auto-correction feature for certain types of DRC errors.
Reviewing the Results
Carefully reviewing the DRC results is essential – automated DRC checks are very useful but are not perfect. Some violations reported may be insignificant in practice or may be intentional based on the design. Each error should be assessed to determine if a design change is truly needed.
If you are unsure about a reported DRC error, consult with your fab partner. They can usually provide guidance on if a violation is acceptable in terms of manufacturability and reliability.
Limitations of DRC
While DRC is a powerful tool for verifying manufacturability, it does have some limitations to be aware of:
- DRC does not check electrical connectivity or schematic-to-layout synchronization
- DRC rules are only as good as the constraints provided by the designer/fab
- DRC does not verify assembly or mechanical fit
- Complex design constructs may result in false or nuisance DRC errors
- DRC cannot catch all possible manufacturing issues
It is important to recognize that DRC is just one step in the overall design verification process. A comprehensive approach including schematic checks, ECAD/MCAD collaboration, simulation, and design reviews is needed to ensure a successful product.
Best Practices for DRC
Below are some best practices to follow to get the most value out of DRC checks:
- Obtain manufacturing constraints from your fab partner early and refine them as the design progresses
- Use fab-supplied DRC rule files when possible
- Run incremental DRC checks regularly during design, not just at the end
- Carefully review all DRC violations before making changes
- Keep your DRC rule file under version control along with the design files
- Use DRC auto-correction features cautiously, and always double check the results
- Sign off on the final DRC report before releasing design files
FAQ
What is the difference between DRC and DFM?
DRC (Design Rule Check) verifies that a PCB design meets specific manufacturability constraints, spacings, and physical rules. DFM (Design for Manufacturability) is a broader methodology that considers all aspects of a design that impact manufacturing, beyond just physical constraints. DFM incorporates schematic design, component selection, testability, and more. Passing DRC is an important subset of overall DFM.
How often should I run DRC during design?
Ideally, DRC should be run incrementally and frequently during the PCB layout process. This allows errors to be caught early when they are usually easier to correct. At a minimum, a full DRC check should be run before releasing design files to a fab. Many designers run DRC checks nightly or after completing a specific section of the design.
What if my fab partner does not provide DRC rules?
While it is preferable to use DRC rules directly from your fab partner, not all fabs provide them. In this case, you will need to manually create DRC rules based on their published manufacturing capabilities and constraints. Start with common, conservative rules and then refine them as you gain experience with the fab’s processes. If possible, ask the fab to review your DRC rules for alignment with their capabilities.
Can I use the same DRC rules for every design?
DRC rules are usually specific to each fabricator, as they are based on their manufacturing technology and processes. While some baseline rules may apply across designs, it is important to tailor your DRC rules to the fab partner being used. Additionally, more advanced designs may require stricter rules beyond the “standard” constraints, so rules should be assessed on a per-design basis.
What if DRC reports errors that are not true violations?
Occasionally DRC may report violations that are not actually manufacturability problems. This is more common with very complex designs or constructs. If you encounter DRC errors that you believe are not true violations, first double check your design and the specific DRC rule. If the error persists, consult with your fab partner for their assessment. Most CAD tools provide options for waiving or ignoring specific DRC errors if they are determined to be acceptable.
Conclusion
DRC is a critical step of the PCB design process for ensuring manufacturability and catching design errors early. Leveraging the automated DRC features of your CAD tools, based on manufacturing constraints from your fab partner, can save significant time and improve design quality. However, DRC is not a substitute for good design practices and engineering reviews. Used together with a comprehensive design verification process and close collaboration with your fab, DRC can help you get working boards back from manufacturing on the first spin.
Leave a Reply