Introduction to Predictable PCB Design
Printed Circuit Board (PCB) design has become increasingly complex in recent years, with higher speeds, denser layouts, and more stringent requirements for signal integrity and electromagnetic compatibility (EMC). To ensure that PCBs perform as expected and meet these challenges, it is essential to incorporate electromagnetic (EM) analysis into the design process. One powerful tool for this purpose is Simbeor, a comprehensive software package for EM analysis and simulation of PCBs.
In this article, we will explore how Simbeor can help you design predictable PCBs, focusing on the following key aspects:
- The importance of EM analysis in modern PCB design
- An overview of Simbeor and its capabilities
- Setting up and running EM simulations in Simbeor
- Interpreting simulation results and optimizing your PCB design
- Real-world examples and case studies
By the end of this article, you will have a solid understanding of how to leverage Simbeor for designing predictable PCBs that meet your performance goals and minimize the risk of costly redesigns and manufacturing issues.
The Importance of EM Analysis in Modern PCB Design
As PCB designs become more complex and operate at higher frequencies, the impact of electromagnetic effects on signal integrity and EMC becomes more significant. Some of the key challenges that modern PCB designers face include:
- Signal integrity issues, such as reflections, crosstalk, and lossy transmission lines
- Power integrity problems, including voltage drops, ground bounces, and power supply noise
- EMC concerns, such as radiated emissions, susceptibility to external interference, and regulatory compliance
To address these challenges and ensure that PCBs perform as expected, it is crucial to incorporate EM analysis into the design process. EM analysis allows designers to:
- Accurately model and simulate the electromagnetic behavior of PCBs and their components
- Identify potential signal and power integrity issues early in the design cycle
- Optimize the PCB layout and stack-up to minimize electromagnetic effects and improve performance
- Verify compliance with EMC regulations and standards
- Reduce the risk of costly redesigns, manufacturing issues, and product failures
Traditional vs. Modern PCB Design Approaches
Traditionally, PCB designers relied on general design guidelines, rules of thumb, and post-design testing to address electromagnetic issues. However, this approach has several limitations:
- General guidelines may not be sufficient for complex, high-speed designs
- Post-design testing can be time-consuming and expensive, and may require multiple iterations to resolve issues
- Redesigns and manufacturing delays can significantly impact project timelines and costs
In contrast, a modern PCB design approach that incorporates EM analysis offers several benefits:
- Early identification and resolution of potential issues, reducing the need for costly redesigns
- Optimization of PCB performance and reliability through simulation-driven design
- Faster time-to-market and lower development costs
- Increased confidence in the final product’s performance and compliance with requirements
An Overview of Simbeor and Its Capabilities
Simbeor is a comprehensive software package for electromagnetic analysis and simulation of PCBs, developed by Simberian Inc. It offers a wide range of features and capabilities to help designers create predictable PCBs, including:
Frequency-Domain Analysis
Simbeor utilizes the Generalized Method of Moments (GMoM) and the Method of Lines (MoL) to perform accurate frequency-domain analysis of PCBs. This allows designers to:
- Simulate S-parameters, impedance profiles, and insertion/return loss
- Analyze single-ended and differential transmission lines, vias, and connectors
- Model and optimize discontinuities, such as bends, splits, and transitions
Time-Domain Analysis
In addition to frequency-domain analysis, Simbeor also supports time-domain simulations using the Finite-Difference Time-Domain (FDTD) method. This enables designers to:
- Simulate eye diagrams, rise/fall times, and jitter
- Analyze crosstalk, reflections, and power supply noise
- Perform transient analysis of non-linear and active components
Material Modeling and Characterization
Simbeor includes a comprehensive material library and tools for accurate modeling and characterization of dielectric and conductor materials. This allows designers to:
- Define and manage custom material properties, including frequency-dependent and anisotropic materials
- Extract material parameters from measured data using the Simbeor Material Manager
- Account for the impact of material properties on PCB performance and manufacturability
Integration with PCB Design Tools
Simbeor integrates seamlessly with popular PCB design tools, such as Altium Designer, Cadence Allegro, and Mentor Graphics Xpedition. This enables designers to:
- Import PCB layouts and stack-up information directly from their design tools
- Use Simbeor’s EM analysis results to optimize their designs and verify performance
- Export simulation results back to their design tools for documentation and collaboration
Advanced Features and Add-Ons
Simbeor also offers several advanced features and add-ons to further enhance its EM analysis capabilities, including:
- 3D full-wave analysis for complex structures and packaging
- Electromagnetic Compatibility (EMC) analysis, including far-field radiation patterns and coupling
- Thermal analysis and modeling of PCBs and components
- Design optimization and parametric sweeps
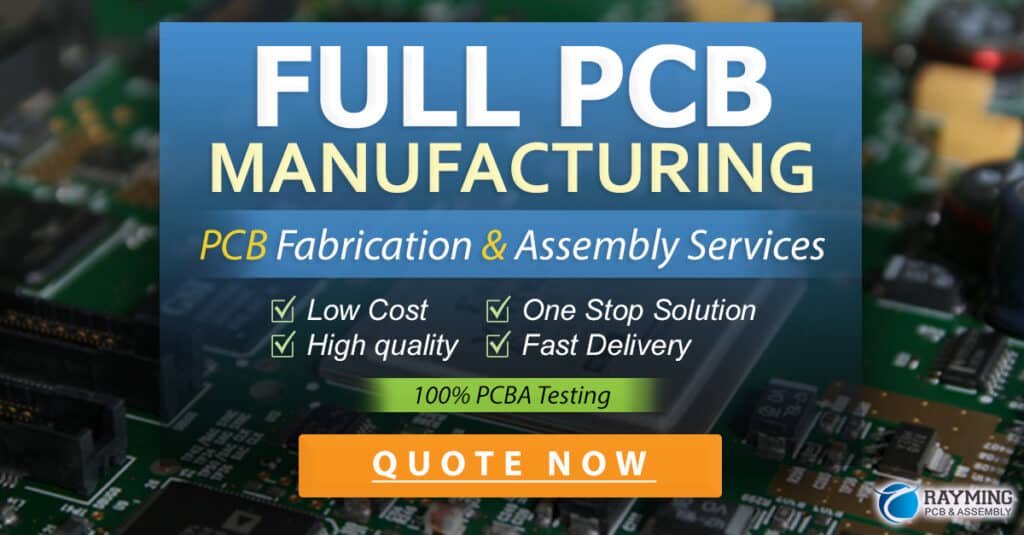
Setting Up and Running EM Simulations in Simbeor
To effectively use Simbeor for designing predictable PCBs, it is essential to understand the process of setting up and running EM simulations. This section will guide you through the key steps involved, including:
Importing and Preparing Your PCB Design
The first step in running EM simulations in Simbeor is to import your PCB design from your preferred PCB design tool. Simbeor supports a wide range of file formats, such as ODB++, IPC-2581, and Gerber. Once your design is imported, you can:
- Review and verify the PCB layout, stack-up, and material properties
- Define simulation domains and boundary conditions
- Assign ports and reference planes for S-parameter analysis
Defining Simulation Settings and Parameters
Next, you need to define the simulation settings and parameters that are appropriate for your analysis goals and design requirements. This includes:
- Selecting the appropriate simulation method (e.g., GMoM, MoL, or FDTD)
- Specifying the frequency range and resolution for frequency-domain simulations
- Setting up time-domain simulation parameters, such as rise/fall times and bit patterns
- Defining convergence criteria and accuracy settings
Running EM Simulations and Monitoring Progress
Once your simulation setup is complete, you can run the EM simulations in Simbeor. The software provides a user-friendly interface for managing and monitoring your simulations, including:
- Real-time progress tracking and estimated completion time
- Logging and reporting of simulation status and any errors or warnings
- Ability to pause, resume, or cancel simulations as needed
Post-Processing and Visualizing Results
After your simulations are complete, Simbeor offers a range of post-processing and visualization tools to help you analyze and interpret the results. This includes:
- Plotting S-parameters, impedance profiles, and eye diagrams
- Generating field distribution plots and animations
- Calculating and displaying derived quantities, such as insertion loss, return loss, and crosstalk
- Comparing simulation results with measurement data or design specifications
Interpreting Simulation Results and Optimizing Your PCB Design
With the EM simulation results in hand, the next step is to interpret the data and use it to optimize your PCB design for better performance and predictability. This section will cover some key strategies and techniques for analyzing simulation results and making informed design decisions.
Identifying Potential Signal and Power Integrity Issues
One of the primary goals of EM analysis is to identify potential signal and power integrity issues in your PCB design. By examining the simulation results, you can look for:
- Impedance mismatches and discontinuities that can cause reflections and signal distortion
- Excessive insertion loss or return loss that may degrade signal quality and limit bandwidth
- Crosstalk between adjacent traces or vias that can lead to signal interference and noise
- Power supply noise and ground bounces that can impact the stability and performance of active components
Evaluating Compliance with Design Specifications and Standards
EM simulations can also help you evaluate your PCB design’s compliance with various design specifications and industry standards. This may include:
- Verifying that signal integrity metrics, such as eye height and jitter, meet the required values
- Checking that EMC emissions and susceptibility levels are within acceptable limits
- Ensuring that the PCB layout and stack-up adhere to recommended design guidelines and best practices
Exploring Design Alternatives and Optimizations
Based on the insights gained from EM simulations, you can explore various design alternatives and optimizations to improve your PCB’s performance and predictability. Some common strategies include:
- Adjusting trace widths, spacings, and routing to minimize crosstalk and impedance discontinuities
- Optimizing via placement and design to reduce signal reflections and power supply noise
- Modifying the PCB stack-up and material properties to improve signal integrity and manufacturability
- Implementing advanced techniques, such as differential signaling, edge coupling, and ground shielding
Iterative Design and Simulation Process
Designing predictable PCBs is often an iterative process, involving multiple rounds of simulation, analysis, and optimization. By using Simbeor to guide your design decisions and verify the impact of each change, you can gradually refine your PCB layout and stack-up until it meets your performance goals and design requirements.
Real-World Examples and Case Studies
To illustrate the practical application of Simbeor for designing predictable PCBs, this section will present several real-world examples and case studies. These examples will demonstrate how EM analysis has been used to solve complex PCB design challenges and achieve better performance and reliability.
High-Speed Digital PCB Design
- Challenge: Designing a high-speed digital PCB for a 10 Gbps serial communication interface, while minimizing signal integrity issues and ensuring compliance with industry standards.
- Solution: Using Simbeor to simulate the PCB’s S-parameters, eye diagrams, and crosstalk, and optimizing the layout and stack-up based on the simulation results. Achieved a clean eye opening and low bit error rate, meeting the design requirements.
RF and Microwave PCB Design
- Challenge: Developing a complex RF PCB for a 5G wireless application, with multiple antennas, filters, and amplifiers, while minimizing losses and ensuring proper impedance matching.
- Solution: Utilizing Simbeor’s 3D full-wave analysis capabilities to model the PCB’s electromagnetic behavior accurately, and optimizing the component placement, trace routing, and via design. Achieved the desired frequency response and radiation patterns, and reduced the need for prototyping and testing.
Automotive Electronics PCB Design
- Challenge: Designing a robust and reliable PCB for an automotive electronics module, subject to harsh environmental conditions and strict EMC requirements.
- Solution: Employing Simbeor to simulate the PCB’s thermal and EMC performance, and making design changes to improve heat dissipation and reduce electromagnetic emissions. Passed the required EMC tests and qualification processes, and achieved a high level of reliability in the field.
FAQ
- Q: What are the system requirements for running Simbeor?
A: Simbeor is compatible with Windows, Linux, and macOS operating systems. The minimum recommended hardware specifications are: - Processor: Intel Core i5 or equivalent
- RAM: 8 GB
- Storage: 500 GB HDD or SSD
-
Graphics: OpenGL 3.3 compatible GPU
-
Q: How does Simbeor compare to other EM simulation tools in terms of accuracy and performance?
A: Simbeor offers state-of-the-art EM simulation algorithms, such as GMoM, MoL, and FDTD, which provide high accuracy and performance. In benchmarking studies and customer testimonials, Simbeor has demonstrated results that are comparable to or better than other leading EM simulation tools. -
Q: Can Simbeor handle complex PCB designs with multiple layers and dense layouts?
A: Yes, Simbeor is designed to handle complex PCB designs with multiple layers, dense layouts, and advanced packaging technologies. It offers efficient meshing and solving techniques to manage the computational complexity and memory requirements of large-scale EM simulations. -
Q: Is training and support available for learning and using Simbeor effectively?
A: Yes, Simberian Inc. offers comprehensive training and support services for Simbeor users, including: - Online documentation, tutorials, and application examples
- Webinars, workshops, and on-site training sessions
- Technical support via email, phone, and web-based ticketing system
-
Consulting services for complex design challenges and custom applications
-
Q: How can I integrate Simbeor into my existing PCB design workflow and tools?
A: Simbeor provides seamless integration with popular PCB design tools, such as Altium Designer, Cadence Allegro, and Mentor Graphics Xpedition, through industry-standard file formats and direct interface plugins. This allows you to easily import your PCB designs into Simbeor, run EM simulations, and export the results back to your design environment for implementation and documentation.
Conclusion
In this article, we have explored how Simbeor electromagnetic analysis can help you design predictable PCBs that meet your performance goals and minimize the risk of costly redesigns and manufacturing issues. By incorporating EM simulations into your PCB design process, you can:
- Accurately model and simulate the electromagnetic behavior of your PCBs and components
- Identify and resolve potential signal and power integrity issues early in the design cycle
- Optimize your PCB layout and stack-up for better performance and manufacturability
- Verify compliance with EMC regulations and design specifications
- Achieve faster time-to-market and lower development costs
We have covered the key features and capabilities of Simbeor, including frequency-domain and time-domain analysis, material modeling, and integration with PCB design tools. We have also provided guidance on setting up and running EM simulations, interpreting results, and optimizing your designs based on the insights gained from simulations.
Finally, we have presented real-world examples and case studies to demonstrate the practical application of Simbeor in various PCB design scenarios, from high-speed digital to RF and automotive electronics.
By leveraging the power of Simbeor electromagnetic analysis, you can design predictable PCBs with confidence and stay ahead of the curve in today’s competitive electronics industry.
Leave a Reply