PCB Material Selection
One of the first DFM considerations is selecting the appropriate laminate material for your PCB based on the end application and operating environment. The most common materials are:
Material | Composition | Typical Applications |
---|---|---|
FR-4 | Woven fiberglass with epoxy resin | Most common for standard PCBs |
Polyimide | Heat-resistant polymer film | High-temp, flex and rigid-flex PCBs |
Rogers | Ceramic-filled PTFE composite | RF/microwave PCBs |
Aluminum | Metal-core laminates | High power LEDs, motor controllers |
Consult with your manufacturer on material availability and lead times. Using uncommon or specialty laminates may increase costs and turnaround time.
Copper Weight and Thickness
The copper foil weight and finished copper thickness after plating must be specified. Standard 1 oz. copper (35 μm) is sufficient for most designs, but 2-3 oz. copper may be needed for high current applications. Thicker copper requires wider trace widths and spaces.
Ensure the selected copper weight is appropriate and available for the number of layers in your stackup. For example, 0.5 oz. copper is typically only used for inner layers.
Drill Holes and Vias
Careful consideration of drilled holes and vias is crucial for manufacturability:
Drill Size
Use standard drill sizes when possible to avoid custom drill charges. The smallest mechanical drill is typically 0.2 mm, while micro vias can be laser drilled down to 0.1 mm.
Drill Type | Finished Hole Size (mm) |
---|---|
Standard mech. | 0.2 – 6.3 |
Micro via | 0.1 – 0.15 |
Aspect Ratio
The aspect ratio is the ratio of the drilled hole depth to its diameter. The maximum producible aspect ratio depends on the drilling method:
Drilling Method | Max Aspect Ratio |
---|---|
Mechanical | 8:1 |
Laser | 1:1 |
Exceeding these ratios may result in unreliable drilling, barrel plating issues, or breakout. Consult your fab house for their specific aspect ratio guidelines.
Via Types
There are several types of vias that can be used depending on the design requirements:
- Through vias: drilled through the entire board
- Blind vias: drilled from an outer layer to an inner layer
- Buried vias: drilled between inner layers only
Blind and buried vias add significant cost, as they require additional drilling and plating steps. Avoid them unless absolutely necessary.
Via-in-Pad
Vias in SMD pads can cause soldering issues due to wicking of solder down the hole. Tented, filled, or capped vias should be used if vias must be placed in pads.
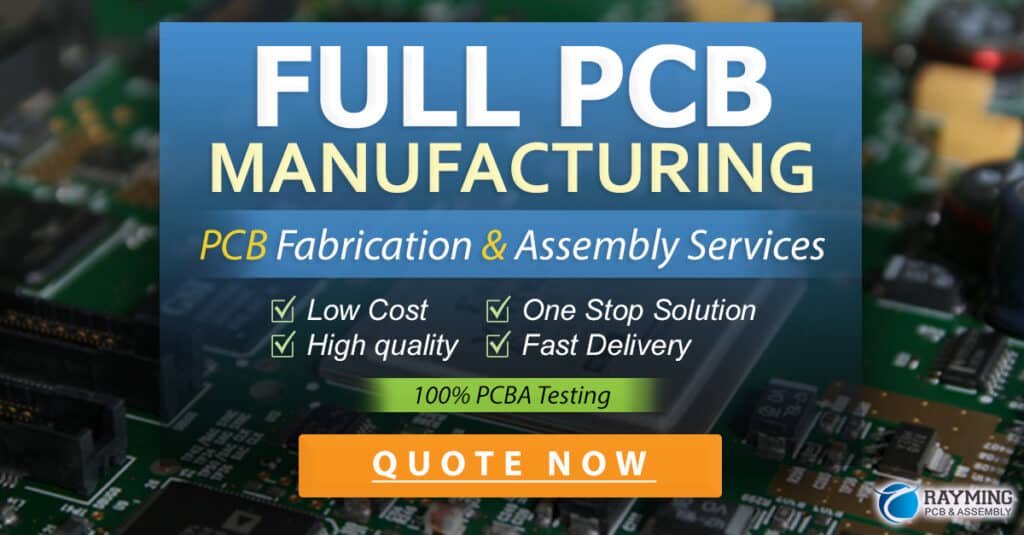
Trace Routing
Proper trace routing is essential for both manufacturability and signal integrity.
Trace Width and Spacing
Traces that are too thin or narrowly spaced can cause fabrication issues. The minimum trace width and spacing depends on the copper weight and PCB class.
For example, a typical 1 oz. copper Class 2 PCB has a minimum trace width and spacing of 0.2 mm. Consult IPC-2221 for details on trace width and spacing per copper weight and class.
Acid Traps
Acid traps are acute angles in traces where etchant can get trapped, leading to over-etching. Avoid acid traps by using gentler angles (>90°) and rounding trace corners.
Starved Thermals
Thermal reliefs that are too small can lead to soldering problems. Ensure thermal spokes and webbing are at least as wide as the minimum producible trace width.
Solder Mask and Silkscreen
The solder mask and silkscreen layers also have several DFM considerations:
Solder Mask Clearance
Mask openings should be larger than the copper feature by a minimum solder mask expansion value, typically 0.05-0.1 mm depending on tolerances. This allows for registration errors between the copper and mask layers.
Silkscreen Text and Lines
Text should be at least 0.15 mm in height with line widths of 0.15-0.2 mm for readability. Avoid placing text or lines over pads, holes, or vias.
Solder Mask Between Pads
For fine-pitch SMD parts, solder mask between pads is recommended to prevent solder bridging. The minimum web size is typically 0.1 mm but consult your manufacturer.
Panelization
PCBs are fabricated in panels which are then separated into individual boards. DFM considerations for panelization include:
Rail Size
Rails at the panel edges allow for handling and tooling. Typical rail sizes are:
Panel Thickness | Recommended Rail Width |
---|---|
<1.0 mm | 5 mm |
1.0 – 2.5 mm | 7.5 mm |
>2.5 mm | 10 mm |
Tooling Holes
Tooling holes are drilled in the rails for registration and securing the panel during fabrication. Typical tooling hole sizes are 2.4 mm and 3.2 mm depending on panel thickness. Consult the fab house for placement requirements.
V-Scoring
V-scoring is a common depanelization method where a v-shaped groove is cut partway into the panel along board edges. Ensure there is adequate space between components and the board edge to accommodate the v-score. A typical v-score is 1 mm wide and 1/3 the board thickness deep.
Submitting Design Files
When submitting design files to the manufacturer, include all necessary files in the correct formats:
- Gerber files: Copper layers, soldermask, silkscreen, drill drawing
- NC drill files: Excellon format
- Fabrication drawing: PDF or DXF with dimensions, tolerances, materials, finishes, etc.
- Assembly drawing: PDF with component placement, orientation, and special instructions
- BOM: Excel or CSV with manufacturer part numbers and quantities
Ensure all files use the same units (inches or mm) and include a readme detailing the contents of each file.
Conclusion
Checking these key DFM considerations before manufacturing will help ensure your PCB can be fabricated efficiently with high yield and reliability. Work closely with your manufacturer and assembly house to understand their specific capabilities, guidelines, and requirements. Catching and resolving dfm pcb issues early in the design phase will save time, money, and headaches later in the product development cycle.
Frequently Asked Questions
What is DFM in PCB design?
DFM (Design for Manufacturability) refers to the process of designing a PCB with consideration for the manufacturing processes and limitations. The goal of DFM is to create a design that can be efficiently and reliably manufactured with high yield.
What are some common DFM issues in PCB design?
Some common DFM issues include using non-standard drill sizes, exceeding maximum aspect ratios for drilled holes, using traces that are too thin or closely spaced, creating acid traps in copper geometry, insufficient solder mask clearances, and silkscreen text that is too small.
How can I check my PCB design for DFM issues?
Many PCB design tools have built-in DFM checks that can analyze your design and flag potential manufacturing issues. You can also manually review your design for common DFM problems and consult with your manufacturer for their specific guidelines and feedback.
What files do I need to submit to my PCB manufacturer?
The typical file package for PCB fabrication includes Gerber files for each copper layer, solder mask, and silkscreen; NC drill files in Excellon format; a fabrication drawing with dimensions, materials, and specifications; an assembly drawing showing component placement; and a bill of materials (BOM).
How can I avoid delays or quality issues when manufacturing my PCB?
To minimize delays and quality issues, thoroughly check your design for DFM problems before submitting it for manufacturing. Provide complete and accurate design files, drawings, and specifications to your manufacturer. Communicate closely with your fab house and assembly partner to understand their capabilities and resolve any discrepancies.
Leave a Reply