Understanding BGA Packages and Fanout
A ball grid array (BGA) is a surface-mount package with an array of solder balls on the bottom for connection to a PCB. BGAs allow for a high density of interconnections in a small package size. However, as the pin count of a BGA increases, properly routing all the connections becomes more challenging. This is especially true for large BGAs with hundreds or even thousands of pins.
Fanout refers to the process of routing the connections from the BGA landing pads on the PCB to other components, signal layers, power planes, and vias. The goal is to escape all the BGA pads while maintaining signal integrity, controlling impedance, minimizing crosstalk, and adhering to manufacturing constraints.
Key Design Rules for BGA Fanout
To successfully fanout a large BGA, there are several key design rules that must be followed:
1. Pad Size and Pitch
The size and pitch of the BGA pads on the PCB are critical for proper soldering and reliability. The pad size should be slightly larger than the BGA ball diameter to allow for some alignment tolerance. A typical recommendation is to use a pad size that is 80-90% of the ball pitch.
For example, for a 1 mm pitch BGA, the pad size would be:
| Ball Pitch | Recommended Pad Size |
| — | — |
| 1.00 mm | 0.80-0.90 mm |
The pad pitch should match the ball pitch of the BGA package exactly. Any mismatch can cause soldering issues and stress on the solder joints.
2. Solder Mask Clearance
Solder mask is applied over the copper pads on the PCB to prevent solder bridging and control the spread of solder paste. For BGA pads, the solder mask opening should be slightly smaller than the copper pad to ensure proper solder wetting.
A typical recommendation is to use a solder mask opening that is 50-100 μm smaller than the copper pad on all sides.
Pad Size | Solder Mask Opening |
---|---|
0.80 mm | 0.70-0.75 mm |
3. Via Types and Size
To route the connections from the BGA pads to inner signal layers, vias are used. There are several types of vias that can be used for BGA fanout:
- Through vias: go through the entire PCB thickness
- Blind vias: start on an outer layer and end on an inner layer
- Buried vias: connect inner layers without reaching the surface
Through vias are the simplest and least expensive, but may not be feasible for very high-density designs. Blind and buried vias allow for greater routing density but are more complex to manufacture.
The size of the vias is another important consideration. Smaller vias allow for tighter spacing and more routing channels, but are more difficult to manufacture reliably. A typical recommendation is to use a via diameter that is 0.25-0.33 mm for a standard multi-layer PCB.
4. Via-in-Pad vs. Dog-Bone Fanout
There are two main approaches to connecting the BGA pads to the vias for fanout:
-
Via-in-pad: The via is placed directly in the BGA pad. This allows for the highest routing density but requires very precise manufacturing to avoid issues with solder wicking down the via hole.
-
Dog-bone fanout: The via is placed outside the BGA pad and connected with a short trace (dog-bone). This is more forgiving for manufacturing but requires more space between pads.
The best approach depends on the specific design requirements and manufacturing capabilities. Via-in-pad is often used for the highest density designs, while dog-bone fanout is more common for standard designs.
5. Trace Width and Spacing
The width and spacing of the traces used for BGA fanout impact the impedance, crosstalk, and manufacturability of the PCB. Thinner traces allow for tighter spacing but have higher impedance and are more susceptible to manufacturing defects.
A typical recommendation is to use a minimum trace width of 0.1-0.125 mm and a minimum spacing of 0.1-0.125 mm for standard designs. For high-speed designs, wider traces and greater spacing may be needed to control impedance.
Trace Width/Spacing | Standard Design | High-Speed Design |
---|---|---|
Minimum Trace Width | 0.1-0.125 mm | 0.2-0.3 mm |
Minimum Trace Spacing | 0.1-0.125 mm | 0.2-0.3 mm |
6. Differential Pair Routing
Many high-speed signals use differential pairs, which require careful routing to maintain signal integrity. Differential pairs should be routed together with a controlled spacing between the traces to maintain the differential impedance.
The spacing between differential pairs should be at least 2-3 times the trace width to minimize crosstalk. Tighter spacing may be possible with more advanced PCB materials and manufacturing processes.
Trace Width | Intra-Pair Spacing | Inter-Pair Spacing |
---|---|---|
0.1 mm | 0.1 mm | 0.2-0.3 mm |
0.2 mm | 0.2 mm | 0.4-0.6 mm |
7. Signal Layers and Plane Layers
For complex BGA fanouts, it is often necessary to use multiple signal layers in the PCB stackup. Alternating signal layers with ground planes helps to control impedance and reduce crosstalk between signals.
A typical 8-layer stackup for a BGA design might look like:
Layer | Type |
---|---|
Top | Signal |
2 | Ground Plane |
3 | Signal |
4 | Power Plane |
5 | Signal |
6 | Ground Plane |
7 | Signal |
Bottom | Signal |
8. Decoupling Capacitors
Adding decoupling capacitors near the BGA power pins is important to maintain power integrity and reduce noise. The placement and value of the decoupling capacitors depends on the specific power requirements of the BGA device.
A typical recommendation is to place at least one low-value (0.1 μF) and one high-value (1-10 μF) capacitor as close as possible to each power pin pair. Additional bulk capacitance may be needed elsewhere on the board.
Fanout Routing Strategies
With the key design rules in mind, there are several strategies that can be used to route the fanout for a large BGA:
1. Rows and Columns
The simplest approach is to route the fanout in rows and columns, escaping the pads to the edges of the BGA. This works well for smaller BGAs but becomes difficult for larger pin counts.
2. Staggered Vias
To increase the routing density, the vias can be staggered in a diagonal pattern around the BGA. This allows for more routing channels between the pads.
3. Multiple Rows
For very large BGAs, multiple rows of vias can be used to gradually fanout the connections. The inner rows handle the most dense connections, while the outer rows provide more space for routing.
4. Hybrid Approaches
Combining different strategies, such as rows and columns for signal pins and staggered vias for power pins, can provide an optimal balance of density and manufacturability.
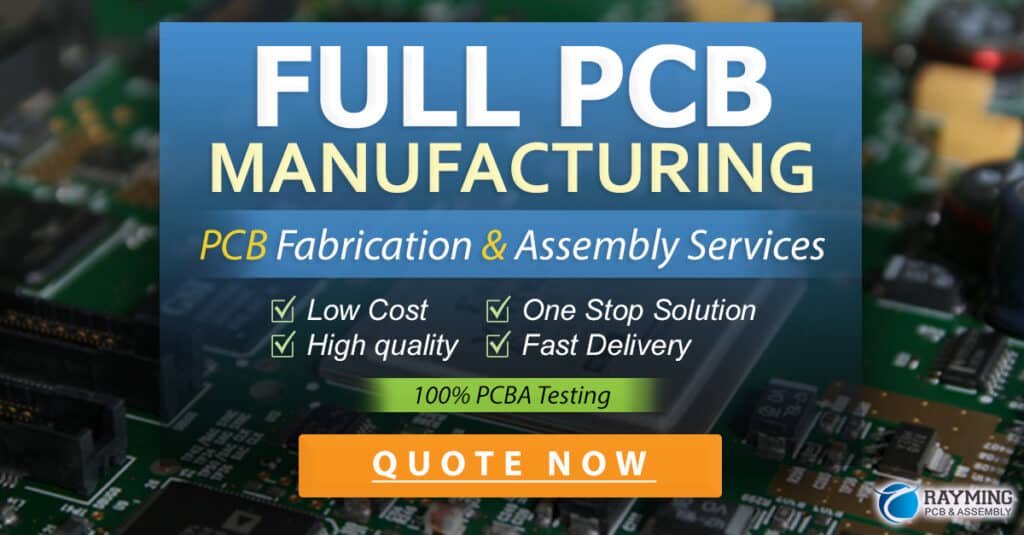
FAQ
- What is the most important factor in BGA fanout design?
The most important factor is achieving a balance between routing density, signal integrity, and manufacturability. Following the key design rules for pad size, via size, trace width, and spacing is critical to ensure a successful fanout.
- How many PCB layers are needed for a large BGA fanout?
The number of layers depends on the complexity of the design and the number of pins on the BGA. A typical high-density design might require 8 or more layers, with alternating signal and plane layers. Simpler designs may be possible with 4 or 6 layers.
- What is the difference between via-in-pad and dog-bone fanout?
Via-in-pad places the via directly in the BGA pad, allowing for maximum routing density but requiring precise manufacturing. Dog-bone fanout places the via outside the pad and connects it with a short trace, which is more forgiving for manufacturing but requires more space.
- How do you control impedance in a BGA fanout?
Impedance is controlled by adjusting the trace width, spacing, and reference plane spacing. Wider traces and larger spacing increase impedance, while narrower traces and smaller spacing decrease impedance. Placing reference planes close to the signal layers also helps to control impedance.
- What is the best way to place decoupling capacitors for a BGA?
Decoupling capacitors should be placed as close as possible to the BGA power pins, typically within a few millimeters. A combination of low-value and high-value capacitors is recommended to handle both high-frequency and low-frequency noise. The specific values and placement depend on the power requirements of the BGA device.
Conclusion
Designing the fanout for a large BGA package requires careful consideration of multiple design rules and tradeoffs. By understanding the key factors of pad size, via size, trace width, and spacing, and by applying appropriate routing strategies, it is possible to achieve a high-density fanout while maintaining signal integrity and manufacturability.
As PCB designs continue to push the limits of density and speed, the importance of optimizing BGA fanouts will only continue to grow. By staying up-to-date with the latest design techniques and manufacturing capabilities, PCB designers can successfully overcome the challenges of large BGA fanouts and deliver reliable, high-performance products.
Leave a Reply